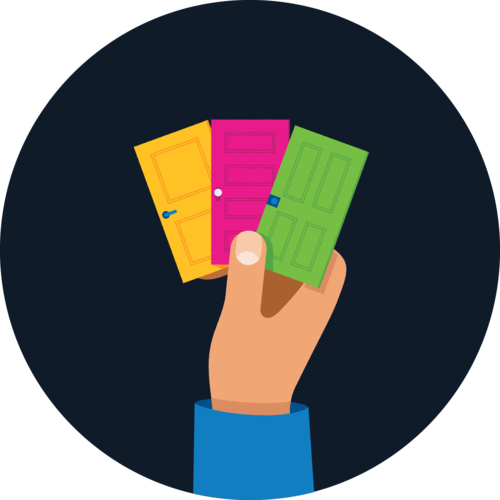
Consumers are increasingly expecting products to provide a holistic experience. To fulfill that expectation, companies will need to have a supply network that can deliver personalized, fast, and customized products. Modern supply chains are more flexible and responsive to changing needs than their traditional counterparts. Companies can make better decisions and monitor disruptions to ensure reliable and timely deliveries by using data and analytics.
Accenture Strategy, a service offered by Accenture, assists companies in transforming their supply chain capabilities. This includes creating new solutions, accelerating skills and capabilities of supply chain workers, and aligning operating model with business strategies. This includes a strong focus on sustainability and good governance. The company hopes to create long-term wealth for its clients.
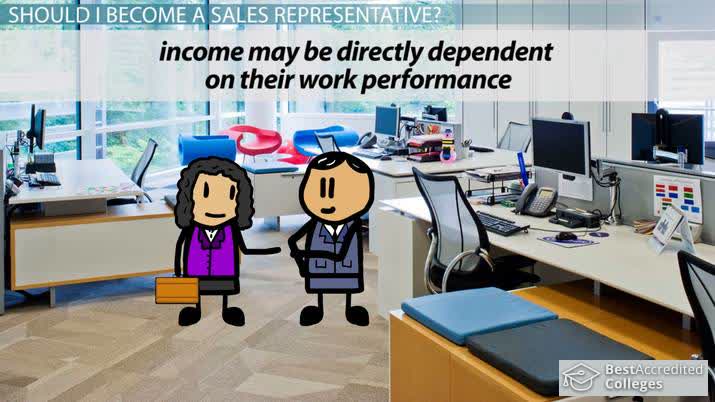
Accenture focuses its efforts on improving global supply chains. Accenture combines industry knowledge with digital services to help achieve this goal. Combined with a global supply network, they can help companies build intelligent supply chains that drive profitable growth and positive social change. Accenture has a broad range of supply chain expertise, which includes everything from energy to consumer packaged good. Accenture's supply-chain experts collaborate with clients to create, operate, and transform their supply systems.
Accenture also works with clients on sustainability initiatives. Accenture has a global supplier inclusion program which aims to assist more companies in making good business decisions and advancing a sustainable, inclusive, ethical supply chain ecosystem. The company has released a report on creating sustainable supply chains, leveraging data, governance, and other topics. The report also offers suggestions for creating resilient supply network and supplier scoring data.
Accenture's supply chains analytics team works with clients, helping them improve sustainability practices and encourage responsible behavior. They are able help clients identify strengths, weaknesses, opportunities for improvement and to design and implement solutions to make them more resilient. Blue Yonder technology was used by the team in order to assist companies with optimizing their supply chain.
Accenture is well-known for its supply chain expertise. The company also has considerable purchasing power. Accenture created an enterprise business system in 2007 which allows companies to more effectively manage and implement their supply chain. Most companies couldn't see beyond a handful of major suppliers, and had no idea about their supply chains. This made it difficult for companies to respond effectively to demand. The company introduced myConcerto, an enterprise-wide solution that provides companies with comprehensive information on how to monitor their supply chain.
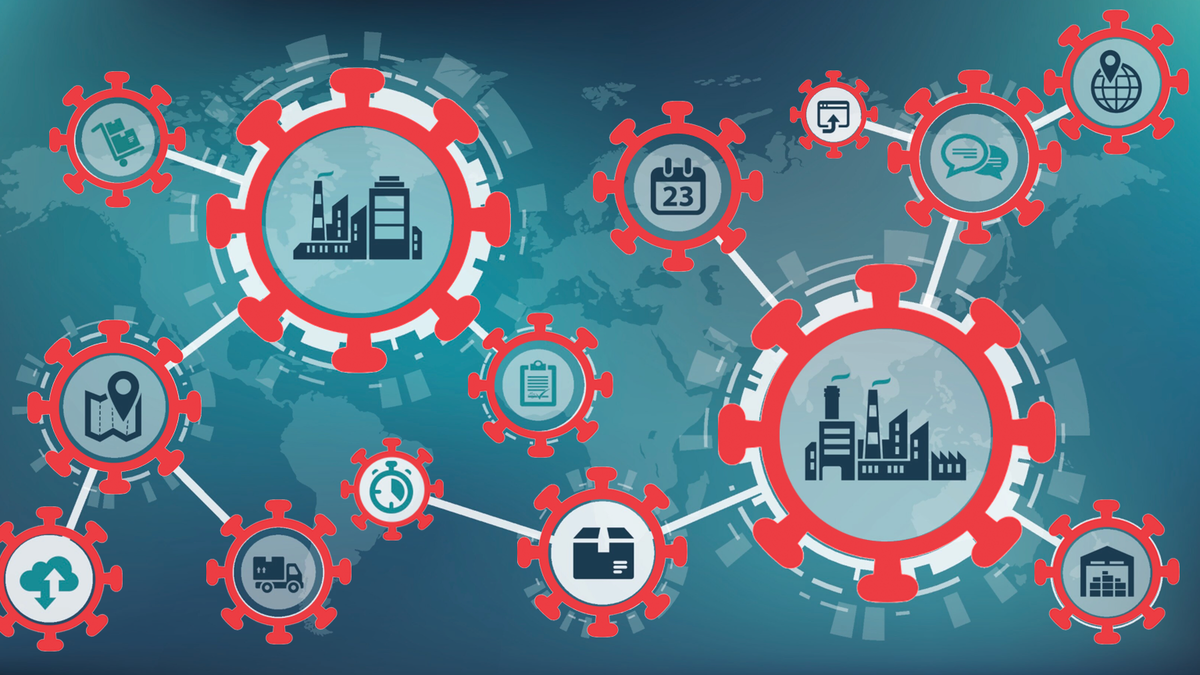
Accenture supply chain specialists also collaborate with the Defense Logistics Agency to improve the reliability of the military supply network. The DLA oversees 520,000 shipments annually, and averages over 8,000 contracts per hour. Accenture collaborates closely with the DLA for product availability and faster delivery times. Accenture works with Coles Supermarkets, to improve the customer experience. The company also developed a Splunk technology control tower monitoring solution.
FAQ
How can manufacturing efficiency be improved?
First, identify the factors that affect production time. Then we need to find ways to improve these factors. If you don't know where to start, then think about which factor(s) have the biggest impact on production time. Once you've identified them, try to find solutions for each of those factors.
What are the 4 types manufacturing?
Manufacturing refers to the transformation of raw materials into useful products by using machines and processes. It includes many different activities like designing, building and testing, packaging, shipping and selling, as well as servicing.
What do we need to know about Manufacturing Processes in order to learn more about Logistics?
No. No. However, knowing about manufacturing processes will definitely give you a better understanding of how logistics works.
How does a production planner differ from a project manager?
The difference between a product planner and project manager is that a planer is typically the one who organizes and plans the entire project. A production planner, however, is mostly involved in the planning stages.
What are the goods of logistics?
Logistics involves the transportation of goods from point A and point B.
These include all aspects related to transport such as packaging, loading and transporting, storing, transporting, unloading and warehousing inventory management, customer service. Distribution, returns, recycling are some of the options.
Logisticians ensure the product reaches its destination in the most efficient manner. Logisticians help companies improve their supply chain efficiency by providing information about demand forecasts and stock levels, production schedules, as well as availability of raw materials.
They keep track and monitor the transit of shipments, maintain quality standards, order replenishment and inventories, coordinate with suppliers, vendors, and provide support for sales and marketing.
What is manufacturing and logistics?
Manufacturing is the act of producing goods from raw materials using machines and processes. Logistics encompasses the management of all aspects associated with supply chain activities such as procurement, production planning, distribution and inventory control. It also includes customer service. Manufacturing and logistics can often be grouped together to describe a larger term that covers both the creation of products, and the delivery of them to customers.
What type of jobs is there in logistics
There are many types of jobs in logistics. These are some of the jobs available in logistics:
-
Warehouse workers - They load trucks and pallets.
-
Transportation drivers: They drive trucks and trailers and deliver goods and make pick-ups.
-
Freight handlers - They sort and pack freight in warehouses.
-
Inventory managers: They are responsible for the inventory and management of warehouses.
-
Sales reps are people who sell products to customers.
-
Logistics coordinators - They plan and organize logistics operations.
-
Purchasing agents - They purchase goods and services needed for company operations.
-
Customer service representatives - They answer calls and emails from customers.
-
Shipping clerks: They process shipping requests and issue bills.
-
Order fillers – They fill orders based upon what was ordered and shipped.
-
Quality control inspectors: They inspect outgoing and incoming products for any defects.
-
Other - Logistics has many other job opportunities, including transportation supervisors, logistics specialists, and cargo specialists.
Statistics
- Job #1 is delivering the ordered product according to specifications: color, size, brand, and quantity. (netsuite.com)
- According to a Statista study, U.S. businesses spent $1.63 trillion on logistics in 2019, moving goods from origin to end user through various supply chain network segments. (netsuite.com)
- In 2021, an estimated 12.1 million Americans work in the manufacturing sector.6 (investopedia.com)
- It's estimated that 10.8% of the U.S. GDP in 2020 was contributed to manufacturing. (investopedia.com)
- In the United States, for example, manufacturing makes up 15% of the economic output. (twi-global.com)
External Links
How To
How to use lean manufacturing in the production of goods
Lean manufacturing is an approach to management that aims for efficiency and waste reduction. It was created in Japan by Taiichi Ohno during the 1970s and 80s. He received the Toyota Production System award (TPS), from Kanji Toyoda, founder of TPS. The first book published on lean manufacturing was titled "The Machine That Changed the World" written by Michael L. Watkins and published in 1990.
Lean manufacturing refers to a set of principles that improve the quality, speed and costs of products and services. It is about eliminating defects and waste from all stages of the value stream. Lean manufacturing is called just-in-time (JIT), zero defect, total productive maintenance (TPM), or 5S. Lean manufacturing seeks to eliminate non-value added activities, such as inspection, work, waiting, and rework.
In addition to improving product quality and reducing costs, lean manufacturing helps companies achieve their goals faster and reduces employee turnover. Lean Manufacturing is one of the most efficient ways to manage the entire value chains, including suppliers and customers as well distributors and retailers. Lean manufacturing practices are widespread in many industries. Toyota's philosophy has been a key driver of success in many industries, including automobiles and electronics.
Five fundamental principles underlie lean manufacturing.
-
Define Value - Determine the value that your business brings to society. Also, identify what sets you apart from your competitors.
-
Reduce Waste – Eliminate all activities that don't add value throughout the supply chain.
-
Create Flow – Ensure that work flows smoothly throughout the process.
-
Standardize and Simplify – Make processes as consistent, repeatable, and as simple as possible.
-
Building Relationships – Establish personal relationships with both external and internal stakeholders.
Lean manufacturing, although not new, has seen renewed interest in the economic sector since 2008. Many businesses have adopted lean production techniques to make them more competitive. Many economists believe lean manufacturing will play a major role in economic recovery.
Lean manufacturing, which has many benefits, is now a standard practice in the automotive industry. These include better customer satisfaction and lower inventory levels. They also result in lower operating costs.
Any aspect of an enterprise can benefit from Lean manufacturing. Lean manufacturing is most useful in the production sector of an organisation because it ensures that each step in the value-chain is efficient and productive.
There are three main types in lean manufacturing
-
Just-in Time Manufacturing: This lean manufacturing method is commonly called "pull systems." JIT is a process in which components can be assembled at the point they are needed, instead of being made ahead of time. This method reduces lead times, increases availability, and decreases inventory.
-
Zero Defects Manufacturing - ZDM: ZDM focuses its efforts on making sure that no defective units leave a manufacturing facility. You should repair any part that needs to be repaired during an assembly line. This applies to finished goods that may require minor repairs before shipment.
-
Continuous Improvement (CI),: Continuous improvement aims improve the efficiency and effectiveness of operations by continuously identifying issues and making changes to reduce waste. It involves continuous improvement of processes, people, and tools.