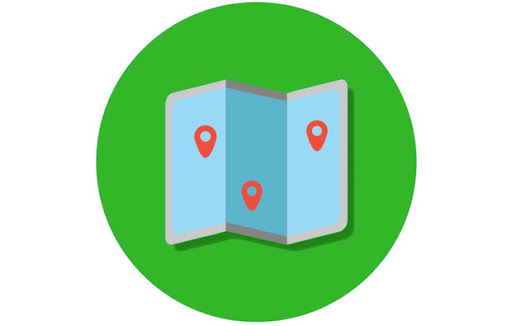
Located in Gibson County, Indiana, Toyota Motor Manufacturing Indiana Inc. is the first Toyota plant to be wholly owned by Toyota in the United States. The plant manufactures Toyota's full-size pickup trucks, including the Avalon and the Corolla, as well as the Sienna minivan. It also makes the Toyota RAV4 Hybrid Hybrid, the best-selling hybrid Toyota ever produced.
It was originally designed to manufacture Toyota Highlander. The plant has since been moved to Gibson County. Since 2011, the Toyota RAV4 Hybrid compact SUV has been produced here, as well as the Lexus ES 350. The plant was worth more than $1.33 Billion in 2017.
Toyota Safety Sense 2.5+ is also manufactured at the plant. It features automatic emergency braking. The plant also prepares all of the new 2018 Camry models. The new model boasts a new transmission with more power and a more stylish look. It will cost $25,900.
Toyota is the biggest American producer of the Toyota Camry. It is currently the best selling midsize sedan in America, and has been for 15 years. Toyota has manufactured 10 million Camrys in Kentucky. The hybrid model is being manufactured in the plant's first production facility in North America.
The Toyota Production System is a collection of practices and techniques that improve quality and efficiency. This system includes 600 Toyota engineers. It also houses the Toyota Production Engineering and Manufacturing Center. The center will also become the first to build hydrogen fuel-cell modules for heavy-duty trucks. It can produce up to 100,000 vehicles annually.
Toyota has made $1.5 billion investments in the plant during the last five-years. It has also hired 700 additional workers. This investment will create 470,100 jobs in the United States by 2020. Toyota has made over $147 Million in Kentucky non-profit partners since 1986.
The Toyota Camry, a reliable and elegant vehicle, is very popular. It comes with the GAK platform and a completely new transmission. It is also fun to drive. Consumer Reports highlighted Toyota Camry's popularity as one of America’s top-selling cars in July.
The Toyota production system includes a number of elements, including continuous improvement, just-in-time parts delivery, and a sophisticated robotic welding system. Toyota's Kentucky Investments in Kentucky have been well demonstrated by its Toyota Production Engineering and Manufacturing Center.
A new production hall design allows Toyota to save on construction costs and air conditioning costs. The building also features a Visitor Center, which includes interactive video displays and exhibits on hybrid technology. Toyota will produce approximately 2 million vehicles in North America within 10 years. This is the largest Toyota facility outside Japan.
Toyota's New Global Architecture marks a major improvement in the company's production systems. The strategy includes a new engine, organization of production, and a module that unifies the structure of vehicle components. The new design preserves Toyota's innovation spirit and reflects Toyota’s traditional values.
FAQ
What does it mean to warehouse?
A warehouse or storage facility is where goods are stored before they are sold. It can be an outdoor or indoor area. In some cases, it may be a combination of both.
What are manufacturing & logistics?
Manufacturing refers to the process of making goods using raw materials and machines. Logistics covers all aspects involved in managing supply chains, including procurement and production planning. Sometimes manufacturing and logistics are combined to refer to a wider term that includes both the process of creating products as well as their delivery to customers.
What are the 7 Rs of logistics management?
The acronym 7Rs of Logistics refers to the seven core principles of logistics management. It was developed by International Association of Business Logisticians (IABL), and published as part of their "Seven Principles of Logistics Management Series" in 2004.
The acronym is composed of the following letters.
-
Responsible - ensure that actions are in compliance with legal requirements and do not cause harm to others.
-
Reliable – have faith in your ability and capability to keep promises.
-
It is reasonable to use resources efficiently and not waste them.
-
Realistic – Consider all aspects, including cost-effectiveness as well as environmental impact.
-
Respectful - show respect and treat others fairly and fairly
-
Resourceful - look for opportunities to save money and increase productivity.
-
Recognizable: Provide customers with value-added service
What are the four types in manufacturing?
Manufacturing refers the process of turning raw materials into useful products with machines and processes. It includes many different activities like designing, building and testing, packaging, shipping and selling, as well as servicing.
Why automate your warehouse?
Modern warehouses are increasingly dependent on automation. E-commerce has brought increased demand for more efficient and quicker delivery times.
Warehouses need to adapt quickly to meet changing needs. In order to do this, they need to invest in technology. Automating warehouses is a great way to save money. These are just a few reasons to invest in automation.
-
Increases throughput/productivity
-
Reduces errors
-
Increases accuracy
-
Boosts safety
-
Eliminates bottlenecks
-
This allows companies to scale easily
-
Makes workers more efficient
-
It gives visibility to everything that happens inside the warehouse
-
Enhances customer experience
-
Improves employee satisfaction
-
Reduces downtime and improves uptime
-
You can be sure that high-quality products will arrive on time
-
Eliminates human error
-
It ensures compliance with regulations
What are the responsibilities of a manufacturing manager
A manufacturing manager has to ensure that all manufacturing processes work efficiently and effectively. They should be aware of any issues within the company and respond accordingly.
They should also know how to communicate with other departments such as sales and marketing.
They should also be aware of the latest trends in their industry and be able to use this information to help improve productivity and efficiency.
Statistics
- According to a Statista study, U.S. businesses spent $1.63 trillion on logistics in 2019, moving goods from origin to end user through various supply chain network segments. (netsuite.com)
- In the United States, for example, manufacturing makes up 15% of the economic output. (twi-global.com)
- Many factories witnessed a 30% increase in output due to the shift to electric motors. (en.wikipedia.org)
- Job #1 is delivering the ordered product according to specifications: color, size, brand, and quantity. (netsuite.com)
- (2:04) MTO is a production technique wherein products are customized according to customer specifications, and production only starts after an order is received. (oracle.com)
External Links
How To
How to Use 5S for Increasing Productivity in Manufacturing
5S stands in for "Sort", the "Set In Order", "Standardize", or "Separate". Toyota Motor Corporation was the first to develop the 5S approach in 1954. It improves the work environment and helps companies to achieve greater efficiency.
The basic idea behind this method is to standardize production processes, so they become repeatable, measurable, and predictable. This means that every day tasks such cleaning, sorting/storing, packing, and labeling can be performed. Through these actions, workers can perform their jobs more efficiently because they know what to expect from them.
Implementing 5S requires five steps. These are Sort, Set In Order, Standardize. Separate. And Store. Each step is a different action that leads to greater efficiency. If you sort items, it makes them easier to find later. When you arrange items, you place them together. Next, organize your inventory into categories and store them in containers that are easily accessible. Labeling your containers will ensure that everything is correctly labeled.
This process requires employees to think critically about how they do their job. Employees need to be able understand their motivations and discover alternative ways to do them. In order to use the 5S system effectively, they must be able to learn new skills.
The 5S Method not only improves efficiency, but it also helps employees to be more productive and happier. As they begin to see improvements, they feel motivated to continue working towards the goal of achieving higher levels of efficiency.