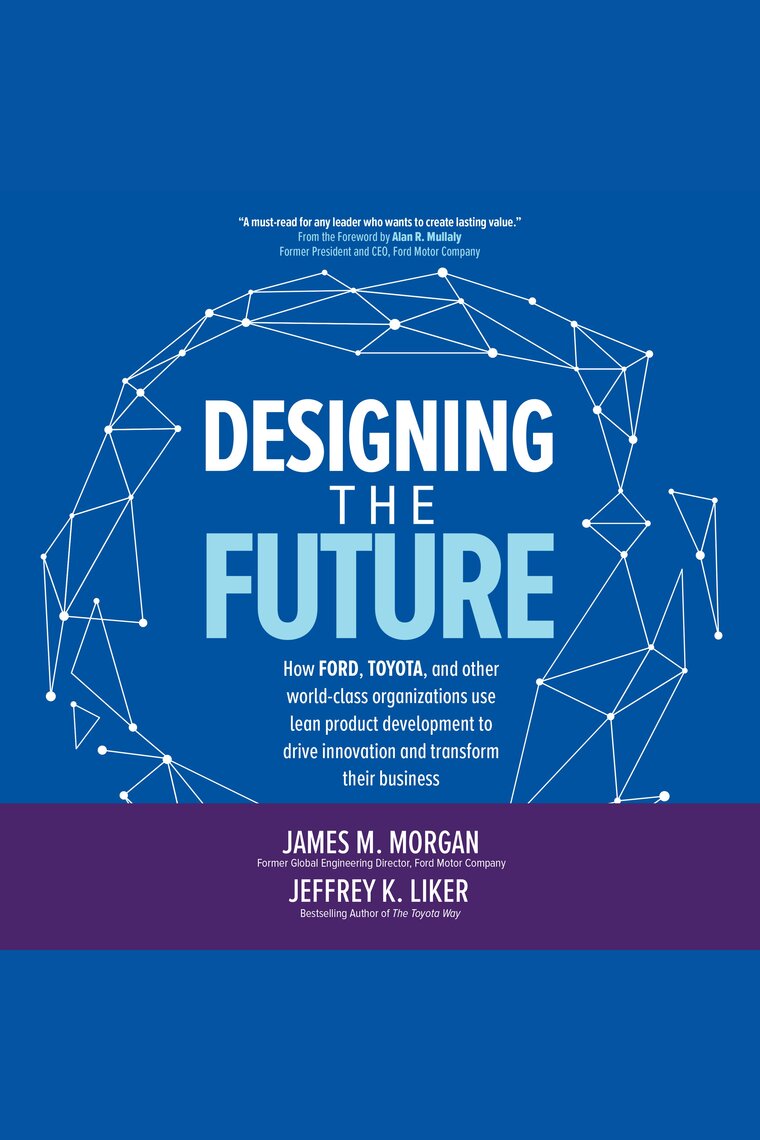
The Defense Industrial Base is a network of more that 200,000 companies who supply goods and service to the Department of Defense. It is made up of small businesses, large corporations, and startups. The Government Accountability Office has released a new report that highlights the risks and challenges facing the DIB, as well its efforts to address these.
In the past ten years, the defense industry base has dropped by nearly 40%. As a result, the Department of Defense has struggled to attract new entrants into the sector. The Defense Department has made a number of attempts to encourage businesses to join the sector. Despite these attempts, many smaller firms are being left behind. This has resulted in a growing threat to national security.
Diverse DOD offices are working on mitigation of risks in the DIB. However, the department has not developed a comprehensive strategy to assess and manage these risks. GAO conducted an analysis of several department reports and interviewed DOD representatives to determine where improvements could be made. GAO identified five elements which could help the department reach its goals.
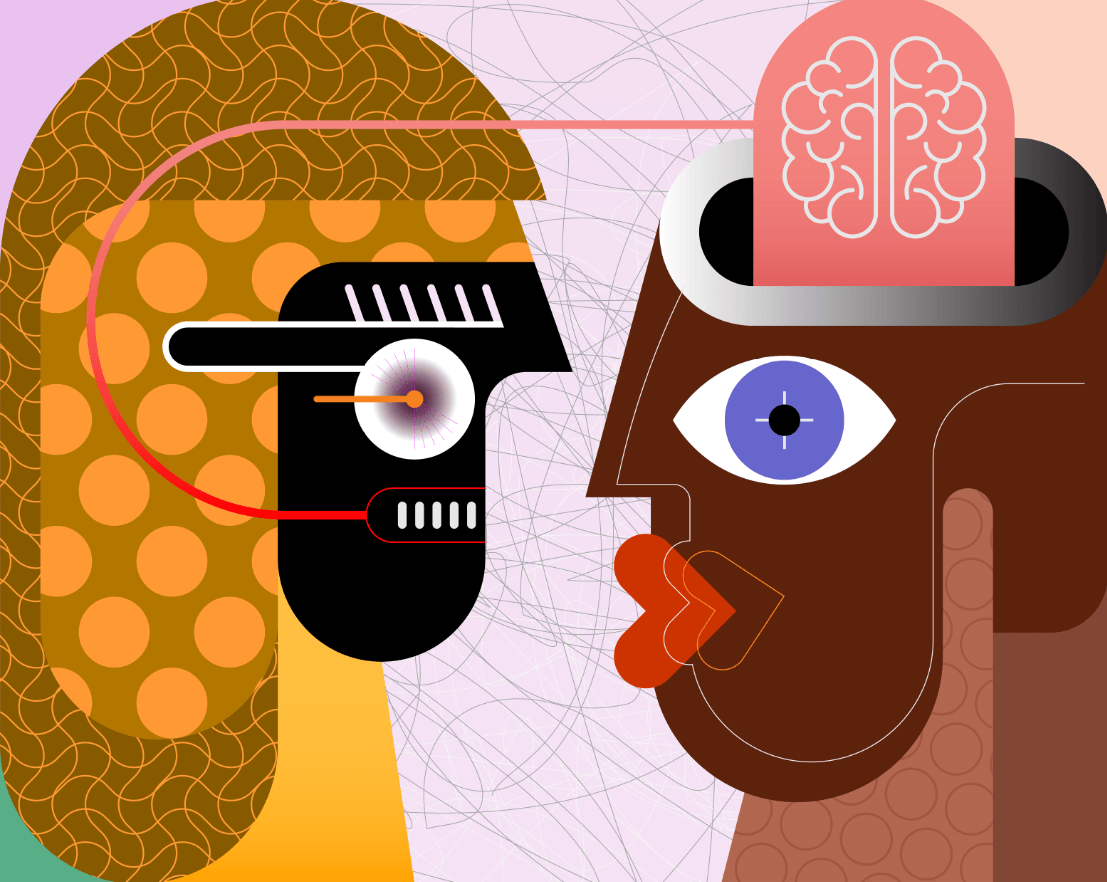
Loss or reduction of commercial suppliers is one concern. These businesses supply parts for the Pentagon's weapon systems. Over the last decade, the number of small businesses in this industry has declined. There is no clear indicator of how many new companies are entering this market.
Material shortages and dependence on foreign suppliers are two other issues. Additional problems include intellectual property restrictions that slow down the military's acquisitions process and a lack of standardization for what is considered "new entrant" to the defense industry base.
GAO recommended the Department of Defense revise its policy on mitigating the risks in the DIB. It is important that the department continues to engage traditional defense contractors, and develop tools that will allow commercial technology providers to gain access to the DoD marketplace. These suggestions should be part the overall strategy to address issues related to the industrial base.
As a part of this strategy, the Defense Department should consider how its OTAs and CSOs can be used to expedite acquisition strategy development. You can restructure the supply chain to achieve dynamic results by using the right people, processes and technologies.
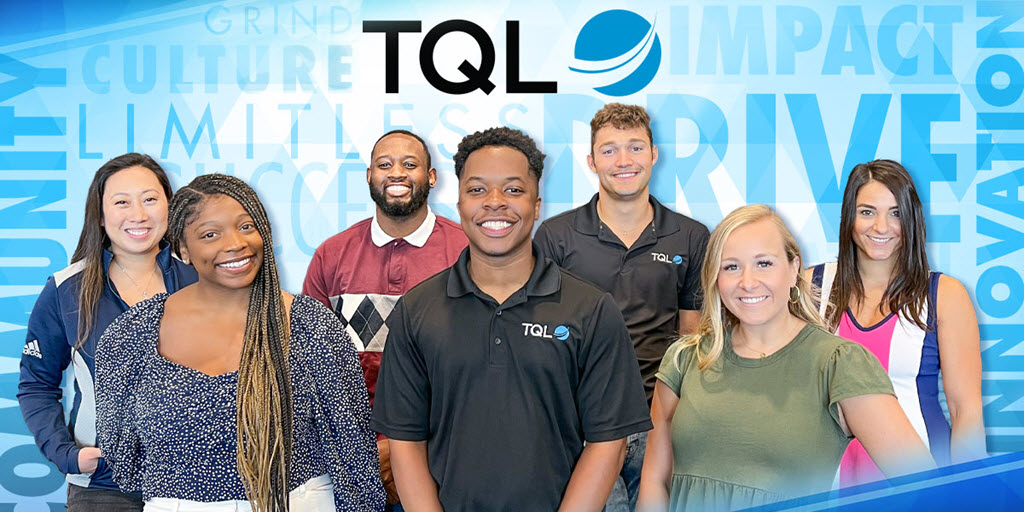
Although the number of new entrants into the defense industrial base has decreased over the last decade, the defense industry is still evolving. Many companies aren’t familiar with the Federal Acquisition Regulations process (FAR). The current landscape could also make it harder for small businesses to compete.
Small businesses and startups are crucial for innovation in the defense industrial base. Part of the resilient DIB, companies can support National Security needs while allowing Department of Defense to develop new and better military equipment.
The defense industrial base is complex and requires a comprehensive strategy in order to ensure that the resources are available for the military's needs. In the meantime, it is essential that the Department of Defense learn more about best practices for integrating technology into its business processes, which will allow for more efficient and innovative products and services.
FAQ
What are the main products of logistics?
Logistics is the process of moving goods from one point to another.
They include all aspects associated with transport including packaging, loading transporting, unloading storage, warehousing inventory management customer service, distribution returns and recycling.
Logisticians ensure that the product is delivered to the correct place, at the right time, and under safe conditions. They assist companies with their supply chain efficiency through information on demand forecasts. Stock levels, production times, and availability.
They monitor shipments in transit, ensure quality standards, manage inventories, replenish orders, coordinate with suppliers and other vendors, and offer support services for sales, marketing, and customer service.
How can manufacturing reduce production bottlenecks?
Avoiding production bottlenecks is as simple as keeping all processes running smoothly, from the time an order is received until the product ships.
This includes planning for capacity requirements as well as quality control measures.
Continuous improvement techniques like Six Sigma are the best way to achieve this.
Six Sigma can be used to improve the quality and decrease waste in all areas of your company.
It focuses on eliminating variation and creating consistency in your work.
Do we need to know about Manufacturing Processes before learning about Logistics?
No. No. However, knowing about manufacturing processes will definitely give you a better understanding of how logistics works.
How does a production planner differ from a project manager?
The major difference between a Production Planner and a Project Manager is that a Project Manager is often the person responsible for organizing and planning the entire project. While a Production Planner is involved mainly in the planning stage,
Statistics
- Many factories witnessed a 30% increase in output due to the shift to electric motors. (en.wikipedia.org)
- It's estimated that 10.8% of the U.S. GDP in 2020 was contributed to manufacturing. (investopedia.com)
- According to a Statista study, U.S. businesses spent $1.63 trillion on logistics in 2019, moving goods from origin to end user through various supply chain network segments. (netsuite.com)
- Job #1 is delivering the ordered product according to specifications: color, size, brand, and quantity. (netsuite.com)
- In the United States, for example, manufacturing makes up 15% of the economic output. (twi-global.com)
External Links
How To
How to Use Lean Manufacturing for the Production of Goods
Lean manufacturing is a management system that aims at increasing efficiency and reducing waste. It was created in Japan by Taiichi Ohno during the 1970s and 80s. He received the Toyota Production System award (TPS), from Kanji Toyoda, founder of TPS. The first book published on lean manufacturing was titled "The Machine That Changed the World" written by Michael L. Watkins and published in 1990.
Lean manufacturing is often described as a set if principles that help improve the quality and speed of products and services. It emphasizes the elimination of defects and waste throughout the value stream. Just-in-time (JIT), zero defect (TPM), and 5S are all examples of lean manufacturing. Lean manufacturing focuses on eliminating non-value-added activities such as rework, inspection, and waiting.
Lean manufacturing can help companies improve their product quality and reduce costs. Additionally, it helps them achieve their goals more quickly and reduces employee turnover. Lean manufacturing can be used to manage all aspects of the value chain. Customers, suppliers, distributors, retailers and employees are all included. Lean manufacturing is widely practiced in many industries around the world. Toyota's philosophy is the foundation of its success in automotives, electronics and appliances, healthcare, chemical engineers, aerospace, paper and food, among other industries.
Five basic principles of Lean Manufacturing are included in lean manufacturing
-
Define Value - Determine the value that your business brings to society. Also, identify what sets you apart from your competitors.
-
Reduce Waste - Remove any activity which doesn't add value to your supply chain.
-
Create Flow - Make sure work runs smoothly without interruptions.
-
Standardize & simplify - Make processes consistent and repeatable.
-
Build Relationships - Establish personal relationships with both internal and external stakeholders.
Although lean manufacturing isn't a new concept in business, it has gained popularity due to renewed interest in the economy after the 2008 global financial crisis. Many businesses have adopted lean production techniques to make them more competitive. According to some economists, lean manufacturing could be a significant factor in the economic recovery.
Lean manufacturing has many benefits in the automotive sector. These include improved customer satisfaction, reduced inventory levels, lower operating costs, increased productivity, and better overall safety.
Any aspect of an enterprise can benefit from Lean manufacturing. However, it is particularly useful when applied to the production side of an organization because it ensures that all steps in the value chain are efficient and effective.
There are three main types:
-
Just-in Time Manufacturing, (JIT): This kind of lean manufacturing is also commonly known as "pull-systems." JIT is a method in which components are assembled right at the moment of use, rather than being manufactured ahead of time. This approach is designed to reduce lead times and increase the availability of components. It also reduces inventory.
-
Zero Defects Manufacturing: ZDM ensures that no defective units leave the manufacturing plant. Repairing a part that is damaged during assembly should be done, not scrapping. This is also true for finished products that require minor repairs before shipping.
-
Continuous Improvement: Continuous Improvement aims to improve efficiency by continually identifying problems and making adjustments to eliminate or minimize waste. Continuous Improvement (CI) involves continuous improvement in processes, people, tools, and infrastructure.