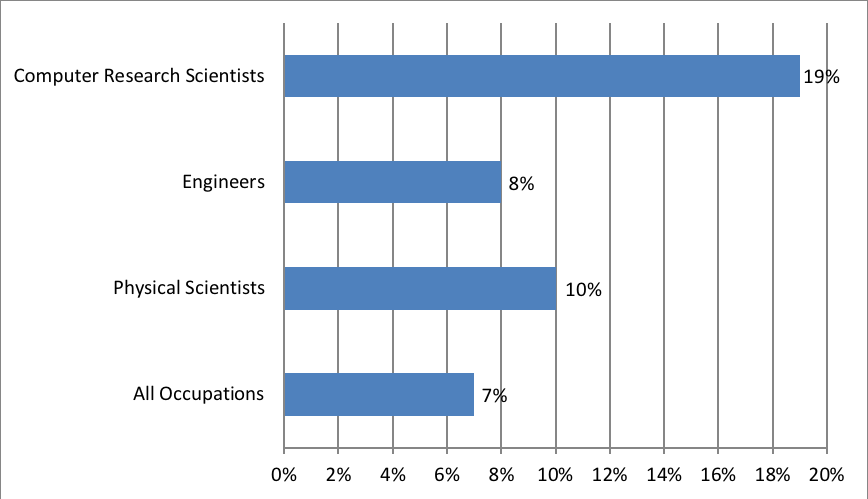
An artisan who works in the production process of chemical products is called a Chemical Technician. He or she also conducts tests on the materials used during manufacturing. They may work in research and development, in manufacturing lines or laboratories.
They are often supervised by chemists. They monitor the product's quality, test new materials, and collect samples. As they gain experience, they may be promoted. Pharmaceutical manufacturers are some of the companies that employ them. A bachelor's degree in engineering, biology, and chemistry can help you earn more.
The average salary for a Chemical Technician is $48,990. Although pay for this job can vary by region, it is the median. This includes taxable salaries and bonuses. This includes the worker's education, skills, experience, and other factors. The highest earning Chemical Technicians earned more than $60,000 per year.
As a Chemical Technician, you will be responsible for conducting research and developing new chemicals and pharmaceuticals. They are responsible for analysing the ingredients of pharmaceuticals, food, as well as other products. They can also supervise workers in the production line.
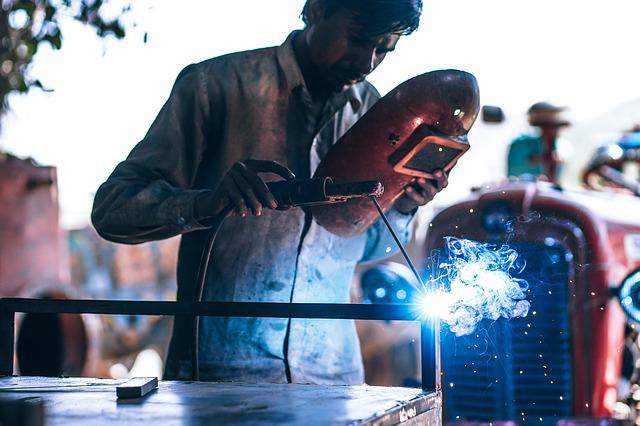
You will need an associate's/bachelor's degree to be a Chemical Technician. A graduate or doctoral degree is also possible. Some companies prefer to hire chemical technicians with college degrees. A master's degree may be required for other jobs.
You can learn more about the employment opportunities available by visiting a school placement office. There are many job banks available online. The American Chemical Society is another good resource. Local chapters often have job postings.
Looking for a job to be a Chemical Technician? You need to be able to work long hours. Many laboratories operate on a seven day schedule. However, skilled workers are often called in to conduct odd-hours inspections of experiments.
Most of the Chemical Technicians' salaries range between $36,000 and $47,000. Experienced workers can earn up to $11,000 more. Entry-level workers earn between $15 and 18 an hour.
Among the major cities in the United States, the San Francisco and San Jose area are at the top of the list for Chemical Technician salaries. Both cities outperformed the national average by more than 20%. In addition, the BLS reported that Chemical Technicians in these areas earned more than $83,600.
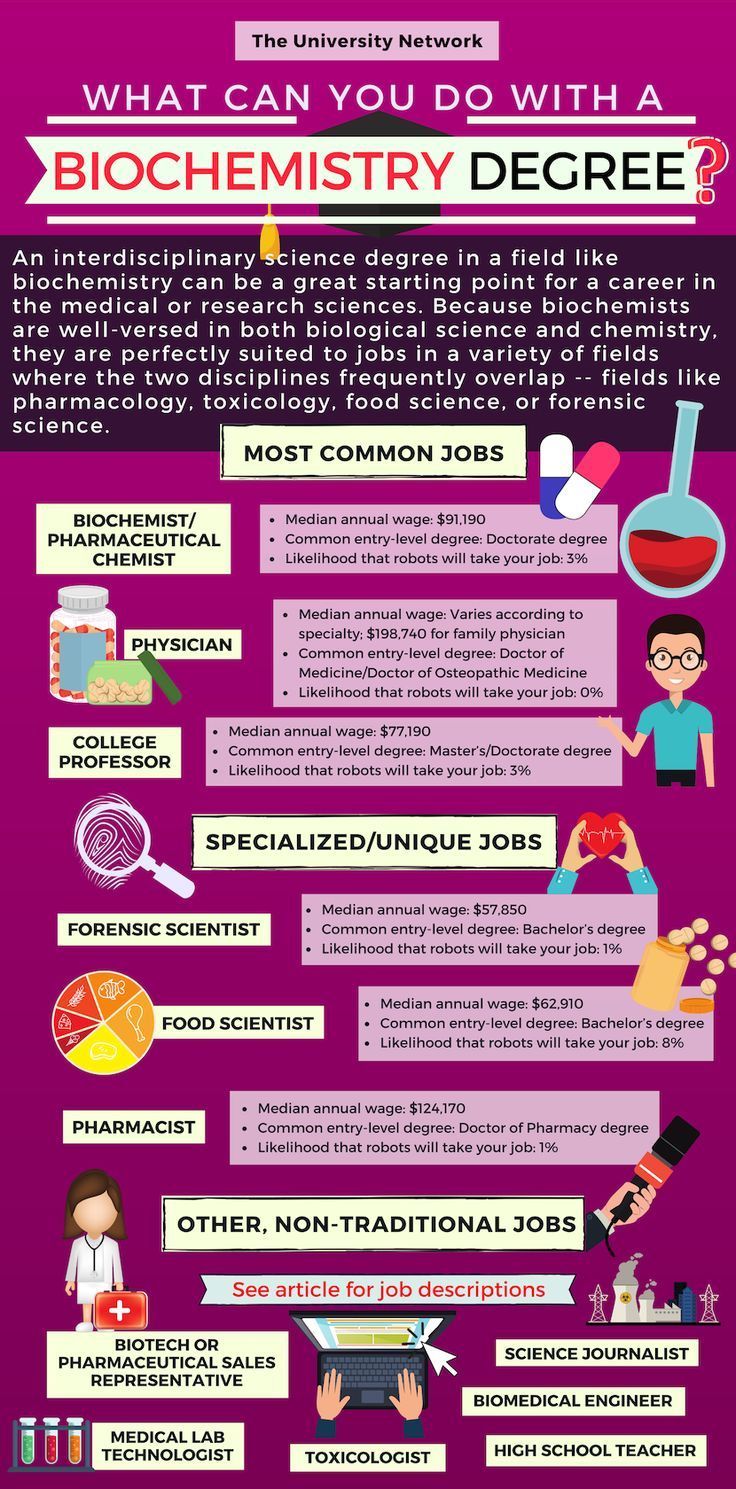
According to the Bureau of Labor Statistics, Chemical Technicians are expected to see a slower growth rate than average in terms of job opportunities. Although their employment is expected to grow by 3 percent through 2014, the number of jobs will increase by only 4 percent over the next ten years. This will likely lead to a higher demand for skilled technicians.
Chemical R&D will be in high demand as environmental issues continue to grow. These workers will have the best jobs in laboratories where they can test new materials.
FAQ
What is the difference between Production Planning, Scheduling and Production Planning?
Production Planning (PP), is the process of deciding what production needs to take place at any given time. This is done through forecasting demand and identifying production capacities.
Scheduling refers to the process of allocating specific dates to tasks in order that they can be completed within a specified timeframe.
What are the main products of logistics?
Logistics refers to the movement of goods from one place to another.
They encompass all aspects transport, including packaging and loading, transporting, storage, unloading.
Logisticians make sure that the right product arrives at the right place at the correct time and in safe conditions. They help companies manage their supply chain efficiency by providing information on demand forecasts, stock levels, production schedules, and availability of raw materials.
They monitor shipments in transit, ensure quality standards, manage inventories, replenish orders, coordinate with suppliers and other vendors, and offer support services for sales, marketing, and customer service.
How can manufacturing efficiency be improved?
The first step is to determine the key factors that impact production time. The next step is to identify the most important factors that affect production time. You can start by identifying the most important factors that impact production time. Once you have identified them, it is time to identify solutions.
What does the term manufacturing industries mean?
Manufacturing Industries is a group of businesses that produce goods for sale. Consumers are people who purchase these goods. These companies use various processes such as production, distribution, retailing, management, etc., to fulfill this purpose. They make goods from raw materials with machines and other equipment. This includes all types if manufactured goods.
Statistics
- According to the United Nations Industrial Development Organization (UNIDO), China is the top manufacturer worldwide by 2019 output, producing 28.7% of the total global manufacturing output, followed by the United States, Japan, Germany, and India.[52][53] (en.wikipedia.org)
- Job #1 is delivering the ordered product according to specifications: color, size, brand, and quantity. (netsuite.com)
- Many factories witnessed a 30% increase in output due to the shift to electric motors. (en.wikipedia.org)
- (2:04) MTO is a production technique wherein products are customized according to customer specifications, and production only starts after an order is received. (oracle.com)
- You can multiply the result by 100 to get the total percent of monthly overhead. (investopedia.com)
External Links
How To
How to Use Six Sigma in Manufacturing
Six Sigma is defined by "the application SPC (statistical process control) techniques to achieve continuous improvements." Motorola's Quality Improvement Department, Tokyo, Japan, developed it in 1986. The basic idea behind Six Sigma is to improve quality by improving processes through standardization and eliminating defects. This method has been adopted by many companies in recent years as they believe there are no perfect products or services. The main goal of Six Sigma is to reduce variation from the mean value of production. This means that if you take a sample of your product, then measure its performance against the average, you can find out what percentage of the time the process deviates from the norm. If it is too large, it means that there are problems.
Understanding the nature of variability in your business is the first step to Six Sigma. Once you have this understanding, you will need to identify sources and causes of variation. You'll also want to determine whether these variations are random or systematic. Random variations are caused by human errors. Systematic variations can be caused by outside factors. These are, for instance, random variations that occur when widgets are made and some fall off the production line. It would be considered a systematic problem if every widget that you build falls apart at the same location each time.
Once you have identified the problem, you can design solutions. You might need to change the way you work or completely redesign the process. You should then test the changes again after they have been implemented. If they don't work you need to rework them and come up a better plan.