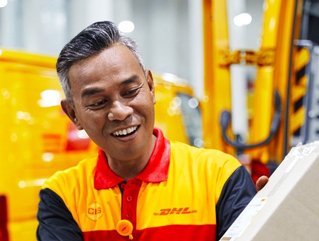
The list of manufacturers by state reveals a surprising trend: the usual suspects, such as the southeastern states, are near the top of the list. However, this trend is changing. Many states have shown that they can make tradeoffs between quality and cost to get the best deals. This trend shows that there are many factors that determine a state's ability to attract manufacturing jobs. How can you decide the right location to start your business?
Group Five
If you're looking for a list of Group Five manufacturers by state, then you've come to the right place. Group Five's product portfolio includes steel pipes, industrial engineering products, and structural components. The company provides pipe design services that offer the best price-to quality ratio for steel grade and thickness, as well as stiffening thin-walled pipes. The company makes use of the most recent CAD systems to design your pipes.
Group Three
According to the United States Census Bureau there are roughly 50,000 manufacturers in Group Three. It has a low unemployment rate and a high rate economic growth. However it also has a low GDP growth rate. This is because the majority of manufacturers in this group have small businesses. These limitations aside, data can still be useful. Listed below are the top manufacturers in each state. Continue reading to learn more.
Audi, Mercedes-Benz, and BMW are the biggest three manufacturers in Europe. Honda and Toyota have dropped to fifth and sixth, respectively. However, the Detroit Three have reclaimed the Big Three title. Below is a table listing these carmakers along with their sales in each state. Click the link to see the state's top-selling vehicle. There are many models available from these manufacturers, including SUVs and midsize sedans as well as minivans.
FAQ
How can manufacturing avoid production bottlenecks
Avoiding production bottlenecks is as simple as keeping all processes running smoothly, from the time an order is received until the product ships.
This includes planning for both capacity requirements and quality control measures.
Continuous improvement techniques such Six Sigma can help you achieve this.
Six Sigma Management System is a method to increase quality and reduce waste throughout your organization.
It's all about eliminating variation and creating consistency in work.
What are the goods of logistics?
Logistics refers to all activities that involve moving goods from A to B.
They include all aspects associated with transport including packaging, loading transporting, unloading storage, warehousing inventory management customer service, distribution returns and recycling.
Logisticians ensure that products reach the right destination at the right moment and under safe conditions. Logisticians help companies improve their supply chain efficiency by providing information about demand forecasts and stock levels, production schedules, as well as availability of raw materials.
They monitor shipments in transit, ensure quality standards, manage inventories, replenish orders, coordinate with suppliers and other vendors, and offer support services for sales, marketing, and customer service.
How can manufacturing efficiency improved?
The first step is to identify the most important factors affecting production time. Next, we must find ways to improve those factors. If you don’t know how to start, look at which factors have the greatest impact upon production time. Once you have identified them, it is time to identify solutions.
Can some manufacturing processes be automated?
Yes! Since ancient times, automation has been in existence. The Egyptians created the wheel thousands years ago. To help us build assembly lines, we now have robots.
Actually, robotics can be used in manufacturing for many purposes. These include:
-
Automation line robots
-
Robot welding
-
Robot painting
-
Robotics inspection
-
Robots that produce products
Automation can be applied to manufacturing in many other ways. For example, 3D printing allows us to make custom products without having to wait for weeks or months to get them manufactured.
What is the role of a manager in manufacturing?
A manufacturing manager must make sure that all manufacturing processes run smoothly and effectively. They should also be aware and responsive to any company problems.
They should also be able communicate with other departments, such as sales or marketing.
They must also keep up-to-date with the latest trends in their field and be able use this information to improve productivity and efficiency.
What is meant by manufacturing industries?
Manufacturing Industries are companies that manufacture products. These products are sold to consumers. To accomplish this goal, these companies employ a range of processes including distribution, sales, management, and production. They manufacture goods from raw materials using machines and other equipment. This includes all types if manufactured goods.
Why is logistics so important in manufacturing?
Logistics are essential to any business. They are essential to any business's success.
Logistics plays a significant role in reducing cost and increasing efficiency.
Statistics
- (2:04) MTO is a production technique wherein products are customized according to customer specifications, and production only starts after an order is received. (oracle.com)
- [54][55] These are the top 50 countries by the total value of manufacturing output in US dollars for its noted year according to World Bank.[56] (en.wikipedia.org)
- Many factories witnessed a 30% increase in output due to the shift to electric motors. (en.wikipedia.org)
- Job #1 is delivering the ordered product according to specifications: color, size, brand, and quantity. (netsuite.com)
- According to a Statista study, U.S. businesses spent $1.63 trillion on logistics in 2019, moving goods from origin to end user through various supply chain network segments. (netsuite.com)
External Links
How To
How to Use the Just In Time Method in Production
Just-intime (JIT), which is a method to minimize costs and maximize efficiency in business process, is one way. It is a process where you get the right amount of resources at the right moment when they are needed. This means that your only pay for the resources you actually use. Frederick Taylor developed the concept while working as foreman in early 1900s. He noticed that workers were often paid overtime when they had to work late. He decided that workers would be more productive if they had enough time to complete their work before they started to work.
JIT is a way to plan ahead and make sure you don't waste any money. Look at your entire project, from start to end. Make sure you have enough resources in place to deal with any unexpected problems. You'll be prepared to handle any potential problems if you know in advance. This will ensure that you don't spend more money on things that aren't necessary.
There are many JIT methods.
-
Demand-driven: This is a type of JIT where you order the parts/materials needed for your project regularly. This will allow for you to track the material that you have left after using it. This will allow to you estimate the time it will take for more to be produced.
-
Inventory-based: This is a type where you stock the materials required for your projects in advance. This allows you to predict how much you can expect to sell.
-
Project-driven: This means that you have enough money to pay for your project. When you know how much you need, you'll purchase the appropriate amount of materials.
-
Resource-based JIT: This type of JIT is most commonly used. You assign certain resources based off demand. For example, if there is a lot of work coming in, you will have more people assigned to them. If there aren't many orders, you will assign fewer people.
-
Cost-based: This is similar to resource-based, except that here you're not just concerned about how many people you have but how much each person costs.
-
Price-based pricing: This is similar in concept to cost-based but instead you look at how much each worker costs, it looks at the overall company's price.
-
Material-based - This is a variant of cost-based. But instead of looking at the total company cost, you focus on how much raw material you spend per year.
-
Time-based JIT: A variation on resource-based JIT. Instead of focusing solely on the amount each employee costs, focus on how long it takes for the project to be completed.
-
Quality-based JIT - This is another form of resource-based JIT. Instead of focusing on the cost of each worker or how long it takes, think about how high quality your product is.
-
Value-based JIT: One of the most recent forms of JIT. In this instance, you are not concerned about the product's performance or meeting customer expectations. Instead, you focus on the added value that you provide to your market.
-
Stock-based is an inventory-based system that measures the number of items produced at any given moment. This is used to increase production and minimize inventory.
-
Just-in-time (JIT) planning: This is a combination of JIT and supply chain management. It is the process of scheduling components' delivery as soon as they have been ordered. It's important as it reduces leadtimes and increases throughput.