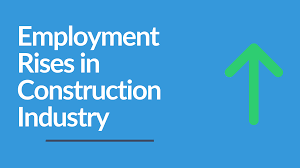
To be a safety engineer, you must have a bachelor's in engineering or science. Along with a degree in engineering or science, you must also be able work well with others. You may also need to earn additional certifications.
You will learn about the different regulations and procedures that safety engineers must follow during training. Also, you'll learn how to spot potential hazards and investigate accident reports. You will learn how to test, evaluate, and report on machinery, buildings, and consumer goods. You will also be able to prepare safety protocols and reports. You will learn how you can conduct routine compliance inspections, and prepare safety and occupational health programs.
Safety engineers are usually under the direct supervision of more experienced engineers. You may also join professional safety engineering networks such as the American Society of Safety Professionals. This is a great way for you to meet people in your field. You can also use this opportunity to meet experienced safety engineers and learn from them. Keep your resume current with your qualifications if you plan to become a safety engineer.
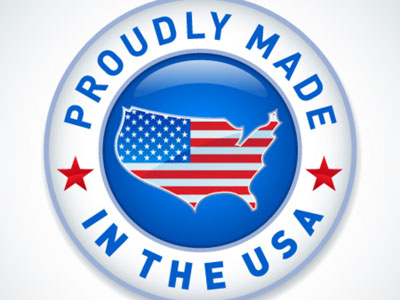
Once you have completed your bachelor's degree, you may want to consider getting a master's degree in health and safety. This will help you be more competitive on the job market. You can also use a master's to rise to a higher level in your industry.
Your master's program will teach you how to create safety systems and implement organizational-wide procedures. Additionally, you will acquire advanced planning and analysis skills. This will prepare you to work on more complex projects and will allow you to advance to a higher position. You can also use your master's to apply for managerial positions in health and safety.
Cooperative education is offered by many colleges and universities. These programs allow you to earn a bachelor's degree and gain practical experience at the same time. This allows you to apply for jobs that are more difficult to get without the degree. Many of these programs allow students to take part-time classes, while others allow them to work full time while they earn their degree.
To work as a safety engineer, you will need to have a bachelor's degree. Most states will issue a license. A state examination will be required and you must have at least four years' experience in your field. You may also need to take a course in workplace health.
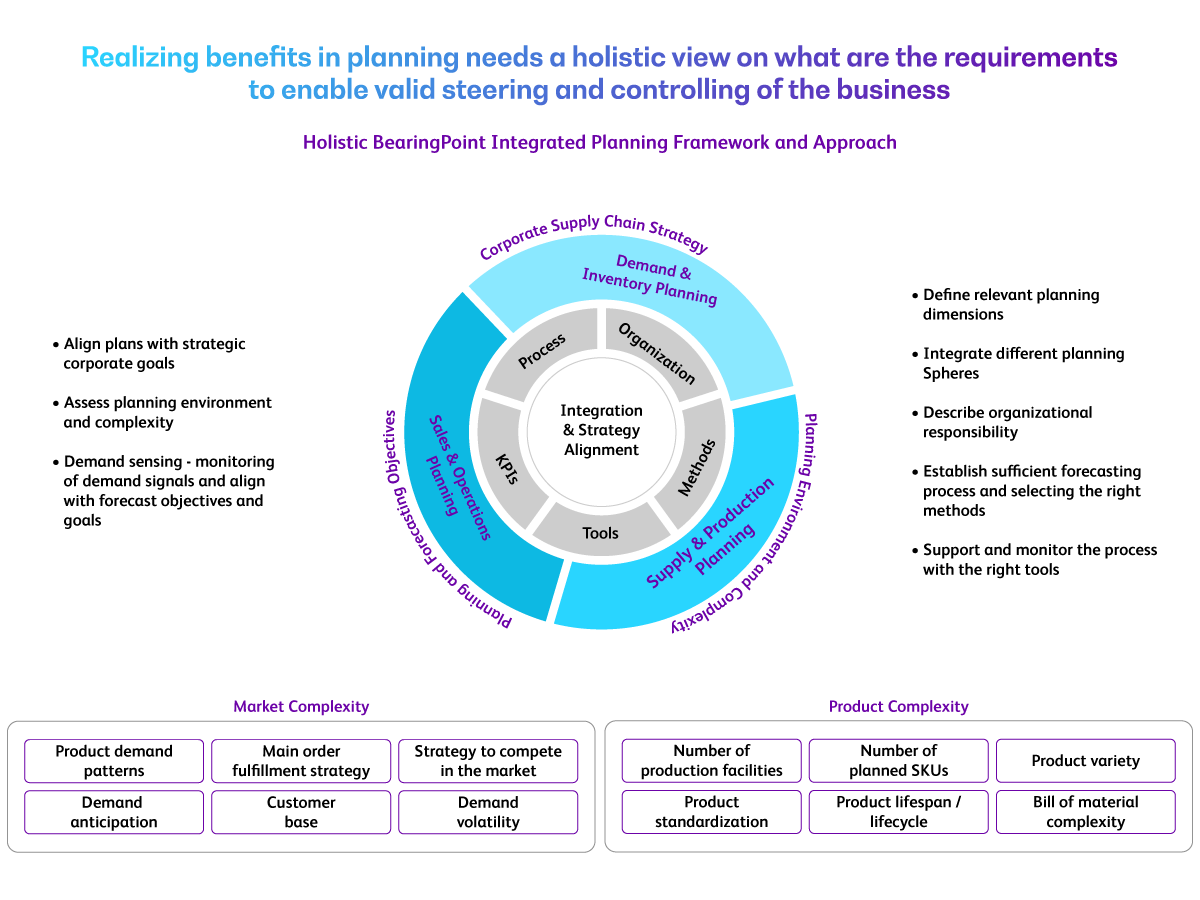
Employers will often prefer to hire people with experience after you have been licensed. Many schools offer cooperative education programs, and some allow students to take classes part-time. You can also search online for employment. You might consider joining professional organizations like the American Society of Safety Engineers. You can also join the Institute of Hazardous Materials Management, which helps safety professionals to develop leadership skills.
Safety and health engineering are exciting career options. It requires great skills in science, math, and communication. Also, you must be creative and skilled at solving difficult problems.
FAQ
What are the responsibilities of a logistic manager?
Logistics managers are responsible for ensuring that all goods arrive in perfect condition and on time. This is done through his/her expertise and knowledge about the company's product range. He/she should make sure that enough stock is on hand to meet the demands.
Can certain manufacturing steps be automated?
Yes! Since ancient times, automation has been in existence. The Egyptians discovered the wheel thousands and years ago. To help us build assembly lines, we now have robots.
There are many uses of robotics today in manufacturing. These include:
-
Automated assembly line robots
-
Robot welding
-
Robot painting
-
Robotics inspection
-
Robots that create products
There are many other examples of how manufacturing could benefit from automation. 3D printing makes it possible to produce custom products in a matter of days or weeks.
How can manufacturing efficiency improved?
The first step is to determine the key factors that impact production time. Then we need to find ways to improve these factors. If you don’t know how to start, look at which factors have the greatest impact upon production time. Once you've identified them, try to find solutions for each of those factors.
Why is logistics important in manufacturing?
Logistics are an integral part any business. They are essential to any business's success.
Logistics play an important role in reducing costs as well as increasing efficiency.
What are the 7 Rs of logistics.
The acronym 7R's of Logistic is an acronym that stands for seven fundamental principles of logistics management. It was developed and published by the International Association of Business Logisticians in 2004 as part of the "Seven Principles of Logistics Management".
The following letters form the acronym:
-
Responsible - ensure that all actions taken are within legal requirements and are not harmful to others.
-
Reliable - Have confidence in your ability to fulfill all of your commitments.
-
It is reasonable to use resources efficiently and not waste them.
-
Realistic – Consider all aspects, including cost-effectiveness as well as environmental impact.
-
Respectful - treat people fairly and equitably.
-
Be resourceful: Look for opportunities to save money or increase productivity.
-
Recognizable is a company that provides customers with value-added solutions.
What is production planning?
Production Planning includes planning for all aspects related to production. This document aims to ensure that everything is planned and ready when you are ready to shoot. This document should include information about how to achieve the best results on-set. This includes shooting schedules, locations, cast lists, crew details, and equipment requirements.
The first step is to outline what you want to film. You might have an idea of where you want to film, or you may have specific locations or sets in mind. Once you've identified the locations and scenes you want to use, you can begin to plan what elements you need for each scene. For example, you might decide that you need a car but don't know exactly what model you want. To narrow your options, you can search online for available models.
After you have selected the car you want, you can begin to think about additional features. Do you have people who need to be seated in the front seat? Or maybe you just need someone to push the car around. You may want to change the interior's color from black or white. These questions will help determine the look and feel you want for your car. It is also worth considering the types of shots that you wish to take. Are you going to be shooting close-ups? Or wide angles? Maybe you want the engine or the steering wheels to be shown. All of these things will help you identify the exact style of car you want to film.
Once you have determined all of the above, you can move on to creating a schedule. You can use a schedule to determine when and where you need it to be shot. A schedule for each day will detail when you should arrive at the location and when you need leave. It will help everyone know exactly what they have to do and when. Hire extra staff by booking them ahead of time. You don't want to hire someone who won't show up because he didn't know.
You will need to factor in the days that you have to film when creating your schedule. Some projects only take one or two days, while others may last weeks. While creating your schedule, it is important to remember whether you will require more than one shot per day. Multiple shots at the same location can increase costs and make it more difficult to complete. It's better to be safe than sorry and shoot less takes if you're not certain whether you need more takes.
Budgeting is another important aspect of production planning. Setting a realistic budget is essential as it will allow you to work within your means. It is possible to reduce the budget at any time if you experience unexpected problems. You shouldn't underestimate the amount you'll spend. If you underestimate the cost of something, you will have less money left after paying for other items.
Production planning is a very detailed process, but once you understand how everything works together, it becomes easier to plan future projects.
Statistics
- (2:04) MTO is a production technique wherein products are customized according to customer specifications, and production only starts after an order is received. (oracle.com)
- In 2021, an estimated 12.1 million Americans work in the manufacturing sector.6 (investopedia.com)
- Many factories witnessed a 30% increase in output due to the shift to electric motors. (en.wikipedia.org)
- You can multiply the result by 100 to get the total percent of monthly overhead. (investopedia.com)
- According to the United Nations Industrial Development Organization (UNIDO), China is the top manufacturer worldwide by 2019 output, producing 28.7% of the total global manufacturing output, followed by the United States, Japan, Germany, and India.[52][53] (en.wikipedia.org)
External Links
How To
How to use lean manufacturing in the production of goods
Lean manufacturing is an approach to management that aims for efficiency and waste reduction. It was developed by Taiichi Okono in Japan, during the 1970s & 1980s. TPS founder Kanji Takoda awarded him the Toyota Production System Award (TPS). Michael L. Watkins published the "The Machine That Changed the World", the first book about lean manufacturing. It was published in 1990.
Lean manufacturing, often described as a set and practice of principles, is aimed at improving the quality, speed, cost, and efficiency of products, services, and other activities. It is about eliminating defects and waste from all stages of the value stream. Just-in-time (JIT), zero defect (TPM), and 5S are all examples of lean manufacturing. Lean manufacturing emphasizes reducing non-value-added activities like inspection, rework and waiting.
Lean manufacturing is a way for companies to achieve their goals faster, improve product quality, and lower costs. Lean manufacturing is considered one of the most effective ways to manage the entire value chain, including suppliers, customers, distributors, retailers, and employees. Lean manufacturing practices are widespread in many industries. Toyota's philosophy is a great example of this. It has helped to create success in automobiles as well electronics, appliances and healthcare.
Five fundamental principles underlie lean manufacturing.
-
Define Value - Determine the value that your business brings to society. Also, identify what sets you apart from your competitors.
-
Reduce Waste – Eliminate all activities that don't add value throughout the supply chain.
-
Create Flow: Ensure that the work process flows without interruptions.
-
Standardize and simplify – Make processes as repeatable and consistent as possible.
-
Develop Relationships: Establish personal relationships both with internal and external stakeholders.
Lean manufacturing is not a new concept, but it has been gaining popularity over the last few years due to a renewed interest in the economy following the global financial crisis of 2008. To increase their competitiveness, many businesses have turned to lean manufacturing. Economists think that lean manufacturing is a crucial factor in economic recovery.
Lean manufacturing is becoming a popular practice in automotive. It has many advantages. These include improved customer satisfaction, reduced inventory levels, lower operating costs, increased productivity, and better overall safety.
The principles of lean manufacturing can be applied in almost any area of an organization. Because it makes sure that all value chains are efficient and effectively managed, Lean Manufacturing is particularly helpful for organizations.
There are three main types of lean manufacturing:
-
Just-in Time Manufacturing (JIT), also known as "pull system": This form of lean manufacturing is often referred to simply as "pull". JIT means that components are assembled at the time of use and not manufactured in advance. This approach is designed to reduce lead times and increase the availability of components. It also reduces inventory.
-
Zero Defects Manufacturing: ZDM ensures that no defective units leave the manufacturing plant. Repairing a part that is damaged during assembly should be done, not scrapping. This applies to finished products, which may need minor repairs before they are shipped.
-
Continuous Improvement (CI),: Continuous improvement aims improve the efficiency and effectiveness of operations by continuously identifying issues and making changes to reduce waste. Continuous Improvement (CI) involves continuous improvement in processes, people, tools, and infrastructure.