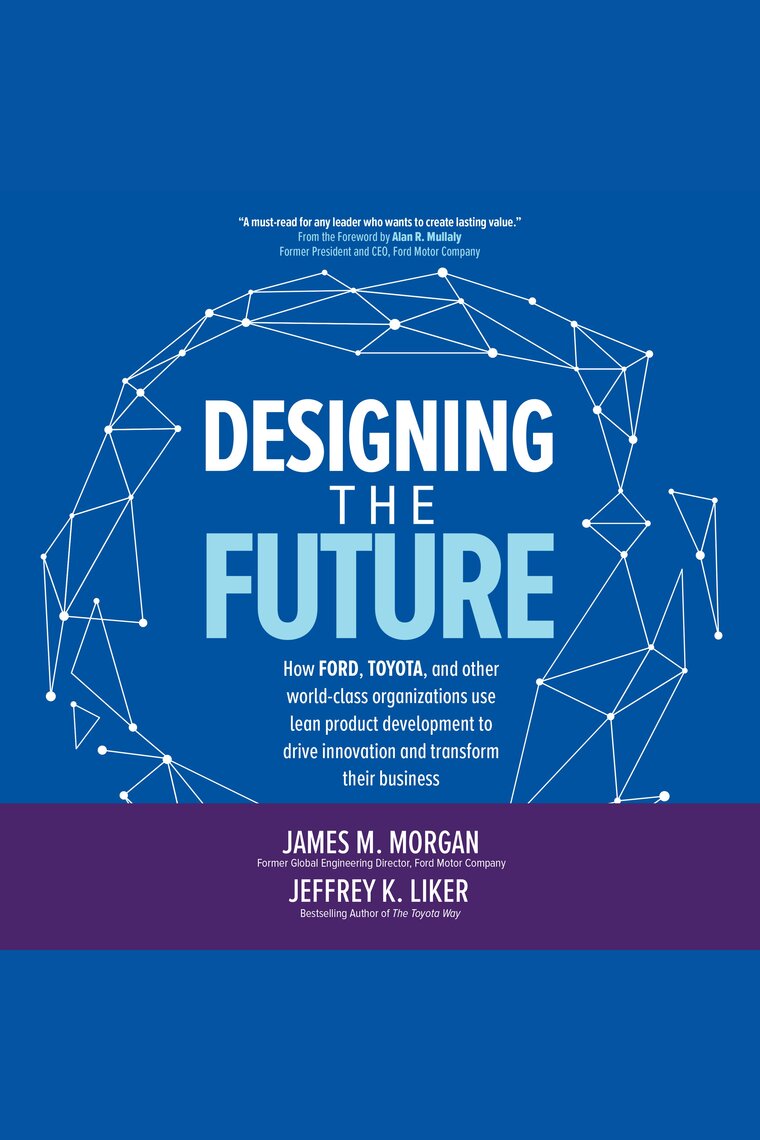
Just-in–time production is a system of principles and practices that businesses use to produce goods in a timely manner. This method relies on high quality controls and efficient workflows during the manufacturing process. It allows manufacturers lower inventory levels and less warehouse space. These benefits come with lower costs.
JIT is a method that has helped many companies to lower their overall costs. However, it can be difficult to implement. Not only does it require coordination in operations but it also depends on the function of the supply network. This makes it vulnerable to disruptions on the global economy or logistics. There are many tools that can help you manage the JIT challenges.
JIT can drastically reduce costs when implemented correctly. It can also improve the quality and performance of the final product. This technique can also improve the efficiency of both machine and human labor. This method also improves the efficiency and speed of the production cycle. It reduces the time required to process non-essential output and will therefore have a positive impact on the environment.
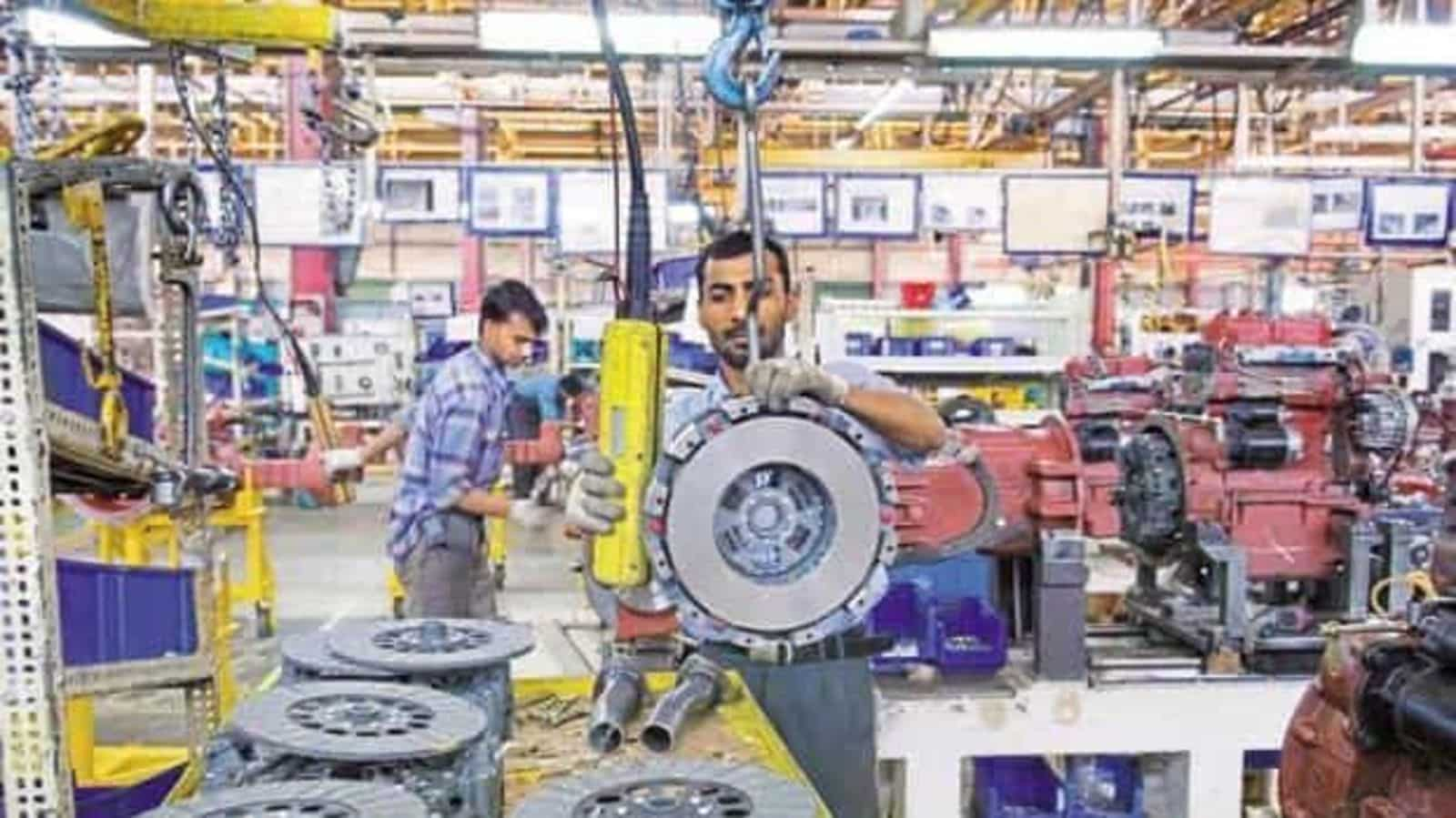
In Japan, the concept for just-intime production was first introduced with the advent of lean manufacturing. After World War II ended, Japanese organisations were forced to depend on limited resources. To survive, they needed to streamline their manufacturing processes. They used JIT methods to get the maximum output.
Toyota's management team adapt the technique to transform their production from a questionable test case into an example of success. This was achieved in just a few decades. This was a method that became so popular that other Japanese companies started to pay attention.
JIT is becoming a well-known technique in the Japanese market due to its effectiveness. The risks and benefits of JIT implementation should be understood by manufacturers before they embark on this project. It is important to establish strong relationships with suppliers in order for a JIT implementation to be successful. Suppliers can reduce stock-keeping and speed up deliveries.
There are two main types of JIT methods. Pull and push. Push is the traditional Make to Stock method of manufacturing. However, push puts pressure on the other areas of your business. Moreover, the cost of retooling can be high. Similarly, the pull method is based on the actual demand for the products.
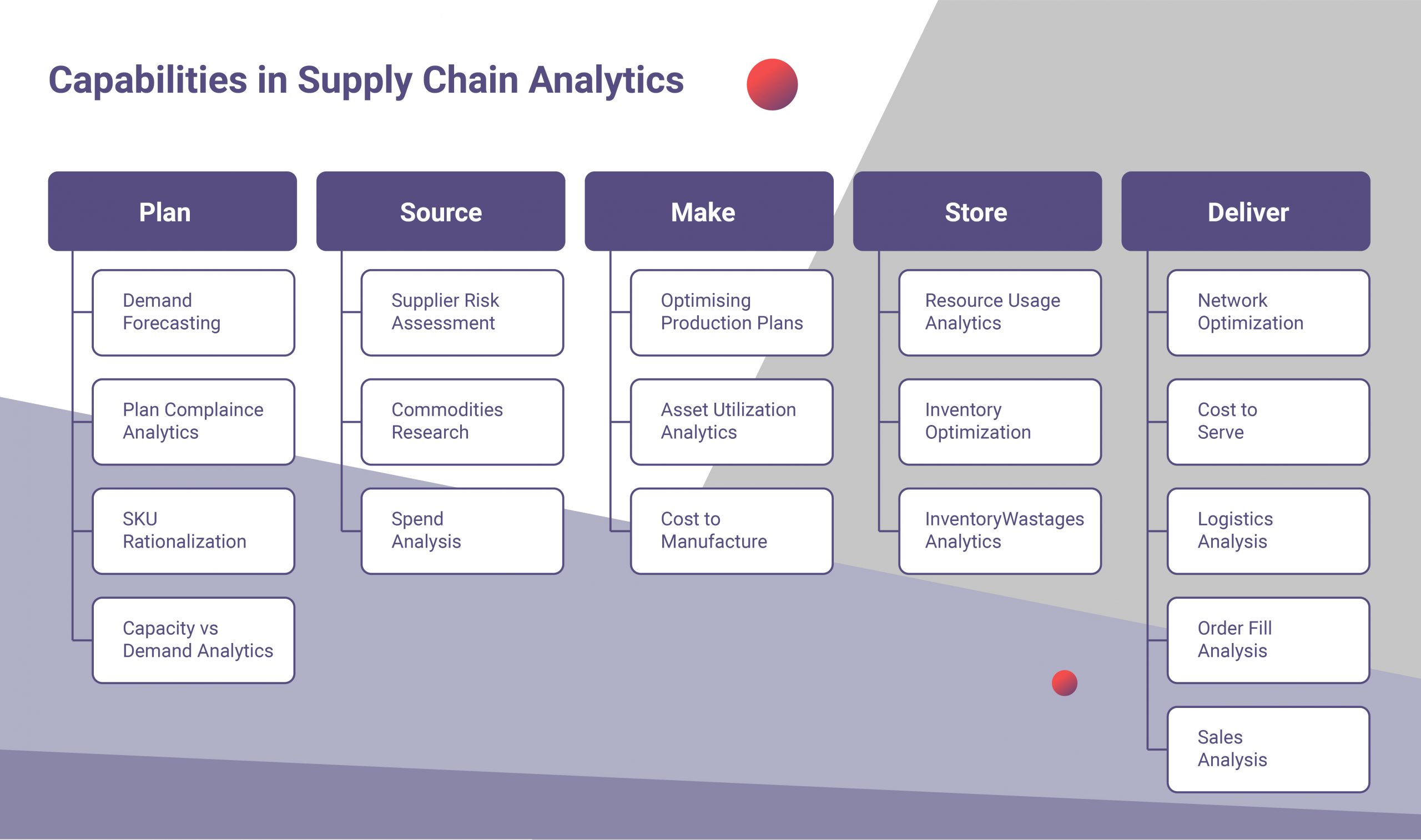
Many companies worldwide have successfully used these two methods. It is important that workers are empowered to solve quality issues. This is key to successful implementation. JIT's effectiveness is also affected by factors such as complexity in manufacturing processes and length of time between supplier deliveries and manufacturer deliveries.
Ideally, a firm should not have a stock of finished products or raw materials. If it does, it should only have a limited number of reusable containers that are called kanban.
JIT is not only focused on reducing waste but also strives to maximize the efficiency both of human and machine labor. It is vital to detect and resolve any quality problems as soon as they occur.
FAQ
Is it possible to automate certain parts of manufacturing
Yes! Since ancient times, automation has been in existence. The Egyptians invent the wheel thousands of year ago. Today, robots assist in the assembly of lines.
In fact, there are several applications of robotics in manufacturing today. These include:
-
Automation line robots
-
Robot welding
-
Robot painting
-
Robotics inspection
-
Robots that create products
There are many other examples of how manufacturing could benefit from automation. For instance, 3D printing allows us make custom products and not have to wait for months or even weeks to get them made.
What is the role and responsibility of a Production Planner?
A production planner makes sure all project elements are delivered on schedule, within budget, as well as within the agreed scope. They make sure that the product and services meet client expectations.
How can excess manufacturing production be reduced?
The key to reducing overproduction lies in developing better ways to manage inventory. This would decrease the time that is spent on inefficient activities like purchasing, storing, or maintaining excess stock. This could help us free up our time for other productive tasks.
You can do this by adopting a Kanban method. A Kanban board can be used to monitor work progress. Kanban systems allow work items to move through different states until they reach their final destination. Each state has a different priority level.
When work is completed, it can be transferred to the next stage. If a task is still in its beginning stages, it will continue to be so until it reaches the end.
This allows work to move forward and ensures that no work is missed. A Kanban board allows managers to monitor how much work is being completed at any given moment. This allows them the ability to adjust their workflow using real-time data.
Lean manufacturing, another method to control inventory levels, is also an option. Lean manufacturing emphasizes eliminating waste in all phases of production. Any product that isn't adding value can be considered waste. The following are examples of common waste types:
-
Overproduction
-
Inventory
-
Unnecessary packaging
-
Excess materials
These ideas can help manufacturers improve efficiency and reduce costs.
What is the difference between a production planner and a project manager?
The difference between a product planner and project manager is that a planer is typically the one who organizes and plans the entire project. A production planner, however, is mostly involved in the planning stages.
Why is logistics important in manufacturing?
Logistics are an essential part of any business. They can help you achieve great success by helping you manage product flow from raw material to finished goods.
Logistics also play a major role in reducing costs and increasing efficiency.
What's the difference between Production Planning & Scheduling?
Production Planning (PP), or production planning, is the process by which you determine what products are needed at any given time. This is done through forecasting demand and identifying production capacities.
Scheduling is the process that assigns dates to tasks so they can get completed within a given timeframe.
What do you mean by warehouse?
Warehouses and storage facilities are where goods are kept before being sold. It can be either an indoor or outdoor space. In some cases it could be both indoors and outdoors.
Statistics
- According to a Statista study, U.S. businesses spent $1.63 trillion on logistics in 2019, moving goods from origin to end user through various supply chain network segments. (netsuite.com)
- Job #1 is delivering the ordered product according to specifications: color, size, brand, and quantity. (netsuite.com)
- It's estimated that 10.8% of the U.S. GDP in 2020 was contributed to manufacturing. (investopedia.com)
- Many factories witnessed a 30% increase in output due to the shift to electric motors. (en.wikipedia.org)
- You can multiply the result by 100 to get the total percent of monthly overhead. (investopedia.com)
External Links
How To
How to Use Lean Manufacturing in the Production of Goods
Lean manufacturing is an approach to management that aims for efficiency and waste reduction. It was created in Japan by Taiichi Ohno during the 1970s and 80s. He received the Toyota Production System award (TPS), from Kanji Toyoda, founder of TPS. Michael L. Watkins published the first book on lean manufacturing in 1990.
Lean manufacturing can be described as a set or principles that are used to improve quality, speed and cost of products or services. It emphasizes reducing defects and eliminating waste throughout the value chain. Lean manufacturing is called just-in-time (JIT), zero defect, total productive maintenance (TPM), or 5S. Lean manufacturing focuses on eliminating non-value-added activities such as rework, inspection, and waiting.
In addition to improving product quality and reducing costs, lean manufacturing helps companies achieve their goals faster and reduces employee turnover. Lean Manufacturing is one of the most efficient ways to manage the entire value chains, including suppliers and customers as well distributors and retailers. Lean manufacturing is widely practiced in many industries around the world. Toyota's philosophy, for example, is what has enabled it to be successful in electronics, automobiles, medical devices, healthcare and chemical engineering as well as paper and food.
Five fundamental principles underlie lean manufacturing.
-
Define Value: Identify the social value of your business and what sets you apart.
-
Reduce Waste – Eliminate all activities that don't add value throughout the supply chain.
-
Create Flow: Ensure that the work process flows without interruptions.
-
Standardize & Simplify - Make processes as consistent and repeatable as possible.
-
Building Relationships – Establish personal relationships with both external and internal stakeholders.
Lean manufacturing is not a new concept, but it has been gaining popularity over the last few years due to a renewed interest in the economy following the global financial crisis of 2008. Many businesses are now using lean manufacturing to improve their competitiveness. In fact, some economists believe that lean manufacturing will be an important factor in economic recovery.
With many benefits, lean manufacturing is becoming more common in the automotive industry. These benefits include increased customer satisfaction, reduced inventory levels and lower operating costs.
You can apply Lean Manufacturing to virtually any aspect of your organization. It is especially useful for the production aspect of an organization, as it ensures that every step in the value chain is efficient and effective.
There are three main types:
-
Just-in-Time Manufacturing (JIT): This type of lean manufacturing is commonly referred to as "pull systems." JIT refers to a system in which components are assembled at the point of use instead of being produced ahead of time. This approach reduces lead time, increases availability and reduces inventory.
-
Zero Defects Manufacturing (ZDM): ZDM focuses on ensuring that no defective units leave the manufacturing facility. You should repair any part that needs to be repaired during an assembly line. This applies to finished goods that may require minor repairs before shipment.
-
Continuous Improvement: Continuous Improvement aims to improve efficiency by continually identifying problems and making adjustments to eliminate or minimize waste. Continuous improvement refers to continuous improvement of processes as well people and tools.