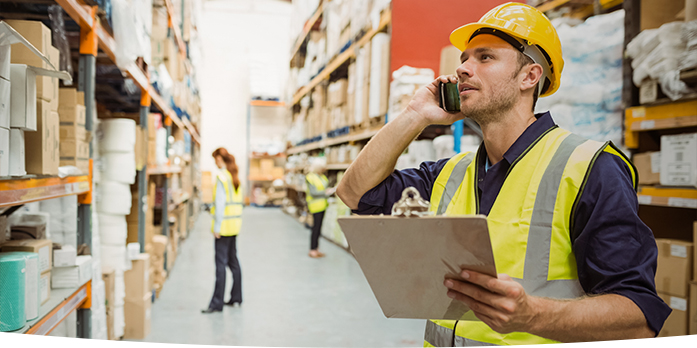
Manufacturing engineers must convert raw materials and create new, updated products. They are also responsible for creating systems that integrate the production process and supervising those who are involved in its manufacture. It is a rewarding career with high job satisfaction, and a good balance between work and life.
The average salary of a US manufacturing engineer is $77,500 per annum. This figure is based off data from TurboTax Users who declared their occupation as manufacturing engineering. It includes tips, bonuses, taxable wages, and other factors.
What is the Manufacturing Engineering Salary in Canada?
The Manufacturing Engineering Salary ranges between $28,500 and $178,500, depending on your education, skills and experience, as well as the employer you work for. Those with experience tend to earn higher salaries than those who do not.
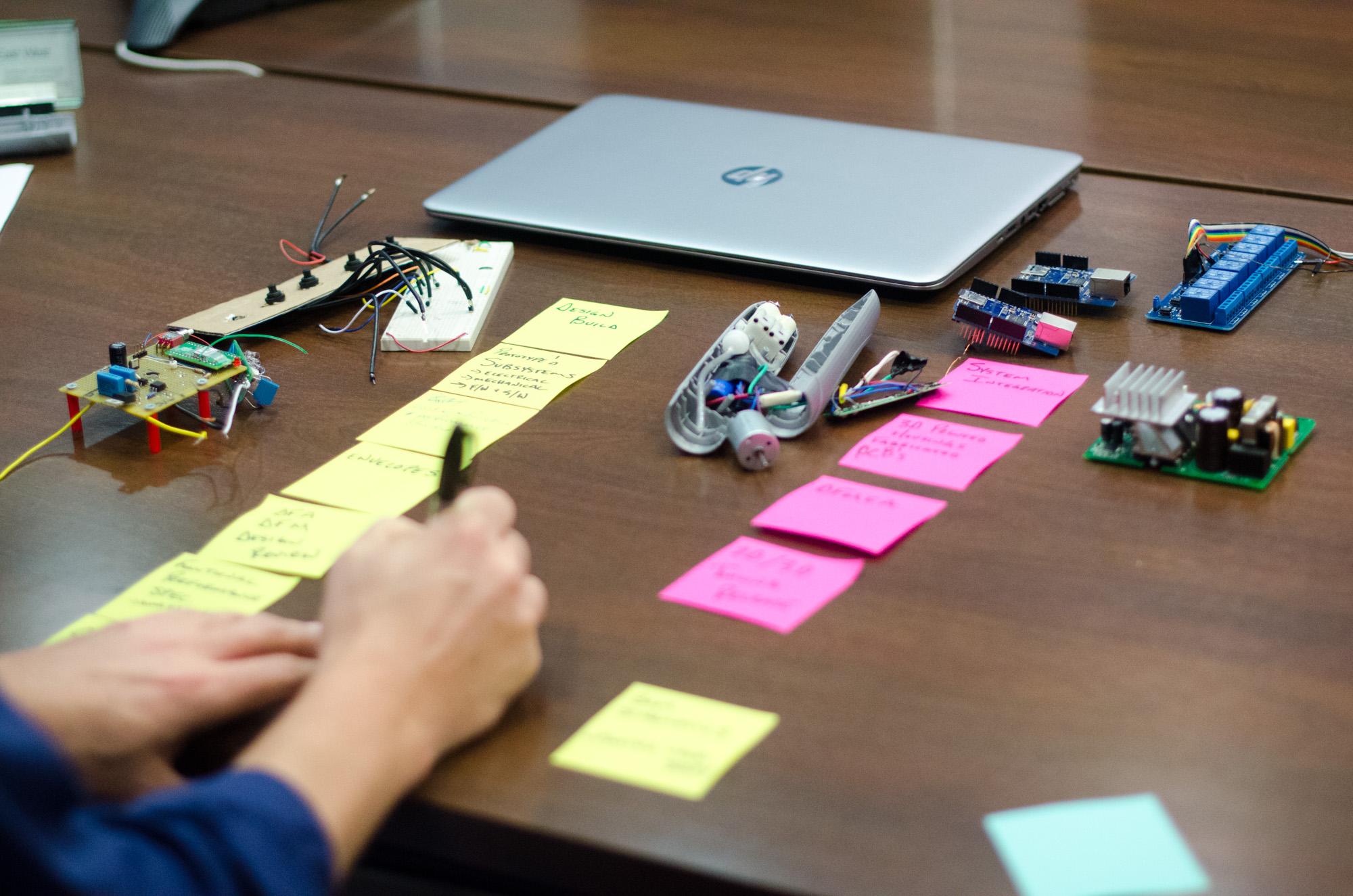
Entry Level Manufacturing engineer Salary The average salary of an entry level manufacturing engineers is $52,000 a year. This amount can vary from state to state, so it's important to find out what the average pay is in your area before applying for a job.
What are the requirements to become a manufacturing engineer
In general, a bachelor’s degree is required in an appropriate subject. It could be any of the engineering specialties available or something more general, like computer science. You will need a graduate level degree if your goal is to work in research or to progress within the field.
What is the typical manufacturing engineer's job?
The majority of engineers develop and design systems to improve workplace productivity. They are experts at creating the processes which turn raw materials in to a finished product while focusing on eliminating wastage. These engineers are also highly skilled at solving problems, which allows them to identify issues and quickly solve them when creating new products or upgrading older ones.
What do manufacturing engineers do in their day-to-day duties?
A manufacturing engineer's main duties include maintaining projects on schedule and within budget, as well as ensuring production efficiency and high quality. They must have the ability to communicate effectively with technicians, design engineers and management. They must also understand how their decisions impact production cost and timelines, and how to manage these factors in a way that benefits the entire project team.
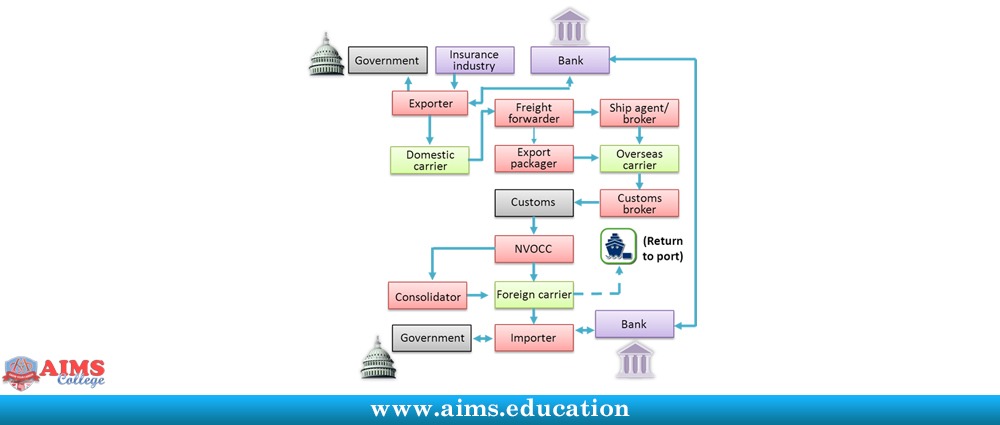
What are the qualifications to become an Industrial and Manufacturing Engineer?
Almost any company that has in-house manufacturing needs a manufacturing engineer. Large multinational corporations, smaller companies, R&D labs, or local companies can all be included. These companies produce products ranging from pharmaceuticals to foods and drinks.
What are the most popular jobs for manufacturing engineers?
There are a variety of industries that employ manufacturing engineers, including aerospace, defense, software and hardware development, robotics and assembly line automation. A manufacturing engineer's work environment can be an office, laboratory, or factory.
What is a typical manufacturing engineer's salary?
Manufacturing engineer salaries in the US range from $57.839 to $86,809 per year. This figure is based upon data from 655 TurboTax users that reported their occupation as manufacturing engineer and includes a mix of taxable wages, tips, bonuses and more.
FAQ
Is there anything we should know about Manufacturing Processes prior to learning about Logistics.
No. No. Knowing about manufacturing processes will help you understand how logistics works.
What is meant by manufacturing industries?
Manufacturing Industries is a group of businesses that produce goods for sale. Consumers are those who purchase these products. These companies use a variety processes such as distribution, retailing and management to accomplish their purpose. They manufacture goods from raw materials using machines and other equipment. This includes all types and varieties of manufactured goods, such as food items, clothings, building supplies, furnitures, toys, electronics tools, machinery vehicles, pharmaceuticals medical devices, chemicals, among others.
What are the goods of logistics?
Logistics refers to all activities that involve moving goods from A to B.
They include all aspects associated with transport including packaging, loading transporting, unloading storage, warehousing inventory management customer service, distribution returns and recycling.
Logisticians ensure the product reaches its destination in the most efficient manner. Logisticians assist companies in managing their supply chains by providing information such as demand forecasts, stock levels and production schedules.
They monitor shipments in transit, ensure quality standards, manage inventories, replenish orders, coordinate with suppliers and other vendors, and offer support services for sales, marketing, and customer service.
What jobs are available in logistics?
There are many kinds of jobs available within logistics. Here are some:
-
Warehouse workers – They load and unload pallets and trucks.
-
Transportation drivers: They drive trucks and trailers and deliver goods and make pick-ups.
-
Freight handlers – They sort and package freight at warehouses.
-
Inventory managers - These are responsible for overseeing the stock of goods in warehouses.
-
Sales reps are people who sell products to customers.
-
Logistics coordinators - They organize and plan logistics operations.
-
Purchasing agents - They buy goods and services that are necessary for company operations.
-
Customer service agents - They answer phone calls and respond to emails.
-
Shippers clerks - They process shipping order and issue bills.
-
Order fillers - They fill orders based on what is ordered and shipped.
-
Quality control inspectors are responsible for inspecting incoming and outgoing products looking for defects.
-
Others - There is a variety of other jobs in logistics. These include transportation supervisors and cargo specialists.
Statistics
- According to the United Nations Industrial Development Organization (UNIDO), China is the top manufacturer worldwide by 2019 output, producing 28.7% of the total global manufacturing output, followed by the United States, Japan, Germany, and India.[52][53] (en.wikipedia.org)
- In the United States, for example, manufacturing makes up 15% of the economic output. (twi-global.com)
- [54][55] These are the top 50 countries by the total value of manufacturing output in US dollars for its noted year according to World Bank.[56] (en.wikipedia.org)
- Job #1 is delivering the ordered product according to specifications: color, size, brand, and quantity. (netsuite.com)
- It's estimated that 10.8% of the U.S. GDP in 2020 was contributed to manufacturing. (investopedia.com)
External Links
How To
How to Use Six Sigma in Manufacturing
Six Sigma is defined as "the application of statistical process control (SPC) techniques to achieve continuous improvement." Motorola's Quality Improvement Department created Six Sigma at their Tokyo plant, Japan in 1986. Six Sigma is a method to improve quality through standardization and elimination of defects. Many companies have adopted this method in recent years. They believe there is no such thing a perfect product or service. Six Sigma aims to reduce variation in the production's mean value. This means that if you take a sample of your product, then measure its performance against the average, you can find out what percentage of the time the process deviates from the norm. If you notice a large deviation, then it is time to fix it.
Understanding how variability works in your company is the first step to Six Sigma. Once you understand this, you can then identify the causes of variation. This will allow you to decide if these variations are random and systematic. Random variations happen when people make errors; systematic variations are caused externally. Random variations would include, for example, the failure of some widgets to fall from the assembly line. You might notice that your widgets always fall apart at the same place every time you put them together.
Once you identify the problem areas, it is time to create solutions. That solution might involve changing the way you do things or redesigning the process altogether. To verify that the changes have worked, you need to test them again. If they don't work, you will need to go back to the drawing boards and create a new plan.