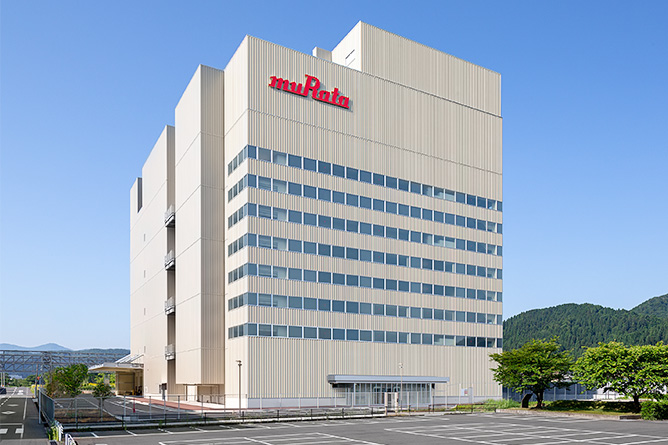
The principles of six sigma are important because they can improve efficiency and productivity in an organization. They also improve the quality of products and reduce costs. The process can be done through various strategies and methodologies, such as process mapping, statistical analysis, and control charts.
What are six sigma?
The 6 sigma Principles are a set methods used to eliminate defects from manufacturing processes. The results are often huge. They can be applied in a variety of ways. The can also be used to ensure that every process runs smoothly and efficiently.
Lean six sigma:
Lean six sigma's first principle is to understand how the workflow actually works. You need to take note of the actual process to determine where you can make improvements. This step is very important because it helps you identify the problem and develop a solution.
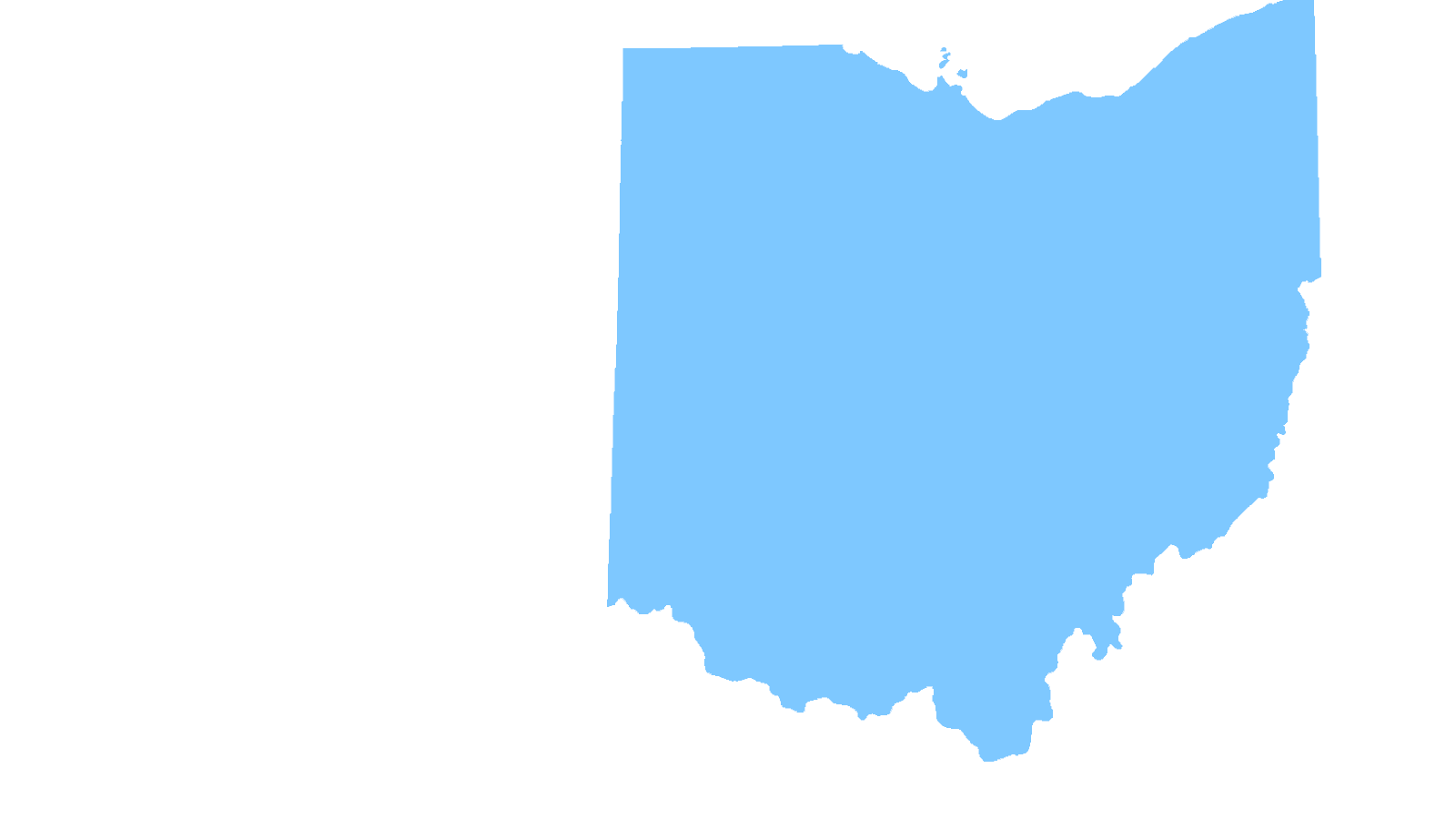
It is important to understand this principle in any project. Process improvement is no exception. This is because if you know what needs to be improved but do not understand how to fix it, it will be difficult to make the change happen.
To improve a business process, it may be necessary to alter the work practices of employees or to adjust their approach. It may seem like a difficult task, but by adapting, a business can make changes quickly and effectively.
Six sigma's key principle is to empower employees to take part in projects. It is very difficult to make these changes happen if only upper-level management is onboard.
In addition to ensuring that all employees are onboard with the changes, it is important that they are trained in the specific principles of the process so that they can identify and eliminate errors or defects. The employees should be provided with the tools and resources needed to take part in the project.
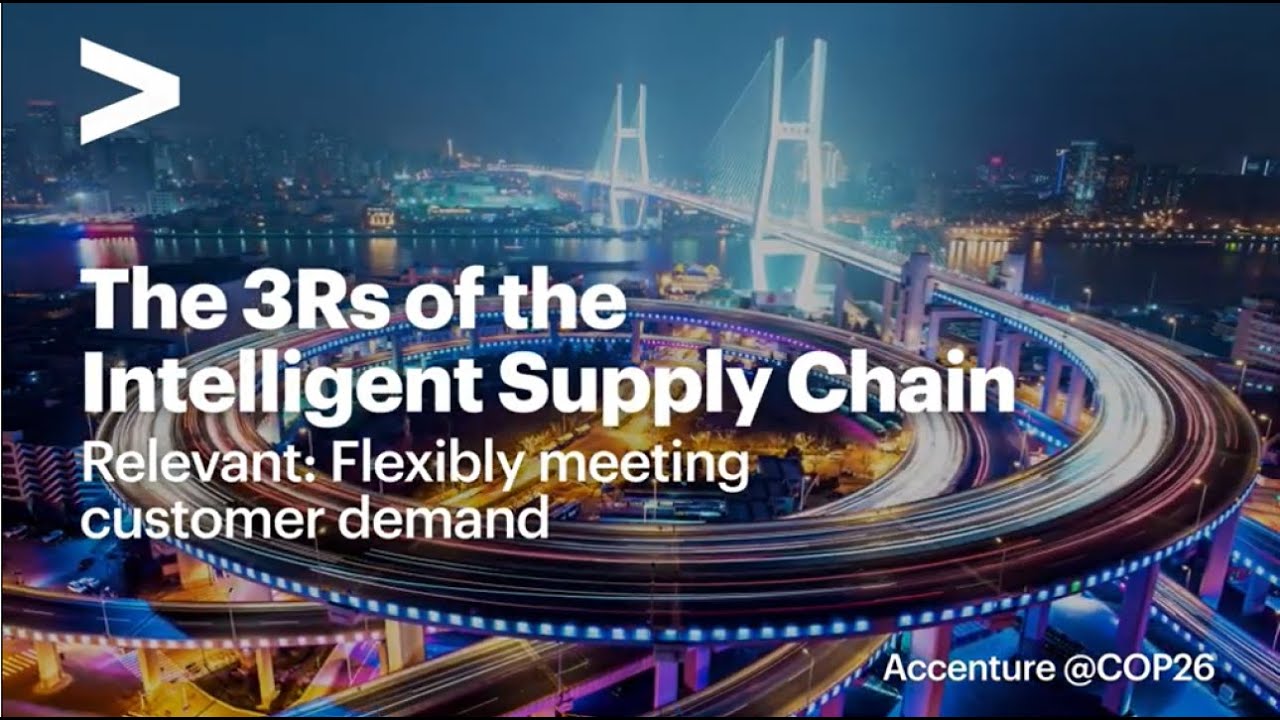
What are the six sigma values?
Six Sigma values focus on customer satisfaction and loyalty, believe that each process should be designed for minimal waste, and place an emphasis on measuring and analysing data. These factors all contribute to a higher level of customer satisfaction and loyalty.
Lastly, the six sigma values involve consistency and reliability. These factors play a vital role in industries that demand high quality products and/or services. They should be applied to all aspects of the company, and they should always be evaluated and revised if needed.
In summary, the six sigma values help organizations improve their operations and become more efficient. They are also important for creating a sustainable system that will allow the company to grow and succeed. This is a great method to make sure that your company remains competitive and profitable.
FAQ
Is there anything we should know about Manufacturing Processes prior to learning about Logistics.
No. You don't have to know about manufacturing processes before learning about logistics. Understanding the manufacturing process will allow you to better understand logistics.
Why automate your warehouse
Automation has become increasingly important in modern warehousing. The rise of e-commerce has led to increased demand for faster delivery times and more efficient processes.
Warehouses must adapt quickly to meet changing customer needs. They must invest heavily in technology to do this. Automating warehouses is a great way to save money. Here are some reasons why it's worth investing in automation:
-
Increases throughput/productivity
-
Reduces errors
-
Improves accuracy
-
Safety increases
-
Eliminates bottlenecks
-
Companies can scale more easily
-
Increases efficiency of workers
-
Provides visibility into everything that happens in the warehouse
-
Enhances customer experience
-
Improves employee satisfaction
-
Reducing downtime and increasing uptime
-
High quality products delivered on-time
-
Eliminates human error
-
Helps ensure compliance with regulations
What are the responsibilities of a manufacturing manager
The manufacturing manager should ensure that every manufacturing process is efficient and effective. They should also be aware of any problems within the company and act accordingly.
They should also learn how to communicate effectively with other departments, including sales and marketing.
They should also be knowledgeable about the latest trends in the industry so they can use this information for productivity and efficiency improvements.
What does manufacturing industry mean?
Manufacturing Industries are those businesses that make products for sale. Consumers are those who purchase these products. These companies use various processes such as production, distribution, retailing, management, etc., to fulfill this purpose. These companies produce goods using raw materials and other equipment. This includes all types manufactured goods such as clothing, building materials, furniture, electronics, tools and machinery.
What are the responsibilities of a logistic manager?
A logistics manager makes sure that all goods are delivered on-time and in good condition. This is achieved by using their knowledge and experience with the products of the company. He/she should ensure that sufficient stock is available in order to meet customer demand.
What can I do to learn more about manufacturing?
Hands-on experience is the best way to learn more about manufacturing. You can read books, or watch instructional videos if you don't have the opportunity to do so.
Statistics
- In the United States, for example, manufacturing makes up 15% of the economic output. (twi-global.com)
- In 2021, an estimated 12.1 million Americans work in the manufacturing sector.6 (investopedia.com)
- You can multiply the result by 100 to get the total percent of monthly overhead. (investopedia.com)
- (2:04) MTO is a production technique wherein products are customized according to customer specifications, and production only starts after an order is received. (oracle.com)
- It's estimated that 10.8% of the U.S. GDP in 2020 was contributed to manufacturing. (investopedia.com)
External Links
How To
Six Sigma in Manufacturing
Six Sigma is defined as "the application of statistical process control (SPC) techniques to achieve continuous improvement." Motorola's Quality Improvement Department created Six Sigma at their Tokyo plant, Japan in 1986. The basic idea behind Six Sigma is to improve quality by improving processes through standardization and eliminating defects. In recent years, many companies have adopted this method because they believe there is no such thing as perfect products or services. Six Sigma's main objective is to reduce variations from the production average. If you take a sample and compare it with the average, you will be able to determine how much of the production process is different from the norm. If there is a significant deviation from the norm, you will know that something needs to change.
Understanding how variability works in your company is the first step to Six Sigma. Once you have this understanding, you will need to identify sources and causes of variation. This will allow you to decide if these variations are random and systematic. Random variations are caused by human errors. Systematic variations can be caused by outside factors. These are, for instance, random variations that occur when widgets are made and some fall off the production line. It would be considered a systematic problem if every widget that you build falls apart at the same location each time.
After identifying the problem areas, you will need to devise solutions. It might mean changing the way you do business or redesigning it entirely. Test them again once you've implemented the changes. If they don’t work, you’ll need to go back and rework the plan.