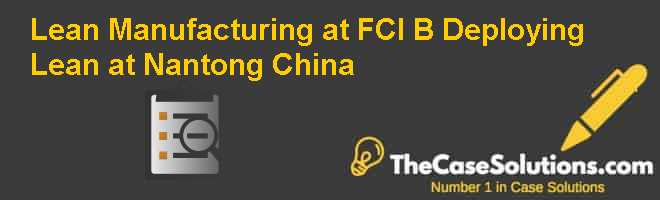
Are you looking to work in the industrial engineering field? Find out what jobs are available by reading on. This article will discuss the types and average salaries of various jobs as well as the education requirements. We'll also discuss what skills are required, and where to look for these jobs. Then, you can apply for the position that is most exciting to your heart! Good luck! Before you apply for an industrial engineering job in the future, be sure to read through the job description.
Job description
Industrial engineers aren't for everyone. This job involves using engineering principles and technology in order to improve production processes and layouts within companies. This type of engineer is responsible for developing tools and analytics that help companies monitor their costs and schedules. He or she also reviews production data, looking for areas of improvement, and compiles material and equipment lists.
An undergraduate degree in mechanical engineer is required for a job as an industrial engineering specialist. This field requires a broad knowledge of engineering principles and practices, as well as a knack for problem-solving. An industrial engineer needs to have a good understanding of the human abilities and needs. Industrial engineers should be well-organized, have strong analytical abilities, and communicate well. They are responsible for improving the production process in companies and managing factories and warehouses.
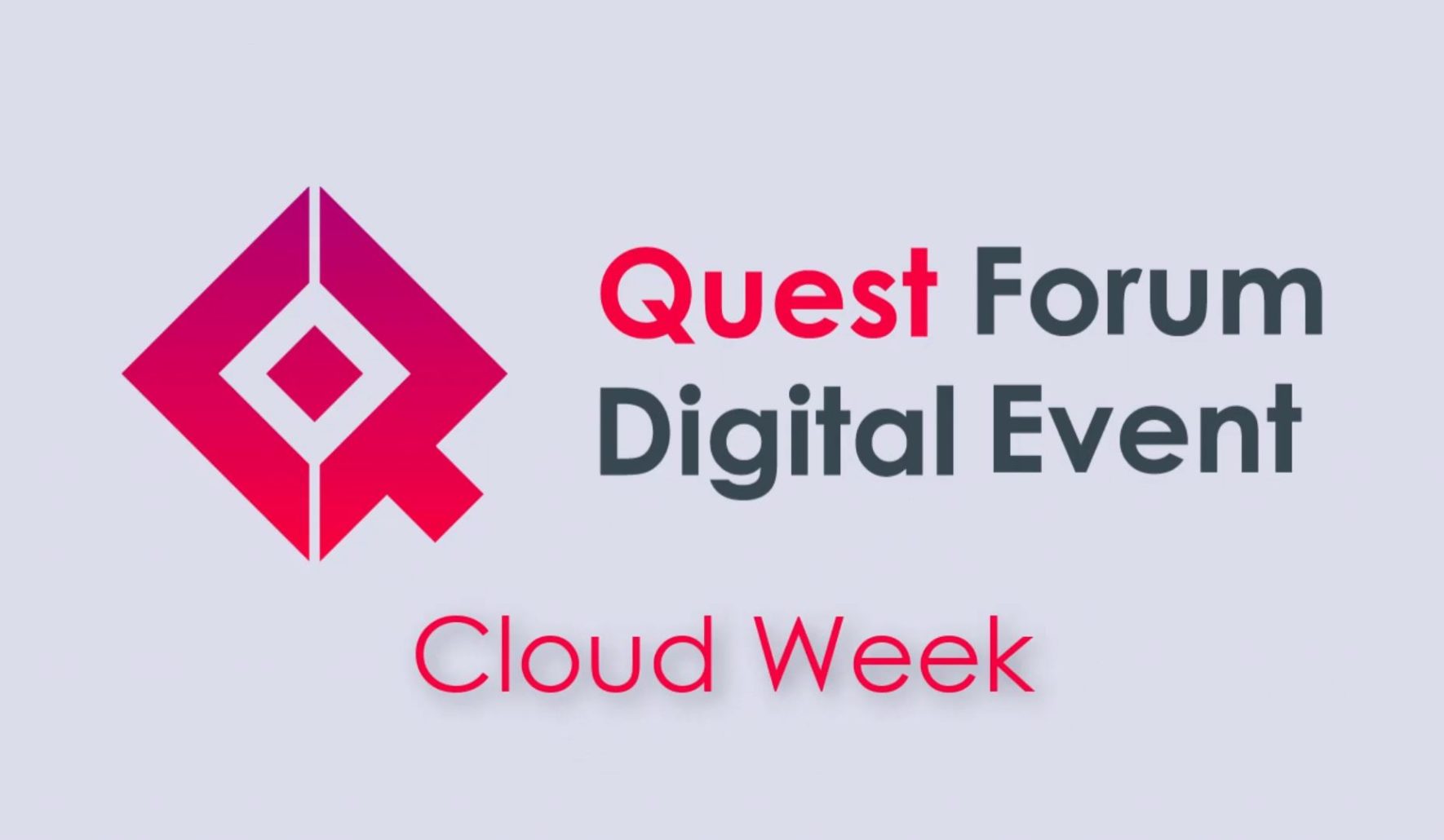
Salary range
The pay range for industrial engineers varies depending upon experience. Starting salaries are around $85,000, but the amount of compensation can go up to $100,000. The following table explains the salary range for industrial engineers by experience level. Ventura, California Entry-Level Engineers can expect to earn approximately $86,000 annually. For an industrial engineer with experience, the annual salary range is between $85,000 and $100,000. As a Project Engineer, you can also be hired. This requires typically a four-year degree.
The average salary for Industrial Engineers varies depending upon where they are located, their industry and the years of experience. The average salary for an industrial engineer in New York is $60,700 to $140,000 each year. The upward trend in salaries is difficult to pinpoint, but national averages have increased by over 40 percent in the past 10 years and are expected to continue to rise. Monster's Salary Tool will help you to find out about local salary ranges.
Education required
While licensing may not be required for industrial engineers it is a requirement for government contracts. For entry level positions, industrial engineers do not require licensing. For professional licensure, however, they will need to have relevant experience and a degree from an institution that is accredited. Industrial engineers can be found working in offices, factories, and labs. Many industrial engineering professionals find work in aerospace product manufacturing, architectural, engineering services, navigational devices manufacturing, and medical and control instrument production.
Many industrial engineers do internships as part of their college careers. This helps them gain valuable work experience. Although entry-level positions in industrial engineering don't usually require professional experience or training, you may be able to gain valuable experience from other roles. If you are interested in working for government agencies or another organization, internships could be a great option. An industrial engineer may need to be cleared for security clearance, in addition to interning.
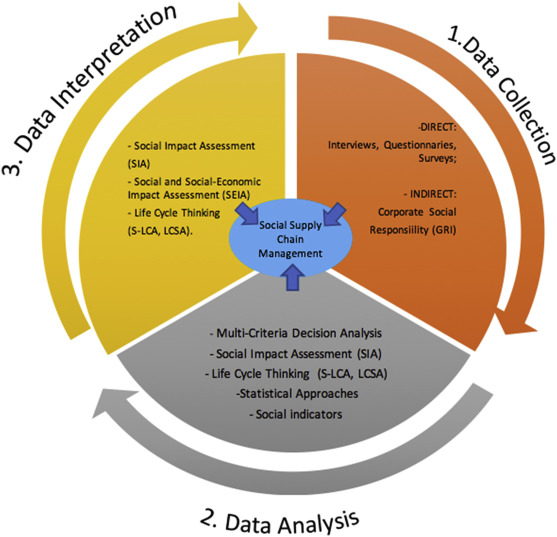
Locations
There are many opportunities for industrial engineering jobs that can be very rewarding and available in a variety settings. Entry-level positions in the field typically involve completing calculations, installing monitoring and testing devices, and documenting findings. They might also help develop budgets or track metrics. For industrial engineers, standing for long periods may be required. Industrial engineers need to communicate effectively. In some cases, they work under the supervision of a more senior engineer.
Industrial engineers help companies create efficient production processes using the most energy and resources. Their main goal is to find ways to streamline the production process, while ensuring maximum labor efficiency. Industrial engineers work in offices, factories, and other settings to implement improvements in the operations of organizations. Entry-level positions in industrial engineering require a bachelor's degree in industrial engineering or a related field. According to the Bureau of Labor Statistics the average salary for industrial engineers is $95,300 by 2021.
FAQ
Can certain manufacturing steps be automated?
Yes! Yes. Automation has been around since ancient time. The Egyptians invent the wheel thousands of year ago. To help us build assembly lines, we now have robots.
Actually, robotics can be used in manufacturing for many purposes. These include:
-
Robots for assembly line
-
Robot welding
-
Robot painting
-
Robotics inspection
-
Robots that make products
Manufacturing can also be automated in many other ways. 3D printing is a way to make custom products quickly and without waiting weeks or months for them to be manufactured.
What is production plan?
Production planning is the process of creating a plan that covers all aspects of production. This includes scheduling, budgeting and crew, location, equipment, props, and more. This document ensures that everything is prepared and available when you are ready for shooting. It should also contain information on achieving the best results on set. This information includes locations, crew details and equipment requirements.
It is important to first outline the type of film you would like to make. You might have an idea of where you want to film, or you may have specific locations or sets in mind. Once you have identified the scenes and locations, you can start to determine which elements are required for each scene. If you decide you need a car and don't know what model to choose, this could be an example. If this is the case, you might start searching online for car models and then narrow your options by selecting from different makes.
Once you have found the right vehicle, you can think about adding accessories. Do you have people who need to be seated in the front seat? Or maybe you just need someone to push the car around. You may want to change the interior's color from black or white. These questions will help to determine the style and feel of your car. You can also think about the type of shots you want to get. Do you want to film close-ups, or wider angles? Maybe the engine or steering wheel is what you are looking to film. These things will help you to identify the car that you are looking for.
Once you have established all the details, you can create a schedule. You will know when you should start and when you should finish shooting. The schedule will show you when to get there, what time to leave, and when to return home. Everyone knows exactly what they should do and when. You can also make sure to book extra staff in advance if you have to hire them. It's not worth paying someone to show up if you haven't told him.
It is important to calculate the amount of filming days when you are creating your schedule. Some projects are quick and easy, while others take weeks. When you are creating your schedule, you should always keep in mind whether you need more than one shot per day or not. Multiple takes of the same location will lead to higher costs and take more time. If you are unsure if you need multiple takes, it is better to err on the side of caution and shoot fewer takes rather than risk wasting money.
Budgeting is another crucial aspect of production plan. As it will allow you and your team to work within your financial means, setting a realistic budget is crucial. If you have to reduce your budget due to unexpected circumstances, you can always lower it later. It is important to not overestimate how much you will spend. You will end up spending less money if you underestimate the cost of something.
Production planning can be a complex process. However, once you know how everything works together it will become easier to plan future projects.
What are manufacturing & logistics?
Manufacturing is the production of goods using raw materials. Logistics covers all aspects involved in managing supply chains, including procurement and production planning. As a broad term, manufacturing and logistics often refer to both the creation and delivery of products.
What does it mean to warehouse?
Warehouses and storage facilities are where goods are kept before being sold. It can be an outdoor or indoor area. It may also be an indoor space or an outdoor area.
Statistics
- It's estimated that 10.8% of the U.S. GDP in 2020 was contributed to manufacturing. (investopedia.com)
- According to the United Nations Industrial Development Organization (UNIDO), China is the top manufacturer worldwide by 2019 output, producing 28.7% of the total global manufacturing output, followed by the United States, Japan, Germany, and India.[52][53] (en.wikipedia.org)
- In 2021, an estimated 12.1 million Americans work in the manufacturing sector.6 (investopedia.com)
- According to a Statista study, U.S. businesses spent $1.63 trillion on logistics in 2019, moving goods from origin to end user through various supply chain network segments. (netsuite.com)
- (2:04) MTO is a production technique wherein products are customized according to customer specifications, and production only starts after an order is received. (oracle.com)
External Links
How To
How to Use 5S to Increase Productivity in Manufacturing
5S stands in for "Sort", the "Set In Order", "Standardize", or "Separate". The 5S methodology was developed at Toyota Motor Corporation in 1954. It improves the work environment and helps companies to achieve greater efficiency.
This method has the basic goal of standardizing production processes to make them repeatable. This means that tasks such as cleaning, sorting, storing, packing, and labeling are performed daily. Through these actions, workers can perform their jobs more efficiently because they know what to expect from them.
Implementing 5S involves five steps: Sort, Set in Order, Standardize Separate, Store, and Each step involves a different action which leads to increased efficiency. You can make it easy for people to find things later by sorting them. Once you have placed items in an ordered fashion, you will put them together. You then organize your inventory in groups. Labeling your containers will ensure that everything is correctly labeled.
This process requires employees to think critically about how they do their job. Employees must be able to see why they do what they do and find a way to achieve them without having to rely on their old methods. To implement the 5S system, employees must acquire new skills and techniques.
In addition to improving efficiency, the 5S system also increases morale and teamwork among employees. They feel more motivated to work towards achieving greater efficiency as they see the results.