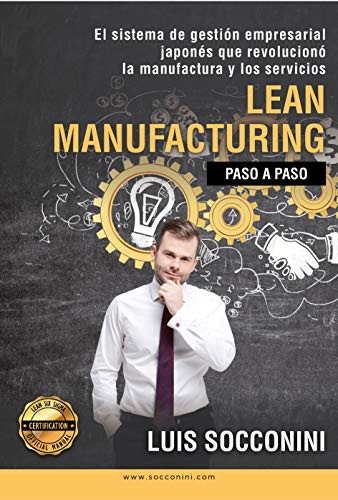
You've found the right place if you are looking for news on manufacturing. Fusion 360 community members share updates about manufacturing innovation and recap the week's events. From Alexandria Industries to Festo's expansion plans, the Fusion 360 community has you covered. From the latest product launches to news about additive manufacturing, Fusion 360 covers a wide range of topics. Here are some recent articles regarding manufacturing innovation. Read on to learn more.
Alexandria Industries
Recent Alexandria Industries manufacturing news focuses their expansion in Douglas County, Minnesota. Their current workforce is 480, but they plan to invest several millions in the new facility. Alexandria Industries' growth has been faster than their revenue and employment levels before the recession. However, they are still struggling to find qualified candidates for 50 new positions. These positions pay $15-30 an hour, plus benefits. Alexandria Industries is a great place to start a new career!
Alexandria Industries recently hired new management to help them grow. Jonathan D. Olson is the new CFO of Alexandria Industries. He is committed to investing and supporting the company's employees. He also joined the company as its new CFO, and is planning to improve the working conditions of employees and invest in training programs. The new acquisition will expand the company's capabilities by integrating the operations of Alexandria Plastics, Inc., a manufacturer of plastic injection and foam-molded components.
Festo U.S. expansion plans
Festo Corp. has announced plans to expand its North American manufacturing operations. The company will increase its presence in Mason by three times and create 350 additional jobs. This expansion will generate new jobs for the next five-years at a cost of $90million. In addition to manufacturing, Festo will provide industrial training solutions and support services. The expansion will also include a new Didactic Education Center to provide support services for manufacturing businesses and colleges throughout the Tristate.
The expansion will see the construction of a new Mason, Ohio plant that manufactures automation components. The new facility will include a Research and Development Center and a Global Production Center. Upon completion, both will employ more than 1,000 people. The company also plans to create new jobs and establish a research and development center for automation technology. This expansion is part the company's larger plan to target the U.S. market.
Additive Manufacturing
As technology advances, additive manufacturing has become more popular among manufacturers. To help reach the global market, many companies have formed partnerships. Some of these partnerships involve Voxeljet and AGC Ceramic, a glass and ceramic company. Voxeljet and AGC Ceramic aim to introduce Brightorb, a high-performance ceramic material, and optimize the VX1000 for 3D printing ceramic powder. Stratasys and Tata Technologies have also partnered to promote additive production technologies in India.
In addition to collaboration agreements, new technologies are being developed for the additive manufacturing process. Optimus 3D now owns a fourth Renishaw system for metal additive manufacturing. The company has also expanded the range of 3D printers to include metal powder. This development will ensure that additive manufacturing becomes an integral part advanced PLM. Advanced PLM will be more IoT-oriented, integrated, and flexible. These developments will allow for rapid growth in a variety of industries.
Collaborative Manufacturing
What is collaborative production? Collaborative Manufacturing is the direct input from the plant floor. This information is important for the management process. This also requires interaction between the manufacturing and design teams. Collaborative Manufacturing can improve productivity, quality, and reduce the number required to perform each production process. But what are the real benefits of collaborative production? Let's discuss a few examples. How can collaborative manufacturing increase plant performance? Continue reading for more information.
Collaboration is a growing trend in many industries. It is used to create new products, improve product design, synchronize inventory across the supply chains, and lower logistics costs. Collaborative manufacturing can also reduce time-to market and volume and shorten the manufacturing cycle for designated suppliers. It is important for companies to realize that collaborative manufacturing offers significant benefits for everyone. It is not right for everyone. Be sure to consider the benefits before you adopt collaborative manufacturing.
FAQ
What are the four types of manufacturing?
Manufacturing refers to the transformation of raw materials into useful products by using machines and processes. It includes many different activities like designing, building and testing, packaging, shipping and selling, as well as servicing.
What is the difference between manufacturing and logistics
Manufacturing is the process of creating goods from raw materials by using machines and processes. Logistics manages all aspects of the supply chain, including procurement, production planning and distribution, inventory control, transportation, customer service, and transport. As a broad term, manufacturing and logistics often refer to both the creation and delivery of products.
How can manufacturing efficiency be improved?
First, determine which factors have the greatest impact on production time. The next step is to identify the most important factors that affect production time. If you don’t know where to begin, consider which factors have the largest impact on production times. Once you've identified them, try to find solutions for each of those factors.
What types of jobs can you find in logistics
Logistics can offer many different jobs. Some examples are:
-
Warehouse workers - They load and unload trucks and pallets.
-
Transportation drivers – These drivers drive trucks and wagons to transport goods and pick up the goods.
-
Freight handlers - They sort and pack freight in warehouses.
-
Inventory managers – They manage the inventory in warehouses.
-
Sales representatives - They sell products to customers.
-
Logistics coordinators - They plan and organize logistics operations.
-
Purchasing agents are those who purchase goods and services for the company.
-
Customer service representatives - Answer calls and email from customers.
-
Shippers clerks - They process shipping order and issue bills.
-
Order fillers – They fill orders based upon what was ordered and shipped.
-
Quality control inspectors - They check incoming and outgoing products for defects.
-
Others - There is a variety of other jobs in logistics. These include transportation supervisors and cargo specialists.
Is it necessary to be familiar with Manufacturing Processes before we learn about Logistics.
No. No. It is important to know about the manufacturing processes in order to understand how logistics works.
What are the main products of logistics?
Logistics refers to all activities that involve moving goods from A to B.
They cover all aspects of transportation, such as packing, loading, transporting and unloading.
Logisticians make sure that the right product arrives at the right place at the correct time and in safe conditions. Logisticians help companies improve their supply chain efficiency by providing information about demand forecasts and stock levels, production schedules, as well as availability of raw materials.
They also keep track of shipments in transit, monitor quality standards, perform inventories and order replenishment, coordinate with suppliers and vendors, and provide support services for sales and marketing.
Statistics
- In the United States, for example, manufacturing makes up 15% of the economic output. (twi-global.com)
- Job #1 is delivering the ordered product according to specifications: color, size, brand, and quantity. (netsuite.com)
- You can multiply the result by 100 to get the total percent of monthly overhead. (investopedia.com)
- According to a Statista study, U.S. businesses spent $1.63 trillion on logistics in 2019, moving goods from origin to end user through various supply chain network segments. (netsuite.com)
- [54][55] These are the top 50 countries by the total value of manufacturing output in US dollars for its noted year according to World Bank.[56] (en.wikipedia.org)
External Links
How To
How to Use Just-In-Time Production
Just-in-time (JIT) is a method that is used to reduce costs and maximize efficiency in business processes. It allows you to get the right amount resources at the right time. This means that your only pay for the resources you actually use. Frederick Taylor first coined this term while working in the early 1900s as a foreman. Taylor observed that overtime was paid to workers if they were late in working. He then concluded that if he could ensure that workers had enough time to do their job before starting to work, this would improve productivity.
JIT is a way to plan ahead and make sure you don't waste any money. Look at your entire project, from start to end. Make sure you have enough resources in place to deal with any unexpected problems. You will have the resources and people to solve any problems you anticipate. This way, you won't end up paying extra money for things that weren't really necessary.
There are many types of JIT methods.
-
Demand-driven: This type of JIT allows you to order the parts/materials required for your project on a regular basis. This will let you track the amount of material left over after you've used it. You'll also be able to estimate how long it will take to produce more.
-
Inventory-based: This is a type where you stock the materials required for your projects in advance. This allows you to predict how much you can expect to sell.
-
Project-driven: This means that you have enough money to pay for your project. Once you have an idea of how much material you will need, you can purchase the necessary materials.
-
Resource-based JIT is the most widespread form. Here you can allocate certain resources based purely on demand. If you have many orders, you will assign more people to manage them. If you don’t have many orders you will assign less people to the work.
-
Cost-based: This is similar to resource-based, except that here you're not just concerned about how many people you have but how much each person costs.
-
Price-based: This approach is very similar to the cost-based method except that you don't look at individual workers costs but the total cost of the company.
-
Material-based - This is a variant of cost-based. But instead of looking at the total company cost, you focus on how much raw material you spend per year.
-
Time-based JIT is another form of resource-based JIT. Instead of focusing on the cost of each employee, you will focus on the time it takes to complete a project.
-
Quality-based: This is yet another variation of resource-based JIT. Instead of thinking about the cost of each employee or the time it takes to produce something, you focus on how good your product quality.
-
Value-based JIT is the newest form of JIT. You don't worry about whether the products work or if they meet customer expectations. Instead, you focus on the added value that you provide to your market.
-
Stock-based. This method is inventory-based and focuses only on the actual production at any given point. This is used to increase production and minimize inventory.
-
Just-intime planning (JIT), is a combination JIT/sales chain management. It is the process that schedules the delivery of components within a short time of their order. This is important as it reduces lead time and increases throughput.