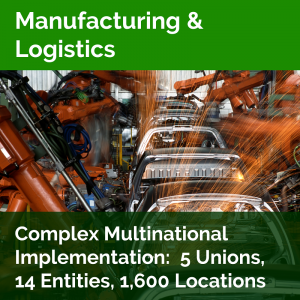
Using Kanban examples in manufacturing can help companies improve efficiency and reduce costs. These principles help to reduce downtime, inefficiencies, and improve customer service. It also allows for continuous improvements.
Kanban can be described as a way to organize and track the work flow. It is used by teams and manufacturers to help them track and monitor the work they do and to increase their productivity. Kanban involves the creation of a visual representation of the steps involved in a particular process and the identification and minimization or inefficiencies.
The kanban process can be applied manually or via a software application. This software helps the team decide what they should do, and who should do it. It optimizes the process. The kanban method also allows for employees to adapt to feedback and make improvements to their processes. It is also a great tool for brainstorming.
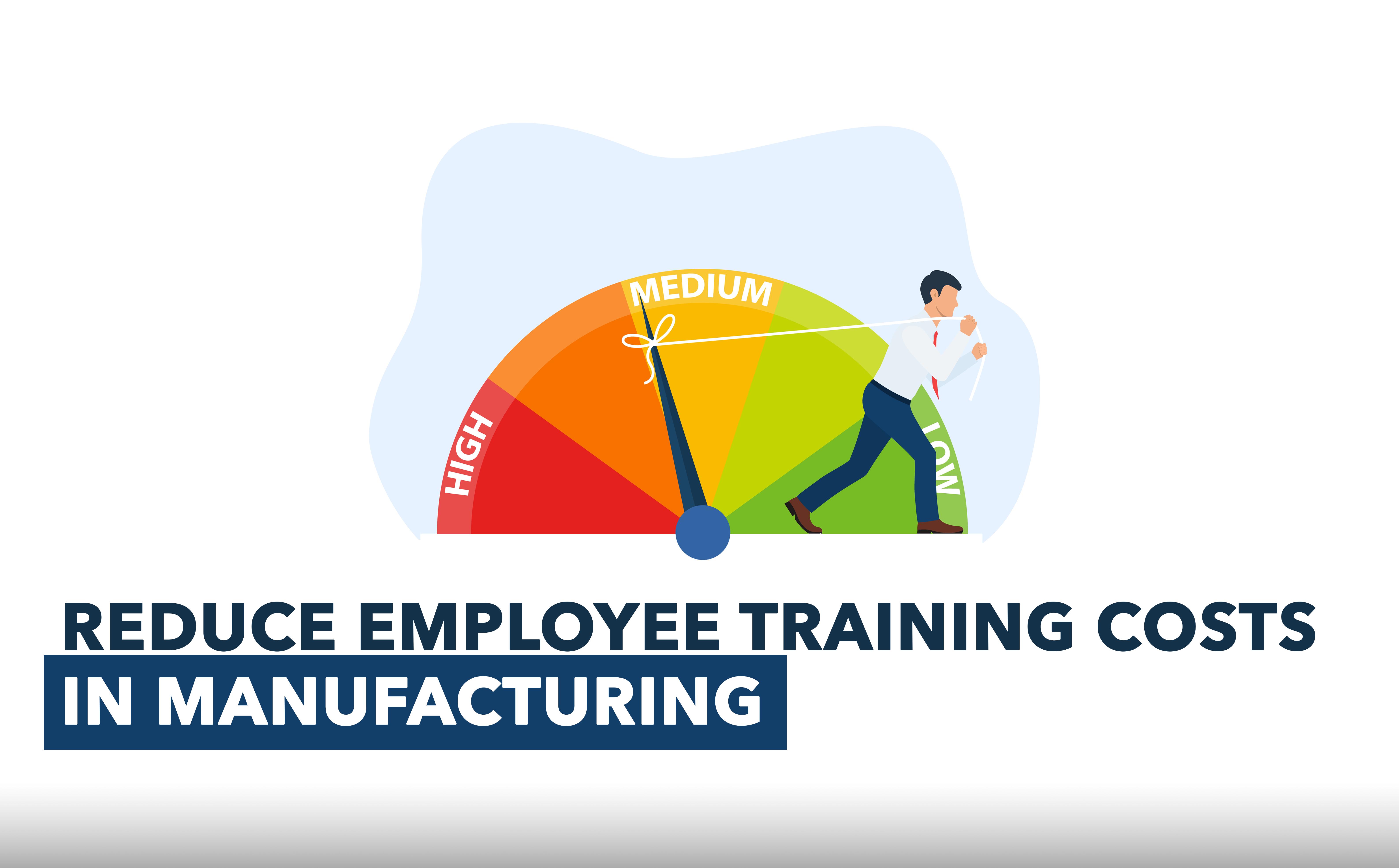
The kanban board is a popular Kanban example in manufacturing. It is a board that shows a process. The board displays the steps involved in the process in order of priority. To contact a supplier is one example. The second task is to order the supplies needed to complete the work. The third task is to start manufacturing. The fourth task involves testing the product and shipping it.
The kanban method also allows the team to visualize their process, and to make small improvements as necessary. Kanban boards can be used to increase communication among teams and to identify and resolve any bottlenecks.
Kanban is also intended to reduce waste, as well as encourage information sharing. This is especially helpful when the company wants to adopt lean principles. There are many kinds of waste and it can add up during a manufacturing process. Manufacturers who eliminate waste are able to add real value to the entire manufacturing process. The kanban system is also useful in managing inventory. It can be used to manage inventory overstocking.
Kanban can be used to simplify the process and cut down on costs. It can improve the efficiency of the process and lead to a decrease in the number items necessary to complete a task. It is also a great way to increase communication and minimize downtime. The kanban method is a great example of how to use technology to accomplish a seemingly complex task.
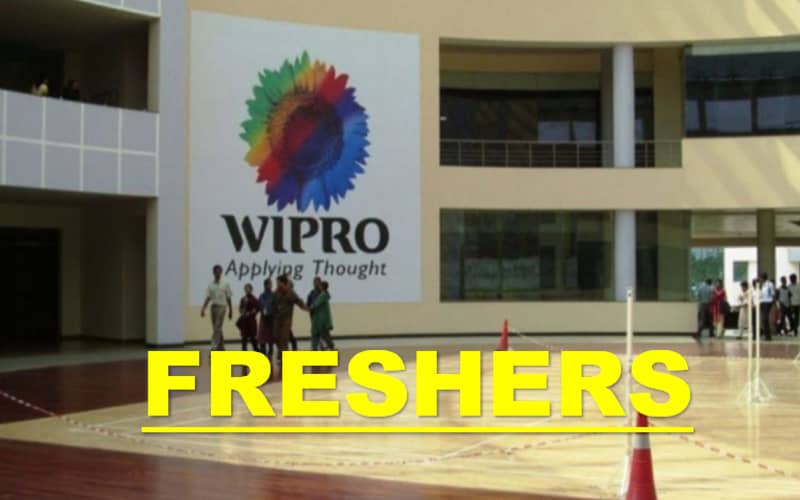
Kanban is also useful for brainstorming and productivity. It can be used for connecting companies with suppliers and improving communication. It improves quality and speeds up production.
A board is one of many common Kanban models in manufacturing. It allows tasks to be grouped according their priority and the time it takes to complete them. The board shows the steps involved in a process like design, manufacturing, testing, and maintenance.
FAQ
How does a Production Planner differ from a Project Manager?
The main difference between a production planner and a project manager is that a project manager is usually the person who plans and organizes the entire project, whereas a production planner is mainly involved in the planning stage of the project.
What is the job of a manufacturer manager?
The manufacturing manager should ensure that every manufacturing process is efficient and effective. They should also be aware of any problems within the company and act accordingly.
They should also know how to communicate with other departments such as sales and marketing.
They should also be knowledgeable about the latest trends in the industry so they can use this information for productivity and efficiency improvements.
Is it possible to automate certain parts of manufacturing
Yes! Yes! Automation has existed since ancient times. The Egyptians discovered the wheel thousands and years ago. To help us build assembly lines, we now have robots.
There are many applications for robotics in manufacturing today. These include:
-
Assembly line robots
-
Robot welding
-
Robot painting
-
Robotics inspection
-
Robots that produce products
Automation can be applied to manufacturing in many other ways. 3D printing makes it possible to produce custom products in a matter of days or weeks.
What jobs are available in logistics?
There are many kinds of jobs available within logistics. These are some of the jobs available in logistics:
-
Warehouse workers – They load, unload and transport pallets and trucks.
-
Transportation drivers - They drive trucks and trailers to deliver goods and carry out pick-ups.
-
Freight handlers: They sort and package freight in warehouses.
-
Inventory managers – They manage the inventory in warehouses.
-
Sales reps are people who sell products to customers.
-
Logistics coordinators are responsible for organizing and planning logistics operations.
-
Purchasing agents: They are responsible for purchasing goods and services to support company operations.
-
Customer service representatives - Answer calls and email from customers.
-
Shipping clerks - They process shipping orders and issue bills.
-
Order fillers - These people fill orders based on what has been ordered.
-
Quality control inspectors are responsible for inspecting incoming and outgoing products looking for defects.
-
Others - There are many other types of jobs available in logistics, such as transportation supervisors, cargo specialists, etc.
What are the main products of logistics?
Logistics refers to all activities that involve moving goods from A to B.
These include all aspects related to transport such as packaging, loading and transporting, storing, transporting, unloading and warehousing inventory management, customer service. Distribution, returns, recycling are some of the options.
Logisticians ensure that the product is delivered to the correct place, at the right time, and under safe conditions. They assist companies with their supply chain efficiency through information on demand forecasts. Stock levels, production times, and availability.
They coordinate with vendors and suppliers, keep track of shipments, monitor quality standards and perform inventory and order replenishment.
Statistics
- (2:04) MTO is a production technique wherein products are customized according to customer specifications, and production only starts after an order is received. (oracle.com)
- Job #1 is delivering the ordered product according to specifications: color, size, brand, and quantity. (netsuite.com)
- According to the United Nations Industrial Development Organization (UNIDO), China is the top manufacturer worldwide by 2019 output, producing 28.7% of the total global manufacturing output, followed by the United States, Japan, Germany, and India.[52][53] (en.wikipedia.org)
- It's estimated that 10.8% of the U.S. GDP in 2020 was contributed to manufacturing. (investopedia.com)
- In the United States, for example, manufacturing makes up 15% of the economic output. (twi-global.com)
External Links
How To
How to use 5S to increase Productivity in Manufacturing
5S stands to stand for "Sort", “Set In Order", “Standardize", and "Store". Toyota Motor Corporation was the first to develop the 5S approach in 1954. It improves the work environment and helps companies to achieve greater efficiency.
This method aims to standardize production processes so that they are repeatable, measurable and predictable. This means that daily tasks such as cleaning and sorting, storage, packing, labeling, and packaging are possible. Through these actions, workers can perform their jobs more efficiently because they know what to expect from them.
There are five steps to implementing 5S, including Sort, Set In Order, Standardize, Separate and Store. Each step requires a different action, which increases efficiency. Sorting things makes it easier to find them later. When you arrange items, you place them together. Then, after you separate your inventory into groups, you store those groups in containers that are easy to access. Labeling your containers will ensure that everything is correctly labeled.
Employees will need to be more critical about their work. Employees should understand why they do the tasks they do, and then decide if there are better ways to accomplish them. They must learn new skills and techniques in order to implement the 5S system.
The 5S method increases efficiency and morale among employees. As they begin to see improvements, they feel motivated to continue working towards the goal of achieving higher levels of efficiency.