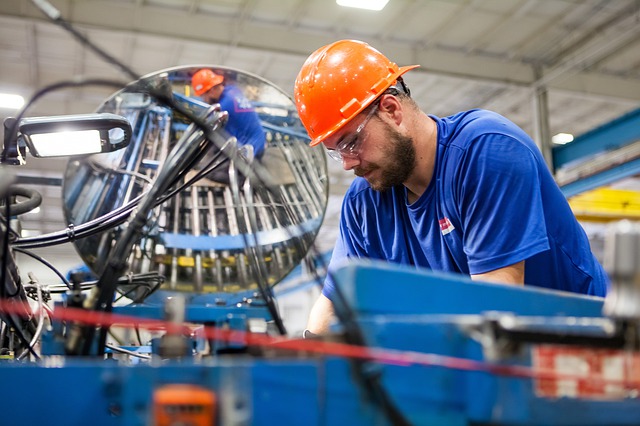
Six-Sigma, lean and Lean are complementary methods of improving processes. Although they both have the same tools for problem solving, each has its strengths and weaknesses. Six Sigma is a statistical process control technique. Lean starts with Lean's premise that a product must provide value, not just create it. Lean is about reducing waste and improving the quality of products as they are being made.
PDCA problem solving
While there are differences between DMAIC and PDCA, both approaches are based on DMAIC. Planning and analysis is required to complete the PDCA process. PDCA, unlike DMAIC is not effective in solving urgent problems. This approach requires a problem solver with technical skills. Six Sigma's problem-solving leader will need to be a Six Sigma "green belt" practitioner.
Six Sigma follows a cycle first introduced by W. Edwards Deming back in 1950s. It was developed to be used alongside continuous improvement methods to aid in rebuilding Japan's economy. The P (Plan) stage requires real data to be gathered and a clear mission. After the PDCA phase, the team must agree on a solution.
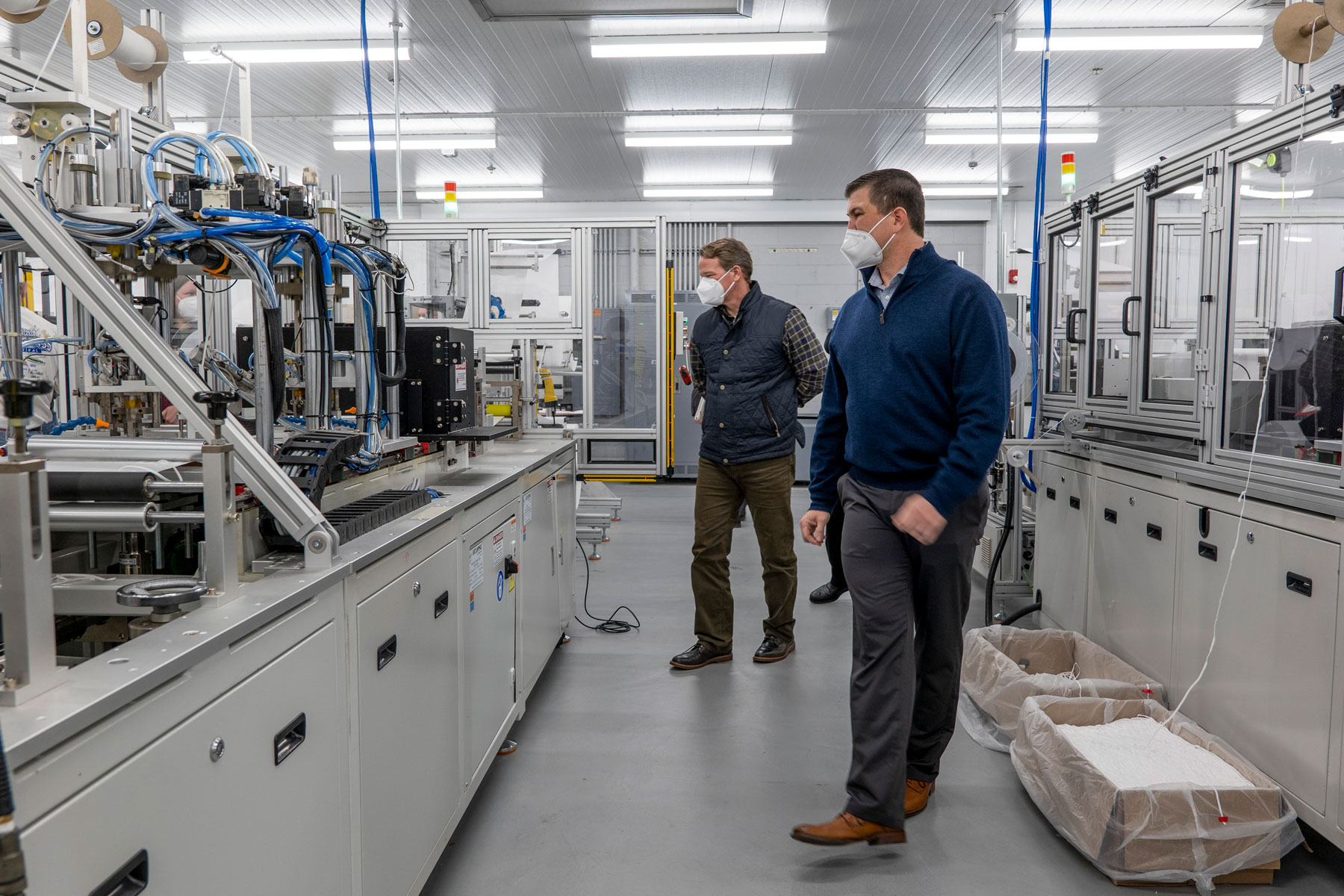
Process maps
Lean and Six Sigma processes maps have a significant difference in how they describe the processes. Both emphasize defining a process in detail, but each methodology focuses on different aspects of the process. Lean, for instance, involves mapping actual processes as opposed to standard operating procedures. Consider major decisions and approval sources when creating process maps. Include areas where multiple methods are used and factors that could hinder members. Make sure you match the roles and look at the process flow.
To illustrate the process flow, a process map must include steps, symbols, or arrows. To ensure the process is accurate, it should be reviewed by multiple people. It should also contain information about the date and who to call if you have any questions. Process maps are an excellent way to improve processes. They can be too complex.
Analysis of cause and effect
Six Sigma and lean project management techniques include statistical analysis and stochastic optimizing. The Cause and Effect Matrix is a way to link the steps in a process with their outputs and inputs. The customer's requirements are listed according to their importance. Outputs and inputs are ranked according the effect on the outcome. It is important to determine the ranking of key process input variables.
While each technique has a unique set of benefits, they are not the same. Lean Six Sigma uses a process management methodology that is based around Frederick Winslow Taylor’s Principles of Scientific Management. Taylor saw business processes in terms of interconnected processes and workflows. Taylor advocated reducing variation and also minimizing waste. Six-Sigma and Lean complement each other in the reduction of waste.
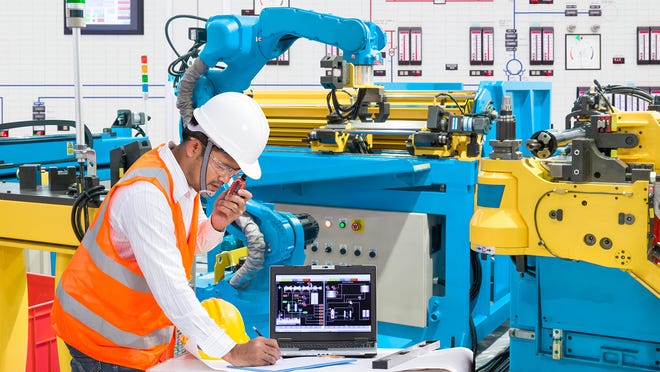
Eliminating Variation
Variation is a part of any manufacturing process. Variability in manufacturing processes can cause uncertainty regarding the outcome. Consistency is essential to provide professional results. Six Sigma and Lean manufacturing methods strive to eliminate variation. While some variation is acceptable, too much can lead to costly repairs and rework. The best way to manage variation is to identify the root cause.
The decision points are the best place to search for variations. Process maps show decision points and are represented by diamonds. Six Sigma teams can start by identifying decision points and start eliminating variations there. This information can be obtained from the Six Sigma team or the process owner. The Six Sigma Team cannot focus on any process that the owner isn't following a standardized process. The Six Sigma team may not have enough technical capacity to modify the process map in this instance.
FAQ
Are there any Manufacturing Processes that we should know before we can learn about Logistics?
No. No. However, knowing about manufacturing processes will definitely give you a better understanding of how logistics works.
Why is logistics important in manufacturing
Logistics are an essential component of any business. They can help you achieve great success by helping you manage product flow from raw material to finished goods.
Logistics play an important role in reducing costs as well as increasing efficiency.
How can manufacturing prevent production bottlenecks?
Production bottlenecks can be avoided by ensuring that processes are running smoothly during the entire production process, starting with the receipt of an order and ending when the product ships.
This includes planning to meet capacity requirements and quality control.
Continuous improvement techniques like Six Sigma are the best way to achieve this.
Six Sigma is a management system used to improve quality and reduce waste in every aspect of your organization.
It focuses on eliminating variation and creating consistency in your work.
What is the responsibility for a logistics manager
Logistics managers are responsible for ensuring that all goods arrive in perfect condition and on time. This is achieved by using their knowledge and experience with the products of the company. He/she also needs to ensure adequate stock to meet demand.
What is production plan?
Production Planning includes planning for all aspects related to production. This document ensures that everything is prepared and available when you are ready for shooting. This document should include information about how to achieve the best results on-set. This includes shooting schedules, locations, cast lists, crew details, and equipment requirements.
First, you need to plan what you want to film. You may already know where you want the film to be shot, or perhaps you have specific locations and sets you wish to use. Once you have identified your locations and scenes, you can start working out which elements you require for each scene. Perhaps you have decided that you need to buy a car but aren't sure which model. You could look online for cars to see what options are available, and then narrow down your choices by selecting between different makes or models.
Once you have found the right vehicle, you can think about adding accessories. What about additional seating? Perhaps you have someone who needs to be able to walk around the back of your car. Maybe you want to change the interior color from black to white? These questions will help you determine the exact look and feel of your car. It is also worth considering the types of shots that you wish to take. What type of shots will you choose? Maybe you want to show your engine or the steering wheel. These things will help you to identify the car that you are looking for.
Once you have all the information, you are ready to create a plan. You can create a schedule that will outline when you must start and finish your shoots. Each day will include the time when you need to arrive at the location, when you need to leave and when you need to return home. Everyone will know what they need and when. If you need to hire extra staff, you can make sure you book them in advance. There is no point in hiring someone who won't turn up because you didn't let him know.
Also, consider how many days you will be filming your schedule. Some projects take only a few days while others can last several weeks. It is important to consider whether you require more than one photo per day when you create your schedule. Multiplying takes in the same area will result both in increased costs and a longer time. If you are unsure if you need multiple takes, it is better to err on the side of caution and shoot fewer takes rather than risk wasting money.
Budget setting is an important part of production planning. It is important to set a realistic budget so you can work within your budget. Remember that you can always reduce the budget later on if you run into unforeseen problems. However, it is important not to overestimate the amount that you will spend. If you underestimate the cost of something, you will have less money left after paying for other items.
Production planning can be a complex process. However, once you know how everything works together it will become easier to plan future projects.
What are the 7 Rs of logistics.
The acronym 7R's of Logistic is an acronym that stands for seven fundamental principles of logistics management. It was developed by the International Association of Business Logisticians (IABL) and published in 2004 as part of its "Seven Principles of Logistics Management" series.
The acronym is made up of the following letters:
-
Responsible - ensure that actions are in compliance with legal requirements and do not cause harm to others.
-
Reliable: Have faith in your ability or the ability to honor any promises made.
-
It is reasonable to use resources efficiently and not waste them.
-
Realistic - Consider all aspects of operations, including environmental impact and cost effectiveness.
-
Respectful - Treat people fairly and equitably
-
Responsive - Look for ways to save time and increase productivity.
-
Recognizable - Provide value-added services to customers
What does it take for a logistics enterprise to succeed?
It takes a lot of skills and knowledge to run a successful logistics business. For clients and suppliers to be successful, you need to have excellent communication skills. It is important to be able to analyse data and draw conclusions. You must be able manage stress and pressure under pressure. You need to be innovative and creative to come up with new ways to increase efficiency. To motivate and guide your team towards reaching organizational goals, you must have strong leadership skills.
You should also be organized and efficient to meet tight deadlines.
Statistics
- According to the United Nations Industrial Development Organization (UNIDO), China is the top manufacturer worldwide by 2019 output, producing 28.7% of the total global manufacturing output, followed by the United States, Japan, Germany, and India.[52][53] (en.wikipedia.org)
- (2:04) MTO is a production technique wherein products are customized according to customer specifications, and production only starts after an order is received. (oracle.com)
- Many factories witnessed a 30% increase in output due to the shift to electric motors. (en.wikipedia.org)
- According to a Statista study, U.S. businesses spent $1.63 trillion on logistics in 2019, moving goods from origin to end user through various supply chain network segments. (netsuite.com)
- You can multiply the result by 100 to get the total percent of monthly overhead. (investopedia.com)
External Links
How To
Six Sigma in Manufacturing
Six Sigma can be described as "the use of statistical process control (SPC), techniques to achieve continuous improvement." It was developed by Motorola's Quality Improvement Department at their plant in Tokyo, Japan, in 1986. Six Sigma's main goal is to improve process quality by standardizing processes and eliminating defects. Many companies have adopted this method in recent years. They believe there is no such thing a perfect product or service. Six Sigma aims to reduce variation in the production's mean value. It is possible to measure the performance of your product against an average and find the percentage of time that it differs from the norm. If there is a significant deviation from the norm, you will know that something needs to change.
Understanding how variability works in your company is the first step to Six Sigma. Once you have this understanding, you will need to identify sources and causes of variation. It is important to identify whether the variations are random or systemic. Random variations occur when people do mistakes. Symmetrical variations are caused due to factors beyond the process. These are, for instance, random variations that occur when widgets are made and some fall off the production line. But if you notice that every widget you make falls apart at the exact same place each time, this would indicate that there is a problem.
Once you have identified the problem, you can design solutions. It might mean changing the way you do business or redesigning it entirely. Test them again once you've implemented the changes. If they don't work, you will need to go back to the drawing boards and create a new plan.