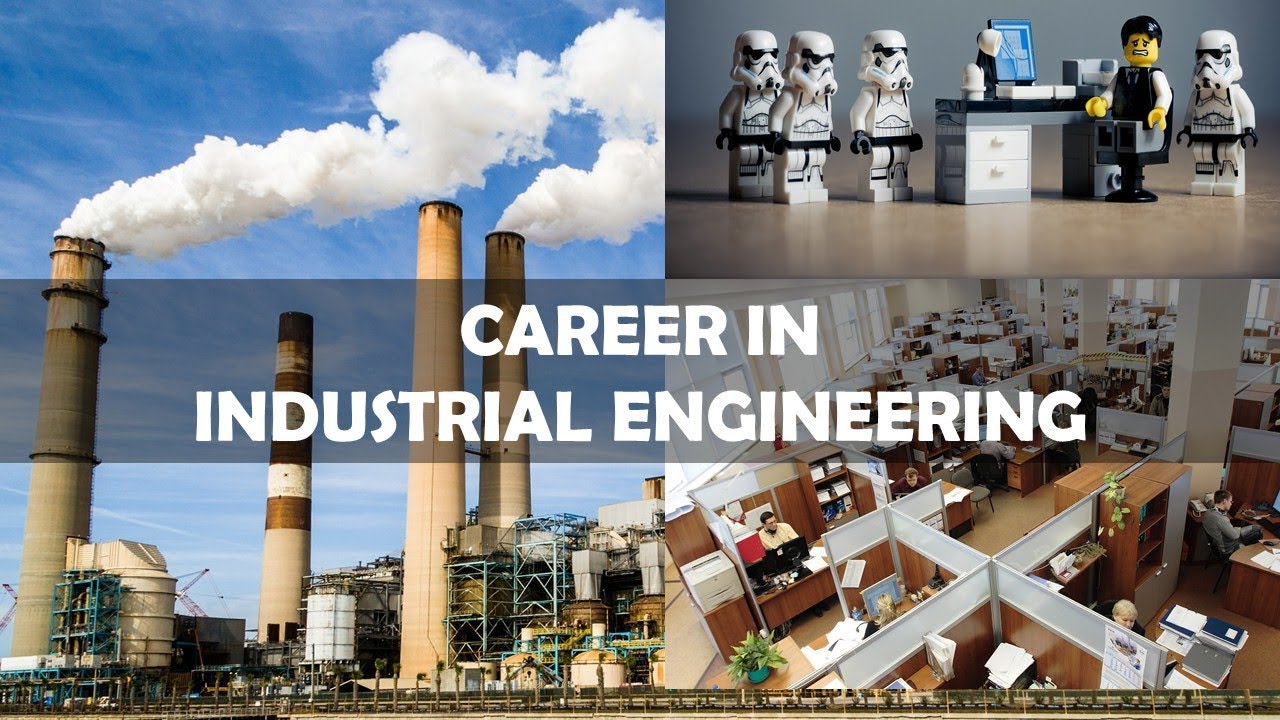
Mexico was one the major actors in DVA's trade network for global manufacturing exports, during the period under analysis. The automotive industry, while a larger export sector than the textiles, has not followed the same path. Both industries are important players on the Mexican export market and still have relevance for Mexico's job creation.
The Mexican automotive industry supplies the United States with the majority of its auto parts. It is also one of the fastest growing industries in Mexico. However, it has not been able to pull the rest of the economy onto a high expansion trajectory. In fact, the automotive industry is undergoing a transition from a domestic-oriented industry to a regional auto parts/automobile chain. This transition is a result of a combination international direct investment and regional processes.
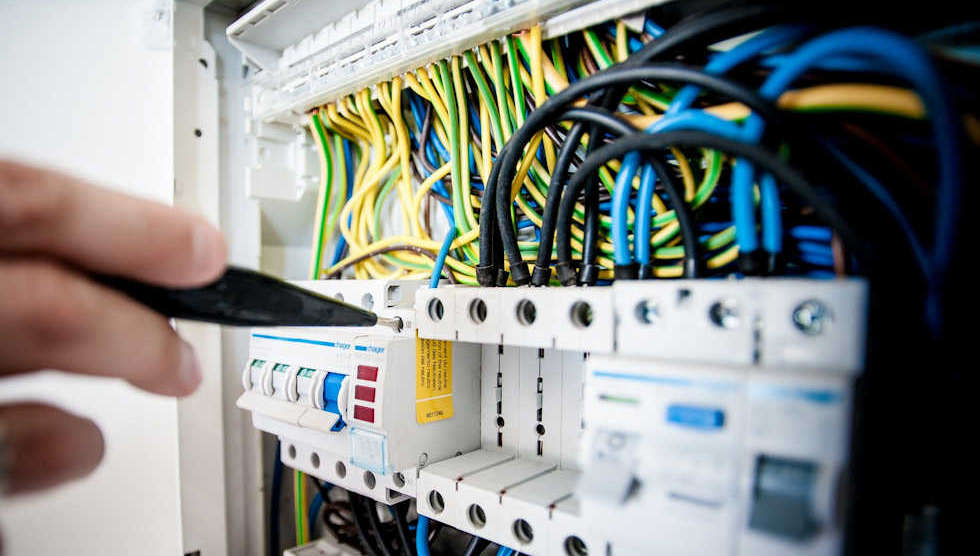
Many special Mexican development programs have benefited the automotive industry. It has been the top supplier of auto parts in the U.S. and has seen remarkable growth on international markets. It also has received foreign direct investment which has helped to increase its position in global value chains.
The Mexican automobile industry is also a key participant in the GVCs Europe and America. Mexico's automotive industry was a major part of its economy in the 1970s and 1980s. However, it has not achieved the same level of penetration in the world market as the textile industry has. In addition, it has not achieved a high level of expansion in its output, although it has achieved remarkable penetration into the world market.
The framework of decent work indicators created by the International Labour Organization is used to analyze the relationship between Mexican international trade and labor in the country's manufacturing sector. The indicators are based primarily on official data and consider the interconnections between Mexico's labor regulations and trade agreements. The indicators also include the input-output analysis of international trade, which shows that Mexico plays a relatively small role in the domestic value-added of global manufacturing exports.
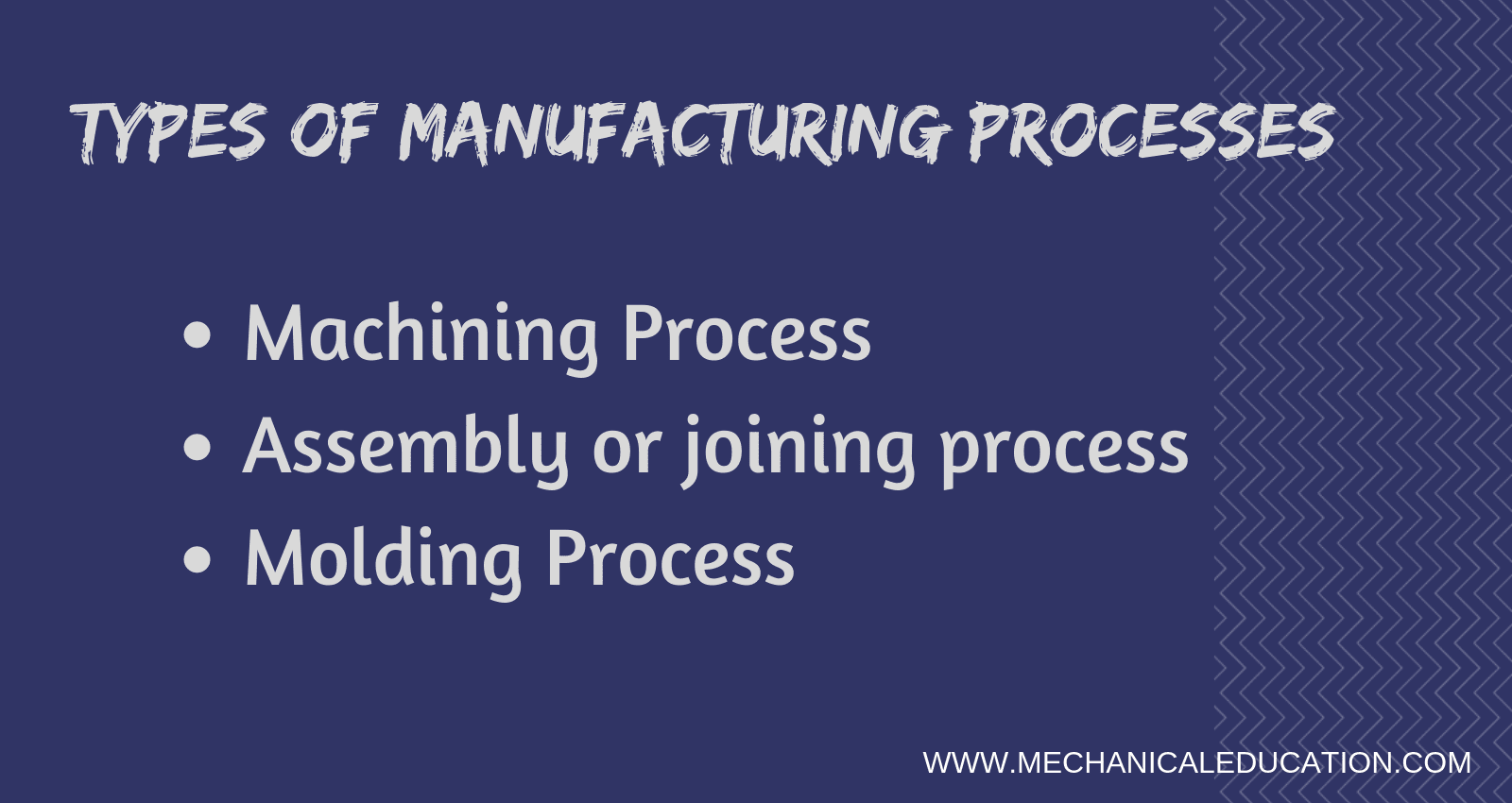
The study also examines the effects of trade liberalization on employment in the manufacturing industry of Mexico. It uses the System of National Accounts to build a set of indicators for decent work in two industrial areas of Mexico. It constructs a time series of these indicators and uses them to assess the evolution of decent work in Mexico. The study shows that DVAG VC in the manufacturing sector is lower than in its counterpart in the textiles sector. In the same way, the study found that the level for employment in automobile industry is lower then in the textile. The study also finds that real wages have decreased since the beginning. In other words, the nominal wage adjustment was not enough to compensate for the deterioration of real wages. The study found that DVA in transportation equipment exports has been increasing over the past decade, while DVA in textile exports have declined.
FAQ
What are the logistics products?
Logistics refers to all activities that involve moving goods from A to B.
They encompass all aspects transport, including packaging and loading, transporting, storage, unloading.
Logisticians ensure that products reach the right destination at the right moment and under safe conditions. They assist companies with their supply chain efficiency through information on demand forecasts. Stock levels, production times, and availability.
They also keep track of shipments in transit, monitor quality standards, perform inventories and order replenishment, coordinate with suppliers and vendors, and provide support services for sales and marketing.
What type of jobs is there in logistics
Logistics can offer many different jobs. Here are some examples:
-
Warehouse workers - They load and unload trucks and pallets.
-
Transportation drivers – They drive trucks or trailers to transport goods and perform pick-ups.
-
Freight handlers - They sort and pack freight in warehouses.
-
Inventory managers – These people oversee inventory at warehouses.
-
Sales representatives - They sell products.
-
Logistics coordinators - They plan and organize logistics operations.
-
Purchasing agents – They buy goods or services necessary to run a company.
-
Customer service representatives – They answer emails and phone calls from customers.
-
Shipping clerks – They process shipping orders, and issue bills.
-
Order fillers are people who fill orders based only on what was ordered.
-
Quality control inspectors (QCI) - They inspect all incoming and departing products for potential defects.
-
Others - There are many other types of jobs available in logistics, such as transportation supervisors, cargo specialists, etc.
What are the 7 Rs of logistics?
The 7R's of Logistics is an acronym for the seven basic principles of logistics management. It was developed by the International Association of Business Logisticians (IABL) and published in 2004 as part of its "Seven Principles of Logistics Management" series.
The following letters make up the acronym:
-
Responsible - ensure that all actions taken are within legal requirements and are not harmful to others.
-
Reliable - You can have confidence that you will fulfill your promises.
-
Reasonable - use resources efficiently and don't waste them.
-
Realistic - consider all aspects of operations, including cost-effectiveness and environmental impact.
-
Respectful: Treat others with fairness and equity
-
You are resourceful and look for ways to save money while increasing productivity.
-
Recognizable: Provide customers with value-added service
Can certain manufacturing steps be automated?
Yes! Automation has been around since ancient times. The Egyptians invent the wheel thousands of year ago. We now use robots to help us with assembly lines.
Robotics is used in many manufacturing processes today. These include:
-
Automated assembly line robots
-
Robot welding
-
Robot painting
-
Robotics inspection
-
Robots that create products
Manufacturing can also be automated in many other ways. 3D printing makes it possible to produce custom products in a matter of days or weeks.
How can overproduction in manufacturing be reduced?
The key to reducing overproduction lies in developing better ways to manage inventory. This would reduce the time spent on unproductive activities like purchasing, storing and maintaining excess stock. This would allow us to use our resources for more productive tasks.
You can do this by adopting a Kanban method. A Kanban board can be used to monitor work progress. Work items are moved through various states to reach their destination in a Kanban system. Each state represents an individual priority level.
When work is completed, it can be transferred to the next stage. But if a task remains in the beginning stages it will stay that way until it reaches its end.
This allows you to keep work moving along while making sure that no work gets neglected. Managers can see how much work has been done and the status of each task at any time with a Kanban Board. This allows them the ability to adjust their workflow using real-time data.
Lean manufacturing is another option to control inventory levels. Lean manufacturing emphasizes eliminating waste in all phases of production. Anything that does nothing to add value to a product is waste. These are some of the most common types.
-
Overproduction
-
Inventory
-
Unnecessary packaging
-
Material surplus
These ideas will help manufacturers increase efficiency and lower costs.
Statistics
- It's estimated that 10.8% of the U.S. GDP in 2020 was contributed to manufacturing. (investopedia.com)
- In 2021, an estimated 12.1 million Americans work in the manufacturing sector.6 (investopedia.com)
- You can multiply the result by 100 to get the total percent of monthly overhead. (investopedia.com)
- According to the United Nations Industrial Development Organization (UNIDO), China is the top manufacturer worldwide by 2019 output, producing 28.7% of the total global manufacturing output, followed by the United States, Japan, Germany, and India.[52][53] (en.wikipedia.org)
- Many factories witnessed a 30% increase in output due to the shift to electric motors. (en.wikipedia.org)
External Links
How To
Six Sigma and Manufacturing
Six Sigma is defined as "the application of statistical process control (SPC) techniques to achieve continuous improvement." Motorola's Quality Improvement Department, Tokyo, Japan, developed it in 1986. Six Sigma is a method to improve quality through standardization and elimination of defects. Many companies have adopted this method in recent years. They believe there is no such thing a perfect product or service. The main goal of Six Sigma is to reduce variation from the mean value of production. This means that you can take a sample from your product and then compare its performance to the average to find out how often the process differs from the norm. If this deviation is too big, you know something needs fixing.
Understanding how variability works in your company is the first step to Six Sigma. Once you have a good understanding of the basics, you can identify potential sources of variation. It is important to identify whether the variations are random or systemic. Random variations are caused by human errors. Systematic variations can be caused by outside factors. For example, if you're making widgets, and some of them fall off the assembly line, those would be considered random variations. However, if you notice that every time you assemble a widget, it always falls apart at exactly the same place, then that would be a systematic problem.
Once you have identified the problem, you can design solutions. It might mean changing the way you do business or redesigning it entirely. Once you have implemented the changes, it is important to test them again to ensure they work. If they don't work, you will need to go back to the drawing boards and create a new plan.