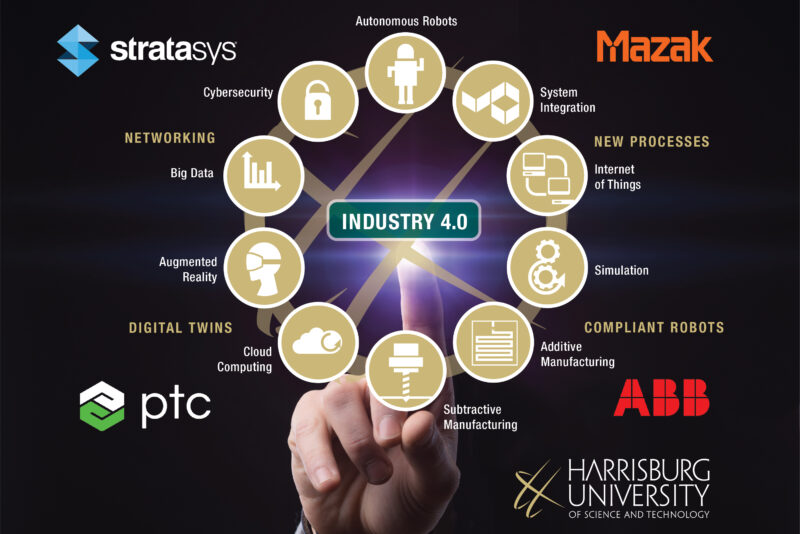
There are many manufacturers. But which one is right for you? Learn about Discrete, Process, Job shop, and Continuous manufacturing. Each type has its pros and cons. This article will detail the differences in these four types. The factors that are most relevant to your business include your industry, geographical location, and product type. Once you decide which type is best for your company, you'll need to consider your sales, production, and quality control.
Displacement manufacturing
Discrete Manufacturing is the process of producing distinct products. These products can include toys, airplanes, and automobiles. Discrete manufacturing allows companies the freedom to concentrate on specific products rather than mass production. It is possible, for instance, to make unique parts of an aeroplane through the integration of several manufacturing processes. Discrete manufacturing is a popular way to manufacture high-tech items.
Discrete manufacturing produces distinct items. Instead of producing many identical products discrete manufacturing creates items that are easily identifiable by serial numbers and labels. One example of this is a smartphone made up different parts in different states. Once the product has been shipped, the parts are assembled. The bag of your smartphone is the same. It might contain different parts of several plants, including the Missouri plant and headquarters.
Process manufacturing
The term process manufacturing is a branch in manufacturing that involves formulas and recipe. The term process manufacturing is not the same as discrete manufacturing. This refers to manufacturing that involves individual units, bills or materials and the assembly of component parts. Both manufacturing methods have different goals. But each one is an important part of the manufacturing process. Here are three methods to distinguish between discrete and process manufacturing. Let's look at each one.
Batch process manufacturing is similar to continuous process manufacturing, but it uses larger batches of raw materials and runs around the clock. Batch process manufacturing can be found in paper production, pharmaceuticals, bookbinding, newspaper printing, and other industries. This method may not be the right fit for all industries. This method can be too difficult and expensive to use by small businesses. This method is used by most companies when they need large quantities of the exact same product.
Factory job shop
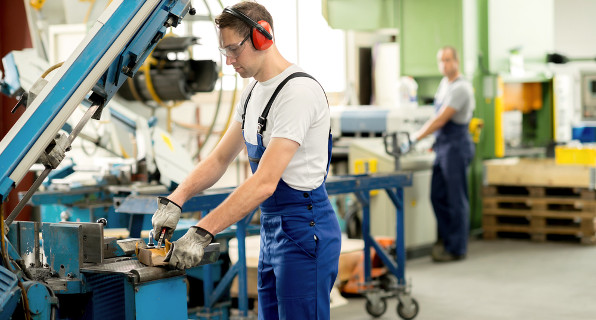
A job shop manufacturing system is a small-scale production facility that specializes on custom, batch, or semi-custom manufacturing. After each job is complete, job shop systems can move to the next. This production method is also known as lean manufacturing. A single shift operation is more efficient than other methods. Here are some of the benefits of job shop manufacturing. Continue reading to learn more about job shop manufacturing. This method of manufacturing might be beneficial for your business.
First, job shops must be more efficient. Incorporating new manufacturing principles is key to achieving lean manufacturing systems. These principles focus on quality control and justin-time production and are especially relevant for high-volume operations. Job shops can increase productivity and decrease costs by adopting new manufacturing methods. Each job must be done one at a given time. There should not be any waiting.
Continuous manufacturing
Continuous manufacturing offers many benefits, including the flexibility of tracking. This is especially useful when it comes down to product failure. Because the production lines can track the amount of raw materials and the time stamp, this information can be used to identify defective batches of drugs. The manufacturer can also reduce the risk of product shortages and waste by increasing their tracking. In the pharmaceutical industry, continuous manufacturing is also gaining popularity.
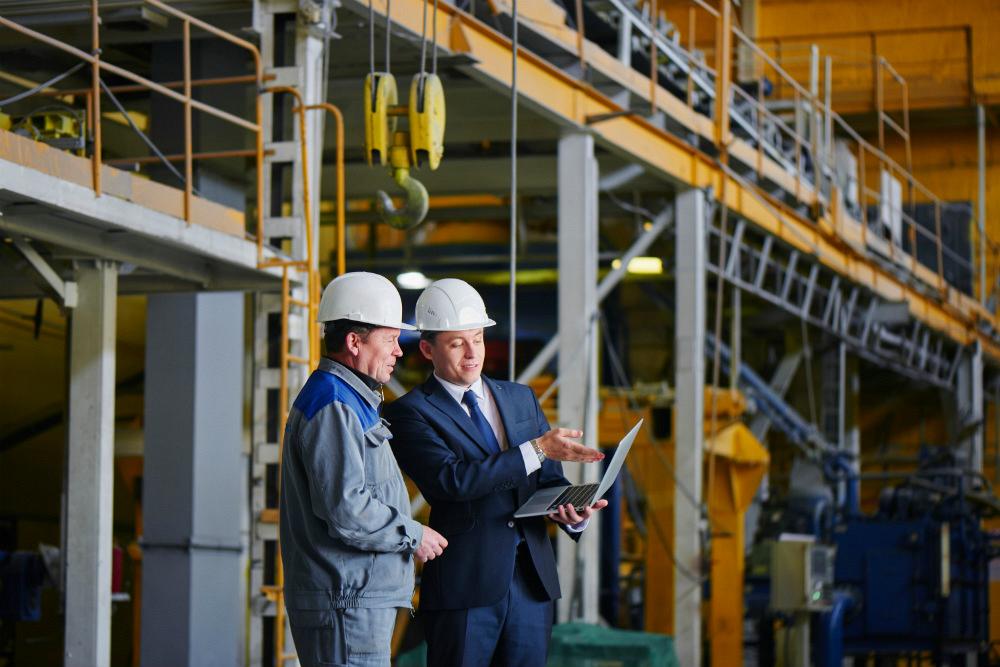
However, while the benefits of continuous manufacturing are clear, implementation is slow. Implementation can be difficult because the process is not fully integrated within the company. Continuous manufacturing, despite its potential benefits, has the potential for a major shift in the pharmaceutical industry. But to be successful, the process must be integrated with end-to-end integration and continuous flow. While the benefits of continuous manufacturing have been well-known in the pharmaceutical sector, implementation has been slow.
FAQ
Why should you automate your warehouse?
Modern warehouses have become more dependent on automation. E-commerce has increased the demand for quicker delivery times and more efficient processes.
Warehouses must adapt quickly to meet changing customer needs. Technology is essential for warehouses to be able to adapt quickly to changing needs. Automation warehouses can bring many benefits. Here are some benefits of investing in automation
-
Increases throughput/productivity
-
Reduces errors
-
Increases accuracy
-
Safety enhancements
-
Eliminates bottlenecks
-
Companies can scale up more easily
-
Makes workers more efficient
-
Gives you visibility into all that is happening in your warehouse
-
Enhances customer experience
-
Improves employee satisfaction
-
It reduces downtime, and increases uptime
-
You can be sure that high-quality products will arrive on time
-
Eliminates human error
-
Helps ensure compliance with regulations
Why is logistics important in manufacturing?
Logistics are an essential component of any business. They can help you achieve great success by helping you manage product flow from raw material to finished goods.
Logistics are also important in reducing costs and improving efficiency.
How can manufacturing excess production be decreased?
Better inventory management is key to reducing excess production. This would reduce the amount of time spent on unnecessary activities such as purchasing, storing, and maintaining excess stock. We could use these resources to do other productive tasks.
This can be done by using a Kanban system. A Kanban board can be used to monitor work progress. Work items are moved through various states to reach their destination in a Kanban system. Each state represents an individual priority level.
As an example, if work is progressing from one stage of the process to another, then the current task is complete and can be transferred to the next. However, if a task is still at the beginning stages, it will remain so until it reaches the end of the process.
This helps to keep work moving forward while ensuring that no work is left behind. Managers can see how much work has been done and the status of each task at any time with a Kanban Board. This allows them the ability to adjust their workflow using real-time data.
Lean manufacturing is another way to manage inventory levels. Lean manufacturing seeks to eliminate waste from every step of the production cycle. Waste includes anything that does not add value to the product. Some common types of waste include:
-
Overproduction
-
Inventory
-
Unnecessary packaging
-
Overstock materials
These ideas will help manufacturers increase efficiency and lower costs.
What are the main products of logistics?
Logistics involves the transportation of goods from point A and point B.
These include all aspects related to transport such as packaging, loading and transporting, storing, transporting, unloading and warehousing inventory management, customer service. Distribution, returns, recycling are some of the options.
Logisticians ensure that the right product reaches the right place at the right time and under safe conditions. They assist companies with their supply chain efficiency through information on demand forecasts. Stock levels, production times, and availability.
They also keep track of shipments in transit, monitor quality standards, perform inventories and order replenishment, coordinate with suppliers and vendors, and provide support services for sales and marketing.
What are the 7 Rs of logistics.
The acronym 7R's for Logistics stands to represent the seven basic principles in logistics management. It was created by the International Association of Business Logisticians and published in 2004 under its "Seven Principles of Logistics Management".
The acronym is made up of the following letters:
-
Responsible - ensure that all actions taken are within legal requirements and are not harmful to others.
-
Reliable – have faith in your ability and capability to keep promises.
-
Be responsible - Use resources efficiently and avoid wasting them.
-
Realistic - Consider all aspects of operations, including environmental impact and cost effectiveness.
-
Respectful: Treat others with fairness and equity
-
You are resourceful and look for ways to save money while increasing productivity.
-
Recognizable: Provide customers with value-added service
What skills should a production planner have?
You must be flexible and organized to become a productive production planner. Effective communication with clients and colleagues is essential.
Statistics
- According to the United Nations Industrial Development Organization (UNIDO), China is the top manufacturer worldwide by 2019 output, producing 28.7% of the total global manufacturing output, followed by the United States, Japan, Germany, and India.[52][53] (en.wikipedia.org)
- In the United States, for example, manufacturing makes up 15% of the economic output. (twi-global.com)
- In 2021, an estimated 12.1 million Americans work in the manufacturing sector.6 (investopedia.com)
- [54][55] These are the top 50 countries by the total value of manufacturing output in US dollars for its noted year according to World Bank.[56] (en.wikipedia.org)
- (2:04) MTO is a production technique wherein products are customized according to customer specifications, and production only starts after an order is received. (oracle.com)
External Links
How To
Six Sigma in Manufacturing:
Six Sigma is defined as "the application of statistical process control (SPC) techniques to achieve continuous improvement." Motorola's Quality Improvement Department, Tokyo, Japan, developed it in 1986. Six Sigma's core idea is to improve the quality of processes by standardizing and eliminating defects. Many companies have adopted this method in recent years. They believe there is no such thing a perfect product or service. The main goal of Six Sigma is to reduce variation from the mean value of production. This means that you can take a sample from your product and then compare its performance to the average to find out how often the process differs from the norm. If it is too large, it means that there are problems.
Understanding how variability works in your company is the first step to Six Sigma. Once you've understood that, you'll want to identify sources of variation. You'll also want to determine whether these variations are random or systematic. Random variations are caused when people make mistakes. While systematic variations are caused outside of the process, they can occur. These are, for instance, random variations that occur when widgets are made and some fall off the production line. If however, you notice that each time you assemble a widget it falls apart in exactly the same spot, that is a problem.
Once you identify the problem areas, it is time to create solutions. This could mean changing your approach or redesigning the entire process. You should then test the changes again after they have been implemented. If they didn't work, then you'll need to go back to the drawing board and come up with another plan.