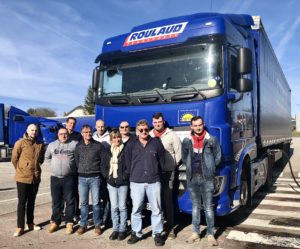
What is supply chain management? The answer is a cross-functional process that focuses on the management of relationships throughout the entire supply chain. Supply chain management can improve overall business performance by improving financial and operational performance. This article will provide a basic definition of supply chain management and how it can improve your organization. Let's dive in! What is supply management? Why is supply chain management important? Here are some examples of how it could benefit your company.
Supply chain management involves the management and coordination of all relationships in the supply chain
Companies that produce and sell products need to consider how to obtain raw materials, produce parts, and distribute finished goods. The physical flow and distribution of goods begins at the supplier. They then move through many steps to a manufacturer and distributor. Finally, they reach the end customer. Although some supply chains skip certain steps altogether, physical items need to be moved from one place to the next, stored for a while, and then be delivered to their destination. This process requires organization and planning.
Successful supply chain management requires integrating all business functions. For example, vendors and suppliers must have clear communications. Information sharing helps both sides know what to expect and reduces costs. It also improves quality. Collaboration improves communication across the supply chains and helps both parties. The customer must have an understanding of the company's operation and the vendor should know how to deliver urgent materials. Lead times are particularly critical when a company is selling perishable goods.
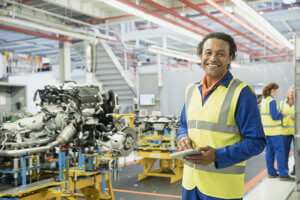
It is cross-functional and business-related.
Many factors are important to consider when it comes down to a company’s supply chain. Supply chain success depends on suppliers being able to deliver goods in a timely manner. It is crucial to coordinate with them. Companies can avoid many problems by following the steps described in Supply Chain Management. This will not only improve efficiency but also save them money.
In addition to understanding the interdependencies of the supply chain, management needs to work toward increasing the profitability of the entire system. All parties should be able to benefit equally from improvements in process, but it is important that there are guidelines about how the rewards will be shared. A common measurement system may be required in order to ensure that all parties can see the benefits of an improved process. It may be deemed uneffective if the value cannot be captured.
It reduces operating costs
Streamlining your ordering processes is one of best ways to reduce operating expenses. Your employees will be more likely to use one software system for all requisitions. A process for approval can be set up to limit the quantity of goods ordered. This will help to lower operating costs. A streamlined software system can help you avoid confusion and errors, monitor your inventory and order only what you need. It will also allow you to stop shipments being made if you are not required.
One way to cut operating costs is to improve the communication between warehouse employees. This process should start with examining the current workflow and identify any bottlenecks that are making the process inefficient. Consolidating or using dedicated transport services can help reduce transportation costs. This will reduce your operating expenses by a substantial amount. This will help you not only lower your transport costs but also speed up the delivery of your products.
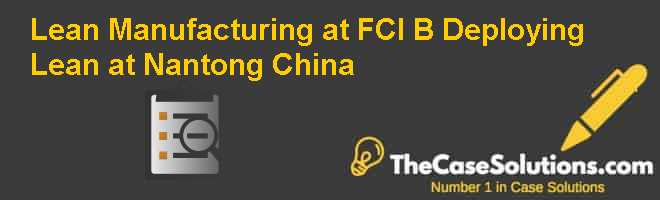
It improves your financial position
The financial performance of a company can be improved in several ways by good supply chain management. Supply chain managers who are skilled in managing supply chains can help to reduce production costs and maximize variable costs. Profit margins can be increased by being able to control costs. Another major benefit is an increase in cash flow. Customers can be invoiced earlier if products are delivered faster, which reduces the need to buy expensive space. Also, a better supply channel reduces fixed asset costs.
The Statement of Shareholders Equity (SSE), a key financial statement, summarizes ownership of a company. A firm can improve its supply chain to increase its after-tax cashflow by around 8.5%. A company can improve its supply chain performance to reduce its costs and increase its customer satisfaction. A company that improves its supply chain management can reduce costs by as much as 10% while increasing customer satisfaction. This will lead to higher operational efficiencies and consequently, greater profits.
FAQ
What are the responsibilities for a manufacturing manager
The manufacturing manager should ensure that every manufacturing process is efficient and effective. They should be alert for any potential problems in the company and react accordingly.
They must also be able to communicate with sales and marketing departments.
They should also be aware of the latest trends in their industry and be able to use this information to help improve productivity and efficiency.
How can manufacturing avoid production bottlenecks
The key to avoiding bottlenecks in production is to keep all processes running smoothly throughout the entire production cycle, from the time you receive an order until the time when the product ships.
This includes planning for both capacity requirements and quality control measures.
Continuous improvement techniques such Six Sigma can help you achieve this.
Six Sigma Management System is a method to increase quality and reduce waste throughout your organization.
It focuses on eliminating variation and creating consistency in your work.
What are the main products of logistics?
Logistics refers to all activities that involve moving goods from A to B.
They cover all aspects of transportation, such as packing, loading, transporting and unloading.
Logisticians make sure that the right product arrives at the right place at the correct time and in safe conditions. Logisticians help companies improve their supply chain efficiency by providing information about demand forecasts and stock levels, production schedules, as well as availability of raw materials.
They monitor shipments in transit, ensure quality standards, manage inventories, replenish orders, coordinate with suppliers and other vendors, and offer support services for sales, marketing, and customer service.
Statistics
- According to a Statista study, U.S. businesses spent $1.63 trillion on logistics in 2019, moving goods from origin to end user through various supply chain network segments. (netsuite.com)
- In 2021, an estimated 12.1 million Americans work in the manufacturing sector.6 (investopedia.com)
- In the United States, for example, manufacturing makes up 15% of the economic output. (twi-global.com)
- [54][55] These are the top 50 countries by the total value of manufacturing output in US dollars for its noted year according to World Bank.[56] (en.wikipedia.org)
- It's estimated that 10.8% of the U.S. GDP in 2020 was contributed to manufacturing. (investopedia.com)
External Links
How To
Six Sigma and Manufacturing
Six Sigma is defined by "the application SPC (statistical process control) techniques to achieve continuous improvements." It was developed by Motorola's Quality Improvement Department at their plant in Tokyo, Japan, in 1986. Six Sigma is a method to improve quality through standardization and elimination of defects. In recent years, many companies have adopted this method because they believe there is no such thing as perfect products or services. Six Sigma seeks to reduce variation between the mean production value. This means that you can take a sample from your product and then compare its performance to the average to find out how often the process differs from the norm. If you notice a large deviation, then it is time to fix it.
Understanding how variability works in your company is the first step to Six Sigma. Once you've understood that, you'll want to identify sources of variation. These variations can also be classified as random or systematic. Random variations happen when people make errors; systematic variations are caused externally. For example, if you're making widgets, and some of them fall off the assembly line, those would be considered random variations. But if you notice that every widget you make falls apart at the exact same place each time, this would indicate that there is a problem.
Once you've identified the problem areas you need to find solutions. This could mean changing your approach or redesigning the entire process. Once you have implemented the changes, it is important to test them again to ensure they work. If they didn't work, then you'll need to go back to the drawing board and come up with another plan.