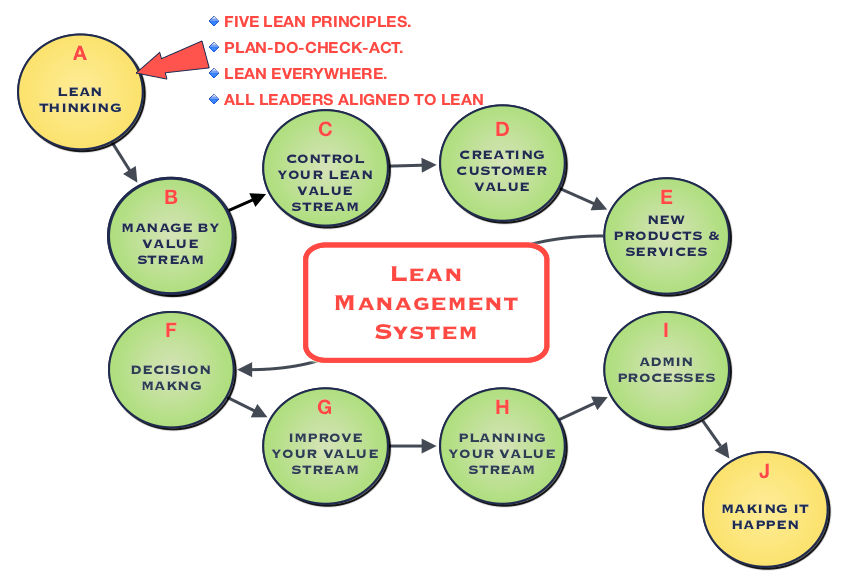
The manufacturing strategy helps a business identify the differentiators that it has over its competitors and concentrates on those areas. This is vital to building a long-term competitive advantage.
Your manufacturing strategy should match your business goals and mission statement. It should also be backed by strong team leadership. It will help to ensure that resources are allocated correctly and that all employees know their roles in the success of the business.
To accomplish this, your team needs to discuss and divide up all the key areas you need to address in order for your strategy of manufacturing success. Once your team has discussed and divided up the key areas, you will be able to create a specific plan for each.
Your team can discuss how to improve the efficiency and quality of their work, for instance, if your goal is to increase productivity. This is vital, as improving your employee's performance will result in an improved working environment for both them and the company.
In the same vein you can look at your total production capacity and decide if it's adequate for your business now and into the future. In this case, you might need to invest into new equipment or in a better location.
Your production process must be efficient and economical, no matter what type of product you are producing. It is crucial to reduce waste and meet customer demands.
One of the best ways to improve your production processes is by improving your inventory management system. By using a stock tracking system, you can easily identify the inventory levels that need to be changed. This will make sure that you don't overstock your inventory and end up having many unsold items.
Another great way to reduce the amount of stock that you produce is by making to order. This is great for businesses offering niche products that can't be found on the highstreet.
You can produce finished products when they are needed rather than waiting to receive orders. It can help you reduce the inventory and associated costs.
Once your product has been confirmed, you can choose to assemble it. This will allow you to save on materials and labour by not producing large quantities of stock. This is a good manufacturing strategy for organisations that want to keep their production process as simple and efficient as possible, but still provide a wide range of products for their customers.
To implement this strategy, you must have a solid understanding of the products you manufacture and how they will be manufactured. This is particularly important if your company produces products that are exclusive to it or if the industry you're in has complicated specifications.
FAQ
How does a Production Planner differ from a Project Manager?
The main difference between a production planner and a project manager is that a project manager is usually the person who plans and organizes the entire project, whereas a production planner is mainly involved in the planning stage of the project.
Why is logistics so important in manufacturing?
Logistics are essential to any business. They help you achieve great results by helping you manage all aspects of product flow, from raw materials to finished goods.
Logistics play a key role in reducing expenses and increasing efficiency.
How can manufacturing prevent production bottlenecks?
Avoiding production bottlenecks is as simple as keeping all processes running smoothly, from the time an order is received until the product ships.
This includes both quality control and capacity planning.
Continuous improvement techniques such Six Sigma can help you achieve this.
Six Sigma Management System is a method to increase quality and reduce waste throughout your organization.
It is focused on creating consistency and eliminating variation in your work.
Statistics
- Job #1 is delivering the ordered product according to specifications: color, size, brand, and quantity. (netsuite.com)
- In the United States, for example, manufacturing makes up 15% of the economic output. (twi-global.com)
- You can multiply the result by 100 to get the total percent of monthly overhead. (investopedia.com)
- According to the United Nations Industrial Development Organization (UNIDO), China is the top manufacturer worldwide by 2019 output, producing 28.7% of the total global manufacturing output, followed by the United States, Japan, Germany, and India.[52][53] (en.wikipedia.org)
- [54][55] These are the top 50 countries by the total value of manufacturing output in US dollars for its noted year according to World Bank.[56] (en.wikipedia.org)
External Links
How To
How to Use Six Sigma in Manufacturing
Six Sigma can be described as "the use of statistical process control (SPC), techniques to achieve continuous improvement." Motorola's Quality Improvement Department in Tokyo, Japan developed Six Sigma in 1986. Six Sigma's basic concept is to improve quality and eliminate defects through standardization. Since there are no perfect products, or services, this approach has been adopted by many companies over the years. The main goal of Six Sigma is to reduce variation from the mean value of production. This means that if you take a sample of your product, then measure its performance against the average, you can find out what percentage of the time the process deviates from the norm. If you notice a large deviation, then it is time to fix it.
The first step toward implementing Six Sigma is understanding how variability works in your business. Once you've understood that, you'll want to identify sources of variation. This will allow you to decide if these variations are random and systematic. Random variations are caused when people make mistakes. While systematic variations are caused outside of the process, they can occur. For example, if you're making widgets, and some of them fall off the assembly line, those would be considered random variations. But if you notice that every widget you make falls apart at the exact same place each time, this would indicate that there is a problem.
Once you've identified the problem areas you need to find solutions. That solution might involve changing the way you do things or redesigning the process altogether. You should then test the changes again after they have been implemented. If they don't work you need to rework them and come up a better plan.