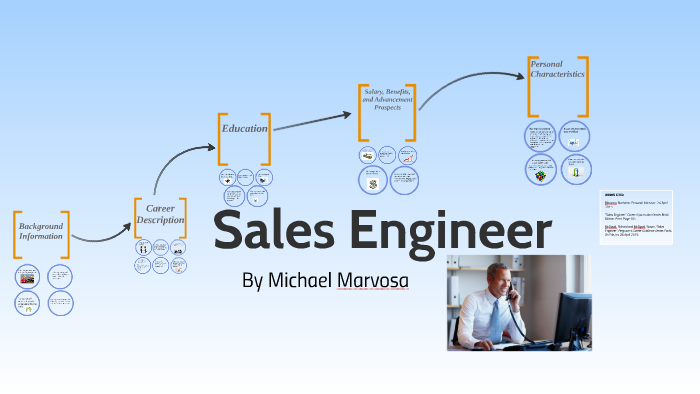
The Lean 5 principles stress the elimination of all waste, even those that don't add value to the product. The principles also promote value stream mapping to identify activities that can be done more efficiently. The key to eliminating waste is to separate value-added, (necessary), waste from non-value added (unnecessary). The most efficient process uses less energy, time and materials by eliminating redundant steps. This allows you to produce high-quality products in a shorter time and keeps customers satisfied.
Value
You can improve the flow of manufacturing by eliminating waste using the Value of Lean 5 principles. It is possible to create smooth flows from production to shipping by eliminating steps that are not adding value. The process also eliminates excess inventory and helps you reduce work in progress and save time.
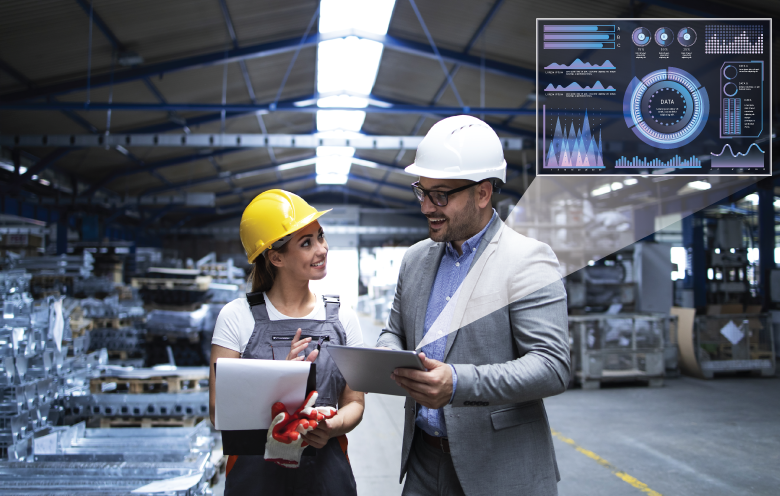
Value stream
The value stream of Lean Manufacturing is a way to eliminate waste from manufacturing processes. This process maps out each step in a process to identify the elements that are necessary and eliminate those that are not. The value stream takes into account the whole life cycle of a product - from the initial idea to the use of the product and its eventual disposal. This process is crucial to eliminate waste. There are three types of waste in a value stream.
Flow
The first of 5 lean principles, Flow, involves identifying customers' actual needs and evaluating them. This is an important step in the design process for new products and/or services. Customers do not always articulate their needs clearly. The second step in the process is to determine the value stream. It's the sequence of activities required to complete the project. This requires close collaboration from all project participants.
Pull
A pull system is only able to start a process when there is a customer request. For example, a pizza restaurant would not make extra pizzas; they would only produce food when they have received a customer order. A restaurant would not waste their time, resources, or ingredients if they did.
Perfection
One of the lean 5 principles is the pursuit of perfection. According to this concept perfection is an ideal state which is accurate, complete, and consistent. But perfection is not possible. This idea is meant to encourage continuous improvement. This helps organizations to achieve a higher level performance.
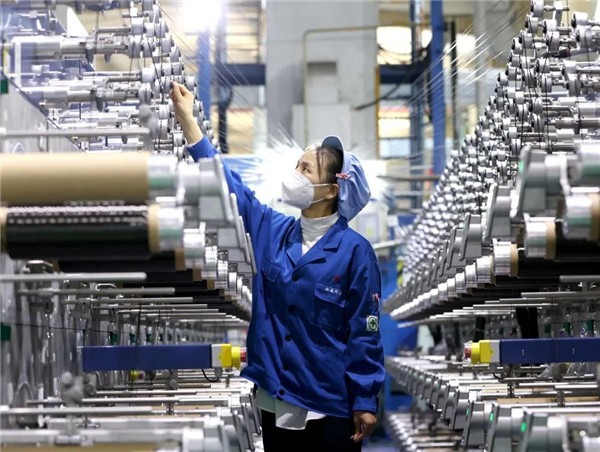
Collaboration among stakeholders
Collaboration between stakeholders is an important element of lean project managing. It involves collaboration between project team members in order to solve problems and increase the value of the project. Teams must identify the problems and areas that need improvement in order to plan. The doing phase is less about execution, but more about gathering data that will help them find solutions. The organizational structure is also important for team collaboration.
FAQ
What's the difference between Production Planning & Scheduling?
Production Planning (PP), also known as forecasting and identifying production capacities, is the process that determines what product needs to be produced at any particular time. Forecasting and identifying production capacity are two key elements to this process.
Scheduling is the process of assigning specific dates to tasks so they can be completed within the specified timeframe.
What are the requirements to start a logistics business?
It takes a lot of skills and knowledge to run a successful logistics business. You must have good communication skills to interact effectively with your clients and suppliers. It is important to be able to analyse data and draw conclusions. You must be able to work well under pressure and handle stressful situations. In order to innovate and create new ways to improve efficiency, creativity is essential. To motivate and guide your team towards reaching organizational goals, you must have strong leadership skills.
To meet tight deadlines, you must also be efficient and organized.
What is the job of a manufacturer manager?
A manufacturing manager must ensure that all manufacturing processes are efficient and effective. They should be aware of any issues within the company and respond accordingly.
They must also be able to communicate with sales and marketing departments.
They must also keep up-to-date with the latest trends in their field and be able use this information to improve productivity and efficiency.
How can manufacturing efficiency improved?
The first step is to identify the most important factors affecting production time. The next step is to identify the most important factors that affect production time. If you aren't sure where to begin, think about the factors that have the greatest impact on production time. Once you've identified them, try to find solutions for each of those factors.
How can overproduction in manufacturing be reduced?
The key to reducing overproduction lies in developing better ways to manage inventory. This would reduce time spent on activities such as purchasing, stocking, and maintaining excess stock. This will allow us to free up resources for more productive tasks.
You can do this by adopting a Kanban method. A Kanban board is a visual display used to track work in progress. A Kanban system allows work items to move through several states before reaching their final destination. Each state is assigned a different priority.
To illustrate, work can move from one stage or another when it is complete enough for it to be moved to a new stage. It is possible to keep a task in the beginning stages until it gets to the end.
This keeps work moving and ensures no work is lost. Managers can view the Kanban board to see how much work they have done. This information allows managers to adjust their workflow based off real-time data.
Another way to control inventory levels is to implement lean manufacturing. Lean manufacturing focuses on eliminating waste throughout the entire production chain. Anything that does not contribute to the product's value is considered waste. Some common types of waste include:
-
Overproduction
-
Inventory
-
Packaging that is not necessary
-
Excess materials
These ideas will help manufacturers increase efficiency and lower costs.
How does a production planner differ from a project manager?
The difference between a product planner and project manager is that a planer is typically the one who organizes and plans the entire project. A production planner, however, is mostly involved in the planning stages.
Is it possible to automate certain parts of manufacturing
Yes! Automation has been around since ancient times. The Egyptians invented the wheel thousands of years ago. Today, robots assist in the assembly of lines.
Actually, robotics can be used in manufacturing for many purposes. These include:
-
Automation line robots
-
Robot welding
-
Robot painting
-
Robotics inspection
-
Robots that produce products
There are many other examples of how manufacturing could benefit from automation. 3D printing, for example, allows us to create custom products without waiting for them to be made.
Statistics
- [54][55] These are the top 50 countries by the total value of manufacturing output in US dollars for its noted year according to World Bank.[56] (en.wikipedia.org)
- In the United States, for example, manufacturing makes up 15% of the economic output. (twi-global.com)
- Many factories witnessed a 30% increase in output due to the shift to electric motors. (en.wikipedia.org)
- According to a Statista study, U.S. businesses spent $1.63 trillion on logistics in 2019, moving goods from origin to end user through various supply chain network segments. (netsuite.com)
- According to the United Nations Industrial Development Organization (UNIDO), China is the top manufacturer worldwide by 2019 output, producing 28.7% of the total global manufacturing output, followed by the United States, Japan, Germany, and India.[52][53] (en.wikipedia.org)
External Links
How To
How to Use the Just In Time Method in Production
Just-in-time (JIT) is a method that is used to reduce costs and maximize efficiency in business processes. It's the process of obtaining the right amount and timing of resources when you need them. This means that only what you use is charged to your account. Frederick Taylor developed the concept while working as foreman in early 1900s. After observing how workers were paid overtime for late work, he realized that overtime was a common practice. He decided that workers would be more productive if they had enough time to complete their work before they started to work.
JIT teaches you to plan ahead and prepare everything so you don’t waste time. You should also look at the entire project from start to finish and make sure that you have sufficient resources available to deal with any problems that arise during the course of your project. You'll be prepared to handle any potential problems if you know in advance. This way, you won't end up paying extra money for things that weren't really necessary.
There are many JIT methods.
-
Demand-driven JIT: This is a JIT that allows you to regularly order the parts/materials necessary for your project. This will enable you to keep track of how much material is left after you use it. This will allow you to calculate how long it will take to make more.
-
Inventory-based: This is a type where you stock the materials required for your projects in advance. This allows you predict the amount you can expect to sell.
-
Project-driven: This method allows you to set aside enough funds for your project. Once you have an idea of how much material you will need, you can purchase the necessary materials.
-
Resource-based JIT : This is probably the most popular type of JIT. Here, you allocate certain resources based on demand. For instance, if you have a lot of orders coming in, you'll assign more people to handle them. If you don’t have many orders you will assign less people to the work.
-
Cost-based : This is similar in concept to resource-based. But here, you aren't concerned about how many people your company has but how much each individual costs.
-
Price-based pricing: This is similar in concept to cost-based but instead you look at how much each worker costs, it looks at the overall company's price.
-
Material-based is an alternative to cost-based. Instead of looking at the total cost in the company, this method focuses on the average amount of raw materials that you consume.
-
Time-based JIT: This is another variant of resource-based JIT. Instead of focusing on how much each employee costs, you focus on how long it takes to complete the project.
-
Quality-based: This is yet another variation of resource-based JIT. Instead of looking at the labor costs and time it takes to make a product, think about its quality.
-
Value-based JIT: One of the most recent forms of JIT. In this scenario, you're not concerned about how products perform or whether customers expect them to meet their expectations. Instead, you're focused on how much value you add to the market.
-
Stock-based: This stock-based method focuses on the actual quantity of products being made at any given time. It's used when you want to maximize production while minimizing inventory.
-
Just-in-time planning (JIT): This is a combination JIT and supply-chain management. This refers to the scheduling of the delivery of components as soon after they are ordered. It's important as it reduces leadtimes and increases throughput.