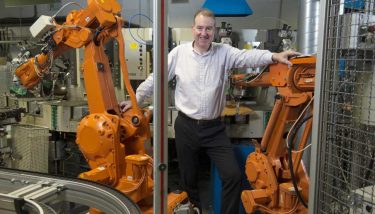
Kanban is a method of reducing costs and improving efficiency in manufacturing. These principles help to reduce downtime, inefficiencies, and improve customer service. This allows for continuous improvement.
Kanban is a system used to organize and monitor the flow of work. It assists manufacturers and teams in better tracking and monitoring their work processes, as well as improving productivity. Kanban involves the creation of a visual representation of the steps involved in a particular process and the identification and minimization or inefficiencies.
The kanban method can be implemented manually, or with the use of a software application. Software can be used to help teams determine what should be done and who should. Employees can also adapt to feedback and make improvements in their work processes using the kanban method. It's also useful for brainstorming.
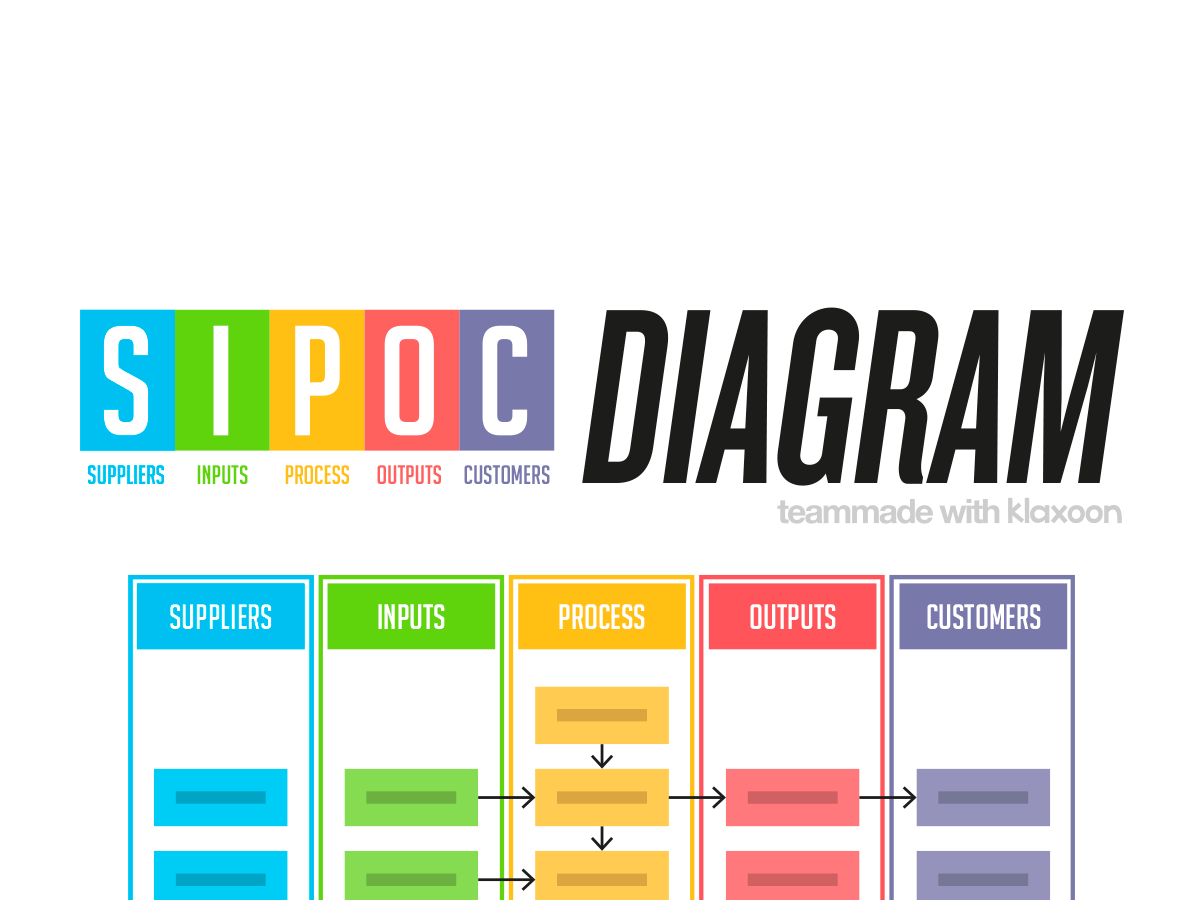
Kanban boards, which are boards that show a process, are one of the most well-known Kanban examples in manufacturing. The board lists the steps in the process, in priority order. First, contact a supplier. The second task is ordering the necessary supplies to complete the job. The third task is to start manufacturing. The fourth task will be to test and deliver the final product.
Kanbans allow teams to visualize and make small improvements to their process. You can use the kanban board to improve communication between teams and identify and fix any bottlenecks.
The kanban method is also designed to eliminate waste, and to promote information sharing. This is especially useful when the company is trying to implement lean principles. It is possible to accumulate waste over the course of a manufacturing operation in many ways. The manufacturer can add value to every stage of the manufacturing process by removing waste. The kanban system can also be used to manage inventory. It can be used to manage inventory overstocking.
Kanban is a great way of visualizing the process and to cut costs. Kanban can help improve efficiency and reduce the number of items required to complete a job. It also helps to improve communication, and to minimize downtime. The kanban system is a good example of how technology can help with a difficult task.
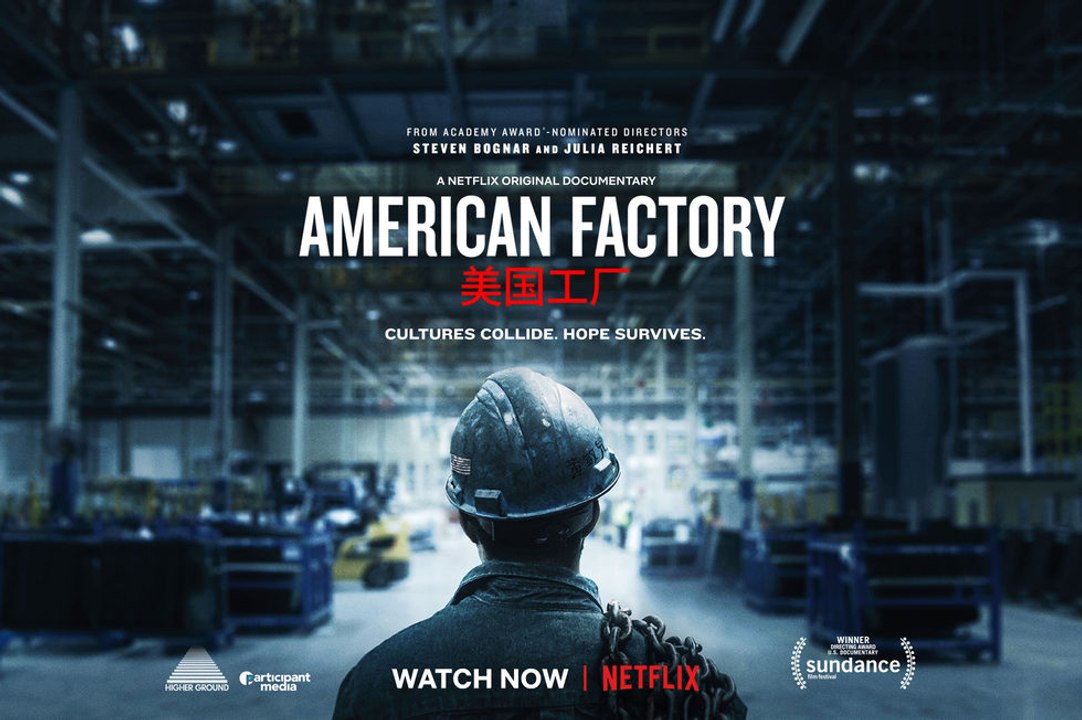
Kanban is also useful for brainstorming and productivity. Kanban can be used to link companies to suppliers and to improve communication. It can also be used to improve quality and streamline production.
One of the most well-known Kanban methods in manufacturing is the board. Tasks are organized according to priority and time needed to complete them. A board can also display the steps involved with a process (such as design and manufacturing, testing, etc.
FAQ
What are the goods of logistics?
Logistics involves the transportation of goods from point A and point B.
They include all aspects associated with transport including packaging, loading transporting, unloading storage, warehousing inventory management customer service, distribution returns and recycling.
Logisticians ensure the product reaches its destination in the most efficient manner. Logisticians assist companies in managing their supply chains by providing information such as demand forecasts, stock levels and production schedules.
They also keep track of shipments in transit, monitor quality standards, perform inventories and order replenishment, coordinate with suppliers and vendors, and provide support services for sales and marketing.
What is the distinction between Production Planning or Scheduling?
Production Planning (PP) refers to the process of determining how much production is needed at any given moment. This is done through forecasting demand and identifying production capacities.
Scheduling is the process of assigning specific dates to tasks so they can be completed within the specified timeframe.
What are the jobs in logistics?
There are many types of jobs in logistics. Some examples are:
-
Warehouse workers – They load and unload pallets and trucks.
-
Transportation drivers: They drive trucks and trailers and deliver goods and make pick-ups.
-
Freight handlers: They sort and package freight in warehouses.
-
Inventory managers - They oversee the inventory of goods in warehouses.
-
Sales representatives - They sell products to customers.
-
Logistics coordinators - They plan and organize logistics operations.
-
Purchasing agents are those who purchase goods and services for the company.
-
Customer service representatives - Answer calls and email from customers.
-
Shipping clerks – They process shipping orders, and issue bills.
-
Order fillers: They fill orders based off what has been ordered and shipped.
-
Quality control inspectors – They inspect incoming and outgoing products to ensure that there are no defects.
-
Other - Logistics has many other job opportunities, including transportation supervisors, logistics specialists, and cargo specialists.
Statistics
- (2:04) MTO is a production technique wherein products are customized according to customer specifications, and production only starts after an order is received. (oracle.com)
- [54][55] These are the top 50 countries by the total value of manufacturing output in US dollars for its noted year according to World Bank.[56] (en.wikipedia.org)
- In the United States, for example, manufacturing makes up 15% of the economic output. (twi-global.com)
- According to the United Nations Industrial Development Organization (UNIDO), China is the top manufacturer worldwide by 2019 output, producing 28.7% of the total global manufacturing output, followed by the United States, Japan, Germany, and India.[52][53] (en.wikipedia.org)
- It's estimated that 10.8% of the U.S. GDP in 2020 was contributed to manufacturing. (investopedia.com)
External Links
How To
Six Sigma in Manufacturing
Six Sigma can be described as "the use of statistical process control (SPC), techniques to achieve continuous improvement." Motorola's Quality Improvement Department developed it at their Tokyo plant in Japan in 1986. Six Sigma's core idea is to improve the quality of processes by standardizing and eliminating defects. Many companies have adopted this method in recent years. They believe there is no such thing a perfect product or service. Six Sigma's primary goal is to reduce variation from the average value of production. This means that if you take a sample of your product, then measure its performance against the average, you can find out what percentage of the time the process deviates from the norm. If it is too large, it means that there are problems.
Understanding the dynamics of variability within your business is the first step in Six Sigma. Once you understand that, it is time to identify the sources of variation. This will allow you to decide if these variations are random and systematic. Random variations are caused when people make mistakes. While systematic variations are caused outside of the process, they can occur. These are, for instance, random variations that occur when widgets are made and some fall off the production line. It would be considered a systematic problem if every widget that you build falls apart at the same location each time.
Once you identify the problem areas, it is time to create solutions. You might need to change the way you work or completely redesign the process. Once you have implemented the changes, it is important to test them again to ensure they work. If they didn't work, then you'll need to go back to the drawing board and come up with another plan.