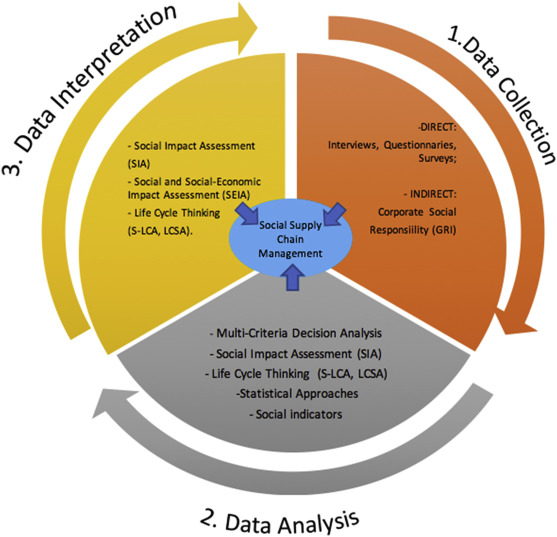
Chemical manufacturing is a major US industry. It transforms organic or inorganic materials into useful products. It provides materials and goods for industries that include plastics, explosives, and consumer goods. There are also many challenges facing the chemical industry. A large number of workers are at risk of health and safety issues.
The two main areas of chemical manufacturing are commodity chemicals and specialty chemicals. These two main segments share common infrastructure, utilities, as well as production processes. The products however, are very different. Specialty chemicals can be used for specific purposes. Specialty chemicals manufacturers make some of the most expensive chemicals. Many of these are protected by patents.
Some chemicals are manufactured in one location. However, the vast majority of petrochemicals (and commodity chemicals) are produced in large facilities. Rotterdam (the Netherlands) and Texas are examples of large scale chemical plants. Large-scale chemical plants often share utilities, infrastructures, and create economies of scale.
The United States is second in the world for chemical manufacturing, after China. According to Statista, the chemical industry is worth more than $4 trillion annually. About half of industry revenue is generated by the top 50 US companies.
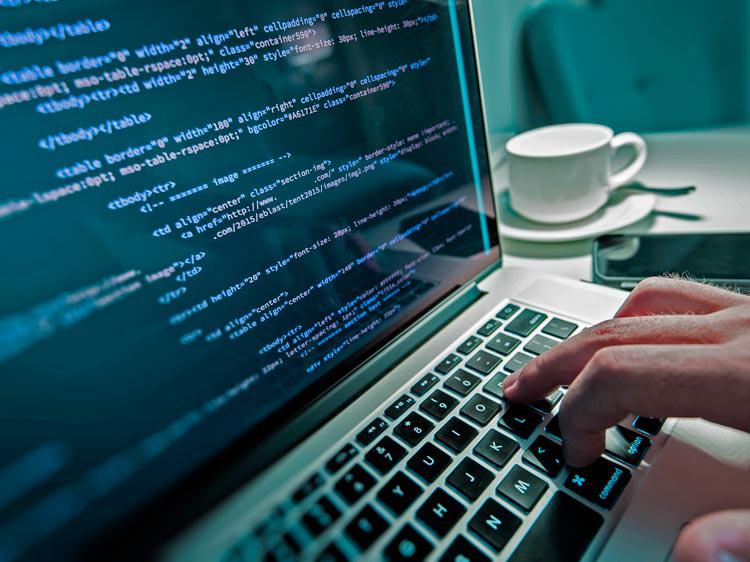
Around 20 million people work in the chemical manufacturing sector worldwide. These workers are mostly employed in large-scale manufacturing plants. However, there are a few contract and part-time workers. The industry's employment has suffered due to increased competition and technological progress.
The U.S. overall economy is the main driver of chemical demand. The chemical industry is also highly regulated. The regulations and standards that govern the manufacturing process are set by government bodies. Companies must ensure that they are operating in an environmentally responsible manner. Additionally, some chemical manufacturing raw materials are dangerous to extract.
The procurement process is challenging for the industry. Additionally, raw material costs are very high. Some companies move their operations to lower-cost locations in order to keep costs down. Lastly, some companies are merging or moving their production activities to developing countries. This will lead eventually to the elimination or merging of companies.
In 2008, basic chemical manufacturing accounted for 80 percent. This group includes producers of pesticides, dyes and other materials. Pfizer and Dow are among the top manufacturing companies in this sector. DuPont is also a major player, as well as Formosa Plastics & Sinopec Group.
Large-scale production facilities can usually be kept clean. Workers are required to wear safety goggles and work in a temperature-controlled environment. Some workers, however, are replaced with advanced machines and computerized controls. Many of these workers work nights.
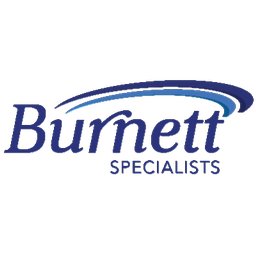
Some chemical manufacturing plants may have to be modified in order to accept new production methods. New processes can improve accuracy, and reduce labor costs. Also, the use of nanotechnology will make chemical manufacturing more efficient. Nanotechnology will also help companies conserve energy and reduce waste.
Some of the other factors affecting the employment of the chemical manufacturing industry are increased foreign competition, technological advancements, and environmental health and safety concerns. In general, the industry's employment will decrease by 13 percent over four years.
FAQ
How can manufacturing reduce production bottlenecks?
Avoiding production bottlenecks is as simple as keeping all processes running smoothly, from the time an order is received until the product ships.
This includes planning for both capacity requirements and quality control measures.
Continuous improvement techniques like Six Sigma are the best way to achieve this.
Six Sigma management is a system that improves quality and reduces waste within your organization.
It's all about eliminating variation and creating consistency in work.
What skills are required to be a production manager?
Production planners must be flexible, organized, and able handle multiple tasks. You must also be able to communicate effectively with clients and colleagues.
Why automate your warehouse
Modern warehouses have become more dependent on automation. With the rise of ecommerce, there is a greater demand for faster delivery times as well as more efficient processes.
Warehouses must adapt quickly to meet changing customer needs. Technology is essential for warehouses to be able to adapt quickly to changing needs. Automation of warehouses offers many benefits. These are just a few reasons to invest in automation.
-
Increases throughput/productivity
-
Reduces errors
-
Accuracy is improved
-
Safety enhancements
-
Eliminates bottlenecks
-
This allows companies to scale easily
-
Workers are more productive
-
Gives you visibility into all that is happening in your warehouse
-
Enhances customer experience
-
Improves employee satisfaction
-
This reduces downtime while increasing uptime
-
Ensures quality products are delivered on time
-
Human error can be eliminated
-
Helps ensure compliance with regulations
Statistics
- (2:04) MTO is a production technique wherein products are customized according to customer specifications, and production only starts after an order is received. (oracle.com)
- According to the United Nations Industrial Development Organization (UNIDO), China is the top manufacturer worldwide by 2019 output, producing 28.7% of the total global manufacturing output, followed by the United States, Japan, Germany, and India.[52][53] (en.wikipedia.org)
- According to a Statista study, U.S. businesses spent $1.63 trillion on logistics in 2019, moving goods from origin to end user through various supply chain network segments. (netsuite.com)
- In 2021, an estimated 12.1 million Americans work in the manufacturing sector.6 (investopedia.com)
- Many factories witnessed a 30% increase in output due to the shift to electric motors. (en.wikipedia.org)
External Links
How To
How to Use the 5S to Increase Productivity In Manufacturing
5S stands to stand for "Sort", “Set In Order", “Standardize", and "Store". Toyota Motor Corporation developed the 5S method in 1954. It improves the work environment and helps companies to achieve greater efficiency.
This method has the basic goal of standardizing production processes to make them repeatable. This means that every day tasks such cleaning, sorting/storing, packing, and labeling can be performed. These actions allow workers to perform their job more efficiently, knowing what to expect.
Implementing 5S requires five steps. These are Sort, Set In Order, Standardize. Separate. And Store. Each step has a different action and leads to higher efficiency. For example, when you sort things, you make them easy to find later. You arrange items by placing them in an order. Next, organize your inventory into categories and store them in containers that are easily accessible. Finally, when you label your containers, you ensure everything is labeled correctly.
Employees must be able to critically examine their work practices. Employees must understand why they do certain tasks and decide if there's another way to accomplish them without relying on the old ways of doing things. To implement the 5S system, employees must acquire new skills and techniques.
The 5S method increases efficiency and morale among employees. They are more motivated to achieve higher efficiency levels as they start to see improvement.