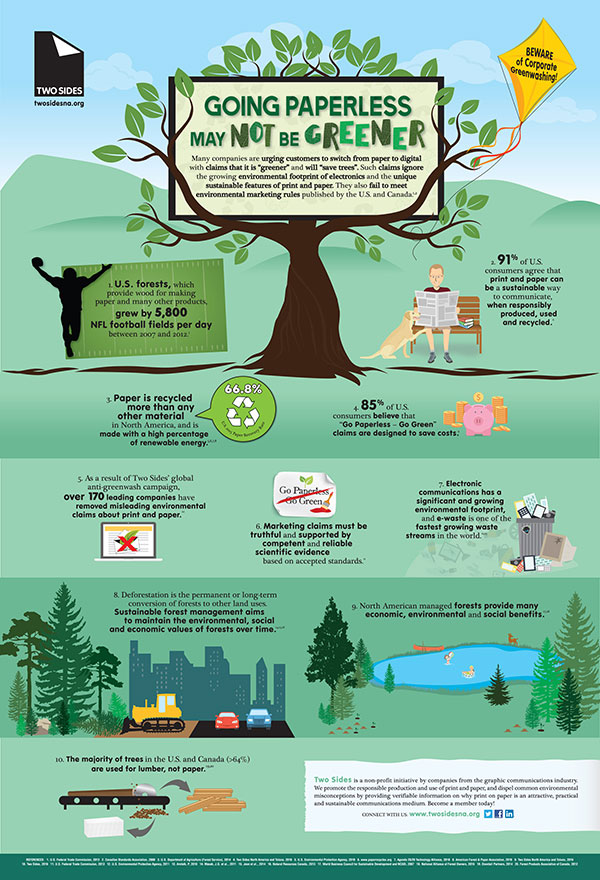
An industrial engineer is responsible for creating and implementing processes that optimize resource utilization and eliminate waste. These engineers work in various industries to design processes that benefit their companies in a variety of ways. They look at production schedules, design specifications, as well as workflows to help create more efficient processes. Industrial engineers also analyze the production process efficiency to increase profitability. They also aid in improving the quality and quantity of products.
Industrial engineer job requirements
A key role for an industrial engineer is to use innovative design systems and streamline production processes in order to provide streamlined operations for natural and organic food industry. This person develops meticulous solutions to meet the needs of internal customers and leads dynamic projects to improve the manufacturing process. A person must be competent and capable of performing all required duties in order to be eligible for this job. Industrial engineers must be familiar with AutoCAD and Pro-E, and they must be knowledgeable of advanced product quality planning and the production part approval process.
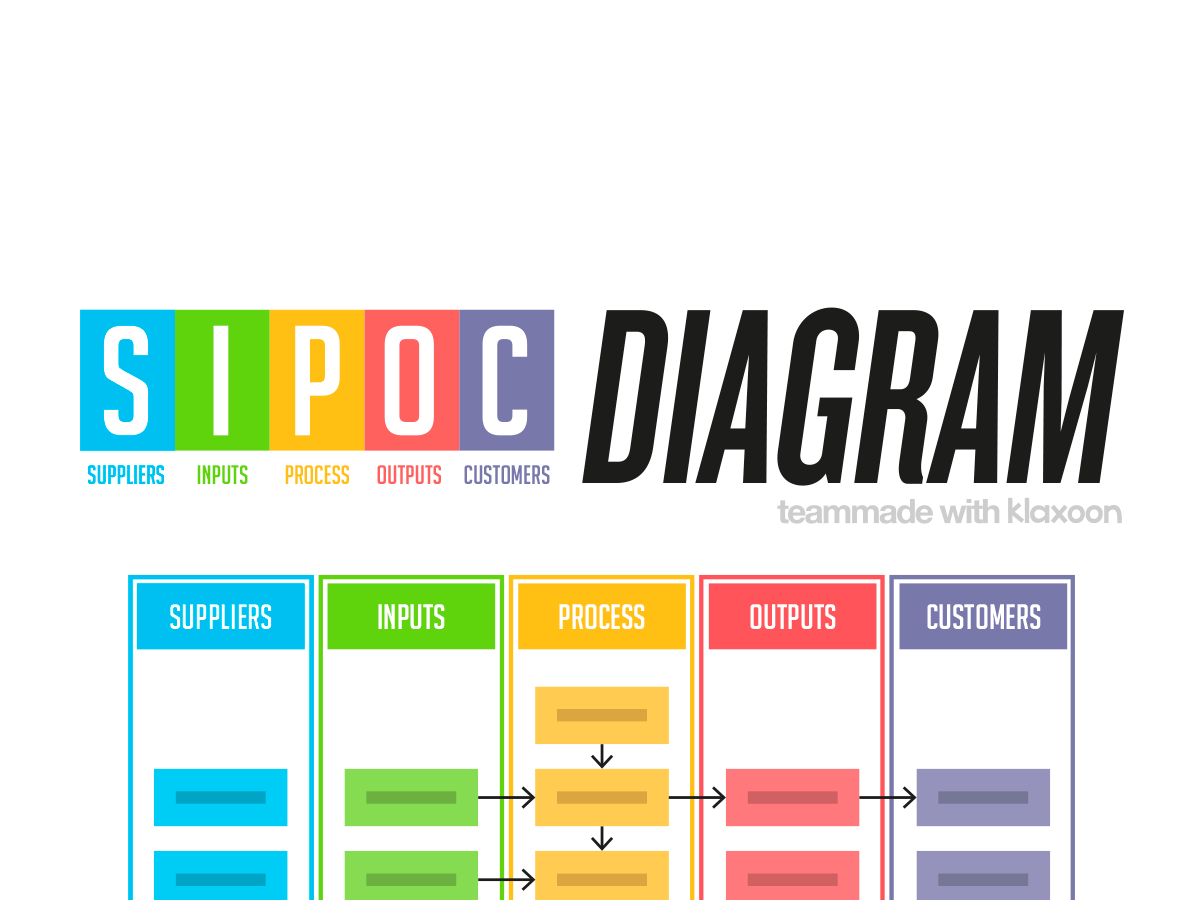
Industrial Engineers focus on the development and testing of integrated systems that maximize efficiency. The job involves not only designing and testing integrated systems, but also studying human factors in order to optimize product quality. Other responsibilities include logistics, cost analysis, and guest coordination. In addition, this person must be proficient in advanced technical skills such as Microsoft Office. Experience in manufacturing, logistics, and systems design is also needed. In Orlando, you must have the technical skills necessary to perform your job well.
Industrial engineer salary
The salaries in Orlando are a good place to start if you're thinking about a career as an Industrial & Manufacturing Engineer. Orlando is considered one of the top places to live. The average salary here is $80,325 annually. This is 6% more than the national median salary and 9% less that the New York, NY median salary. Orlando has a salary range of $64,260- $96,390. The middle 67% earn $85,000 per annum, while the top 10 percent earn $102,000.
Salaries for Industrial Engineers in Orlando can range from $89,700 USD to $114,300 USD. The salaries for industrial engineers are like any other career. The following salary figures are for Industrial Engineers with five to ten years' experience. Those with more experience, however, can expect to make almost twice as much as those with less experience. But, pay scales can vary between industrial engineers.
Industrial engineer responsibilities
As a process designer and manager, you will determine the best ways to improve process performance. It is your responsibility to develop and implement flexible, efficient and effective processes that meet customer requirements and goals. An Industrial Engineer can perform a range of tasks. These include process improvement, capacity planning, cost analysis, reporting, data analysis, capital project management, and discrete event simulation. The Industrial Engineer will also need to assist with cross-functional improvement efforts by carrying out observations and time studies.
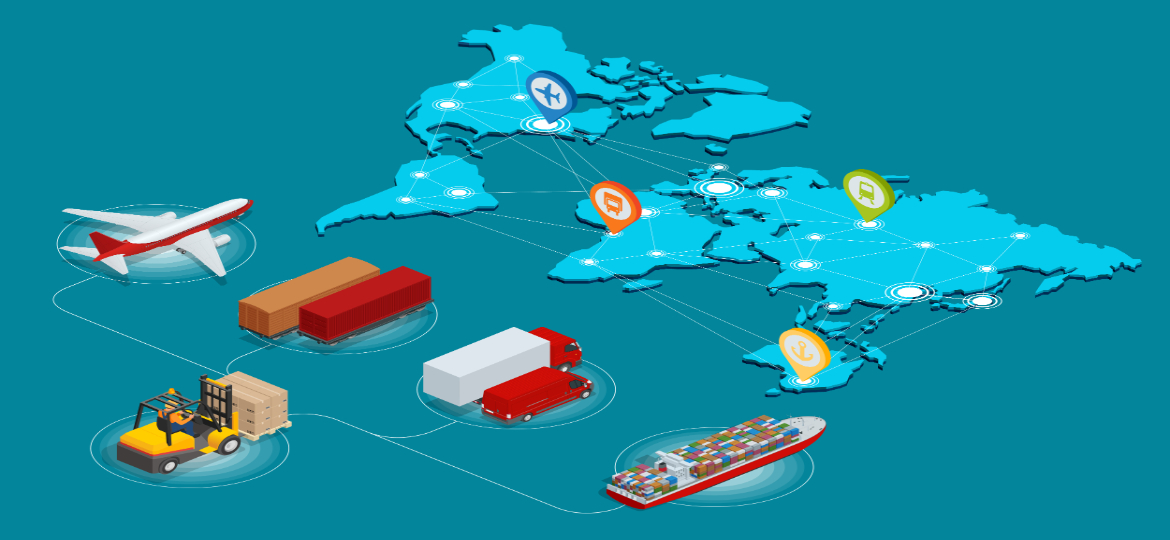
To be able to do this job, you must possess strong communication skills, engineering experience, and a solid grasp of statistical analysis. Industrial engineers work closely alongside management to develop standards and lead industrial engineering projects that are moderately complex. They will analyse data and produce statistical reports to improve quality, process flow, and standard times. They will coordinate important studies and produce key reports on metrics, process documentation, and production reports.
FAQ
What is the best way to learn about manufacturing?
Experience is the best way for you to learn about manufacturing. You can read books, or watch instructional videos if you don't have the opportunity to do so.
How can manufacturing avoid production bottlenecks
Production bottlenecks can be avoided by ensuring that processes are running smoothly during the entire production process, starting with the receipt of an order and ending when the product ships.
This includes planning to meet capacity requirements and quality control.
The best way to do this is to use continuous improvement techniques such as Six Sigma.
Six Sigma Management System is a method to increase quality and reduce waste throughout your organization.
It's all about eliminating variation and creating consistency in work.
What are the jobs in logistics?
There are many kinds of jobs available within logistics. Here are some examples:
-
Warehouse workers - They load and unload trucks and pallets.
-
Transportation drivers – These drivers drive trucks and wagons to transport goods and pick up the goods.
-
Freight handlers, - They sort out and pack freight in warehouses.
-
Inventory managers - They oversee the inventory of goods in warehouses.
-
Sales reps - They sell products and services to customers.
-
Logistics coordinators – They plan and coordinate logistics operations.
-
Purchasing agents are those who purchase goods and services for the company.
-
Customer service representatives – They answer emails and phone calls from customers.
-
Shipping clerks – They process shipping orders, and issue bills.
-
Order fillers - These people fill orders based on what has been ordered.
-
Quality control inspectors (QCI) - They inspect all incoming and departing products for potential defects.
-
Others – There are many other types available in logistics. They include transport supervisors, cargo specialists and others.
How can manufacturing overproduction be reduced?
Improved inventory management is the key to reducing overproduction. This would reduce time spent on activities such as purchasing, stocking, and maintaining excess stock. By doing this, we could free up resources for other productive tasks.
A Kanban system is one way to achieve this. A Kanbanboard is a visual tool that allows you to keep track of the work being done. A Kanban system allows work items to move through several states before reaching their final destination. Each state represents a different priority level.
If work is moving from one stage to the other, then the current task can be completed and moved on to the next. But if a task remains in the beginning stages it will stay that way until it reaches its end.
This keeps work moving and ensures no work is lost. Managers can view the Kanban board to see how much work they have done. This information allows managers to adjust their workflow based off real-time data.
Lean manufacturing is another option to control inventory levels. Lean manufacturing focuses on eliminating waste throughout the entire production chain. Any product that isn't adding value can be considered waste. Here are some examples of common types.
-
Overproduction
-
Inventory
-
Packaging that is not necessary
-
Materials in excess
Manufacturers can reduce their costs and improve their efficiency by using these ideas.
What does "warehouse" mean?
A warehouse is an area where goods are stored before being sold. It can be indoors or out. It may also be an indoor space or an outdoor area.
What are the logistics products?
Logistics are the activities involved in moving goods from point A to point B.
They include all aspects associated with transport including packaging, loading transporting, unloading storage, warehousing inventory management customer service, distribution returns and recycling.
Logisticians ensure that the product is delivered to the correct place, at the right time, and under safe conditions. They provide information on demand forecasts as well stock levels, production schedules and availability of raw material.
They coordinate with vendors and suppliers, keep track of shipments, monitor quality standards and perform inventory and order replenishment.
Statistics
- (2:04) MTO is a production technique wherein products are customized according to customer specifications, and production only starts after an order is received. (oracle.com)
- [54][55] These are the top 50 countries by the total value of manufacturing output in US dollars for its noted year according to World Bank.[56] (en.wikipedia.org)
- According to a Statista study, U.S. businesses spent $1.63 trillion on logistics in 2019, moving goods from origin to end user through various supply chain network segments. (netsuite.com)
- It's estimated that 10.8% of the U.S. GDP in 2020 was contributed to manufacturing. (investopedia.com)
- You can multiply the result by 100 to get the total percent of monthly overhead. (investopedia.com)
External Links
How To
How to Use Lean Manufacturing in the Production of Goods
Lean manufacturing is a management system that aims at increasing efficiency and reducing waste. It was developed in Japan between 1970 and 1980 by Taiichi Ohno. TPS founder Kanji Tyoda gave him the Toyota Production System, or TPS award. Michael L. Watkins published the "The Machine That Changed the World", the first book about lean manufacturing. It was published in 1990.
Lean manufacturing, often described as a set and practice of principles, is aimed at improving the quality, speed, cost, and efficiency of products, services, and other activities. It emphasizes eliminating waste and defects throughout the value stream. Lean manufacturing is also known as just in time (JIT), zero defect total productive maintenance(TPM), and five-star (S). Lean manufacturing seeks to eliminate non-value added activities, such as inspection, work, waiting, and rework.
Lean manufacturing can help companies improve their product quality and reduce costs. Additionally, it helps them achieve their goals more quickly and reduces employee turnover. Lean Manufacturing is one of the most efficient ways to manage the entire value chains, including suppliers and customers as well distributors and retailers. Lean manufacturing is widely used in many industries. Toyota's philosophy is the foundation of its success in automotives, electronics and appliances, healthcare, chemical engineers, aerospace, paper and food, among other industries.
Five basic principles of Lean Manufacturing are included in lean manufacturing
-
Define Value - Identify the value your business adds to society and what makes you different from competitors.
-
Reduce waste - Stop any activity that isn't adding value to the supply chains.
-
Create Flow – Ensure that work flows smoothly throughout the process.
-
Standardize and simplify – Make processes as repeatable and consistent as possible.
-
Build relationships - Develop and maintain personal relationships with both your internal and external stakeholders.
Lean manufacturing is not a new concept, but it has been gaining popularity over the last few years due to a renewed interest in the economy following the global financial crisis of 2008. Many businesses are now using lean manufacturing to improve their competitiveness. Some economists even believe that lean manufacturing can be a key factor in economic recovery.
Lean manufacturing is becoming a popular practice in automotive. It has many advantages. These benefits include increased customer satisfaction, reduced inventory levels and lower operating costs.
You can apply Lean Manufacturing to virtually any aspect of your organization. Because it makes sure that all value chains are efficient and effectively managed, Lean Manufacturing is particularly helpful for organizations.
There are three types principally of lean manufacturing:
-
Just-in-Time Manufacturing (JIT): This type of lean manufacturing is commonly referred to as "pull systems." JIT stands for a system where components are assembled on the spot rather than being made in advance. This strategy aims to decrease lead times, increase availability of parts and reduce inventory.
-
Zero Defects Manufacturing (ZDM),: ZDM is a system that ensures no defective units are left the manufacturing facility. If a part is required to be repaired on the assembly line, it should not be scrapped. This also applies to finished products that need minor repairs before being shipped.
-
Continuous Improvement (CI), also known as Continuous Improvement, aims at improving the efficiency of operations through continuous identification and improvement to minimize or eliminate waste. Continuous improvement involves continuous improvement of processes and people as well as tools.