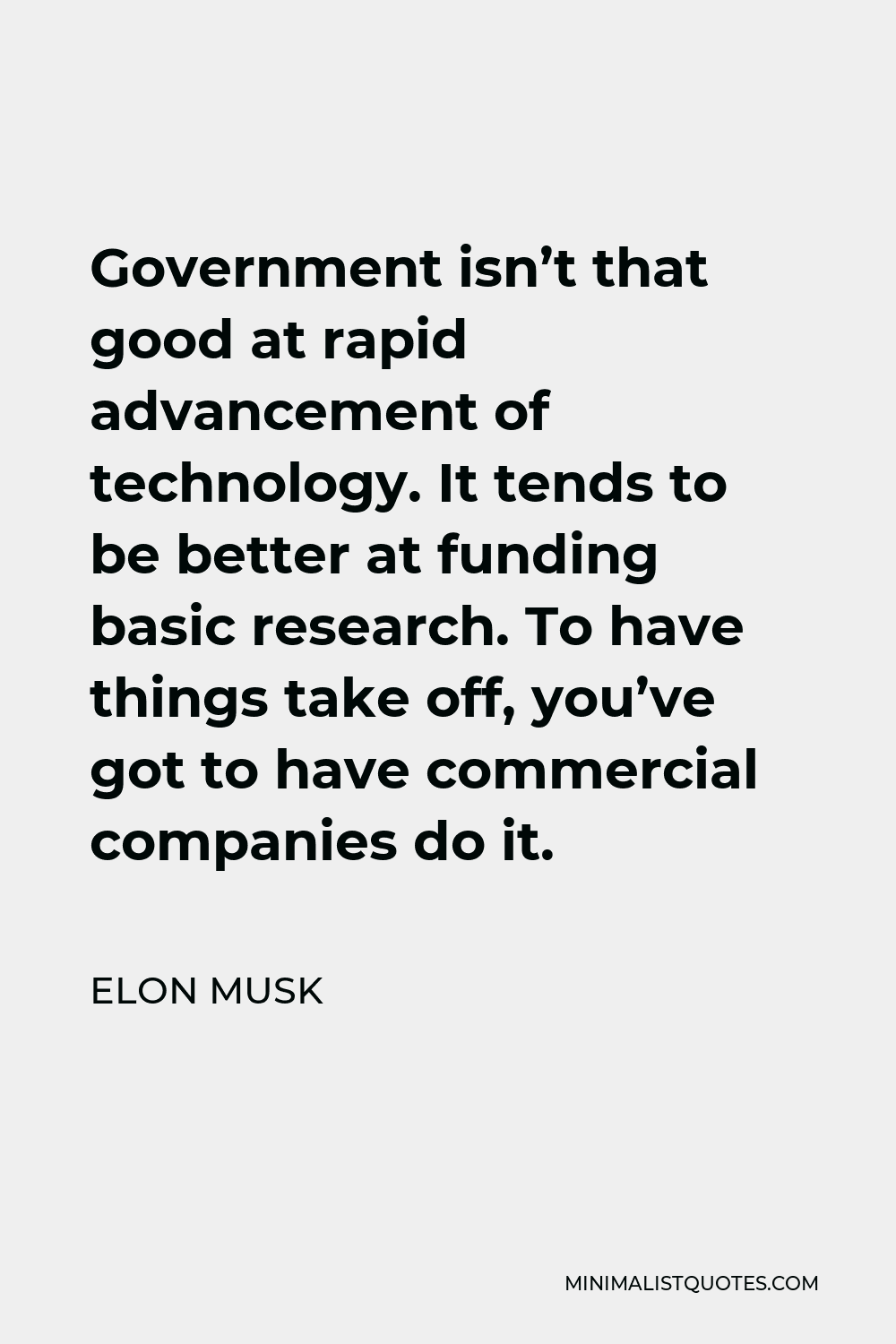
The US service industry has no problem with technology. The slow economy and poor quality of life have not been kind to the US. This is not to mention competition from emerging superpowers like Taiwan or China. In the last few months, there has been an increase in crime and a decrease in employment. The best way to stop this is to keep our brightest and most talented people on home soil. The best way to accomplish this is to provide them with a conducive environment. We will be successful if we have a high-quality education and training program, as well as a healthy dose consumer parity.
FAQ
What does it take to run a logistics business?
To run a successful logistics company, you need a lot knowledge and skills. Good communication skills are essential to effectively communicate with your suppliers and clients. You must be able analyze data and draw out conclusions. You will need to be able handle pressure well and work in stressful situations. You must be creative and innovative to develop new ideas to improve efficiency. To motivate and guide your team towards reaching organizational goals, you must have strong leadership skills.
To meet tight deadlines, you must also be efficient and organized.
Why automate your warehouse?
Modern warehousing has seen automation take center stage. E-commerce has increased the demand for quicker delivery times and more efficient processes.
Warehouses should be able adapt quickly to new needs. Technology investment is necessary to enable warehouses to respond quickly to changing demands. Automation of warehouses offers many benefits. Here are some of the reasons automation is worth your investment:
-
Increases throughput/productivity
-
Reduces errors
-
Improves accuracy
-
Safety increases
-
Eliminates bottlenecks
-
Allows companies to scale more easily
-
Workers are more productive
-
This gives you visibility into what happens in the warehouse
-
Enhances customer experience
-
Improves employee satisfaction
-
Reducing downtime and increasing uptime
-
Ensures quality products are delivered on time
-
Human error can be eliminated
-
Assure compliance with regulations
What is production management?
Production Planning refers to the development of a plan for every aspect of production. This document will ensure everything is in order and ready to go when you need it. This document should also include information on how to get the best result on set. This includes information on shooting times, locations, cast lists and crew details.
It is important to first outline the type of film you would like to make. You may have already decided where you would like to shoot, or maybe there are specific locations or sets that you want to use. Once you have determined your scenes and locations, it is time to start figuring out the elements that you will need for each scene. For example, you might decide that you need a car but don't know exactly what model you want. If this is the case, you might start searching online for car models and then narrow your options by selecting from different makes.
After you have chosen the right car, you will be able to begin thinking about accessories. Do you need people sitting in the front seats? Or perhaps you need someone walking around the back of the car? Maybe you'd like to change the interior from black to a white color. These questions can help you decide the right look for your car. Another thing you can do is think about what type of shots are desired. You will be filming close-ups and wide angles. Maybe you want to show your engine or the steering wheel. All of these things will help you identify the exact style of car you want to film.
Once you have determined all of the above, you can move on to creating a schedule. A schedule will tell you when you need to start shooting and when you need to finish. A schedule for each day will detail when you should arrive at the location and when you need leave. Everyone knows exactly what they should do and when. If you need to hire extra staff, you can make sure you book them in advance. You should not hire anyone who doesn't show up because of your inaction.
Your schedule will also have to be adjusted to reflect the number of days required to film. Some projects may only take a couple of days, while others could last for weeks. You should consider whether you will need more than one shot per week when creating your schedule. Multiple shots at the same location can increase costs and make it more difficult to complete. It's better to be safe than sorry and shoot less takes if you're not certain whether you need more takes.
Budgeting is another important aspect of production planning. Setting a realistic budget is essential as it will allow you to work within your means. If you have to reduce your budget due to unexpected circumstances, you can always lower it later. However, you shouldn't overestimate the amount of money you will spend. Underestimating the cost will result in less money after you have paid for other items.
Production planning can be a complex process. However, once you know how everything works together it will become easier to plan future projects.
Statistics
- Job #1 is delivering the ordered product according to specifications: color, size, brand, and quantity. (netsuite.com)
- According to a Statista study, U.S. businesses spent $1.63 trillion on logistics in 2019, moving goods from origin to end user through various supply chain network segments. (netsuite.com)
- You can multiply the result by 100 to get the total percent of monthly overhead. (investopedia.com)
- In 2021, an estimated 12.1 million Americans work in the manufacturing sector.6 (investopedia.com)
- Many factories witnessed a 30% increase in output due to the shift to electric motors. (en.wikipedia.org)
External Links
How To
Six Sigma in Manufacturing:
Six Sigma is defined by "the application SPC (statistical process control) techniques to achieve continuous improvements." Motorola's Quality Improvement Department in Tokyo, Japan developed Six Sigma in 1986. The basic idea behind Six Sigma is to improve quality by improving processes through standardization and eliminating defects. Since there are no perfect products, or services, this approach has been adopted by many companies over the years. The main goal of Six Sigma is to reduce variation from the mean value of production. This means that you can take a sample from your product and then compare its performance to the average to find out how often the process differs from the norm. If this deviation is too big, you know something needs fixing.
Understanding how your business' variability is a key step towards Six Sigma implementation is the first. Once you've understood that, you'll want to identify sources of variation. It is important to identify whether the variations are random or systemic. Random variations occur when people do mistakes. Symmetrical variations are caused due to factors beyond the process. You could consider random variations if some widgets fall off the assembly lines. However, if you notice that every time you assemble a widget, it always falls apart at exactly the same place, then that would be a systematic problem.
Once you've identified where the problems lie, you'll want to design solutions to eliminate those problems. This could mean changing your approach or redesigning the entire process. You should then test the changes again after they have been implemented. If they don't work you need to rework them and come up a better plan.