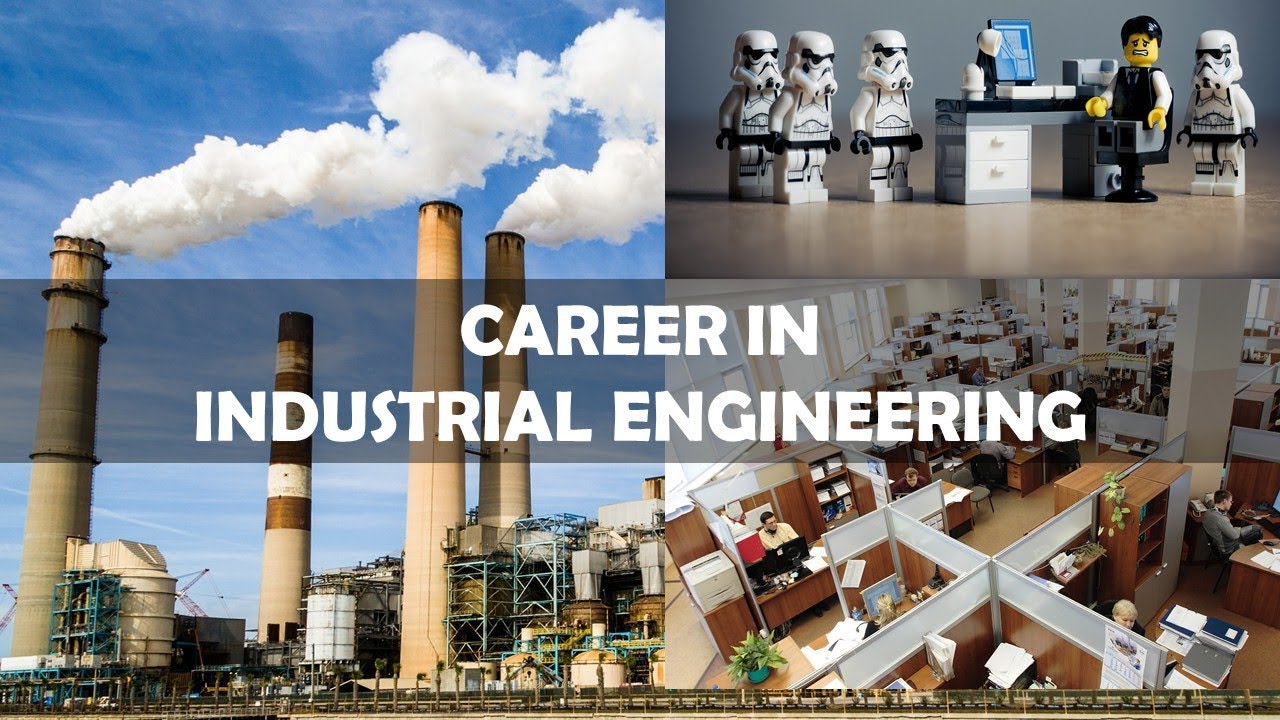
Art Byrne, Wiremold's CEO, introduced many innovative solutions that helped the company reach its goals of reducing costs and increasing productivity. Byrne's lean manufacturing case study demonstrated his keen understanding of how to involve the whole team. Byrne encouraged all members of his team to practice the lean manufacturing techniques and invited them to join the kaizen project.
He created a lean manufacturing program that tracked parts flow through the production process. He also introduced a number of tools that reduce waste and increase production. He also introduced a laser-cutting machine that made it possible to produce small batches and save on tooling. His success was due in large part to his lean strategy which consisted of just a few easy steps.
He also used a JIT manufacturing process. The company could deliver vehicles in a very short time frame thanks to this manufacturing method. It also allowed for harmony through the manufacturing process, which was the key to reducing waste.
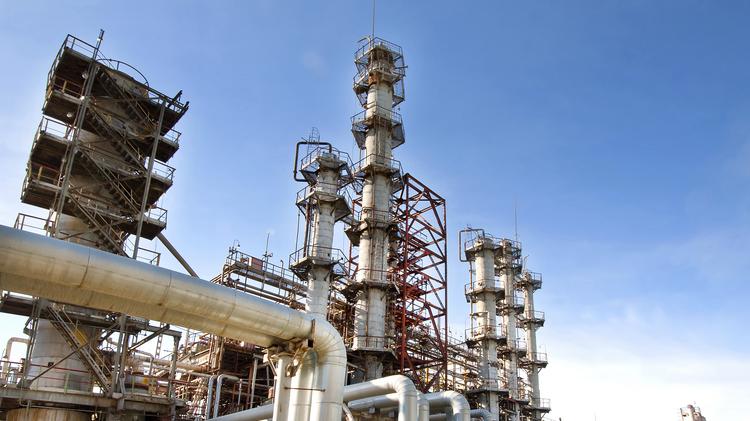
During the recession, he embraced problem-solving ideas and introduced a tool maintenance strategy that helped the company save $2 million. He also introduced an early retirement plan for workers who are unionized. These moves enabled him to transform Wiremold, which was a chaotic and inefficient business, into a Lean company.
He developed a system to monitor raw materials flow throughout the manufacturing process. He also implemented a new ERP system. He made sure his employees understood the importance and value of respecting their colleagues. His lean strategies were simple but effective and allowed him to make sure that everyone understood the concept of Kaizen. His management style promoted respect for people and an active approach.
His knowledge of the Kaizen process was his greatest asset. Danaher Corporation was where he worked, and he understands that a good Kaizen involves the 3 P's: People, Process, and Product. He also implemented modest layoffs of salaried employees. His kaizen strategy was a way for him to ensure that his team did the right thing.
He also introduced the concept of value stream mapping. This diagram shows the effect of manufacturing resources on overall efficiency. He also introduced the Kaizen event sheet, which can be used as a tool to track key improvement actions. A chart showing overall achievements can display the results.
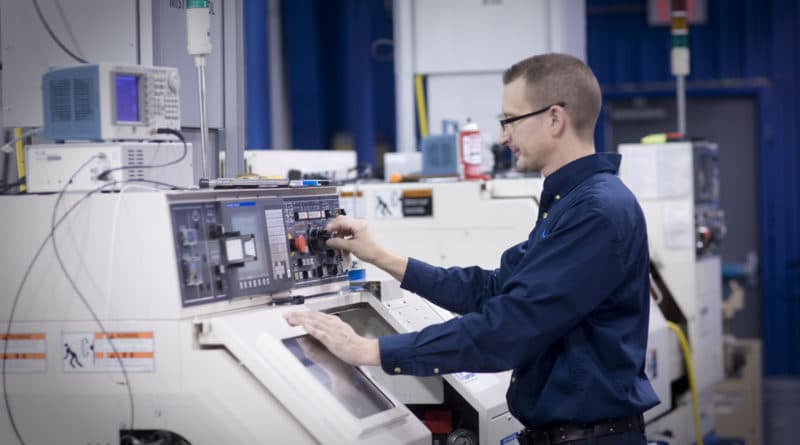
He also created a system for reducing lead times, which is crucial for the manufacturing industry. The fine blanking machine produced 600 to 800-blades per hour. It eliminated the need of a lot manual labor. Kanban cards were another tool that could be used to cut down on lead time.
Wiremold was a pioneer in the manufacture of conduit casing. After a major overhaul by Art Byrne, the company saw its sales rise from 100 million to over 450 million dollars in ten short years. French competitor Legrand purchased the business in 2001. However, Wiremold's journey was not always successful. Its biggest problem, however, was queue processing. This caused stations to have too many or too few jobs.
FAQ
What are the 4 types of manufacturing?
Manufacturing refers the process of turning raw materials into useful products with machines and processes. Manufacturing involves many activities, including designing, building, testing and packaging, shipping, selling, service, and so on.
What makes a production planner different from a project manger?
The primary difference between a producer planner and a manager of a project is that the manager usually plans and organizes the whole project, while a production planner is only involved in the planning stage.
What is the difference in Production Planning and Scheduling, you ask?
Production Planning (PP), or production planning, is the process by which you determine what products are needed at any given time. Forecasting demand is one way to do this.
Scheduling refers to the process of allocating specific dates to tasks in order that they can be completed within a specified timeframe.
What skills should a production planner have?
Being a production planner is not easy. You need to be organized and flexible. It is also important to be able communicate with colleagues and clients.
How can we improve manufacturing efficiency?
First, identify the factors that affect production time. Then we need to find ways to improve these factors. You can start by identifying the most important factors that impact production time. Once you've identified them, try to find solutions for each of those factors.
How can manufacturing reduce production bottlenecks?
You can avoid bottlenecks in production by making sure that everything runs smoothly throughout the production cycle, from the moment you receive an order to the moment the product is shipped.
This includes both quality control and capacity planning.
Continuous improvement techniques like Six Sigma are the best way to achieve this.
Six Sigma can be used to improve the quality and decrease waste in all areas of your company.
It emphasizes consistency and eliminating variance in your work.
Statistics
- (2:04) MTO is a production technique wherein products are customized according to customer specifications, and production only starts after an order is received. (oracle.com)
- According to a Statista study, U.S. businesses spent $1.63 trillion on logistics in 2019, moving goods from origin to end user through various supply chain network segments. (netsuite.com)
- You can multiply the result by 100 to get the total percent of monthly overhead. (investopedia.com)
- In the United States, for example, manufacturing makes up 15% of the economic output. (twi-global.com)
- Job #1 is delivering the ordered product according to specifications: color, size, brand, and quantity. (netsuite.com)
External Links
How To
How to use lean manufacturing in the production of goods
Lean manufacturing (or lean manufacturing) is a style of management that aims to increase efficiency, reduce waste and improve performance through continuous improvement. It was first developed in Japan in the 1970s/80s by Taiichi Ahno, who was awarded the Toyota Production System (TPS), award from KanjiToyoda, the founder of TPS. Michael L. Watkins published the book "The Machine That Changed the World", which was the first to be published about lean manufacturing.
Lean manufacturing is often defined as a set of principles used to improve the quality, speed, and cost of products and services. It emphasizes the elimination of defects and waste throughout the value stream. Lean manufacturing is also known as just in time (JIT), zero defect total productive maintenance(TPM), and five-star (S). Lean manufacturing focuses on eliminating non-value-added activities such as rework, inspection, and waiting.
Lean manufacturing improves product quality and costs. It also helps companies reach their goals quicker and decreases employee turnover. Lean manufacturing can be used to manage all aspects of the value chain. Customers, suppliers, distributors, retailers and employees are all included. Lean manufacturing is widely used in many industries. Toyota's philosophy, for example, is what has enabled it to be successful in electronics, automobiles, medical devices, healthcare and chemical engineering as well as paper and food.
Lean manufacturing is based on five principles:
-
Define Value - Determine the value that your business brings to society. Also, identify what sets you apart from your competitors.
-
Reduce waste - Get rid of any activity that does not add value to the supply chain.
-
Create Flow. Ensure that your work is uninterrupted and flows seamlessly.
-
Standardize and simplify – Make processes as repeatable and consistent as possible.
-
Build relationships - Develop and maintain personal relationships with both your internal and external stakeholders.
Although lean manufacturing isn't a new concept in business, it has gained popularity due to renewed interest in the economy after the 2008 global financial crisis. Many businesses are now using lean manufacturing to improve their competitiveness. In fact, some economists believe that lean manufacturing will be an important factor in economic recovery.
Lean manufacturing is becoming a popular practice in automotive. It has many advantages. These include higher customer satisfaction levels, reduced inventory levels as well as lower operating costs.
Lean manufacturing can be applied to almost every aspect of an organization. However, it is particularly useful when applied to the production side of an organization because it ensures that all steps in the value chain are efficient and effective.
There are three types principally of lean manufacturing:
-
Just-in-Time Manufacturing (JIT): This type of lean manufacturing is commonly referred to as "pull systems." JIT stands for a system where components are assembled on the spot rather than being made in advance. This approach reduces lead time, increases availability and reduces inventory.
-
Zero Defects Manufacturing (ZDM),: ZDM is a system that ensures no defective units are left the manufacturing facility. If a part is required to be repaired on the assembly line, it should not be scrapped. This is true even for finished products that only require minor repairs prior to shipping.
-
Continuous Improvement (CI),: Continuous improvement aims improve the efficiency and effectiveness of operations by continuously identifying issues and making changes to reduce waste. Continuous improvement refers to continuous improvement of processes as well people and tools.