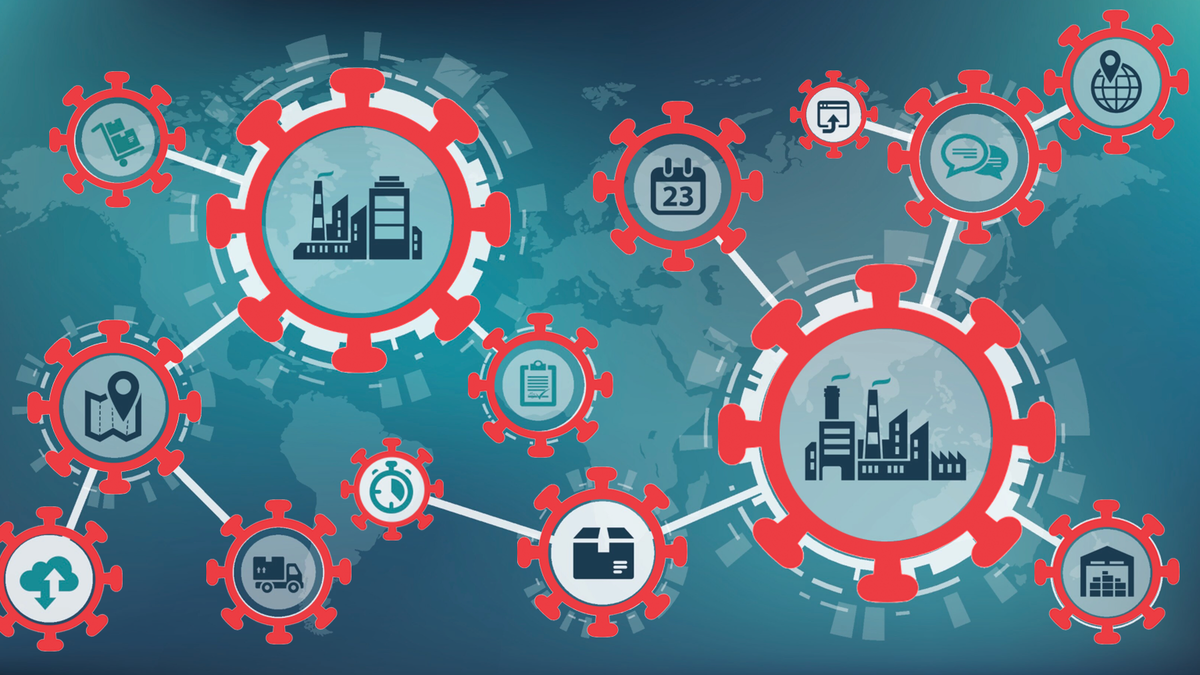
The growing interest in sustainable development has prompted manufacturing industry to integrate environmental management systems into its processes. These systems typically include formal monitoring and collaboration to solve problems and provide opportunities for continuous improvement. These systems are based in the ISO 14001 Standard, which requires that all organizations have an Environmental Management System to reduce waste, pollution, and improve the environment.
Studies have shown that lean production practices improve the environment's performance by reducing waste. All activities that use resources are considered waste. Waste does not create any value. Instead, waste reduces the material required to produce the product. It has a negative effect upon the environment. In order to reduce waste, companies must adopt environmental management strategies that have aligned goals. These strategies can be implemented using lean manufacturing methods. These techniques include 5S and Kaizen Circle, Just in Time, Continuous improvement, Total productive maintenance, Kaizen Circle, and Total production maintenance.
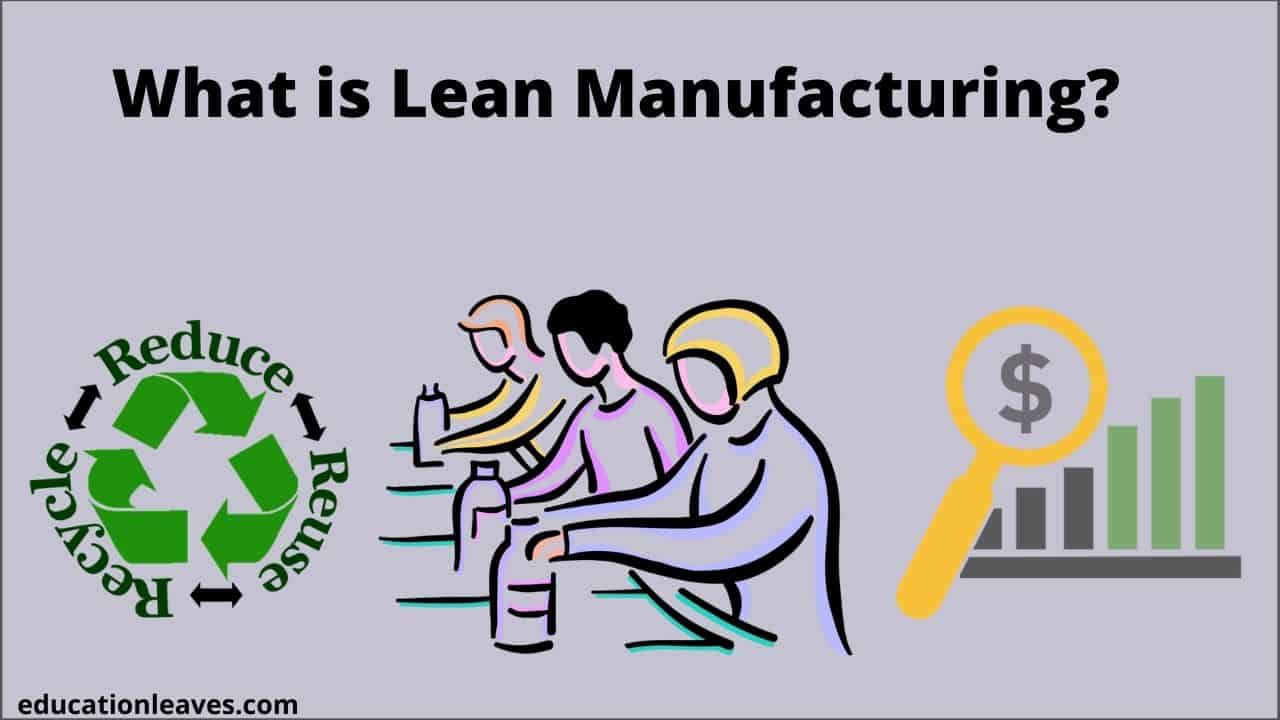
This study examines the relationship between Lean Production practices, and Environmental Management practices. We found a positive correlation between the concepts using multiple case studies. We also identified areas where LM can be beneficial. These areas include supply, logistics, production, quality management, and environmental protection. We investigated the level of implementation of these practices in companies in the North of Portugal. We also investigated the factors that affect the level of implementation of these practices. Particularly, we looked at whether implementation of lean practices can have a positive influence on the application green practices.
An assessment questionnaire was used in order to determine the level of implementation and effectiveness of LM and Green practices within these companies. The questionnaire had two parts. One asked questions about the company. The second included questions about environmental management. The results from the first part were analyzed with the help of the SEM approach. The results were good matches with the data sample. The SEM approach revealed that 76% (or 76%) of the variance in environmental practices could be explained by the model.
The results of the test agree with the literature. We should reconsider the role and involvement of employees in the implementation green practices. It is possible to be passive and not achieve the desired results. Important practice bundles can also be important. We also found that LM and green practices have a positive effect on environmental performance.
Our research also showed that employees' involvement had an impact on the effectiveness of both lean management and green practices. This is because LM involves employee engagement and participation in the production process, which leads to higher efficiency. This can have an effect on the relationship between lean practices & environmental performance. It is therefore important to analyze the relationship between lean tools and environmental practices.
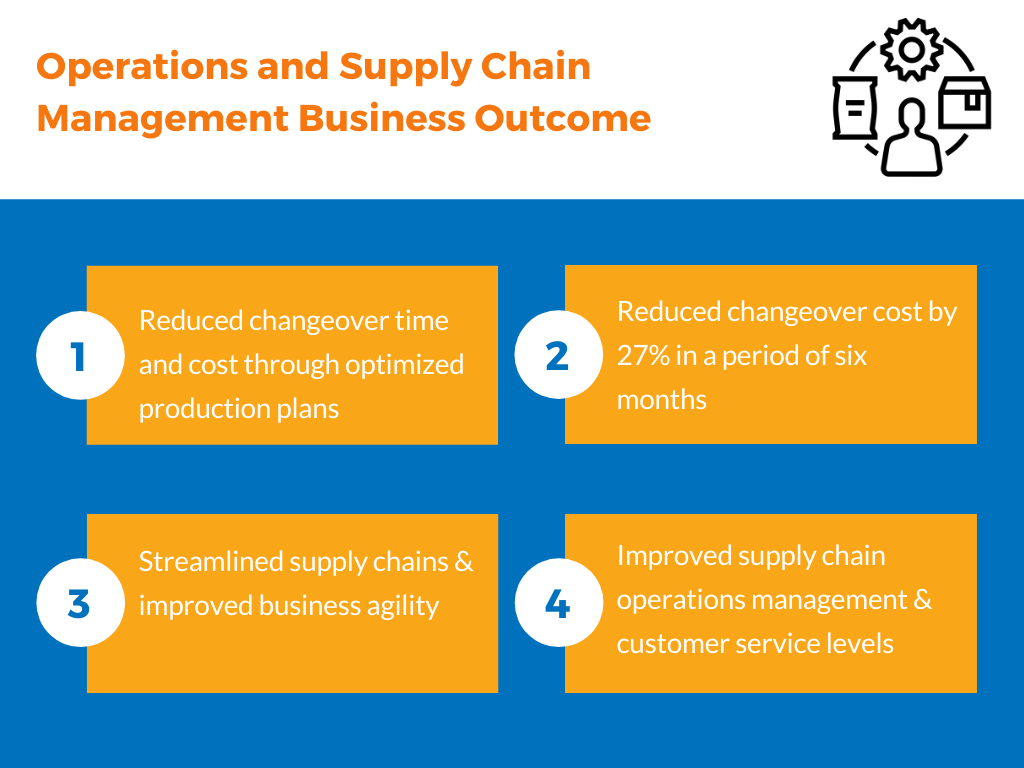
A majority of respondents claimed that Lean Production technologies reduce environmental impact. They also stated that they don't recognize the contributions of Lean Production technologies to their strategic planning.
FAQ
Is it possible to automate certain parts of manufacturing
Yes! Yes. The Egyptians invented the wheel thousands of years ago. To help us build assembly lines, we now have robots.
There are many applications for robotics in manufacturing today. These include:
-
Assembly line robots
-
Robot welding
-
Robot painting
-
Robotics inspection
-
Robots that create products
Automation could also be used to improve manufacturing. 3D printing, for example, allows us to create custom products without waiting for them to be made.
Is automation important in manufacturing?
Not only are service providers and manufacturers important, but so is automation. It allows them provide faster and more efficient services. It helps them to lower costs by reducing human errors, and improving productivity.
What are the essential elements of running a logistics firm?
To run a successful logistics company, you need a lot knowledge and skills. Effective communication skills are necessary to work with suppliers and clients. You will need to know how to interpret data and draw conclusions. You must be able and able to handle stress situations and work under pressure. To improve efficiency, you must be innovative and creative. You must be a strong leader to motivate others and direct them to achieve organizational goals.
You must be organized to meet tight deadlines.
How can manufacturing efficiency be improved?
First, identify the factors that affect production time. The next step is to identify the most important factors that affect production time. If you don’t know how to start, look at which factors have the greatest impact upon production time. Once you have identified them, it is time to identify solutions.
What jobs are available in logistics?
There are different kinds of jobs available in logistics. Here are some examples:
-
Warehouse workers – They load, unload and transport pallets and trucks.
-
Transport drivers - These are people who drive trucks and trailers to transport goods or perform pick-ups.
-
Freight handlers, - They sort out and pack freight in warehouses.
-
Inventory managers - They oversee the inventory of goods in warehouses.
-
Sales representatives - They sell products.
-
Logistics coordinators – They plan and coordinate logistics operations.
-
Purchasing agents - They buy goods and services that are necessary for company operations.
-
Customer service representatives - They answer calls and emails from customers.
-
Shippers clerks - They process shipping order and issue bills.
-
Order fillers - These people fill orders based on what has been ordered.
-
Quality control inspectors: They inspect outgoing and incoming products for any defects.
-
Others – There are many other types available in logistics. They include transport supervisors, cargo specialists and others.
How can overproduction in manufacturing be reduced?
Improved inventory management is the key to reducing overproduction. This would reduce the time needed to manage inventory. This could help us free up our time for other productive tasks.
You can do this by adopting a Kanban method. A Kanban board, a visual display to show the progress of work, is called a Kanban board. Work items are moved through various states to reach their destination in a Kanban system. Each state represents a different priority level.
As an example, if work is progressing from one stage of the process to another, then the current task is complete and can be transferred to the next. But if a task remains in the beginning stages it will stay that way until it reaches its end.
This helps to keep work moving forward while ensuring that no work is left behind. Managers can monitor the work being done by Kanban boards to see what is happening at any given time. This allows them to adjust their workflows based on real-time information.
Lean manufacturing, another method to control inventory levels, is also an option. Lean manufacturing works to eliminate waste throughout every stage of the production chain. Anything that does nothing to add value to a product is waste. Some common types of waste include:
-
Overproduction
-
Inventory
-
Unnecessary packaging
-
Overstock materials
By implementing these ideas, manufacturers can improve efficiency and cut costs.
What is production plan?
Production Planning is the creation of a plan to cover all aspects, such as scheduling, budgeting. Location, crew, equipment, props and other details. This document ensures that everything is prepared and available when you are ready for shooting. You should also have information to ensure the best possible results on set. This includes information on shooting times, locations, cast lists and crew details.
The first step is to outline what you want to film. You may already know where you want the film to be shot, or perhaps you have specific locations and sets you wish to use. Once you have identified your locations and scenes it's time to begin figuring out what elements you will need for each one. One example is if you are unsure of the exact model you want but decide that you require a car. If this is the case, you might start searching online for car models and then narrow your options by selecting from different makes.
Once you have found the right vehicle, you can think about adding accessories. What about additional seating? Or maybe you just need someone to push the car around. Maybe you'd like to change the interior from black to a white color. These questions can help you decide the right look for your car. The type of shots that you are looking for is another thing to consider. You will be filming close-ups and wide angles. Maybe you want the engine or the steering wheels to be shown. These factors will help you determine which car style you want to film.
Once you have established all the details, you can create a schedule. A schedule will tell you when you need to start shooting and when you need to finish. A schedule for each day will detail when you should arrive at the location and when you need leave. This way, everyone knows what they need to do and when. If you need to hire extra staff, you can make sure you book them in advance. You don't want to hire someone who won't show up because he didn't know.
Also, consider how many days you will be filming your schedule. Some projects are quick and easy, while others take weeks. It is important to consider whether you require more than one photo per day when you create your schedule. Multiplying takes in the same area will result both in increased costs and a longer time. It's better to be safe than sorry and shoot less takes if you're not certain whether you need more takes.
Budget setting is another important aspect in production planning. As it will allow you and your team to work within your financial means, setting a realistic budget is crucial. Keep in mind that you can always reduce your budget if you face unexpected difficulties. But, don't underestimate how much money you'll spend. If you underestimate the cost of something, you will have less money left after paying for other items.
Production planning is a detailed process. But, once you understand the workings of everything, it becomes easier for future projects to be planned.
Statistics
- In 2021, an estimated 12.1 million Americans work in the manufacturing sector.6 (investopedia.com)
- [54][55] These are the top 50 countries by the total value of manufacturing output in US dollars for its noted year according to World Bank.[56] (en.wikipedia.org)
- In the United States, for example, manufacturing makes up 15% of the economic output. (twi-global.com)
- (2:04) MTO is a production technique wherein products are customized according to customer specifications, and production only starts after an order is received. (oracle.com)
- According to a Statista study, U.S. businesses spent $1.63 trillion on logistics in 2019, moving goods from origin to end user through various supply chain network segments. (netsuite.com)
External Links
How To
How to use lean manufacturing in the production of goods
Lean manufacturing is a management system that aims at increasing efficiency and reducing waste. It was developed by Taiichi Okono in Japan, during the 1970s & 1980s. TPS founder Kanji Takoda awarded him the Toyota Production System Award (TPS). Michael L. Watkins published the first book on lean manufacturing in 1990.
Lean manufacturing is often defined as a set of principles used to improve the quality, speed, and cost of products and services. It emphasizes the elimination and minimization of waste in the value stream. Just-in-time (JIT), zero defect (TPM), and 5S are all examples of lean manufacturing. Lean manufacturing emphasizes reducing non-value-added activities like inspection, rework and waiting.
Lean manufacturing improves product quality and costs. It also helps companies reach their goals quicker and decreases employee turnover. Lean Manufacturing is one of the most efficient ways to manage the entire value chains, including suppliers and customers as well distributors and retailers. Many industries worldwide use lean manufacturing. Toyota's philosophy is the foundation of its success in automotives, electronics and appliances, healthcare, chemical engineers, aerospace, paper and food, among other industries.
Five fundamental principles underlie lean manufacturing.
-
Define value - Find out what your business contributes to society, and what makes it different from other competitors.
-
Reduce Waste - Eliminate any activity that doesn't add value along the supply chain.
-
Create Flow - Make sure work runs smoothly without interruptions.
-
Standardize & Simplify - Make processes as consistent and repeatable as possible.
-
Build relationships - Develop and maintain personal relationships with both your internal and external stakeholders.
Although lean manufacturing isn't a new concept in business, it has gained popularity due to renewed interest in the economy after the 2008 global financial crisis. Many businesses are now using lean manufacturing to improve their competitiveness. Some economists even believe that lean manufacturing can be a key factor in economic recovery.
Lean manufacturing is becoming a popular practice in automotive. It has many advantages. These benefits include increased customer satisfaction, reduced inventory levels and lower operating costs.
Any aspect of an enterprise can benefit from Lean manufacturing. Lean manufacturing is most useful in the production sector of an organisation because it ensures that each step in the value-chain is efficient and productive.
There are three types principally of lean manufacturing:
-
Just-in Time Manufacturing: This lean manufacturing method is commonly called "pull systems." JIT stands for a system where components are assembled on the spot rather than being made in advance. This approach aims to reduce lead times, increase the availability of parts, and reduce inventory.
-
Zero Defects Manufacturing: ZDM ensures that no defective units leave the manufacturing plant. If a part is required to be repaired on the assembly line, it should not be scrapped. This applies to finished goods that may require minor repairs before shipment.
-
Continuous Improvement (CI),: Continuous improvement aims improve the efficiency and effectiveness of operations by continuously identifying issues and making changes to reduce waste. Continuous Improvement (CI) involves continuous improvement in processes, people, tools, and infrastructure.