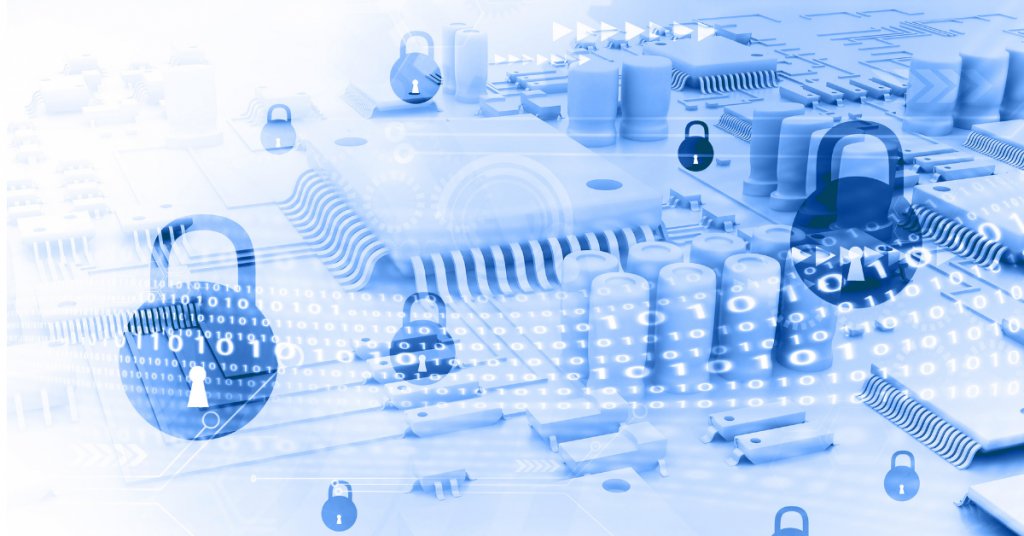
A blue collar job generally refers to manual labor. These jobs can be in any field, including construction, manufacturing and hospitality. Some jobs require some skill, like a plumber or electrician. Others may need to be learned by others. Blue collar jobs tend to pay decent salaries and offer good career growth.
The Fourth Industrial Revolution is changing the landscape for manual workers. This revolution includes robotics, artificial intelligence, machine learning, 3D printing, and robots. Companies will need a new and more skilled workforce in order to succeed. Companies will need to shift from transactional relationships towards more lasting ones.
This means that companies may have to hire workers from other countries. In some cases, these workers can be hired per-item. Other workers may be paid directly by the project. The rise in blue collar jobs is encouraging.
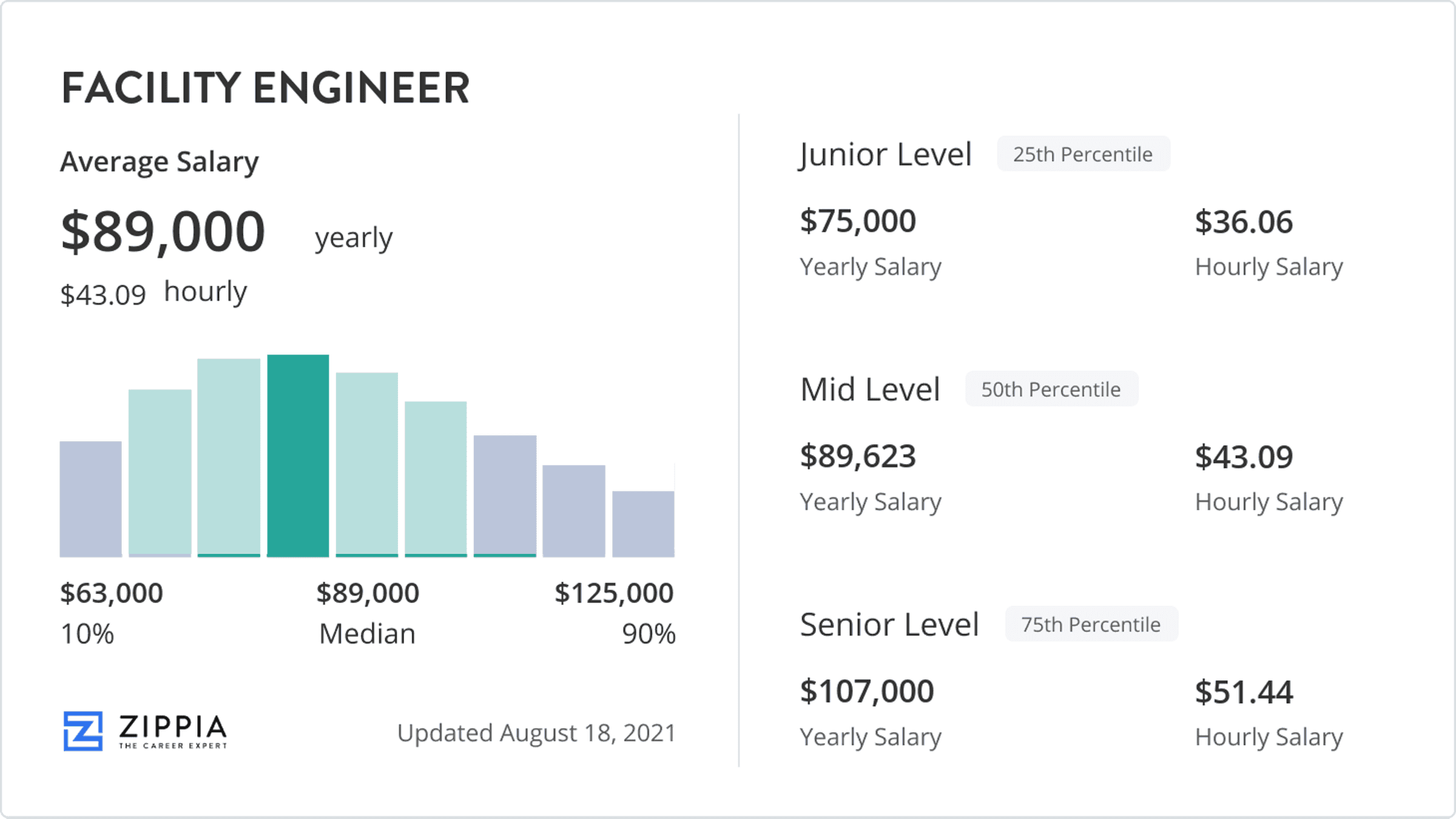
These jobs do require some physical labor but are generally more lucrative than white collar jobs. These jobs are an excellent source of income and many companies will invest in training their staff. There are many examples of these jobs, including signal and track switches repairers and nuclear power plant operators. These jobs do not require a highschool diploma. However, some require on-thejob training.
Blue collar jobs are also more plentiful than white collar jobs. Blue collar workers actually make up a large part of India's workforce. India has approximately 210 million employees in the agriculture sector and 290 millions in the nonagricultural. Blue collar workers are in high demand.
Companies will also be able to manage their blue-collar employees differently thanks to the Fourth Industrial Revolution. Not only are digital jobs replacing manual ones, but firms are also moving away form transactional relationships and toward lasting ones. By putting employee needs first, firms are able to build stronger relationships and improved productivity.
Blue collar workers are also in demand, but they face competing realities. They might be worried about the stability and retirement of their jobs. Regardless of these concerns, blue collar workers tend to be optimistic about their futures. The percentage of blue-collar workers who are saving for retirement is actually increasing. The popularity of blue collar jobs is likely to increase as the economy recovers.
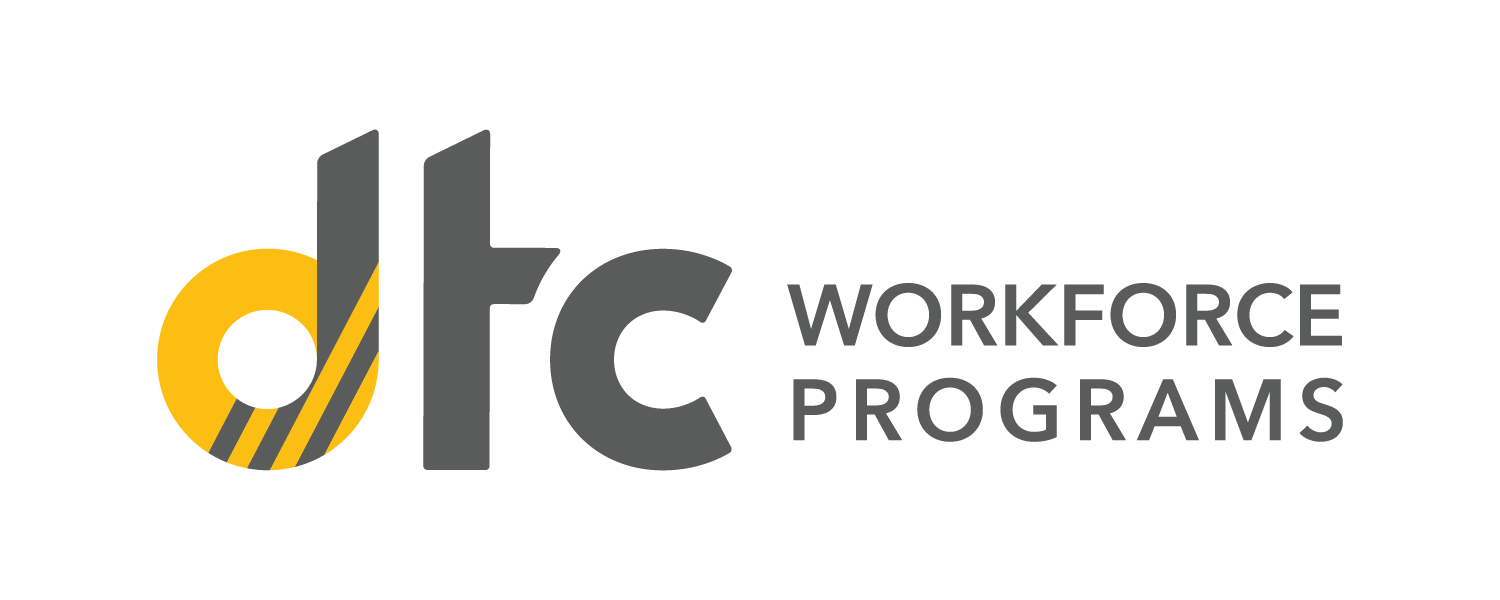
These jobs are also not threatened by automation. According to the Association for Manufacturing Technology (AMT), for every job that was automated, five new jobs were created. Signal and track switch technicians earned $76,210 per year, the average salary.
In addition to being more lucrative, blue collar positions are also becoming more popular. Blue collar jobs often earn well above the average national wage, which makes them a desirable option for those who are looking for a job that pays well. Many blue collar jobs demand a high level of problem solving skills and can provide excellent career growth opportunities.
FAQ
What are the responsibilities of a logistic manager?
A logistics manager ensures that all goods are delivered on time and without damage. This is done through his/her expertise and knowledge about the company's product range. He/she should make sure that enough stock is on hand to meet the demands.
What are the responsibilities of a production planner
A production planner ensures all aspects of the project are delivered on time, within budget, and within scope. A production planner ensures that the service and product meet the client's expectations.
How can excess manufacturing production be reduced?
It is essential to find better ways to manage inventory to reduce overproduction. This would reduce the time needed to manage inventory. This would allow us to use our resources for more productive tasks.
Kanban systems are one way to achieve this. A Kanban board is a visual display used to track work in progress. Work items are moved through various states to reach their destination in a Kanban system. Each state is assigned a different priority.
If work is moving from one stage to the other, then the current task can be completed and moved on to the next. If a task is still in its beginning stages, it will continue to be so until it reaches the end.
This helps to keep work moving forward while ensuring that no work is left behind. A Kanban board allows managers to monitor how much work is being completed at any given moment. This allows them to adjust their workflows based on real-time information.
Lean manufacturing is another way to manage inventory levels. Lean manufacturing works to eliminate waste throughout every stage of the production chain. Any product that isn't adding value can be considered waste. Some common types of waste include:
-
Overproduction
-
Inventory
-
Unnecessary packaging
-
Excess materials
Manufacturers can reduce their costs and improve their efficiency by using these ideas.
Why automate your factory?
Modern warehouses are increasingly dependent on automation. With the rise of ecommerce, there is a greater demand for faster delivery times as well as more efficient processes.
Warehouses must adapt quickly to meet changing customer needs. They must invest heavily in technology to do this. Automating warehouses is a great way to save money. These are just a few reasons to invest in automation.
-
Increases throughput/productivity
-
Reduces errors
-
Improves accuracy
-
Boosts safety
-
Eliminates bottlenecks
-
Companies can scale more easily
-
It makes workers more efficient
-
Gives you visibility into all that is happening in your warehouse
-
Enhances customer experience
-
Improves employee satisfaction
-
This reduces downtime while increasing uptime
-
You can be sure that high-quality products will arrive on time
-
Human error can be eliminated
-
Assure compliance with regulations
What is the job of a manufacturer manager?
Manufacturing managers must ensure that manufacturing processes are efficient, effective, and cost-effective. They should also be aware of any problems within the company and act accordingly.
They should also be able communicate with other departments, such as sales or marketing.
They should be informed about industry trends and be able make use of this information to improve their productivity and efficiency.
What are the differences between these four types?
Manufacturing is the process by which raw materials are transformed into useful products through machines and processes. It can involve many activities like designing, manufacturing, testing packaging, shipping, selling and servicing.
Statistics
- (2:04) MTO is a production technique wherein products are customized according to customer specifications, and production only starts after an order is received. (oracle.com)
- According to a Statista study, U.S. businesses spent $1.63 trillion on logistics in 2019, moving goods from origin to end user through various supply chain network segments. (netsuite.com)
- You can multiply the result by 100 to get the total percent of monthly overhead. (investopedia.com)
- Many factories witnessed a 30% increase in output due to the shift to electric motors. (en.wikipedia.org)
- Job #1 is delivering the ordered product according to specifications: color, size, brand, and quantity. (netsuite.com)
External Links
How To
How to Use Six Sigma in Manufacturing
Six Sigma is defined by "the application SPC (statistical process control) techniques to achieve continuous improvements." It was developed by Motorola's Quality Improvement Department at their plant in Tokyo, Japan, in 1986. Six Sigma is a method to improve quality through standardization and elimination of defects. Many companies have adopted Six Sigma in recent years because they believe that there are no perfect products and services. The main goal of Six Sigma is to reduce variation from the mean value of production. This means that you can take a sample from your product and then compare its performance to the average to find out how often the process differs from the norm. If it is too large, it means that there are problems.
Understanding the nature of variability in your business is the first step to Six Sigma. Once you have a good understanding of the basics, you can identify potential sources of variation. Also, you will need to identify the sources of variation. Random variations are caused by human errors. Systematic variations can be caused by outside factors. If you make widgets and some of them end up on the assembly line, then those are considered random variations. It would be considered a systematic problem if every widget that you build falls apart at the same location each time.
Once you have identified the problem, you can design solutions. You might need to change the way you work or completely redesign the process. Test them again once you've implemented the changes. If they don't work you need to rework them and come up a better plan.