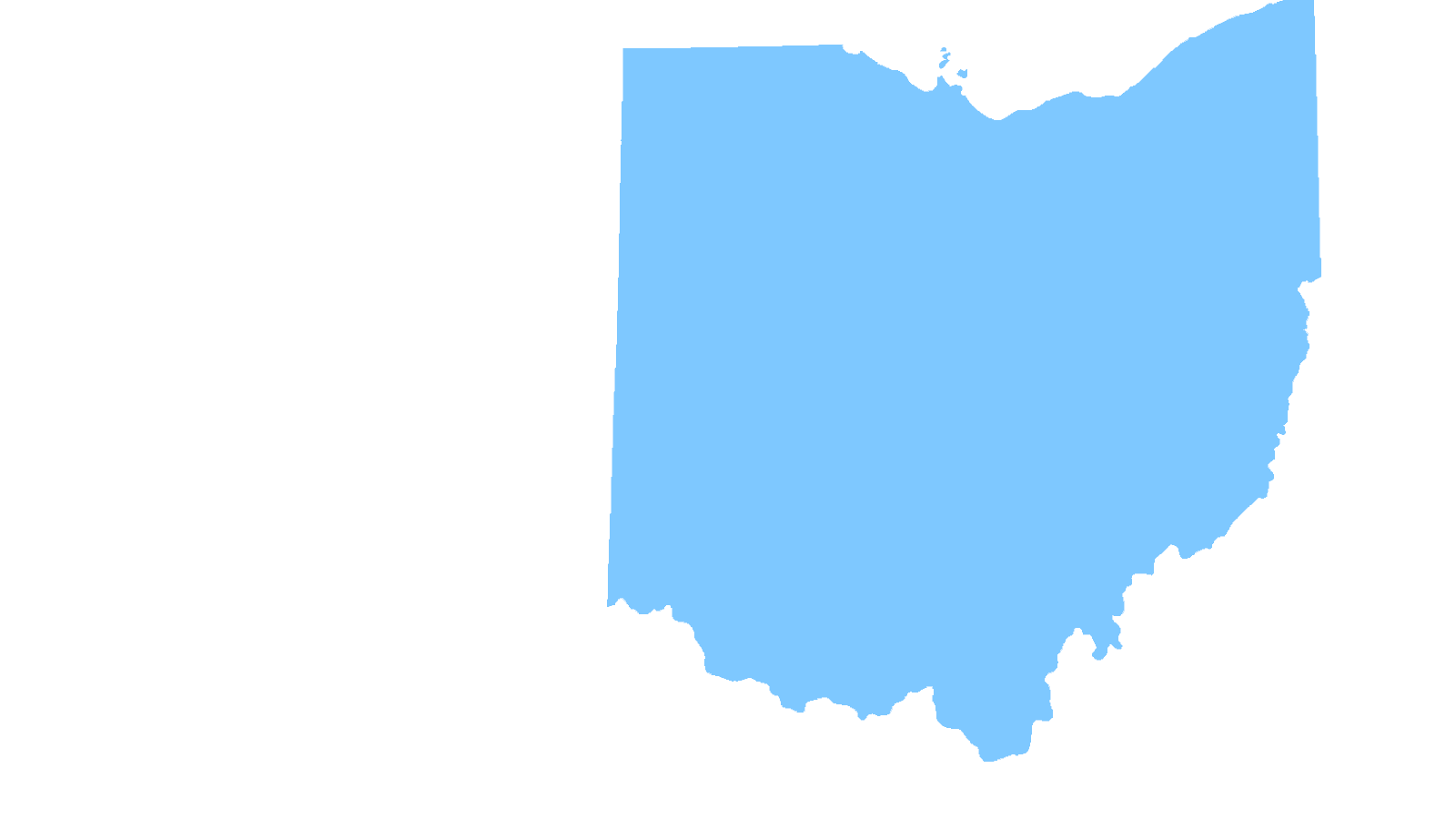
Classical economics identifies three fundamental sectors. These three main sectors include manufacturing, finance, and services. The characteristics and risk factors that go into a business' classification are important. Each of these three sectors is described below. Below is a brief overview about the types of businesses found in each sector. You can further dive into this information if you are interested. Keep in mind, however, that these categories don't have to be mutually exclusive.
Economic activity
Factors used in production, inputs and outputs determine the economic activity of a country or nation. A region's economic activity is often determined by the demand for a specific good or service. There are two types, primary and secondary, of economic activity. Primary economic activities offer goods and services that meet human needs. Secondary economic activities add value to raw materials to create a more valuable product. Examples of secondary economy activities include the manufacturing and processing sectors.
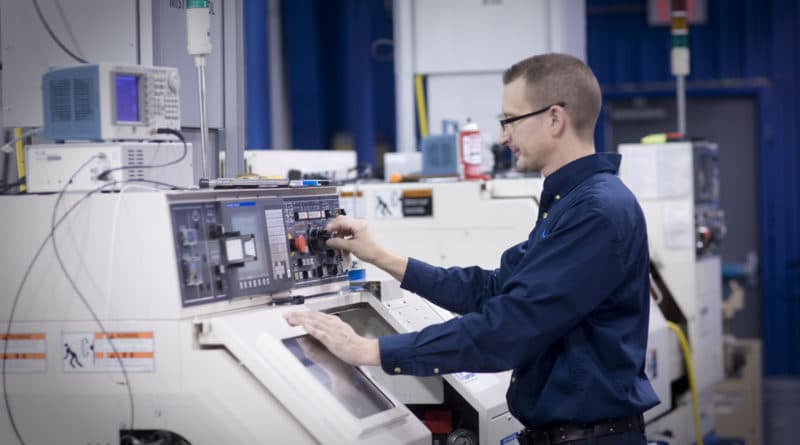
Classification of businesses
Business classification refers to the process of grouping businesses based on their activities. There are two types of businesses: primary and secondary. Primary businesses are those that use natural resources to extract them and then exchange them. The second kind of business converts raw materials and produces products for sale. There are many differences among these types of businesses. Listed below are some of the major differences between the two types. This article can help you choose the right type of business for your company.
Characteristics
This discussion will explain the differences between primary, secondary and tertiary sector and focus on the economic impact of each. First, let's define sectors. Sectors can be considered unique economic entities. They respond differently depending on different factors. These situations may arise from repeated events such as business cycles or single events such as technological advances. These characteristics can be used to identify the most lucrative sectors and to determine their relative importance in an economy.
There are always risks
Industry risk is the variation of performance across industries and among companies. This can be assessed by looking at the variance in profitability and return on equity (ROE). This can be adjusted depending on industry to reflect the performance stock markets. An example of this is a steel company, which is considered to be at high risk because there are potential earthquakes in the region. An analysis of these risks can help investors identify volatile sectors.
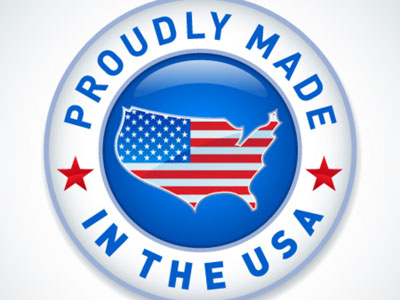
Investments
While some investors may invest in specific companies or sectors, others might choose to invest in broader areas. Sectors offer lower risks and can be found in mutual funds and exchange-traded funds. Sector investing is also becoming a popular investment strategy. This article will show you how sector investing can help find the right investments. Read on to learn more. You can also visit our free resource section for additional information.
FAQ
Why is logistics so important in manufacturing?
Logistics are an essential component of any business. Logistics can help you achieve amazing results by helping to manage product flow from raw materials to finished products.
Logistics also play a major role in reducing costs and increasing efficiency.
Are there ways to automate parts of manufacturing?
Yes! Yes! Automation has existed since ancient times. The Egyptians invented the wheel thousands of years ago. Today, robots assist in the assembly of lines.
There are many uses of robotics today in manufacturing. These include:
-
Robots for assembly line
-
Robot welding
-
Robot painting
-
Robotics inspection
-
Robots that make products
Manufacturing can also be automated in many other ways. For instance, 3D printing allows us make custom products and not have to wait for months or even weeks to get them made.
What does manufacturing mean?
Manufacturing Industries are businesses that produce products for sale. The people who buy these products are called consumers. These companies employ many processes to achieve this purpose, such as production and distribution, retailing, management and so on. These companies produce goods using raw materials and other equipment. This includes all types of manufactured goods, including food items, clothing, building supplies, furniture, toys, electronics, tools, machinery, vehicles, pharmaceuticals, medical devices, chemicals, and many others.
Statistics
- According to a Statista study, U.S. businesses spent $1.63 trillion on logistics in 2019, moving goods from origin to end user through various supply chain network segments. (netsuite.com)
- In the United States, for example, manufacturing makes up 15% of the economic output. (twi-global.com)
- In 2021, an estimated 12.1 million Americans work in the manufacturing sector.6 (investopedia.com)
- According to the United Nations Industrial Development Organization (UNIDO), China is the top manufacturer worldwide by 2019 output, producing 28.7% of the total global manufacturing output, followed by the United States, Japan, Germany, and India.[52][53] (en.wikipedia.org)
- (2:04) MTO is a production technique wherein products are customized according to customer specifications, and production only starts after an order is received. (oracle.com)
External Links
How To
How to use 5S in Manufacturing to Increase Productivity
5S stands for "Sort", "Set In Order", "Standardize", "Separate" and "Store". Toyota Motor Corporation invented the 5S strategy in 1954. It improves the work environment and helps companies to achieve greater efficiency.
The idea behind standardizing production processes is to make them repeatable and measurable. This means that tasks such as cleaning, sorting, storing, packing, and labeling are performed daily. Because workers know what they can expect, this helps them perform their jobs more efficiently.
Implementing 5S involves five steps: Sort, Set in Order, Standardize Separate, Store, and Each step has a different action and leads to higher efficiency. Sorting things makes it easier to find them later. You arrange items by placing them in an order. Once you have separated your inventory into groups and organized them, you will store these groups in easily accessible containers. Make sure everything is correctly labeled when you label your containers.
This requires employees to critically evaluate how they work. Employees must be able to see why they do what they do and find a way to achieve them without having to rely on their old methods. To implement the 5S system, employees must acquire new skills and techniques.
The 5S Method not only improves efficiency, but it also helps employees to be more productive and happier. Once they start to notice improvements, they are motivated to keep working towards their goal of increasing efficiency.