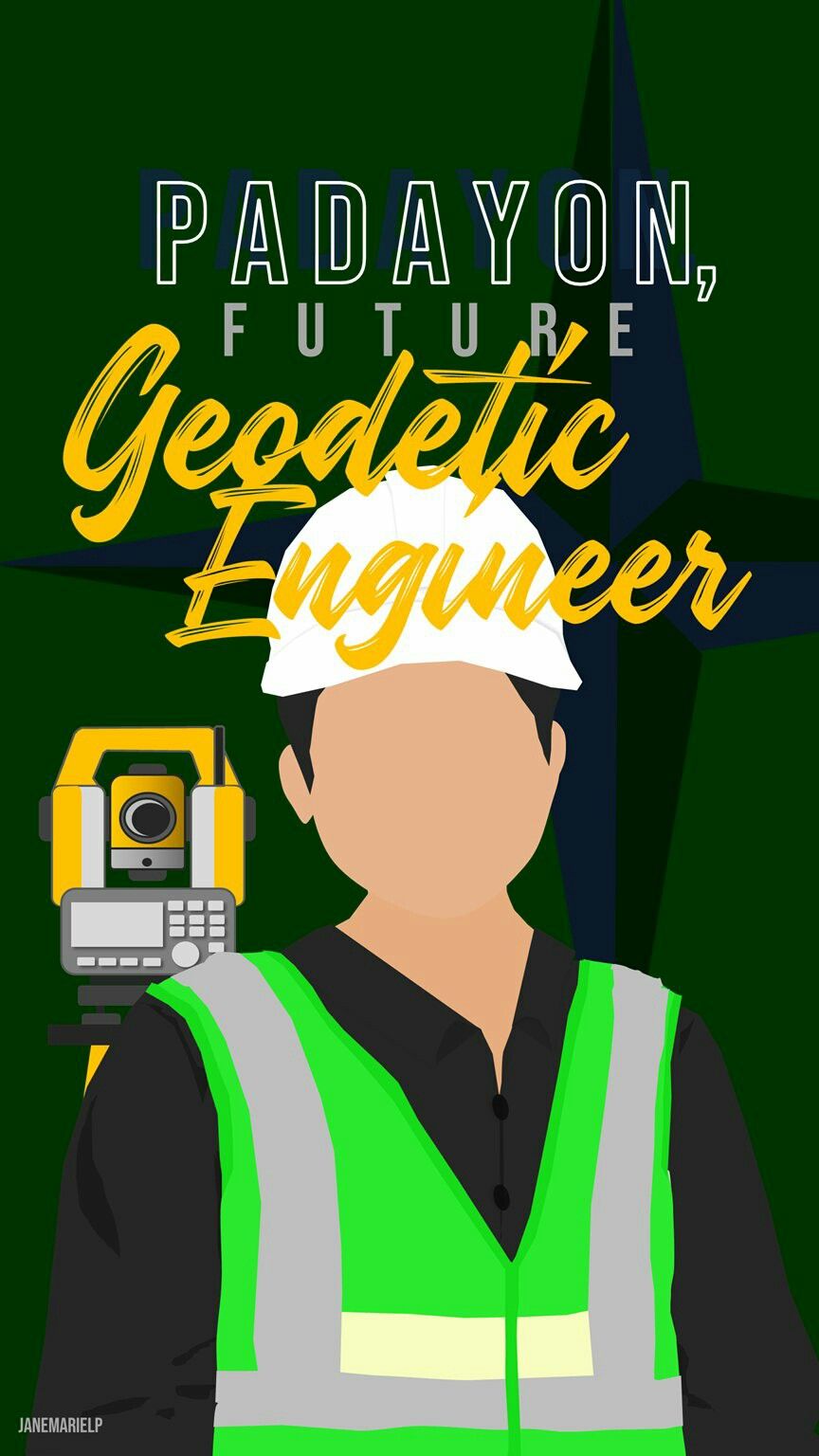
There are many types of manufacturers, but which one is best for your business? Learn more about Continuous manufacturing, Process manufacturing and Job shop manufacturing. Each type of manufacturing has its advantages and disadvantages. This article will describe the differences among these four types. You can choose the best model for your business based on your industry, location, and product type. After you have decided which model is right for you, you will need to think about your sales, production, quality control, and customer service.
Discrete manufacturing
Discrete manufacturing refers to a process where different products are made. These products include automobiles, toys, and aeroplanes. Discrete Manufacturing allows companies to focus more on their individual products than on mass production. In other words, discrete manufacture allows for the creation of unique parts in an aeroplane using multiple manufacturing processes. High-tech products can be made by discrete manufacturing.
Discrete manufacturing produces distinct items. Instead of producing multiple identical products, discrete manufacturing produces items that can be easily identified by serial numbers, labels, and other numerical attributes. One example of this is a smartphone made up different parts in different states. Once the product has been shipped, the parts are assembled. This is also true for the bag. It may contain different parts from several plants, including the headquarters and the Missouri plant.
Process manufacturing
The idea of process manufacturing is a sub-field of manufacturing that includes formulas and recipes. The term process manufacturing is not the same as discrete manufacturing. This refers to manufacturing that involves individual units, bills or materials and the assembly of component parts. Both manufacturing methods have different goals. Each is essential to the manufacturing process. Here are three ways to differentiate process manufacturing from discrete manufacturing. Let's examine each one.
Batch process manufacturing is similar in many ways to continuous process manufacturing. However, it uses larger quantities and runs continuously. Batch process manufacturing can be found in paper production, pharmaceuticals, bookbinding, newspaper printing, and other industries. However, it is not the right choice for every industry. For smaller businesses, it can be too expensive and complex. This is why large-scale companies often use it when they need to make large quantities.
Job shop manufacturing
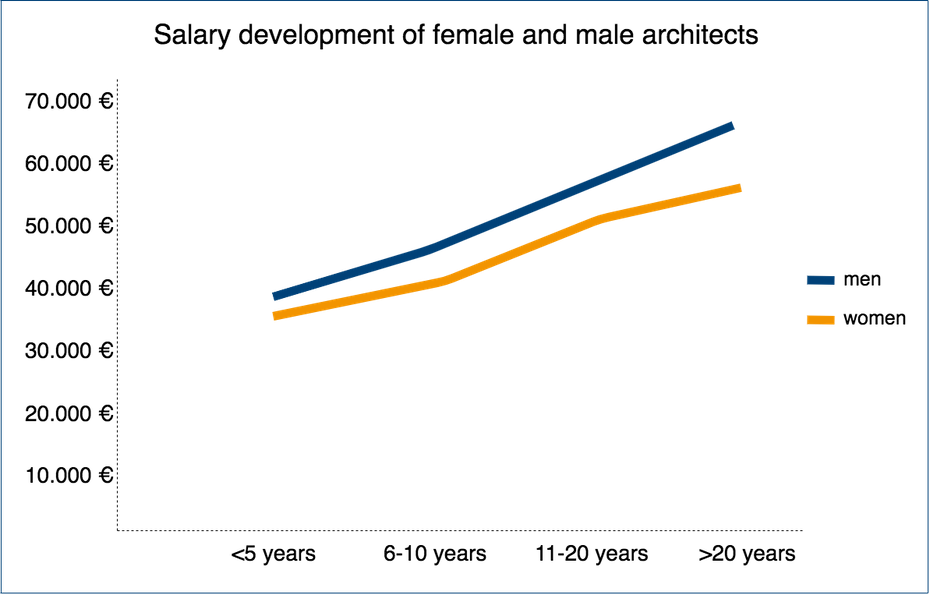
Job shop manufacturing is a small-scale system of production that specializes in custom, batch, and semi-custom manufacturing. Once each job has been completed, job shops can move on. This type of production is also known lean manufacturing. It is more efficient to use a single shift than many other methods. Here are some benefits of job shop manufacturing. This manufacturing process is described in detail below. For your business, you might want to consider it for your product or service needs.
First, job shop efficiency must be improved. The incorporation of new manufacturing principles is crucial to creating a lean manufacturing environment. These principles are particularly relevant for high-volume operations and emphasize quality control and just in-time production. Job shops can increase productivity and decrease costs by adopting new manufacturing methods. Additionally, every job should be processed individually, so there should not be a queue.
Continuous manufacturing
One of the biggest benefits of continuous manufacturing is the fact that it allows for much more flexible tracking. This is especially beneficial when it concerns product failure. Since the production line's time stamp and the raw material quantity can help identify when a batch has gone wrong, continuous manufacturing allows for more flexible tracking. The manufacturer also has a reduced risk of product shortages due to increased tracking. Similarly, continuous manufacturing is becoming popular in the pharmaceutical industry.
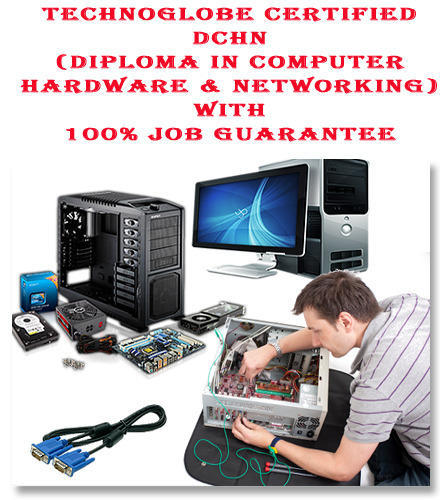
Despite the obvious benefits of continuous manufacturing, implementation can be slow. The fact that continuous manufacturing is not fully integrated into the company is often what hinders its implementation. Continuous manufacturing is a great opportunity for the pharmaceutical industry. Continuous manufacturing is only possible if the process integrates with end-to–end integration and continuous flow. While the benefits of continuous manufacturing have been well-known in the pharmaceutical sector, implementation has been slow.
FAQ
What kind of jobs are there in logistics?
There are many kinds of jobs available within logistics. Here are some examples:
-
Warehouse workers – They load, unload and transport pallets and trucks.
-
Transportation drivers - They drive trucks and trailers to deliver goods and carry out pick-ups.
-
Freight handlers, - They sort out and pack freight in warehouses.
-
Inventory managers: They are responsible for the inventory and management of warehouses.
-
Sales representatives: They sell products to customers.
-
Logistics coordinators – They plan and coordinate logistics operations.
-
Purchasing agents - They purchase goods and services needed for company operations.
-
Customer service representatives are available to answer customer calls and emails.
-
Shipping clerks: They process shipping requests and issue bills.
-
Order fillers - These people fill orders based on what has been ordered.
-
Quality control inspectors - They check incoming and outgoing products for defects.
-
Others - There are many types of jobs in logistics such as transport supervisors and cargo specialists.
How can we reduce manufacturing overproduction?
Better inventory management is key to reducing excess production. This would reduce the time spent on unproductive activities like purchasing, storing and maintaining excess stock. This would allow us to use our resources for more productive tasks.
A Kanban system is one way to achieve this. A Kanbanboard is a visual tool that allows you to keep track of the work being done. Kanban systems allow work items to move through different states until they reach their final destination. Each state is assigned a different priority.
When work is completed, it can be transferred to the next stage. But if a task remains in the beginning stages it will stay that way until it reaches its end.
This helps to keep work moving forward while ensuring that no work is left behind. Managers can see how much work has been done and the status of each task at any time with a Kanban Board. This allows them the ability to adjust their workflow using real-time data.
Lean manufacturing can also be used to reduce inventory levels. Lean manufacturing works to eliminate waste throughout every stage of the production chain. Anything that does nothing to add value to a product is waste. These are some of the most common types.
-
Overproduction
-
Inventory
-
Unnecessary packaging
-
Overstock materials
Manufacturers can increase efficiency and decrease costs by implementing these ideas.
What is the difference between a production planner and a project manager?
The difference between a product planner and project manager is that a planer is typically the one who organizes and plans the entire project. A production planner, however, is mostly involved in the planning stages.
Is it possible to automate certain parts of manufacturing
Yes! Automation has been around since ancient times. The Egyptians invented the wheel thousands of years ago. Today, robots assist in the assembly of lines.
There are many uses of robotics today in manufacturing. These include:
-
Automation line robots
-
Robot welding
-
Robot painting
-
Robotics inspection
-
Robots that create products
Manufacturing can also be automated in many other ways. For instance, 3D printing allows us make custom products and not have to wait for months or even weeks to get them made.
What are the 4 types manufacturing?
Manufacturing refers to the transformation of raw materials into useful products by using machines and processes. Manufacturing involves many activities, including designing, building, testing and packaging, shipping, selling, service, and so on.
How can manufacturing avoid production bottlenecks
You can avoid bottlenecks in production by making sure that everything runs smoothly throughout the production cycle, from the moment you receive an order to the moment the product is shipped.
This includes both planning for capacity and quality control.
This can be done by using continuous improvement techniques, such as Six Sigma.
Six Sigma management is a system that improves quality and reduces waste within your organization.
It is focused on creating consistency and eliminating variation in your work.
How can I learn about manufacturing?
The best way to learn about manufacturing is through hands-on experience. However, if that's not possible, you can always read books or watch educational videos.
Statistics
- According to the United Nations Industrial Development Organization (UNIDO), China is the top manufacturer worldwide by 2019 output, producing 28.7% of the total global manufacturing output, followed by the United States, Japan, Germany, and India.[52][53] (en.wikipedia.org)
- Job #1 is delivering the ordered product according to specifications: color, size, brand, and quantity. (netsuite.com)
- Many factories witnessed a 30% increase in output due to the shift to electric motors. (en.wikipedia.org)
- According to a Statista study, U.S. businesses spent $1.63 trillion on logistics in 2019, moving goods from origin to end user through various supply chain network segments. (netsuite.com)
- [54][55] These are the top 50 countries by the total value of manufacturing output in US dollars for its noted year according to World Bank.[56] (en.wikipedia.org)
External Links
How To
Six Sigma: How to Use it in Manufacturing
Six Sigma is defined as "the application of statistical process control (SPC) techniques to achieve continuous improvement." Motorola's Quality Improvement Department created Six Sigma at their Tokyo plant, Japan in 1986. The basic idea behind Six Sigma is to improve quality by improving processes through standardization and eliminating defects. Many companies have adopted this method in recent years. They believe there is no such thing a perfect product or service. Six Sigma's main objective is to reduce variations from the production average. If you take a sample and compare it with the average, you will be able to determine how much of the production process is different from the norm. If you notice a large deviation, then it is time to fix it.
Understanding the nature of variability in your business is the first step to Six Sigma. Once you've understood that, you'll want to identify sources of variation. It is important to identify whether the variations are random or systemic. Random variations occur when people do mistakes. Symmetrical variations are caused due to factors beyond the process. Random variations would include, for example, the failure of some widgets to fall from the assembly line. If however, you notice that each time you assemble a widget it falls apart in exactly the same spot, that is a problem.
Once you have identified the problem, you can design solutions. You might need to change the way you work or completely redesign the process. Test them again once you've implemented the changes. If they didn't work, then you'll need to go back to the drawing board and come up with another plan.