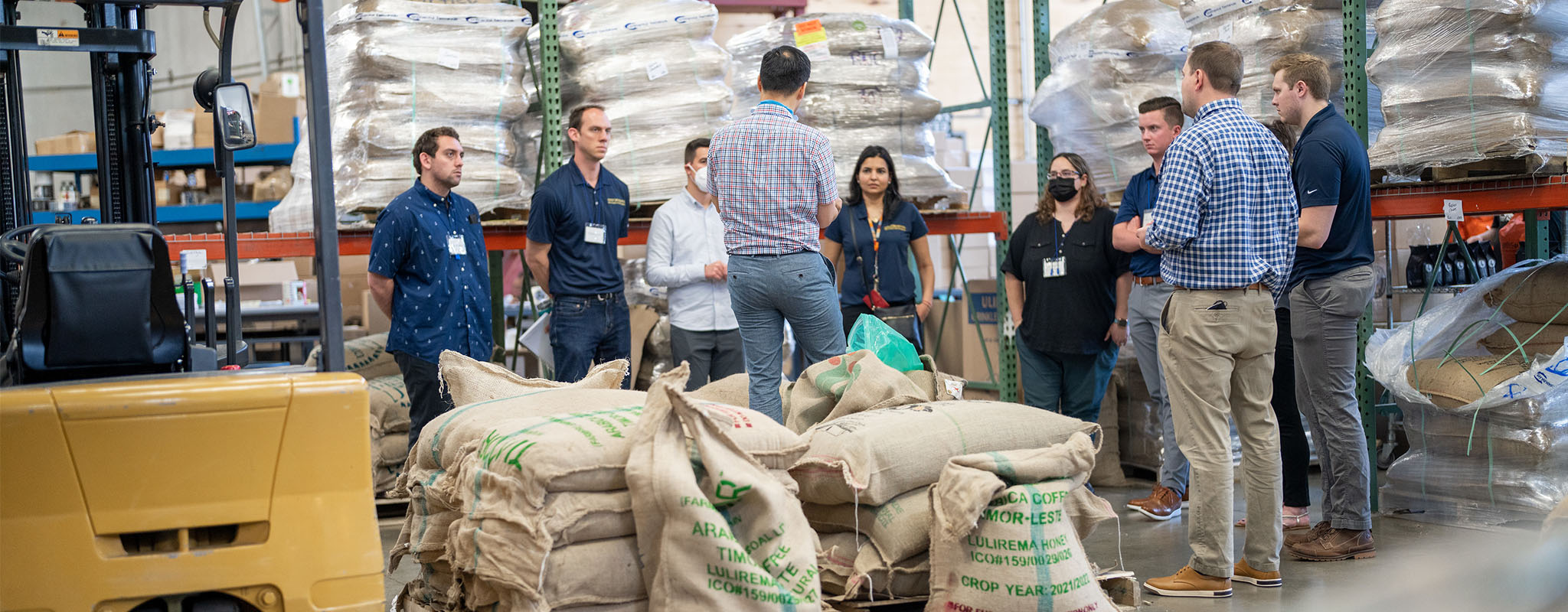
Denver, Colorado is home to a variety of job opportunities. It is home to many logistics companies, which provide a wide range of logistic services. Some of them include freight forwarding services, trucking and logistics & supply-chain consulting.
If you're interested in a career in logistics, you may want to consider a number of different positions, such as dispatcher, transportation director and warehouse assistant. All these positions are in charge of making sure the logistics within an organization run smoothly.
Dispatch Manager
A dispatcher's main responsibility is to direct and coordinate the work of a group that operates in a contact center or warehouse. This includes training new employees, delegating tasks, coordinating the workload of other team members, documenting productivity, and overseeing incoming and outgoing shipments. Dispatch managers usually have a bachelor's degree in business management or logistics and experience with workflow organization.
Transportation Director
A transportation supervisor is responsible for managing the logistics within a company, school, government agency, etc. This includes setting up distribution channels and arranging for transport methods such as trucks or buses to move products from one location.
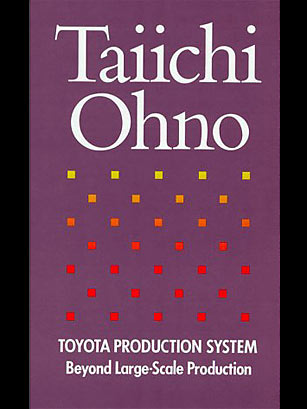
This career is suited to those who want to work for a larger company or government agency. This is a highly competitive career, so you must have good organizational skills and be willing work long hours.
Warehouse Associate
If you are looking for a job that is not as competitive, but offers a more flexible schedule, consider a warehouse associate. A warehouse associate typically handles smaller projects such as picking shipments, packing products, and moving merchandise to other locations.
You can start your job search by creating a Monster profile. You will be notified of all the logistics jobs available in your area.
You will also be able receive expert advice on how to maximize your job application and how to negotiate your wage, among other things.
Logistics Manager
You should at least have a bachelor’s degree in business administration or supply chain management if you plan to be a logistics manager. At least one year experience in the warehouse environment is needed, along with strong organizational skills. You can also earn a master's degree in supply chain management or another related field to become a senior logistics manager.
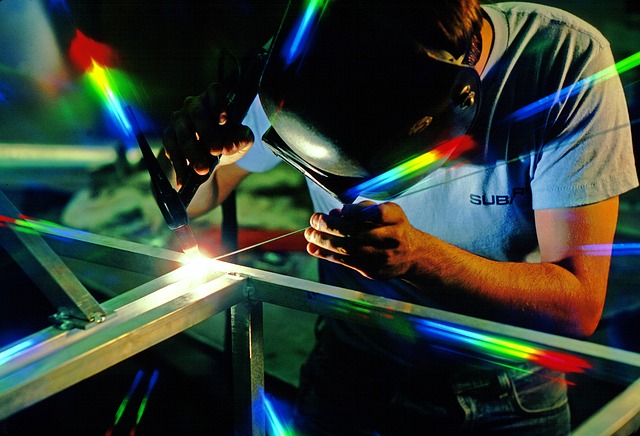
Logistik Analyst
A logistic analyst is responsible for monitoring the logistics of an organization and making changes to help it better achieve its goals. This involves evaluating inventory levels and scheduling delivery times. A logistics analysts must possess a bachelor’s degree, either in business or in engineering. He/she should also have some experience working with the logistics within a certain industry.
The logistics sector is expanding and offers many opportunities. Create your free Monster account if you want to pursue a career in logistics. You'll have the best chances to find the logistics jobs that are right for you if you create a free account on Monster.
FAQ
What is the difference between a production planner and a project manager?
The primary difference between a producer planner and a manager of a project is that the manager usually plans and organizes the whole project, while a production planner is only involved in the planning stage.
How can manufacturing efficiency be improved?
First, we need to identify which factors are most critical in affecting production times. The next step is to identify the most important factors that affect production time. If you don’t know how to start, look at which factors have the greatest impact upon production time. Once you identify them, look for solutions.
What are the responsibilities of a manufacturing manager
A manufacturing manager must ensure that all manufacturing processes are efficient and effective. They should be aware of any issues within the company and respond accordingly.
They should also be able communicate with other departments, such as sales or marketing.
They should also be aware of the latest trends in their industry and be able to use this information to help improve productivity and efficiency.
What is the difference in Production Planning and Scheduling, you ask?
Production Planning (PP) refers to the process of determining how much production is needed at any given moment. This can be done by forecasting demand and identifying production capabilities.
Scheduling refers the process by which tasks are assigned dates so that they can all be completed within the given timeframe.
What skills are required to be a production manager?
A production planner must be organized, flexible, and able multitask to succeed. Effective communication with clients and colleagues is essential.
Why is logistics important for manufacturing?
Logistics are an integral part any business. They can help you achieve great success by helping you manage product flow from raw material to finished goods.
Logistics also play a major role in reducing costs and increasing efficiency.
Statistics
- [54][55] These are the top 50 countries by the total value of manufacturing output in US dollars for its noted year according to World Bank.[56] (en.wikipedia.org)
- In the United States, for example, manufacturing makes up 15% of the economic output. (twi-global.com)
- (2:04) MTO is a production technique wherein products are customized according to customer specifications, and production only starts after an order is received. (oracle.com)
- According to the United Nations Industrial Development Organization (UNIDO), China is the top manufacturer worldwide by 2019 output, producing 28.7% of the total global manufacturing output, followed by the United States, Japan, Germany, and India.[52][53] (en.wikipedia.org)
- In 2021, an estimated 12.1 million Americans work in the manufacturing sector.6 (investopedia.com)
External Links
How To
How to use the Just-In Time Method in Production
Just-in-time is a way to cut costs and increase efficiency in business processes. It's the process of obtaining the right amount and timing of resources when you need them. This means that your only pay for the resources you actually use. Frederick Taylor was the first to coin this term. He developed it while working as a foreman during the early 1900s. He saw how overtime was paid to workers for work that was delayed. He decided to ensure workers have enough time to do their jobs before starting work to improve productivity.
The idea behind JIT is that you should plan ahead and have everything ready so you don't waste money. It is important to look at your entire project from beginning to end and ensure that you have enough resources to handle any issues that may arise. If you anticipate that there might be problems, you'll have enough people and equipment to fix them. This will ensure that you don't spend more money on things that aren't necessary.
There are many JIT methods.
-
Demand-driven: This type of JIT allows you to order the parts/materials required for your project on a regular basis. This will allow for you to track the material that you have left after using it. You'll also be able to estimate how long it will take to produce more.
-
Inventory-based : You can stock the materials you need in advance. This allows you to predict how much you can expect to sell.
-
Project-driven: This means that you have enough money to pay for your project. You will be able to purchase the right amount of materials if you know what you need.
-
Resource-based JIT is the most widespread form. Here, you allocate certain resources based on demand. You will, for example, assign more staff to deal with large orders. If you don’t have many orders you will assign less people to the work.
-
Cost-based: This approach is very similar to resource-based. However, you don't just care about the number of people you have; you also need to consider how much each person will cost.
-
Price-based: This approach is very similar to the cost-based method except that you don't look at individual workers costs but the total cost of the company.
-
Material-based: This is quite similar to cost-based, but instead of looking at the total cost of the company, you're concerned with how much raw materials you spend on average.
-
Time-based: This is another variation of resource-based JIT. Instead of focusing on the cost of each employee, you will focus on the time it takes to complete a project.
-
Quality-based JIT - This is another form of resource-based JIT. Instead of worrying about the costs of each employee or how long it takes for something to be made, you should think about how quality your product is.
-
Value-based JIT is the newest form of JIT. In this instance, you are not concerned about the product's performance or meeting customer expectations. Instead, you are focused on adding value to the marketplace.
-
Stock-based is an inventory-based system that measures the number of items produced at any given moment. It is used when production goals are met while inventory is kept to a minimum.
-
Just-intime planning (JIT), is a combination JIT/sales chain management. This refers to the scheduling of the delivery of components as soon after they are ordered. It reduces lead times and improves throughput.