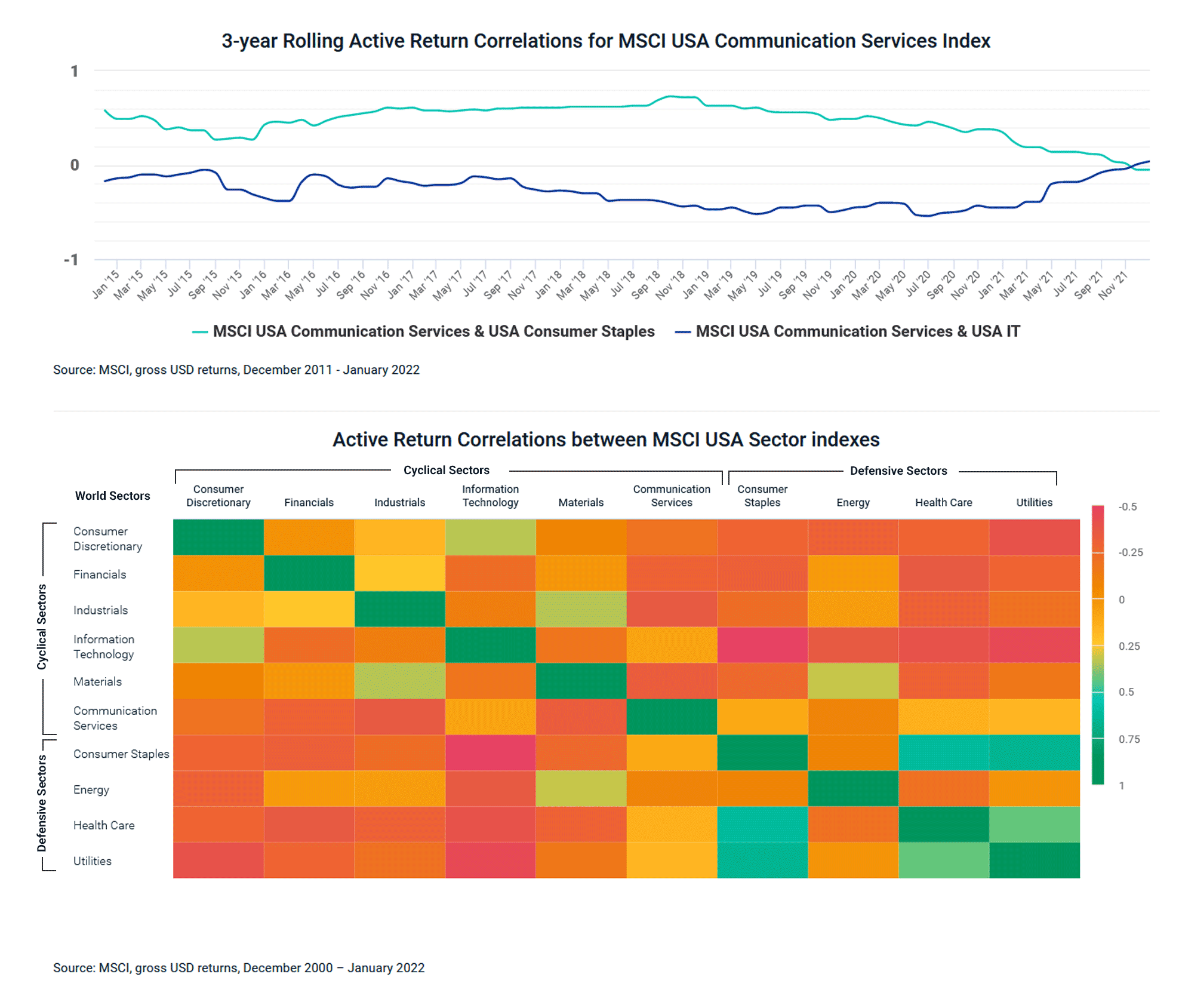
Integrated supply chain management is a process that allows a company to monitor and optimize the performance of its supply chain. The result is a highly responsive and streamlined production network. The more streamlined and responsive your supply chain is, the more efficient your operations will be. Integrated supply chain management is a great way to increase your profits, and decrease waste. This means your products will be more reliable and affordable to make.
Integrated supply chain management can increase the reliability and predictability of your orders. Your production schedule can be more responsive, inventory levels more accurate, and your delivery dates more flexible. Integrated supply chains can also help you manage risk. It can also lower greenhouse gas emissions. This can help you meet your environmental goals.
Drafting a contract with preferred vendors is the first step to integration. These agreements must be tailored to the needs of your company. The agreement should include details about your production schedule, the materials that you require, and the cost involved. Your preferred suppliers must also be able demonstrate how their services will benefit the organization. Lower prices can be achieved by buying more goods and/or services.
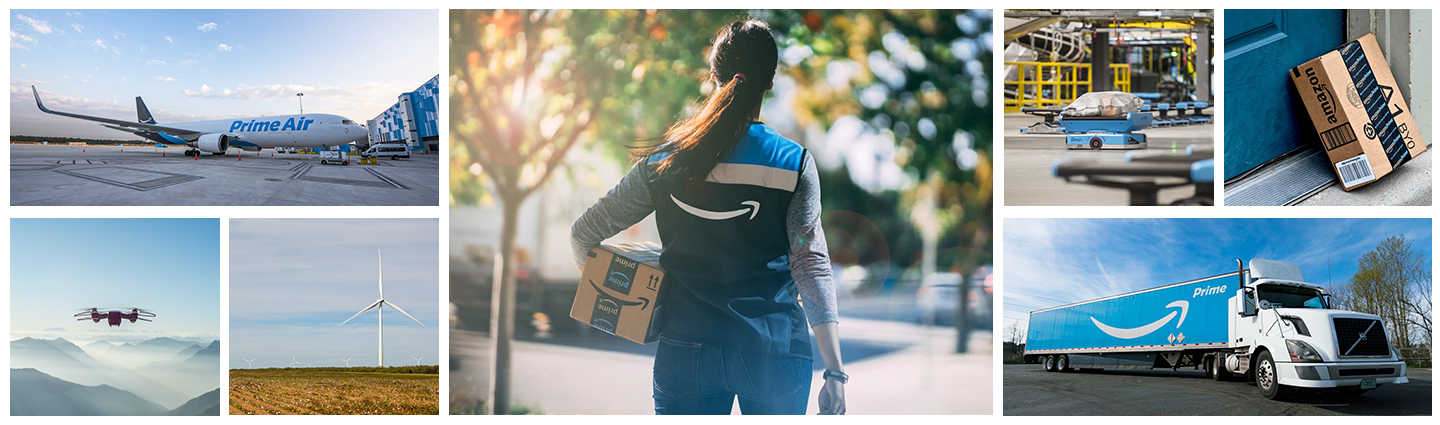
An important part of integrated supply chains management is a good understanding of your connections and how they affect you business. This helps to identify any opportunities for improved performance and avoid mistakes. To meet your needs, you should have an entire end-to-end plan. The plan should be flexible enough to handle any differences in production needs. This will help avoid delays.
Just-in–time distribution is an excellent example of an integral supply chain. This strategy reduces operational costs and increases warehouse space. This strategy can also help with forecasting. Using an integrated supply chain is also important for reducing greenhouse gas emissions. This can be achieved by reducing the use of large fixed assets.
Vertical integration refers to when all the elements are in place for a product. This could be a manufacturer or vendor. This could increase the manufacturer's share of profits. You might also decide to purchase a widget manufacturer or a firm that manufactures widgets. This can help you control your competitor's business, and allow you to set a fair price on widgets.
Container management strategies are another example of an integrated supply chains. This allows for you to monitor inventory levels and make adjustments as necessary to your container pulling strategies. This allows you to modify your production schedule instantly.
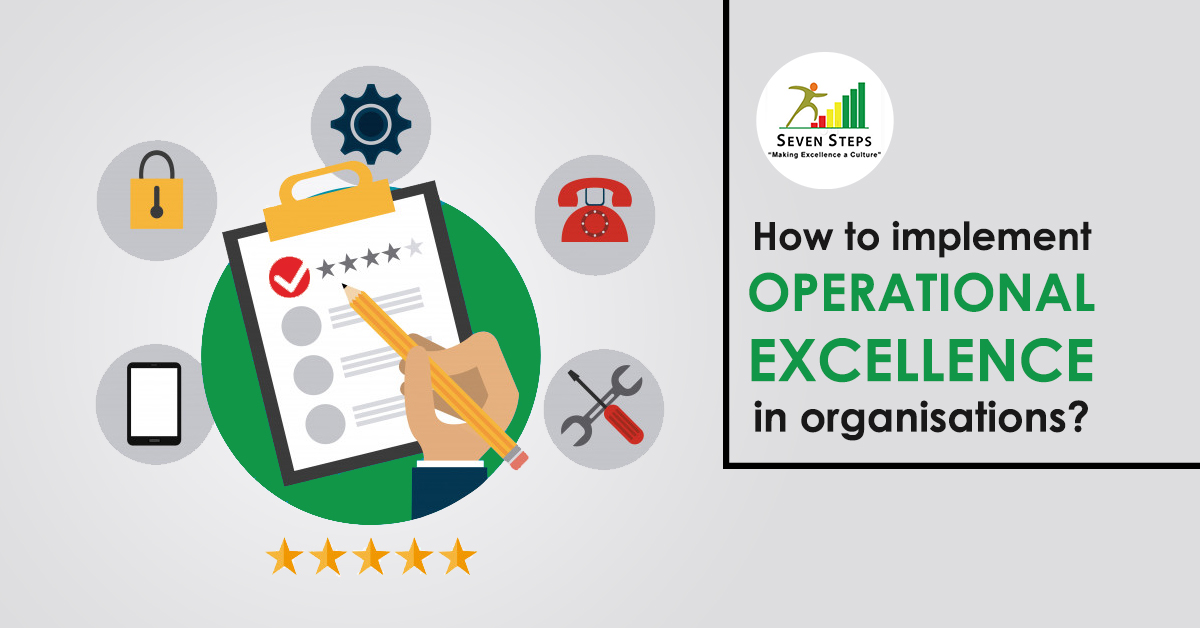
A supply chain management strategy that is clearly defined will make it more effective. Integrated supply chains are designed to optimize performance and offer the best products to your customers. You can use an integrated supply chain to decrease the amount of plastic and other waste produced in the manufacturing process. This can increase your profit margins, and lower your greenhouse gas emissions.
FAQ
What are the differences between these four types?
Manufacturing is the process of transforming raw materials into useful products using machines and processes. It can involve many activities like designing, manufacturing, testing packaging, shipping, selling and servicing.
How can manufacturing efficiency improved?
First, we need to identify which factors are most critical in affecting production times. We then need to figure out how to improve these variables. You can start by identifying the most important factors that impact production time. Once you identify them, look for solutions.
What are the responsibilities for a manufacturing manager
A manufacturing manager must make sure that all manufacturing processes run smoothly and effectively. They should also be aware and responsive to any company problems.
They should also be able communicate with other departments, such as sales or marketing.
They should also be knowledgeable about the latest trends in the industry so they can use this information for productivity and efficiency improvements.
What are the requirements to start a logistics business?
A successful logistics business requires a lot more than just knowledge. You must have good communication skills to interact effectively with your clients and suppliers. You need to understand how to analyze data and draw conclusions from it. You need to be able work under pressure and manage stressful situations. You need to be innovative and creative to come up with new ways to increase efficiency. You must be a strong leader to motivate others and direct them to achieve organizational goals.
You should also be organized and efficient to meet tight deadlines.
Statistics
- You can multiply the result by 100 to get the total percent of monthly overhead. (investopedia.com)
- It's estimated that 10.8% of the U.S. GDP in 2020 was contributed to manufacturing. (investopedia.com)
- [54][55] These are the top 50 countries by the total value of manufacturing output in US dollars for its noted year according to World Bank.[56] (en.wikipedia.org)
- (2:04) MTO is a production technique wherein products are customized according to customer specifications, and production only starts after an order is received. (oracle.com)
- Many factories witnessed a 30% increase in output due to the shift to electric motors. (en.wikipedia.org)
External Links
How To
How to Use lean manufacturing in the Production of Goods
Lean manufacturing is an approach to management that aims for efficiency and waste reduction. It was created in Japan by Taiichi Ohno during the 1970s and 80s. He received the Toyota Production System award (TPS), from Kanji Toyoda, founder of TPS. Michael L. Watkins published the "The Machine That Changed the World", the first book about lean manufacturing. It was published in 1990.
Lean manufacturing is often described as a set if principles that help improve the quality and speed of products and services. It emphasizes the elimination of defects and waste throughout the value stream. Lean manufacturing can be described as just-in–time (JIT), total productive maintenance, zero defect (TPM), or even 5S. Lean manufacturing eliminates non-value-added tasks like inspection, rework, waiting.
In addition to improving product quality and reducing costs, lean manufacturing helps companies achieve their goals faster and reduces employee turnover. Lean manufacturing is a great way to manage the entire value chain including customers, suppliers, distributors and retailers as well as employees. Lean manufacturing practices are widespread in many industries. Toyota's philosophy has been a key driver of success in many industries, including automobiles and electronics.
Five principles are the basis of lean manufacturing:
-
Define Value: Identify the social value of your business and what sets you apart.
-
Reduce Waste - Remove any activity which doesn't add value to your supply chain.
-
Create Flow – Ensure that work flows smoothly throughout the process.
-
Standardize and Simplify – Make processes as consistent, repeatable, and as simple as possible.
-
Develop Relationships: Establish personal relationships both with internal and external stakeholders.
Lean manufacturing isn’t new, but it has seen a renewed interest since 2008 due to the global financial crisis. Many businesses are now using lean manufacturing to improve their competitiveness. In fact, some economists believe that lean manufacturing will be an important factor in economic recovery.
Lean manufacturing has many benefits in the automotive sector. These include improved customer satisfaction, reduced inventory levels, lower operating costs, increased productivity, and better overall safety.
Lean manufacturing can be applied to almost every aspect of an organization. It is especially useful for the production aspect of an organization, as it ensures that every step in the value chain is efficient and effective.
There are three main types:
-
Just-in Time Manufacturing, (JIT): This kind of lean manufacturing is also commonly known as "pull-systems." JIT stands for a system where components are assembled on the spot rather than being made in advance. This approach is designed to reduce lead times and increase the availability of components. It also reduces inventory.
-
Zero Defects Manufacturing: ZDM ensures that no defective units leave the manufacturing plant. Repairing a part that is damaged during assembly should be done, not scrapping. This is true even for finished products that only require minor repairs prior to shipping.
-
Continuous Improvement: Continuous Improvement aims to improve efficiency by continually identifying problems and making adjustments to eliminate or minimize waste. It involves continuous improvement of processes, people, and tools.