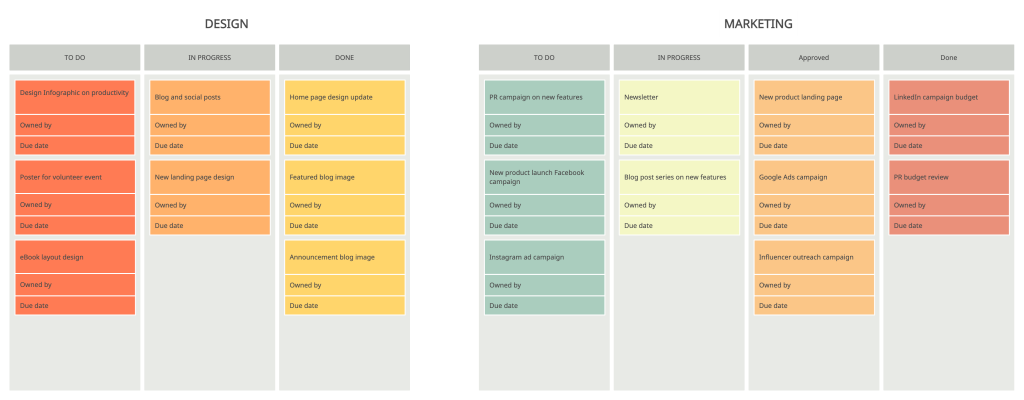
Lean manufacturing allows for a more efficient management system that helps reduce waste. It's based on the principles of Henry Ford and KiichiroToyoda who were the presidents of Toyota Motor Corporation before World War II. Manufacturing is not only an assembly line, but a system. Lean manufacturing considers it to be a whole system. Five key principles of lean manufacturing are: reduce waste, streamline processes, create knowledge and optimize the whole.
First, identify what isn't adding value. This can be done using qualitative or quantitative techniques. This can be done by looking at the price customers pay for your products. If you find that the price is higher than the value you are delivering, you have a problem.
One way to determine the amount of waste in a process is to conduct a kaizen event. This involves everyone in the organization working together to solve problems on an incremental basis. Kaizen events may be used either alone or in conjunction to other lean tools.
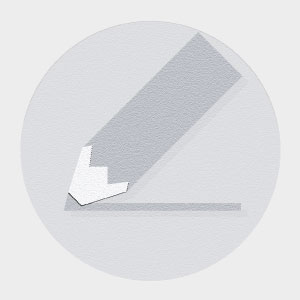
Value stream mapping, another method of identifying waste in production facilities, is also an option. VSM is a way for manufacturers to see the production steps and determine which are the most time-consuming.
Waste areas include inventory, waiting, overproduction, motion, and defects. These areas can be identified and improved by a lean team. They may be in the supply chain, in a production area, or throughout the whole process.
Once the waste has been identified, you can start implementing strategies to eliminate it. These include developing cross-functional teams, flattening your workload, and training your employees to be multi-skilled. Depending on your business, it might be necessary to implement technologies such as cellular or just-intime manufacturing. Other lean tools, such as total production maintenance or kanban management, can be used.
The system can also include standardized containers, which allow workers and other personnel to easily know exact quantities without counting. The standardized containers also make it easier to detect if food or other materials are mixed in the products. Safety mats can also be placed near machine areas to trigger a stoppage if a person steps on them.
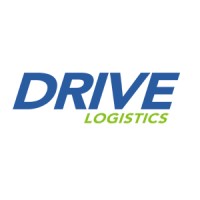
You will need to have a strong organizational culture, as with all lean initiatives. A strong organizational culture will include a clear understanding and communication skills as well as a long-term vision. Your company's success depends on creating a system of continuous improvement.
You can use value stream mapping to help you decide on a new machine. You can create an inventory that includes the future condition of your products, raw materials, and customer needs. This information can help you predict when equipment and supplies will be required. Similarly, you can create a scheduling system to ensure you can fulfill orders on time.
You can make your company more efficient and help you achieve your objectives by using the five core principles of lean manufacture. Find out more information about lean manufacturing techniques and the resources that are available at different websites.
FAQ
What are the four types in manufacturing?
Manufacturing refers the process of turning raw materials into useful products with machines and processes. It can involve many activities like designing, manufacturing, testing packaging, shipping, selling and servicing.
How does manufacturing avoid bottlenecks in production?
To avoid production bottlenecks, ensure that all processes run smoothly from the moment you receive your order to the time the product ships.
This includes both quality control and capacity planning.
Continuous improvement techniques such Six Sigma are the best method to accomplish this.
Six Sigma management is a system that improves quality and reduces waste within your organization.
It's all about eliminating variation and creating consistency in work.
What are the 7 Rs of logistics management?
The acronym 7Rs of Logistics refers to the seven core principles of logistics management. It was developed and published by the International Association of Business Logisticians in 2004 as part of the "Seven Principles of Logistics Management".
The acronym is composed of the following letters.
-
Responsible - ensure that all actions taken are within legal requirements and are not harmful to others.
-
Reliable – have faith in your ability and capability to keep promises.
-
Reasonable - make sure you use your resources well and don't waste them.
-
Realistic – Consider all aspects, including cost-effectiveness as well as environmental impact.
-
Respectful – Treat others fairly and equitably.
-
Responsive - Look for ways to save time and increase productivity.
-
Recognizable: Provide customers with value-added service
What does manufacturing mean?
Manufacturing Industries are those businesses that make products for sale. The people who buy these products are called consumers. These companies use a variety processes such as distribution, retailing and management to accomplish their purpose. These companies produce goods using raw materials and other equipment. This includes all types manufactured goods such as clothing, building materials, furniture, electronics, tools and machinery.
What's the difference between Production Planning & Scheduling?
Production Planning (PP), or production planning, is the process by which you determine what products are needed at any given time. Forecasting demand is one way to do this.
Scheduling involves the assignment of dates and times to tasks in order to complete them within the timeframe.
Can we automate some parts of manufacturing?
Yes! Yes. The Egyptians invented the wheel thousands of years ago. Today, robots assist in the assembly of lines.
There are many uses of robotics today in manufacturing. These include:
-
Line robots
-
Robot welding
-
Robot painting
-
Robotics inspection
-
Robots create products
Automation can be applied to manufacturing in many other ways. 3D printing makes it possible to produce custom products in a matter of days or weeks.
Statistics
- You can multiply the result by 100 to get the total percent of monthly overhead. (investopedia.com)
- [54][55] These are the top 50 countries by the total value of manufacturing output in US dollars for its noted year according to World Bank.[56] (en.wikipedia.org)
- In the United States, for example, manufacturing makes up 15% of the economic output. (twi-global.com)
- (2:04) MTO is a production technique wherein products are customized according to customer specifications, and production only starts after an order is received. (oracle.com)
- Many factories witnessed a 30% increase in output due to the shift to electric motors. (en.wikipedia.org)
External Links
How To
How to Use Lean Manufacturing for the Production of Goods
Lean manufacturing is a management system that aims at increasing efficiency and reducing waste. It was developed by Taiichi Okono in Japan, during the 1970s & 1980s. TPS founder Kanji Takoda awarded him the Toyota Production System Award (TPS). Michael L. Watkins published the book "The Machine That Changed the World", which was the first to be published about lean manufacturing.
Lean manufacturing refers to a set of principles that improve the quality, speed and costs of products and services. It emphasizes the elimination of defects and waste throughout the value stream. Lean manufacturing is called just-in-time (JIT), zero defect, total productive maintenance (TPM), or 5S. Lean manufacturing eliminates non-value-added tasks like inspection, rework, waiting.
Lean manufacturing is a way for companies to achieve their goals faster, improve product quality, and lower costs. Lean manufacturing is considered one of the most effective ways to manage the entire value chain, including suppliers, customers, distributors, retailers, and employees. Many industries worldwide use lean manufacturing. Toyota's philosophy, for example, is what has enabled it to be successful in electronics, automobiles, medical devices, healthcare and chemical engineering as well as paper and food.
Five fundamental principles underlie lean manufacturing.
-
Define Value - Identify the value your business adds to society and what makes you different from competitors.
-
Reduce Waste - Remove any activity which doesn't add value to your supply chain.
-
Create Flow - Make sure work runs smoothly without interruptions.
-
Standardize and Simplify – Make processes as consistent, repeatable, and as simple as possible.
-
Build Relationships - Establish personal relationships with both internal and external stakeholders.
Although lean manufacturing isn't a new concept in business, it has gained popularity due to renewed interest in the economy after the 2008 global financial crisis. Many businesses have adopted lean manufacturing techniques to help them become more competitive. Many economists believe lean manufacturing will play a major role in economic recovery.
Lean manufacturing, which has many benefits, is now a standard practice in the automotive industry. These benefits include increased customer satisfaction, reduced inventory levels and lower operating costs.
It can be applied to any aspect of an organisation. It is especially useful for the production aspect of an organization, as it ensures that every step in the value chain is efficient and effective.
There are three types principally of lean manufacturing:
-
Just-in-Time Manufacturing: Also known as "pull systems", this type of lean manufacturing uses just-in-time manufacturing (JIT). JIT refers to a system in which components are assembled at the point of use instead of being produced ahead of time. This approach is designed to reduce lead times and increase the availability of components. It also reduces inventory.
-
Zero Defects Manufacturing: ZDM ensures that no defective units leave the manufacturing plant. You should repair any part that needs to be repaired during an assembly line. This applies to finished products, which may need minor repairs before they are shipped.
-
Continuous Improvement (CI), also known as Continuous Improvement, aims at improving the efficiency of operations through continuous identification and improvement to minimize or eliminate waste. Continuous improvement refers to continuous improvement of processes as well people and tools.