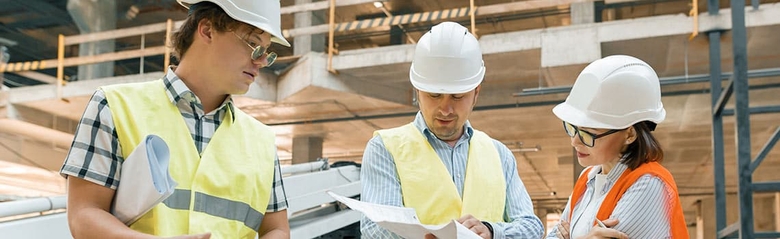
The salary for an engineer varies greatly depending on where you live. Washington is the top-paying state in the United States. New York and California are close behind. When moving to a new country, it is important that you consider the cost per capita. As an example, a salary of $96,640 may not be sufficient to pay all your living expenses. It is crucial to assess your cost of living before applying for a new job.
An average salary for electrical engineers is $96,640
The average annual salary for an electrician is $96,640 according to the U.S. Bureau of Labor Statistics. This number can vary depending on where you live. There are many industry sectors that can have very different salaries. Electrical engineers make the most in retail trade. Education services makes the least. However, there are some important factors to consider when determining the average salary for an electrical engineer. Below is a breakdown of the salary levels for different types of electrical engineers.
They are responsible for the design and development of electrical equipment. They are responsible for overseeing the manufacture and installation of these devices. This statistic includes salaries for all types of electrical engineers, but does not include Computer Hardware Engineers, who make computers. According to the Bureau of Labor Statistics in 2026, these professionals are expected to grow by 7 percent. The majority of electrical engineers will work in an office environment, but they may also travel for work on the field.
Biomedical engineers earn a median salary of $89,130
Biomedical engineer combine their engineering knowledge with knowledge about the human body to design medical devices. Their knowledge of biomechanics allows them to understand the interaction between different medical products and the body. This knowledge can help create artificial organs and medical devices, as well diagnostic tools.
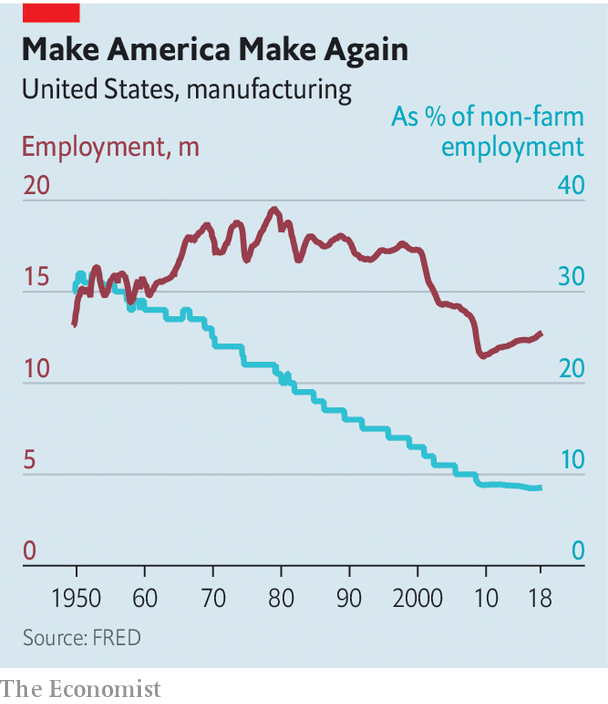
Biomedical engineers must be able to communicate well and not only apply engineering principles to medical procedures. They are expected to communicate with other health care professionals, present research results and publish scientific papers. Advanced mathematics is also required.
A mechanical engineer earns a median salary $91,352
A mechanical engineer's salary is determined by multiple factors. For example, salaries vary by location and industry. According to the 2017 Salary Survey of ASME members, those living in the Northeast and the Southwest earn more than others. The Midwest earns the least.
The average salary for mechanical engineers ranges from $91,352 - $137,028. The average salary of mechanical engineers is $91,352, while the top six percent earn more than this. Those earning less than two years of experience earn an average of $72,400. But, those with more experience than two years can earn up to $150,000.
The median salary for agricultural engineers is $89,130
In order to solve problems in relation to power supply and environment, agricultural engineers are employed in agricultural settings. They also oversee construction and are involved in design. This job requires advanced engineering abilities and knowledge of science and math. They earn comparable salaries to similar occupations in the United States. They typically make less than naval architects or locomotive engineers. The outlook for agricultural engineers' jobs is good. Employment will rise 7.4% between 2016 and 2026.
The average American agricultural engineer salary is $89,130. However, the highest-paid earn more than $110,000. The median salary for agricultural engineers varies by location. Santa Clara (San Francisco) and Bolinas are among the top-paying cities for agricultural engineers.
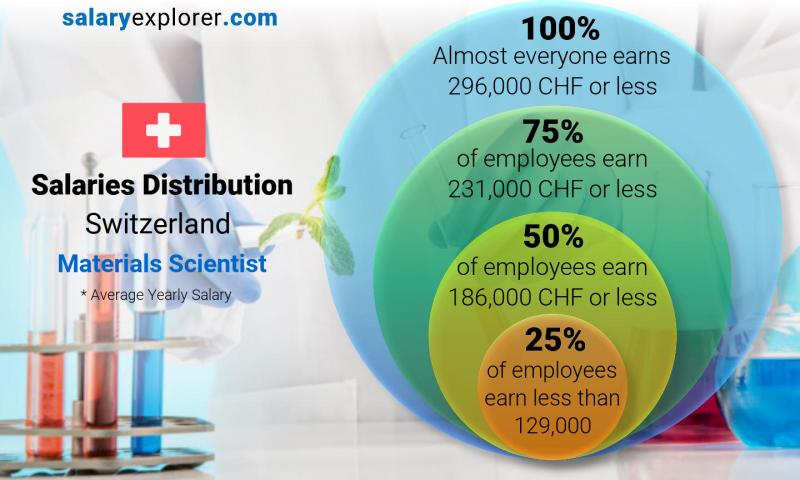
A median salary for an environmental engineer in the United States is $87620
Environmental engineers work to protect the environment from damage by developing and implementing solutions to minimize negative effects. They may be involved in various fields and work with other engineers, including urban planners or construction managers. Their training includes biology and chemical, as well data analysis and critical think. They help organizations comply with regulations and also have a good understanding of environmental law.
Environmental engineers must be flexible and adaptable to new technologies and best practices. They should also be analytically skilled and able to work in a team. They must also be good problem-solvers and have a positive attitude.
FAQ
Can certain manufacturing steps be automated?
Yes! Yes. The Egyptians created the wheel thousands years ago. Robots are now used to assist us in assembly lines.
Actually, robotics can be used in manufacturing for many purposes. These include:
-
Assembly line robots
-
Robot welding
-
Robot painting
-
Robotics inspection
-
Robots create products
There are many other examples of how manufacturing could benefit from automation. For example, 3D printing allows us to make custom products without having to wait for weeks or months to get them manufactured.
How can manufacturing excess production be decreased?
It is essential to find better ways to manage inventory to reduce overproduction. This would reduce the time needed to manage inventory. By doing this, we could free up resources for other productive tasks.
A Kanban system is one way to achieve this. A Kanban board is a visual display used to track work in progress. Kanban systems allow work items to move through different states until they reach their final destination. Each state represents a different priority level.
To illustrate, work can move from one stage or another when it is complete enough for it to be moved to a new stage. However, if a task is still at the beginning stages, it will remain so until it reaches the end of the process.
This helps to keep work moving forward while ensuring that no work is left behind. A Kanban board allows managers to monitor how much work is being completed at any given moment. This information allows them to adjust their workflow based on real-time data.
Lean manufacturing, another method to control inventory levels, is also an option. Lean manufacturing emphasizes eliminating waste in all phases of production. Anything that does nothing to add value to a product is waste. Here are some examples of common types.
-
Overproduction
-
Inventory
-
Unnecessary packaging
-
Material surplus
These ideas will help manufacturers increase efficiency and lower costs.
How can manufacturing avoid production bottlenecks
The key to avoiding bottlenecks in production is to keep all processes running smoothly throughout the entire production cycle, from the time you receive an order until the time when the product ships.
This includes planning for capacity requirements as well as quality control measures.
Continuous improvement techniques like Six Sigma are the best way to achieve this.
Six Sigma can be used to improve the quality and decrease waste in all areas of your company.
It focuses on eliminating variation and creating consistency in your work.
What does it take to run a logistics business?
To be a successful businessman in logistics, you will need many skills and knowledge. You must have good communication skills to interact effectively with your clients and suppliers. You will need to know how to interpret data and draw conclusions. You will need to be able handle pressure well and work in stressful situations. In order to innovate and create new ways to improve efficiency, creativity is essential. You need to have strong leadership qualities to motivate team members and direct them towards achieving organizational goals.
To meet tight deadlines, you must also be efficient and organized.
What is the difference between Production Planning and Scheduling?
Production Planning (PP) is the process of determining what needs to be produced at any given point in time. This is accomplished by forecasting the demand and identifying production resources.
Scheduling refers to the process of allocating specific dates to tasks in order that they can be completed within a specified timeframe.
How important is automation in manufacturing?
Automation is important not only for manufacturers but also for service providers. It enables them to provide services faster and more efficiently. It also helps to reduce costs and improve productivity.
Statistics
- You can multiply the result by 100 to get the total percent of monthly overhead. (investopedia.com)
- In the United States, for example, manufacturing makes up 15% of the economic output. (twi-global.com)
- Job #1 is delivering the ordered product according to specifications: color, size, brand, and quantity. (netsuite.com)
- It's estimated that 10.8% of the U.S. GDP in 2020 was contributed to manufacturing. (investopedia.com)
- Many factories witnessed a 30% increase in output due to the shift to electric motors. (en.wikipedia.org)
External Links
How To
How to Use 5S to Increase Productivity in Manufacturing
5S stands in for "Sort", the "Set In Order", "Standardize", or "Separate". Toyota Motor Corporation created the 5S methodology in 1954. It helps companies achieve higher levels of efficiency by improving their work environment.
This method aims to standardize production processes so that they are repeatable, measurable and predictable. This means that daily tasks such as cleaning and sorting, storage, packing, labeling, and packaging are possible. This knowledge allows workers to be more efficient in their work because they are aware of what to expect.
Five steps are required to implement 5S: Sort, Set In Order, Standardize. Separate. Each step is a different action that leads to greater efficiency. If you sort items, it makes them easier to find later. When items are ordered, they are put together. Once you have separated your inventory into groups and organized them, you will store these groups in easily accessible containers. Finally, label all containers correctly.
This requires employees to critically evaluate how they work. Employees need to be able understand their motivations and discover alternative ways to do them. In order to use the 5S system effectively, they must be able to learn new skills.
The 5S method not only increases efficiency but also boosts morale and teamwork. They are more motivated to achieve higher efficiency levels as they start to see improvement.