
A bill of materials (BOM), is an important part of manufacturing. It contains all necessary items for manufacturing end products. This document is vital for all companies, regardless of whether they sell directly to customers or through retail channels. It assists companies in keeping track of their stock, avoiding waste and reducing production errors. It also helps companies avoid stockouts.
A bill or materials is a detailed, tabular document that lists each component of an assembly. It also lists the parts required to build the assembly. Parts and subassemblies can be bought from outside suppliers or made internally. It is necessary to identify each part with a unique serial number. This allows the assembly crew to correctly identify and gather the material they require. It is also important to note any special requirements on the bill of materials. These special requirements could lead to delays or even errors during the manufacturing process.
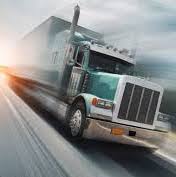
Bills of materials are important to companies because they provide an accurate way to track components and raw materials. They allow for greater production. They can prevent stockouts and allow companies to forecast their sales. These documents can also be used to help companies track materials used in production and prevent over-ordering.
A bill of materials is a document that lists the materials, components, and subassemblies needed to produce a product. The bill also includes the labor and time needed to complete each stage. Importantly, the bill of material must also include the name and contact information for the suppliers for each component. It may also contain other critical details for the production. It is important you remember that the bill may differ from one company for another.
Bills of materials are used in manufacturing processes to make sure that the finished product functions properly. They are also used by companies to plan and order raw materials, reduce waste and minimize production errors. The bill of materials helps manufacturers to identify the raw materials needed to make a product and determine the proper amounts for each piece. Important to remember that the bill of materials is a roadmap for the finished product. It can be challenging to create a bill-of-materials, especially for products with many parts. However, specialized software solutions are available for creating a bill of materials.
A bill to materials is created to meet project specifications and requirements. It can be used as a blueprint for the finished product or as a communication card between manufacturing and supply chain partners. This document helps companies to avoid over-ordering of materials and to keep track of all the components used in the production process.
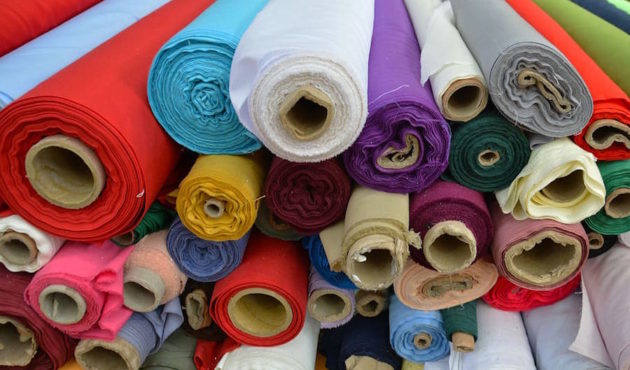
A bill of materials is essential for any company selling through retail channels or directly to customers. Bills of material allow for greater productivity and profits. They are a great way for companies to cut down on waste, prevent stockouts and make production more efficient.
FAQ
What skills should a production planner have?
A production planner must be organized, flexible, and able multitask to succeed. You must also be able to communicate effectively with clients and colleagues.
How can manufacturing prevent production bottlenecks?
The key to avoiding bottlenecks in production is to keep all processes running smoothly throughout the entire production cycle, from the time you receive an order until the time when the product ships.
This includes planning for both capacity requirements and quality control measures.
The best way to do this is to use continuous improvement techniques such as Six Sigma.
Six Sigma Management System is a method to increase quality and reduce waste throughout your organization.
It seeks to eliminate variation and create consistency in your work.
How can excess manufacturing production be reduced?
It is essential to find better ways to manage inventory to reduce overproduction. This would reduce time spent on activities such as purchasing, stocking, and maintaining excess stock. By doing this, we could free up resources for other productive tasks.
This can be done by using a Kanban system. A Kanban board is a visual display used to track work in progress. Work items are moved through various states to reach their destination in a Kanban system. Each state represents an individual priority level.
When work is completed, it can be transferred to the next stage. However, if a task is still at the beginning stages, it will remain so until it reaches the end of the process.
This allows for work to continue moving forward, while also ensuring that there is no work left behind. A Kanban board allows managers to monitor how much work is being completed at any given moment. This allows them the ability to adjust their workflow using real-time data.
Lean manufacturing, another method to control inventory levels, is also an option. Lean manufacturing seeks to eliminate waste from every step of the production cycle. Anything that does nothing to add value to a product is waste. These are some of the most common types.
-
Overproduction
-
Inventory
-
Unnecessary packaging
-
Exceed materials
These ideas will help manufacturers increase efficiency and lower costs.
What are the 7 Rs of logistics?
The acronym 7R's of Logistic is an acronym that stands for seven fundamental principles of logistics management. It was developed by International Association of Business Logisticians (IABL), and published as part of their "Seven Principles of Logistics Management Series" in 2004.
The acronym is composed of the following letters.
-
Responsible - ensure that all actions taken are within legal requirements and are not harmful to others.
-
Reliable - Have confidence in your ability to fulfill all of your commitments.
-
Reasonable - make sure you use your resources well and don't waste them.
-
Realistic - consider all aspects of operations, including cost-effectiveness and environmental impact.
-
Respectful: Treat others with fairness and equity
-
Resourceful - look for opportunities to save money and increase productivity.
-
Recognizable - provide customers with value-added services.
What is the job of a manufacturer manager?
The manufacturing manager should ensure that every manufacturing process is efficient and effective. They should be alert for any potential problems in the company and react accordingly.
They should also know how to communicate with other departments such as sales and marketing.
They should be informed about industry trends and be able make use of this information to improve their productivity and efficiency.
Can certain manufacturing steps be automated?
Yes! Since ancient times, automation has been in existence. The Egyptians created the wheel thousands years ago. Robots are now used to assist us in assembly lines.
There are many applications for robotics in manufacturing today. These include:
-
Automation line robots
-
Robot welding
-
Robot painting
-
Robotics inspection
-
Robots that make products
Automation can be applied to manufacturing in many other ways. 3D printing, for example, allows us to create custom products without waiting for them to be made.
What are the requirements to start a logistics business?
You need to have a lot of knowledge and skills to manage a successful logistic business. Good communication skills are essential to effectively communicate with your suppliers and clients. You must be able analyze data and draw out conclusions. You must be able and able to handle stress situations and work under pressure. To increase efficiency and creativity, you need to be creative. You need to have strong leadership qualities to motivate team members and direct them towards achieving organizational goals.
To meet tight deadlines, you must also be efficient and organized.
Statistics
- According to the United Nations Industrial Development Organization (UNIDO), China is the top manufacturer worldwide by 2019 output, producing 28.7% of the total global manufacturing output, followed by the United States, Japan, Germany, and India.[52][53] (en.wikipedia.org)
- In 2021, an estimated 12.1 million Americans work in the manufacturing sector.6 (investopedia.com)
- Job #1 is delivering the ordered product according to specifications: color, size, brand, and quantity. (netsuite.com)
- [54][55] These are the top 50 countries by the total value of manufacturing output in US dollars for its noted year according to World Bank.[56] (en.wikipedia.org)
- It's estimated that 10.8% of the U.S. GDP in 2020 was contributed to manufacturing. (investopedia.com)
External Links
How To
How to Use the 5S to Increase Productivity In Manufacturing
5S stands in for "Sort", the "Set In Order", "Standardize", or "Separate". Toyota Motor Corporation developed the 5S method in 1954. This methodology helps companies improve their work environment to increase efficiency.
The idea behind standardizing production processes is to make them repeatable and measurable. This means that every day tasks such cleaning, sorting/storing, packing, and labeling can be performed. Because workers know what they can expect, this helps them perform their jobs more efficiently.
There are five steps that you need to follow in order to implement 5S. Each step involves a different action which leads to increased efficiency. If you sort items, it makes them easier to find later. When items are ordered, they are put together. Then, after you separate your inventory into groups, you store those groups in containers that are easy to access. Labeling your containers will ensure that everything is correctly labeled.
This process requires employees to think critically about how they do their job. Employees must understand why they do certain tasks and decide if there's another way to accomplish them without relying on the old ways of doing things. They will need to develop new skills and techniques in order for the 5S system to be implemented.
The 5S method not only increases efficiency but also boosts morale and teamwork. They are more motivated to achieve higher efficiency levels as they start to see improvement.