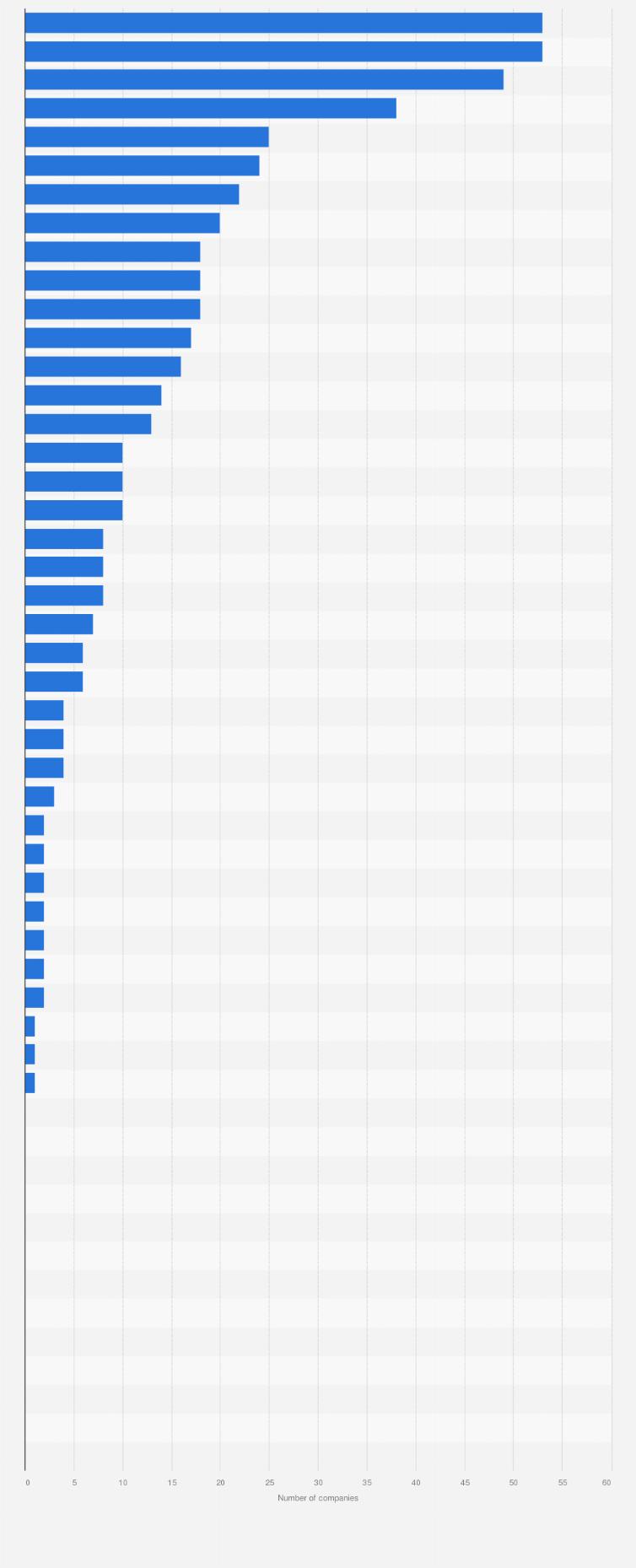
The unemployment rates in Michigan are among the highest in the nation, as well as the Midwest. In order to assist families during economic downturns, Unemployment Insurance was established. However, the system has not been updated in line with today's workforce. Many policies that the state has implemented are not current, particularly in relation to Black and Latinx workers.
Michigan's maximum weekly allowance has been increased only once since 1995. It is also one the six states that provides fewer than 26 weeks of unemployment benefits. In reality, the minimum number of weeks provided is less than 10. A family might find themselves in poverty if they lose their job before the maximum number. Michigan is not doing enough to ensure that all people without work have access to unemployment coverage.
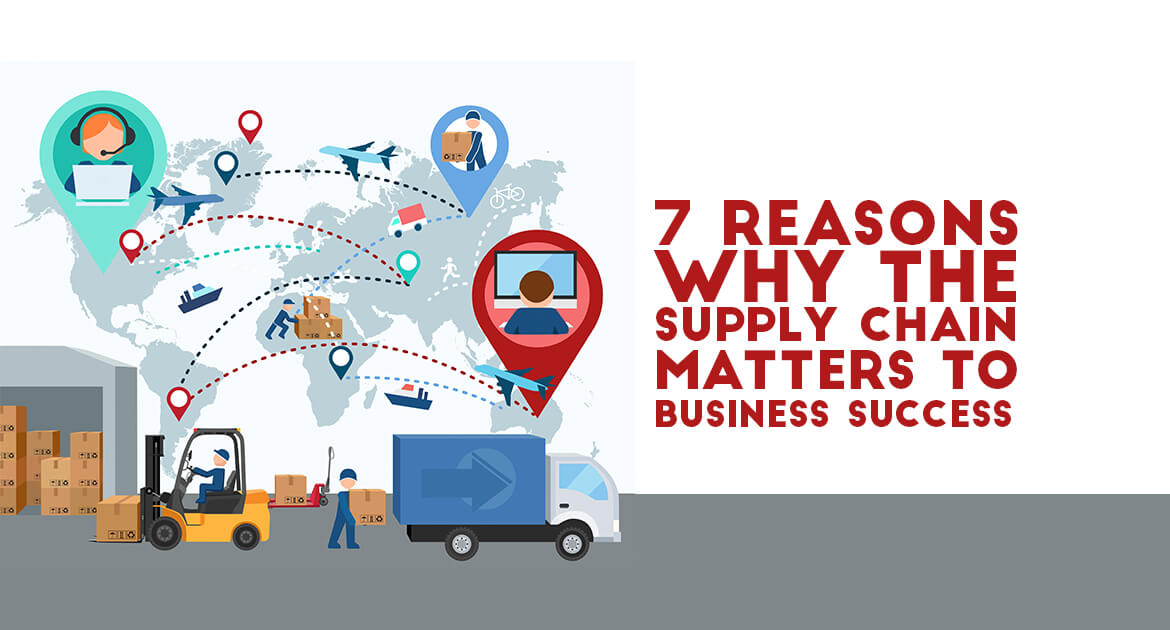
Another example is the minimum wage requirement in Michigan. A worker must make at least $5,667 per weekly to be eligible for UI. This is more than the average wage in other Midwestern states. While this is not a bad thing in and of itself, the fact that the State of Michigan requires a minimum wage of more than a few hundred dollars per week puts it well behind the pack.
According to the Advisory Council's two-thirds rule, Michigan's unemployment benefit should not exceed 50% for a week's average weekly earnings. Instead, the state's maximum benefits are only 34%. Michigan is therefore far behind other states, and should improve its Unemployment insurance game. By contrast, Wisconsin, Iowa, and Pennsylvania provide maximum benefits that are at least 50% of average wages.
The Michigan Legislature should look to improve the state's Unemployment Insurance program. This is an important step in reducing racial disparities while improving the safety net of all workers. The state should also consider expanding the period of eligibility for workers to apply for benefits. A longer base period would be a great way for federal funding to go further in skills training and job search costs. This would also increase the chance that more workers are eligible for the assistance they need.
Although Michigan's unemployment rates are higher than those in other states, they have been decreasing since 2009. The newest figures show that the unemployment rate in the state has decreased to 6.1 percent in January 2021. Since then, it has remained relatively steady. Michigan's unemployment rate was among the worst in the country during the recession. However, with strong investments in the Unemployment insurance system, more workers will find work before the 26-week mark.
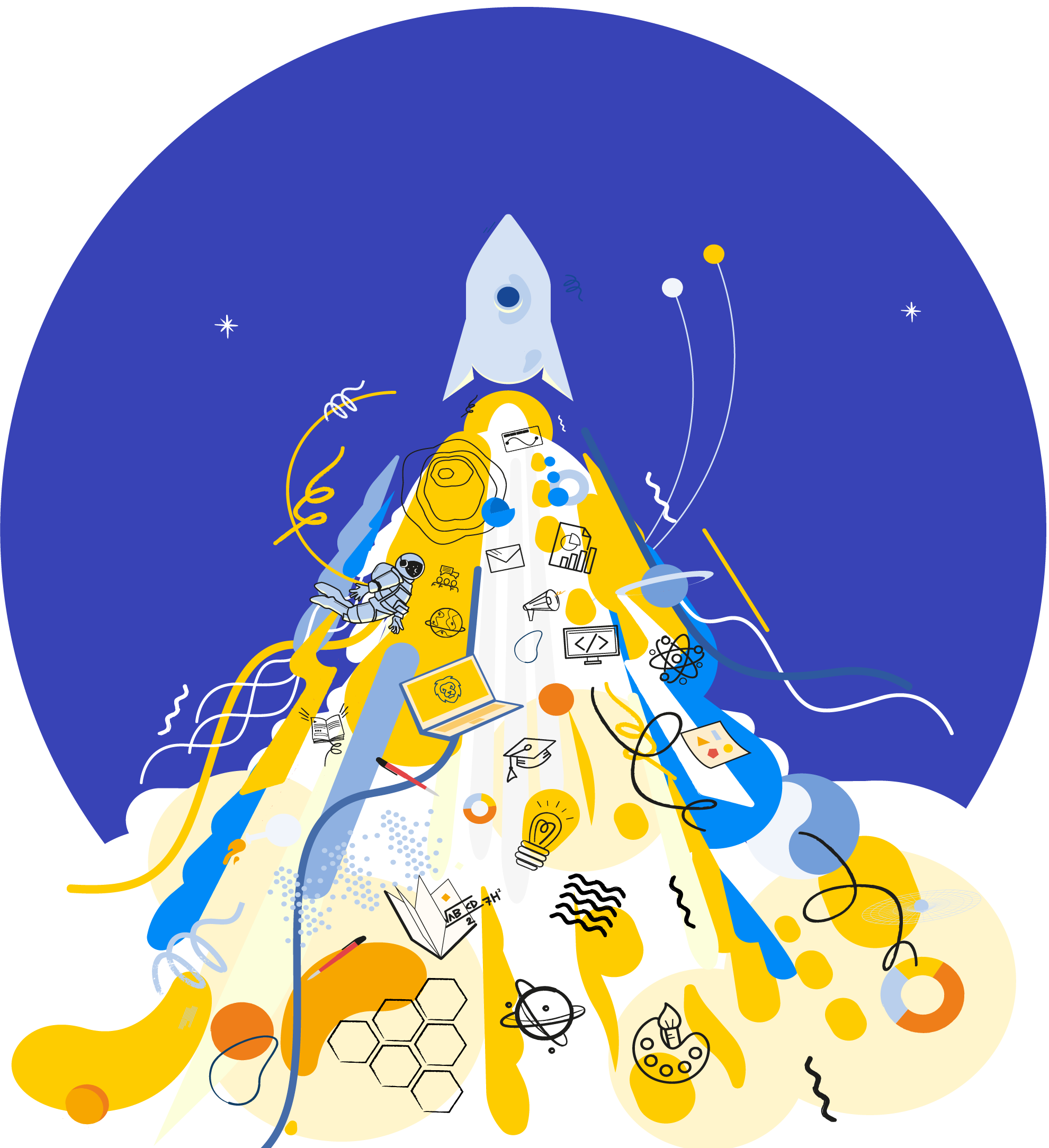
The highest minimum wage in the country for eligibility to receive unemployment benefits is found in the midwest. Michigan's maximum UI-benefit is also the lowest in America.
FAQ
Why automate your warehouse?
Automation has become increasingly important in modern warehousing. The rise of e-commerce has led to increased demand for faster delivery times and more efficient processes.
Warehouses must adapt quickly to meet changing customer needs. To do so, they must invest heavily in technology. Automation warehouses can bring many benefits. Here are some benefits of investing in automation
-
Increases throughput/productivity
-
Reduces errors
-
Increases accuracy
-
Boosts safety
-
Eliminates bottlenecks
-
This allows companies to scale easily
-
It makes workers more efficient
-
This gives you visibility into what happens in the warehouse
-
Enhances customer experience
-
Improves employee satisfaction
-
Minimizes downtime and increases uptime
-
You can be sure that high-quality products will arrive on time
-
Eliminates human error
-
It ensures compliance with regulations
What is the responsibility for a logistics manager
Logistics managers are responsible for ensuring that all goods arrive in perfect condition and on time. This is achieved by using their knowledge and experience with the products of the company. He/she should also ensure enough stock is available to meet demand.
What is the job of a production plan?
Production planners ensure all aspects of the project are delivered within time and budget. They also ensure that the product/service meets the client’s needs.
How is a production manager different from a producer planner?
The primary difference between a producer planner and a manager of a project is that the manager usually plans and organizes the whole project, while a production planner is only involved in the planning stage.
What are the goods of logistics?
Logistics are the activities involved in moving goods from point A to point B.
They encompass all aspects transport, including packaging and loading, transporting, storage, unloading.
Logisticians ensure the product reaches its destination in the most efficient manner. They provide information on demand forecasts as well stock levels, production schedules and availability of raw material.
They can also track shipments in transit and monitor quality standards.
How can manufacturing reduce production bottlenecks?
The key to avoiding bottlenecks in production is to keep all processes running smoothly throughout the entire production cycle, from the time you receive an order until the time when the product ships.
This includes planning to meet capacity requirements and quality control.
Continuous improvement techniques such Six Sigma are the best method to accomplish this.
Six Sigma Management System is a method to increase quality and reduce waste throughout your organization.
It focuses on eliminating variation and creating consistency in your work.
What is the importance of automation in manufacturing?
Not only is automation important for manufacturers, but it's also vital for service providers. They can provide services more quickly and efficiently thanks to automation. It helps them to lower costs by reducing human errors, and improving productivity.
Statistics
- According to the United Nations Industrial Development Organization (UNIDO), China is the top manufacturer worldwide by 2019 output, producing 28.7% of the total global manufacturing output, followed by the United States, Japan, Germany, and India.[52][53] (en.wikipedia.org)
- [54][55] These are the top 50 countries by the total value of manufacturing output in US dollars for its noted year according to World Bank.[56] (en.wikipedia.org)
- You can multiply the result by 100 to get the total percent of monthly overhead. (investopedia.com)
- In the United States, for example, manufacturing makes up 15% of the economic output. (twi-global.com)
- According to a Statista study, U.S. businesses spent $1.63 trillion on logistics in 2019, moving goods from origin to end user through various supply chain network segments. (netsuite.com)
External Links
How To
Six Sigma in Manufacturing:
Six Sigma is defined as "the application of statistical process control (SPC) techniques to achieve continuous improvement." Motorola's Quality Improvement Department developed it at their Tokyo plant in Japan in 1986. Six Sigma is a method to improve quality through standardization and elimination of defects. Many companies have adopted Six Sigma in recent years because they believe that there are no perfect products and services. The main goal of Six Sigma is to reduce variation from the mean value of production. This means that you can take a sample from your product and then compare its performance to the average to find out how often the process differs from the norm. If this deviation is too big, you know something needs fixing.
Understanding the dynamics of variability within your business is the first step in Six Sigma. Once you have a good understanding of the basics, you can identify potential sources of variation. This will allow you to decide if these variations are random and systematic. Random variations are caused when people make mistakes. While systematic variations are caused outside of the process, they can occur. If you make widgets and some of them end up on the assembly line, then those are considered random variations. However, if you notice that every time you assemble a widget, it always falls apart at exactly the same place, then that would be a systematic problem.
After identifying the problem areas, you will need to devise solutions. You might need to change the way you work or completely redesign the process. Test them again once you've implemented the changes. If they fail, you can go back to the drawing board to come up with a different plan.