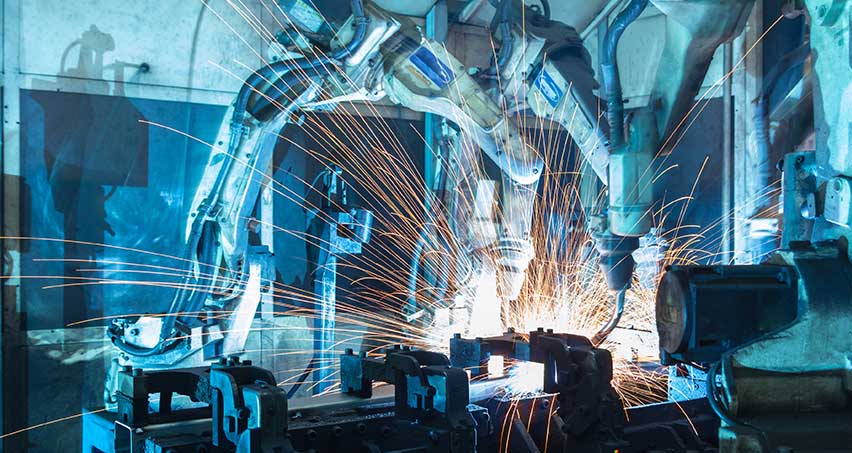
Many factors have contributed to a large chip shortage in recent times. These include transportation issues and manufacturing problems. There have also been many disasters that have caused the closure of chip plants. This has affected consumer devices like gaming consoles, medical devices, and data centres. The Chinese government is making several efforts to encourage semiconductor manufacturing in China. To support chip manufacturers, the government even created an investment fund.
China's chip industry has seen remarkable improvements over the past several years as a result. According to IC Insights's projections, China's chip manufacturing will increase by 19.4% in 2025. However, the industry still has a long way to go before it reaches its former levels. Despite these achievements, the number domestic chip companies remains small. Many of these companies remain independent.
Huawei, Oppo and Midea are some of China's most well-known chip manufacturers. Chinese companies have also been gaining significant market share within the mobile processor space. They are also creating their own chips, which allows them to increase their chip making capabilities. This has helped them become more competitive in this industry.
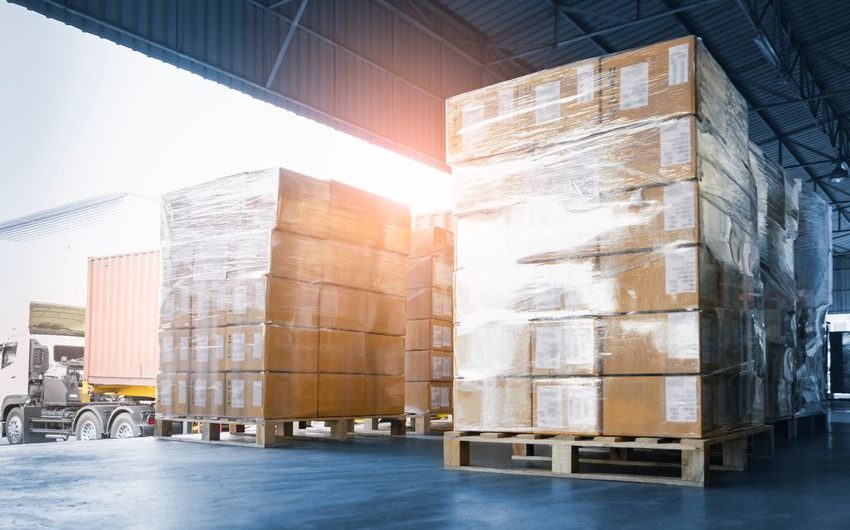
China is fast becoming a global hub for chip manufacturing. But there are still challenges. Chinese companies have limited resources and are not able to mass-produce high end microchips. These chips are used in servers, smartphones, and wearable devices. The country is also not yet able to produce the raw materials necessary for chip manufacturing. These include enriched isotopes, tantalum, and neon. These raw materials can be refined by chemical processes.
The Chinese government also wants to reduce its dependence on imported chips. China will produce 70% of its chips in China by 2025, according to the country. This is likely to take years. China currently has 32 registered chips companies. Many more are still awaiting IPOs. The government is also marketing its industrial policy. It hopes to encourage companies to produce more chips in the country, which is a significant challenge given the limited resources available.
The US semiconductor market is experiencing an unprecedented shortage. In addition, Washington recently passed new rules that restrict the ability of US persons to support chip production.
TSMC, one of the world's largest chipmakers, has not yet made any announcements about a future plant in Europe. It hasn't ruled out the possibility of building an older-generation chip factory there. The company has also partnered to purchase chips with European carmakers. The idea has been resisted by most European auto companies. Adding a European plant would enhance the supply chain. Chips would then have to be shipped back into Asia for further processing. This could make the chip last several years longer.
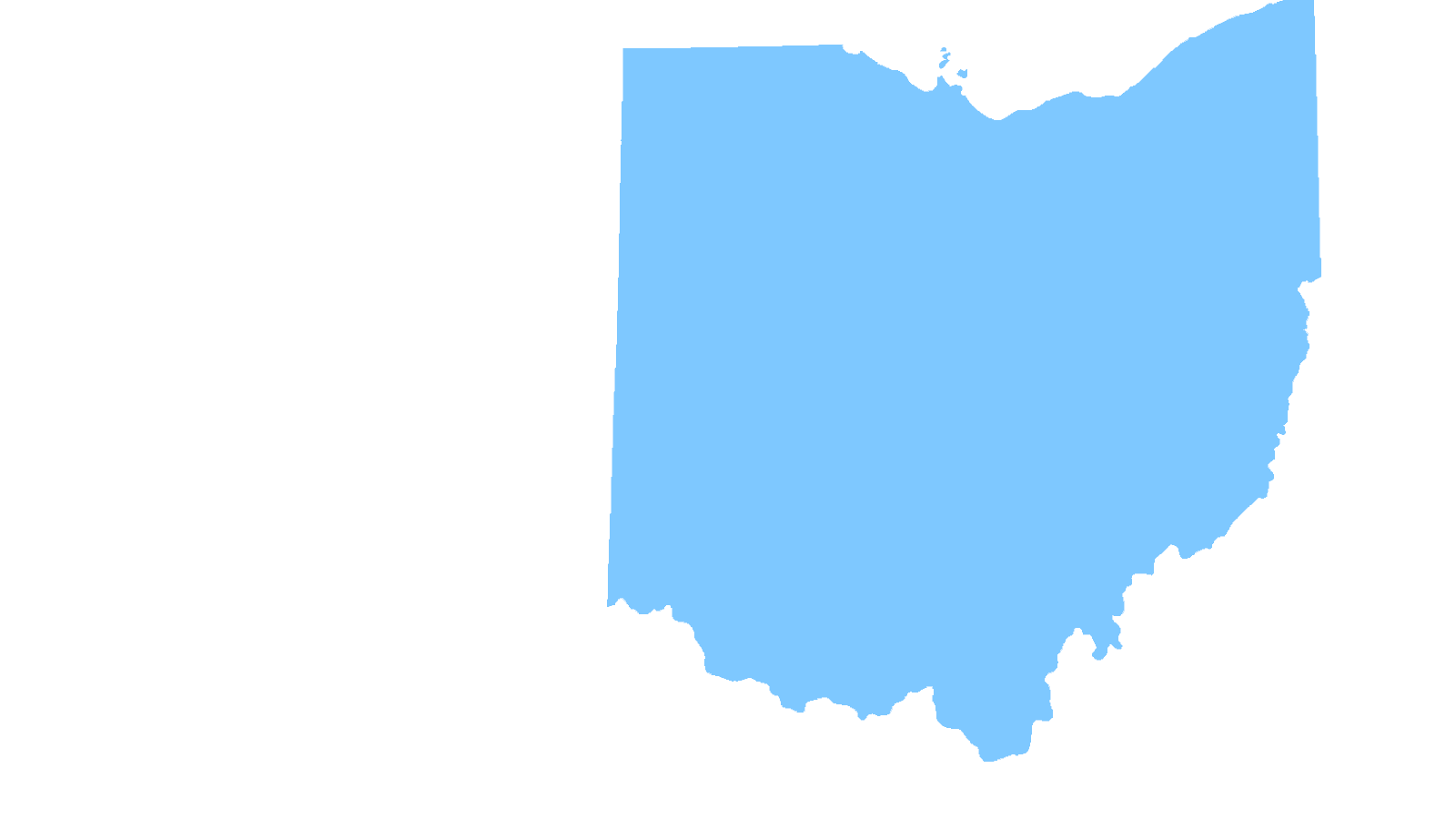
According to a report by the US Commerce Department, the chip shortage will become bad in 2021. This has led to long delays for consumers. The shortage has also had a negative impact on transportation, healthcare, as well as gaming consoles. However, the government's investments in reshoring chip production will help create hundreds of thousands of jobs in the US, and ensure a more resilient chip supply chain.
FAQ
What makes a production planner different from a project manger?
The major difference between a Production Planner and a Project Manager is that a Project Manager is often the person responsible for organizing and planning the entire project. While a Production Planner is involved mainly in the planning stage,
What do you mean by warehouse?
Warehouses and storage facilities are where goods are kept before being sold. It can be an indoor space or an outdoor area. In some cases, it may be a combination of both.
Why is logistics important in manufacturing
Logistics are an integral part any business. They help you achieve great results by helping you manage all aspects of product flow, from raw materials to finished goods.
Logistics play a key role in reducing expenses and increasing efficiency.
What is the difference between manufacturing and logistics
Manufacturing is the act of producing goods from raw materials using machines and processes. Logistics includes all aspects related to supply chain management, such as procurement, distribution planning, inventory control and transportation. Logistics and manufacturing are often referred to as one thing. It encompasses both the creation of products and their delivery to customers.
Statistics
- Job #1 is delivering the ordered product according to specifications: color, size, brand, and quantity. (netsuite.com)
- According to a Statista study, U.S. businesses spent $1.63 trillion on logistics in 2019, moving goods from origin to end user through various supply chain network segments. (netsuite.com)
- In the United States, for example, manufacturing makes up 15% of the economic output. (twi-global.com)
- You can multiply the result by 100 to get the total percent of monthly overhead. (investopedia.com)
- In 2021, an estimated 12.1 million Americans work in the manufacturing sector.6 (investopedia.com)
External Links
How To
How to Use Six Sigma in Manufacturing
Six Sigma refers to "the application and control of statistical processes (SPC) techniques in order to achieve continuous improvement." Motorola's Quality Improvement Department created Six Sigma at their Tokyo plant, Japan in 1986. Six Sigma's basic concept is to improve quality and eliminate defects through standardization. In recent years, many companies have adopted this method because they believe there is no such thing as perfect products or services. Six Sigma aims to reduce variation in the production's mean value. If you take a sample and compare it with the average, you will be able to determine how much of the production process is different from the norm. If it is too large, it means that there are problems.
Understanding the nature of variability in your business is the first step to Six Sigma. Once you have this understanding, you will need to identify sources and causes of variation. You'll also want to determine whether these variations are random or systematic. Random variations happen when people make errors; systematic variations are caused externally. For example, if you're making widgets, and some of them fall off the assembly line, those would be considered random variations. However, if you notice that every time you assemble a widget, it always falls apart at exactly the same place, then that would be a systematic problem.
After identifying the problem areas, you will need to devise solutions. This could mean changing your approach or redesigning the entire process. Once you have implemented the changes, it is important to test them again to ensure they work. If they fail, you can go back to the drawing board to come up with a different plan.