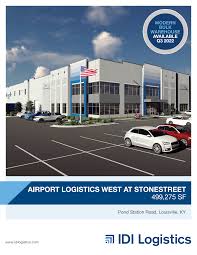
A Master of Science degree in Supply Chain Management can bring you many benefits. To begin, you can benefit from the rising demand for supply chain management professionals. The career prospects of this degree are also very attractive. Find out more about the various program options and requirements for this degree. A cost breakdown is also available. Learn more.
There are many career opportunities
An MBA in Supply Chain Management will help you become a supply-chain management expert and bridge to other jobs. Supply chain jobs are becoming more important in today's market and can be a bridge to other positions. A master's in Supply Chain Management could give you a competitive edge as well as a lucrative career. There are many career options for this degree, so it is important to learn how to get the most out of it.
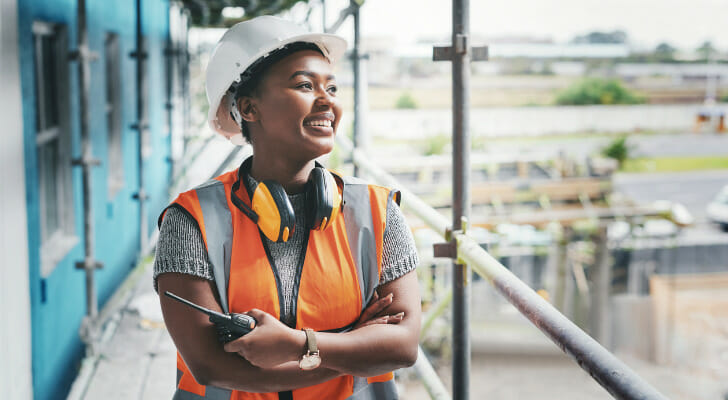
Education requirements
Rutgers Business School provides an online master in science supply chain administration program for 30 credits. This prepares students in one of most rapidly-growing fields of business. Many of the biggest companies around the globe consider supply chain management an essential skill and actively recruit students to their ranks. This program covers every aspect of supply chain operations, from the fundamental principles of operations to the intricate logistics of global supply chains.
Programs available
There are many Master of Science supply chain management programs that you can choose from if you want to be a supply chain manager. These programs will prepare and equip you to succeed in this rapidly growing field. The minimum required credits for the Master's Degree are 30 credits. Your individual program may need fewer credits. If you'd like to be more flexible with your schedule, you can choose a program with accelerated classes, asynchronous courses, or a weekend format. You can contact the graduate school directly to learn more about the various programs and inquire about their start dates, the transferability of credits and whether financial aid is accepted.
Prices
The MSSCM Master of Science in Supply Chain Management program is considerably less expensive than other graduate programs. The MSSCM requires fewer credits so graduates can earn their high-quality graduate degree at half the price of other graduate programs. Saint Louis University alumni friends provide generous scholarships to students that make it possible to pay less for their education.
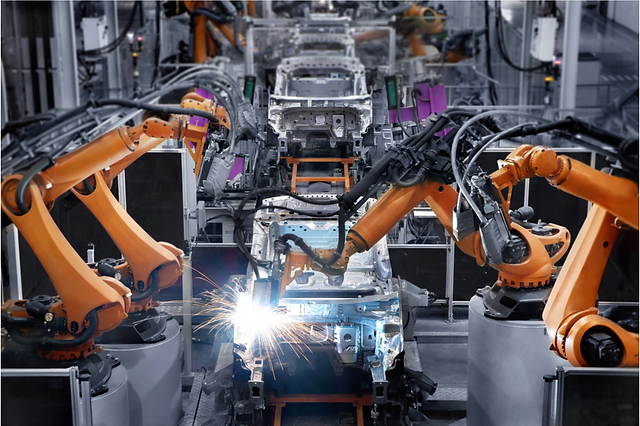
The typical program length
A typical Master of Science in Supply Chain Management (MSSCM) program is 30 credit hours. The curriculum is designed for working professionals. This curriculum is based on simulations and case study learning. Students will get real-world exposure and can then apply what they have learned to their current workplace. This program is for students who have a bachelor's in engineering, business, economics or another related field.
FAQ
What is meant by manufacturing industries?
Manufacturing Industries are those businesses that make products for sale. The people who buy these products are called consumers. To accomplish this goal, these companies employ a range of processes including distribution, sales, management, and production. They create goods from raw materials, using machines and various other equipment. This includes all types if manufactured goods.
What is production planning?
Production Planning includes planning for all aspects related to production. It is important to have everything ready and planned before you start shooting. You should also have information to ensure the best possible results on set. This includes information on shooting times, locations, cast lists and crew details.
It is important to first outline the type of film you would like to make. You may have already chosen the location you want, or there are locations or sets you prefer. Once you've identified the locations and scenes you want to use, you can begin to plan what elements you need for each scene. You might decide you need a car, but not sure what make or model. To narrow your options, you can search online for available models.
After you have selected the car you want, you can begin to think about additional features. What about additional seating? Maybe you need someone to move around in the back. Perhaps you would like to change the interior colour from black to white. These questions can help you decide the right look for your car. You can also think about the type of shots you want to get. What type of shots will you choose? Perhaps you want to show the engine or the steering wheel? These factors will help you determine which car style you want to film.
Once you have established all the details, you can create a schedule. You can create a schedule that will outline when you must start and finish your shoots. Every day will have a time for you to arrive at the location, leave when you are leaving and return home when you are done. Everyone will know what they need and when. Hire extra staff by booking them ahead of time. You should not hire anyone who doesn't show up because of your inaction.
It is important to calculate the amount of filming days when you are creating your schedule. Some projects are quick and easy, while others take weeks. While creating your schedule, it is important to remember whether you will require more than one shot per day. Multiple takes of the same location will lead to higher costs and take more time. It is better to be cautious and take fewer shots than you risk losing money if you are not sure if multiple takes are necessary.
Another important aspect of production planning is setting budgets. A realistic budget will help you work within your means. You can always lower the budget if you encounter unexpected problems. It is important to not overestimate how much you will spend. You will end up spending less money if you underestimate the cost of something.
Production planning is a very detailed process, but once you understand how everything works together, it becomes easier to plan future projects.
What are the four types of manufacturing?
Manufacturing is the process of transforming raw materials into useful products using machines and processes. Manufacturing can include many activities such as designing and building, testing, packaging shipping, selling, servicing, and other related activities.
How does manufacturing avoid bottlenecks in production?
Production bottlenecks can be avoided by ensuring that processes are running smoothly during the entire production process, starting with the receipt of an order and ending when the product ships.
This includes both planning for capacity and quality control.
Continuous improvement techniques such Six Sigma can help you achieve this.
Six Sigma is a management system used to improve quality and reduce waste in every aspect of your organization.
It seeks to eliminate variation and create consistency in your work.
Why automate your warehouse
Modern warehouses have become more dependent on automation. E-commerce has increased the demand for quicker delivery times and more efficient processes.
Warehouses should be able adapt quickly to new needs. Technology investment is necessary to enable warehouses to respond quickly to changing demands. The benefits of automating warehouses are numerous. Here are some reasons why it's worth investing in automation:
-
Increases throughput/productivity
-
Reduces errors
-
Increases accuracy
-
Safety enhancements
-
Eliminates bottlenecks
-
This allows companies to scale easily
-
Increases efficiency of workers
-
This gives you visibility into what happens in the warehouse
-
Enhances customer experience
-
Improves employee satisfaction
-
Reducing downtime and increasing uptime
-
You can be sure that high-quality products will arrive on time
-
Human error can be eliminated
-
Helps ensure compliance with regulations
What is the role of a manager in manufacturing?
A manufacturing manager has to ensure that all manufacturing processes work efficiently and effectively. They should be alert for any potential problems in the company and react accordingly.
They should also learn how to communicate effectively with other departments, including sales and marketing.
They must also keep up-to-date with the latest trends in their field and be able use this information to improve productivity and efficiency.
What does warehouse refer to?
A warehouse or storage facility is where goods are stored before they are sold. It can be indoors or out. It could be one or both.
Statistics
- Many factories witnessed a 30% increase in output due to the shift to electric motors. (en.wikipedia.org)
- It's estimated that 10.8% of the U.S. GDP in 2020 was contributed to manufacturing. (investopedia.com)
- According to the United Nations Industrial Development Organization (UNIDO), China is the top manufacturer worldwide by 2019 output, producing 28.7% of the total global manufacturing output, followed by the United States, Japan, Germany, and India.[52][53] (en.wikipedia.org)
- [54][55] These are the top 50 countries by the total value of manufacturing output in US dollars for its noted year according to World Bank.[56] (en.wikipedia.org)
- Job #1 is delivering the ordered product according to specifications: color, size, brand, and quantity. (netsuite.com)
External Links
How To
How to Use Just-In-Time Production
Just-in-time is a way to cut costs and increase efficiency in business processes. It's the process of obtaining the right amount and timing of resources when you need them. This means that you only pay for what you actually use. Frederick Taylor was the first to coin this term. He developed it while working as a foreman during the early 1900s. Taylor observed that overtime was paid to workers if they were late in working. He realized that workers should have enough time to complete their jobs before they begin work. This would help increase productivity.
JIT is about planning ahead. You should have all the necessary resources ready to go so that you don’t waste money. Look at your entire project, from start to end. Make sure you have enough resources in place to deal with any unexpected problems. If you expect problems to arise, you will be able to provide the necessary equipment and personnel to address them. You won't have to pay more for unnecessary items.
There are different types of JIT methods:
-
Demand-driven JIT: This is a JIT that allows you to regularly order the parts/materials necessary for your project. This will allow to track how much material has been used up. It will also allow you to predict how long it takes to produce more.
-
Inventory-based: This allows you to store the materials necessary for your projects in advance. This allows you to forecast how much you will sell.
-
Project-driven : This is a method where you make sure that enough money is set aside to pay the project's cost. You will be able to purchase the right amount of materials if you know what you need.
-
Resource-based JIT is the most widespread form. You allocate resources based on the demand. If you have many orders, you will assign more people to manage them. If you don't receive many orders, then you'll assign fewer employees to handle the load.
-
Cost-based: This is similar to resource-based, except that here you're not just concerned about how many people you have but how much each person costs.
-
Price-based: This is a variant of cost-based. However, instead of focusing on the individual workers' costs, this looks at the total price of the company.
-
Material-based is an alternative to cost-based. Instead of looking at the total cost in the company, this method focuses on the average amount of raw materials that you consume.
-
Time-based: Another variation of resource-based JIT. Instead of focusing on how much each employee costs, you focus on how long it takes to complete the project.
-
Quality-based JIT: Another variation on resource-based JIT. Instead of thinking about how much each employee costs or how long it takes to manufacture something, you think about how good the quality of your product is.
-
Value-based: This is one of the newest forms of JIT. This is where you don't care about how the products perform or whether they meet customers' expectations. Instead, your goal is to add value to the market.
-
Stock-based. This method is inventory-based and focuses only on the actual production at any given point. It's useful when you want maximum production and minimal inventory.
-
Just-intime planning (JIT), is a combination JIT/sales chain management. It's the process of scheduling delivery of components immediately after they are ordered. It is essential because it reduces lead-times and increases throughput.