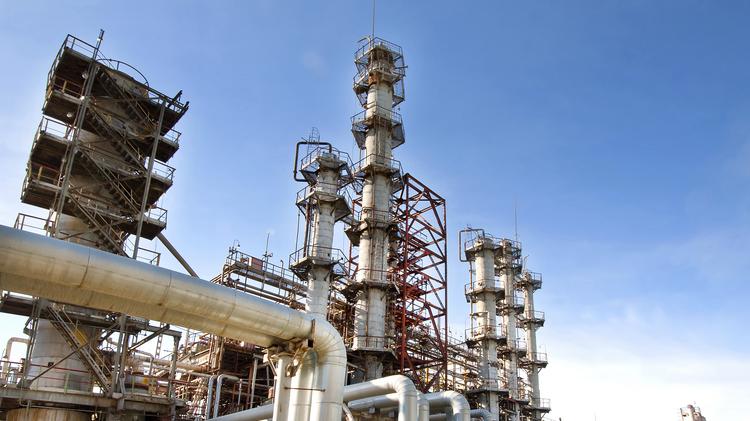
Heijunka was first developed by Toyota Japan to improve efficiency in multi-step production. It reduces waste in the production process by ensuring that the production schedule corresponds with customer demand. It eliminates abrupt fluctuations in production, which also reduces waste. Heijunka aids manufacturers to satisfy customer demands and increase their profits.
Heijunka is the process of coordinating small production batches across manufacturing line lines. It's used to improve efficiency when multi-step production is being done, particularly when just-in time principles are used. It is also part in the Toyota Production System. It reduces production waste by leveling production volume and mixing products.
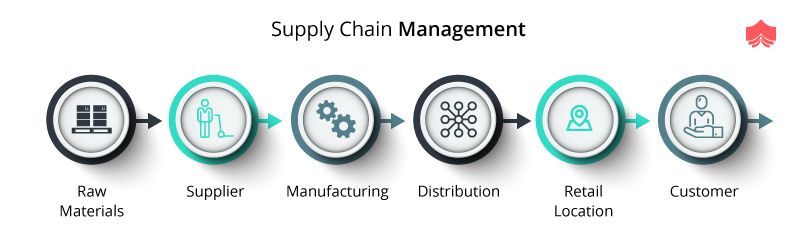
Two methods can be used to implement Heijunka. One is the use of a heijunkabox. It is a grid containing small boxes that is fixed or mounted to a wall. It allows production personnel visualize the production process and schedules them. Magnetic cards can also be used to implement Heijunka.
Toyota dealers use Heijunka to increase their changeover time. It is also part of Toyota's Lean manufacturing framework. Heijunka can be used to improve production and inventory management. Heijunka allows for better utilization of equipment and labor. It provides a lean production system that reduces waste, thereby making better products available to customers.
The takt rate, also called the customer buying price, is essential in order to use heijunka. This is the amount of time it takes to complete a product to meet customer demand. Heijunka uses the takt time to determine the pace of production. You can calculate how many products you want to make and at what rate customers will buy your products using the takttime. In back office settings, the takt timing is used to help determine how quickly customers purchase the company's products.
Production staff can visually plan and schedule their production using the heijunka boxes. The heijunka is also useful for shop floor visualizations of the production process. The heijunka box is made up of rows and columns which represent each product type or component. The column of boxes represents each time period of the day, and the rows of boxes represent each product type.
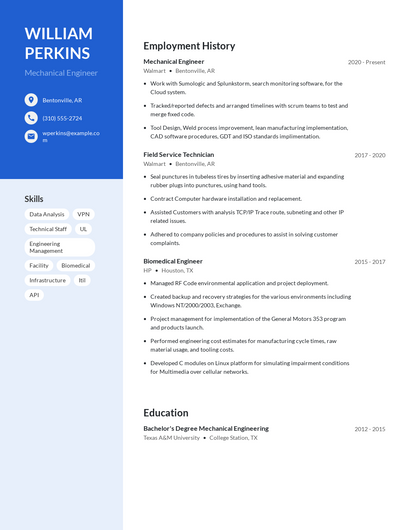
Heijunka Box (or Heijunka Box) is one of most commonly used visual management tools in manufacturing. This tool allows you to see the relationships between component production and product production. This tool provides visual representations of the production workload for each week. It is used together with the kanban deck, which is a set of colored cards that represents the product required for each production step. Kanban cards are usually taken from the heijunka boxes at a particular time and then delivered to the correct production area.
FAQ
What do you mean by warehouse?
A warehouse is a place where goods are stored until they are sold. It can be an outdoor or indoor area. It could be one or both.
What does it take for a logistics enterprise to succeed?
To be a successful businessman in logistics, you will need many skills and knowledge. Effective communication skills are necessary to work with suppliers and clients. You must be able analyze data and draw out conclusions. You must be able and able to handle stress situations and work under pressure. You need to be innovative and creative to come up with new ways to increase efficiency. To motivate and guide your team towards reaching organizational goals, you must have strong leadership skills.
It is also important to be efficient and well organized in order meet deadlines.
What does the term manufacturing industries mean?
Manufacturing Industries are businesses that produce products for sale. These products are sold to consumers. This is accomplished by using a variety of processes, including production, distribution and retailing. They make goods from raw materials with machines and other equipment. This includes all types and varieties of manufactured goods, such as food items, clothings, building supplies, furnitures, toys, electronics tools, machinery vehicles, pharmaceuticals medical devices, chemicals, among others.
What is the responsibility of a logistics manager?
Logistics managers ensure that goods arrive on time and are unharmed. This is accomplished by using the experience and knowledge gained from working with company products. He/she also needs to ensure adequate stock to meet demand.
How can efficiency in manufacturing be improved?
The first step is to determine the key factors that impact production time. Next, we must find ways to improve those factors. If you don’t know how to start, look at which factors have the greatest impact upon production time. Once you've identified them, try to find solutions for each of those factors.
Why automate your factory?
Modern warehouses are increasingly dependent on automation. E-commerce has brought increased demand for more efficient and quicker delivery times.
Warehouses should be able adapt quickly to new needs. Technology investment is necessary to enable warehouses to respond quickly to changing demands. Automation of warehouses offers many benefits. Here are some of the reasons automation is worth your investment:
-
Increases throughput/productivity
-
Reduces errors
-
Improves accuracy
-
Safety increases
-
Eliminates bottlenecks
-
Companies can scale up more easily
-
This makes workers more productive
-
This gives you visibility into what happens in the warehouse
-
Enhances customer experience
-
Improves employee satisfaction
-
Reduces downtime and improves uptime
-
You can be sure that high-quality products will arrive on time
-
Human error can be eliminated
-
Helps ensure compliance with regulations
What type of jobs is there in logistics
There are many types of jobs in logistics. Here are some examples:
-
Warehouse workers – They load and unload pallets and trucks.
-
Transport drivers - These are people who drive trucks and trailers to transport goods or perform pick-ups.
-
Freight handlers are people who sort and pack freight into warehouses.
-
Inventory managers - They oversee the inventory of goods in warehouses.
-
Sales representatives - They sell products to customers.
-
Logistics coordinators – They plan and coordinate logistics operations.
-
Purchasing agents: They are responsible for purchasing goods and services to support company operations.
-
Customer service agents - They answer phone calls and respond to emails.
-
Shipping clerks – They process shipping orders, and issue bills.
-
Order fillers - They fill orders based on what is ordered and shipped.
-
Quality control inspectors – They inspect incoming and outgoing products to ensure that there are no defects.
-
Others – There are many other types available in logistics. They include transport supervisors, cargo specialists and others.
Statistics
- You can multiply the result by 100 to get the total percent of monthly overhead. (investopedia.com)
- According to a Statista study, U.S. businesses spent $1.63 trillion on logistics in 2019, moving goods from origin to end user through various supply chain network segments. (netsuite.com)
- Many factories witnessed a 30% increase in output due to the shift to electric motors. (en.wikipedia.org)
- [54][55] These are the top 50 countries by the total value of manufacturing output in US dollars for its noted year according to World Bank.[56] (en.wikipedia.org)
- Job #1 is delivering the ordered product according to specifications: color, size, brand, and quantity. (netsuite.com)
External Links
How To
How to Use 5S for Increasing Productivity in Manufacturing
5S stands to stand for "Sort", “Set In Order", “Standardize", and "Store". The 5S methodology was developed at Toyota Motor Corporation in 1954. It helps companies achieve higher levels of efficiency by improving their work environment.
The basic idea behind this method is to standardize production processes, so they become repeatable, measurable, and predictable. This means that every day tasks such cleaning, sorting/storing, packing, and labeling can be performed. Workers can be more productive by knowing what to expect.
Five steps are required to implement 5S: Sort, Set In Order, Standardize. Separate. Each step requires a different action, which increases efficiency. By sorting, for example, you make it easy to find the items later. When you set items in an order, you put items together. After you have divided your inventory into groups you can store them in easy-to-reach containers. Finally, when you label your containers, you ensure everything is labeled correctly.
Employees must be able to critically examine their work practices. Employees should understand why they do the tasks they do, and then decide if there are better ways to accomplish them. To be successful in the 5S system, employees will need to acquire new skills and techniques.
The 5S method not only increases efficiency but also boosts morale and teamwork. Once they start to notice improvements, they are motivated to keep working towards their goal of increasing efficiency.