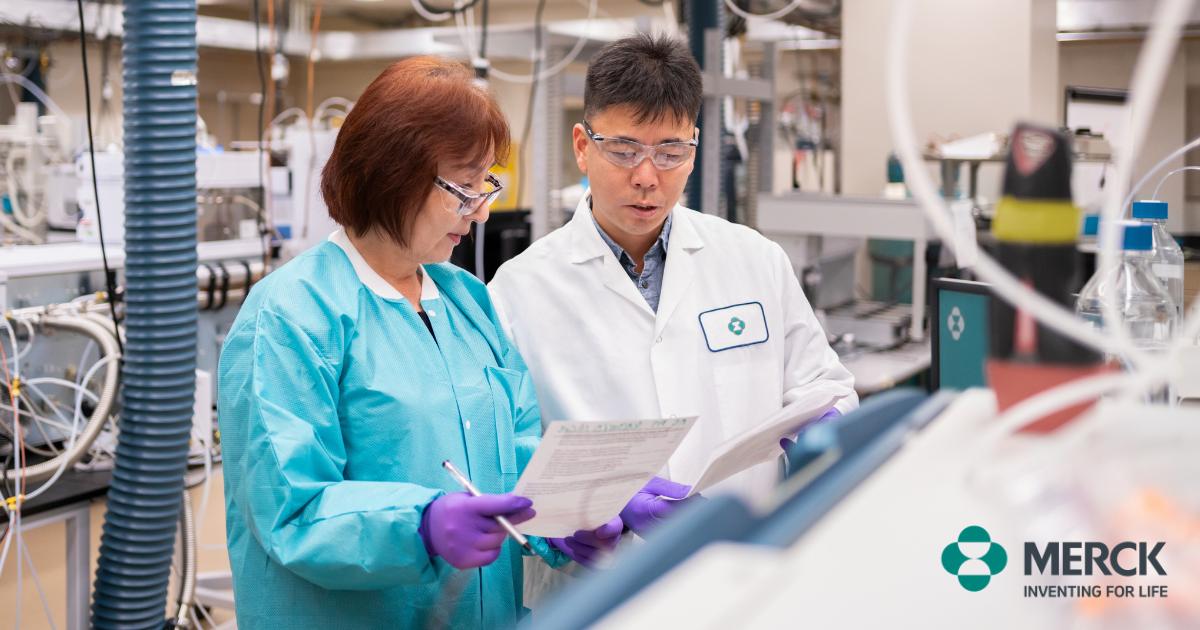
Are you searching for jobs in logistics in New Jersey? These jobs can be in any setting and require many skills. A bachelor's degree is preferable. The following qualifications are necessary to obtain a job in logistics management. These skills include the ability to work independently and problem-solve. You should have a positive attitude and be a natural problem-solver.
A bachelor's degree or equivalent is required
You will need to have a bachelor's degree from an accredited university and 4+ years of experience in logistics. Additionally, you must demonstrate organizational and time-management skills. Additionally, you will need to have excellent communication skills and fluency in English. In addition, you should have an aptitude for data analysis, proven leadership abilities, and excellent interpersonal skills.
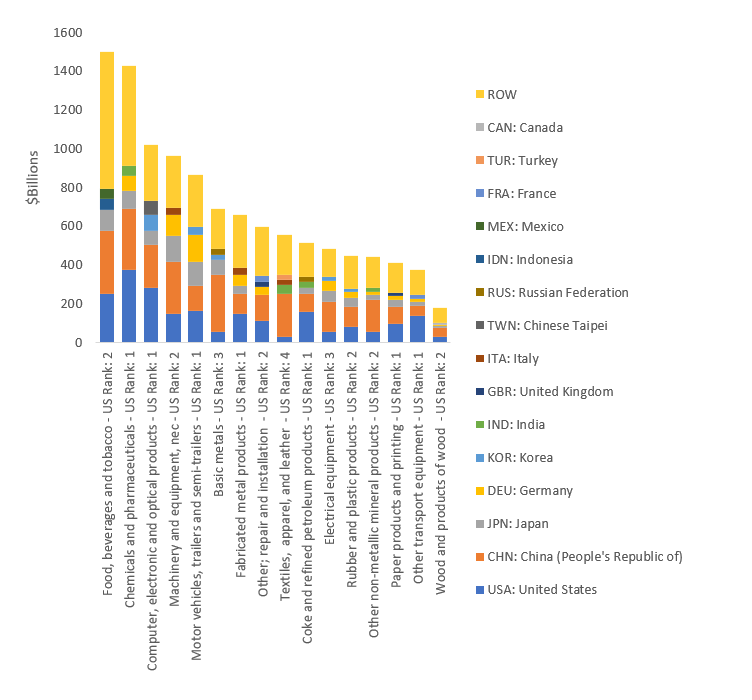
A Bachelor's degree in logistics in New Jersey is a prerequisite for many of these positions. You can make a lot if you apply your skills to other industries, even though most of the jobs in this field require middle-skill. New Jersey is home to many middle-skill jobs, which require workers who have received specialized training. NJCU's Center for Workforce and Community Development offers one of these middle-skill training programs.
Employers will accept a work experience in logistics as an alternative to a college education. Experience can help you be more marketable and increase the likelihood of being hired. You may have a job as a customer service representative or freight agent if you have a bachelor's degree in logistics. You can get promoted to management positions in logistics if you have experience and other qualifications. Further education is possible in logistics as well, including postsecondary teaching or research.
Preferably, a bachelor's is required
Several logistics positions require a bachelor's degree, and a bachelor's degree in a related field is often preferred. A bachelor's degree is preferred by employers because it allows them to deal with complicated supply chains as well as transportation laws. A bachelor's degree gives students a broad knowledge of logistics and helps them to build professional networks. One entry-level job in logistics could be as a dispatcher or customer service representative. Manager positions are possible with advanced qualifications and training. Research, consulting, and teaching are all options for higher-level logistics jobs.
Employers prefer a bachelor's degree in logistics, but an associate's degree is also possible. Relevant work experience could be used in some cases to replace education. Certifications in industry-specific fields such as data analysis, warehouse management, or supply chain management are also helpful for job seekers. In New Jersey, however, a bachelor's is preferable for jobs in logistics. A bachelor's program in logistics will allow you to gain the insight necessary to understand the workings of a supply-chain. Many companies require a bachelor's degree, particularly if they handle large-scale transactions.
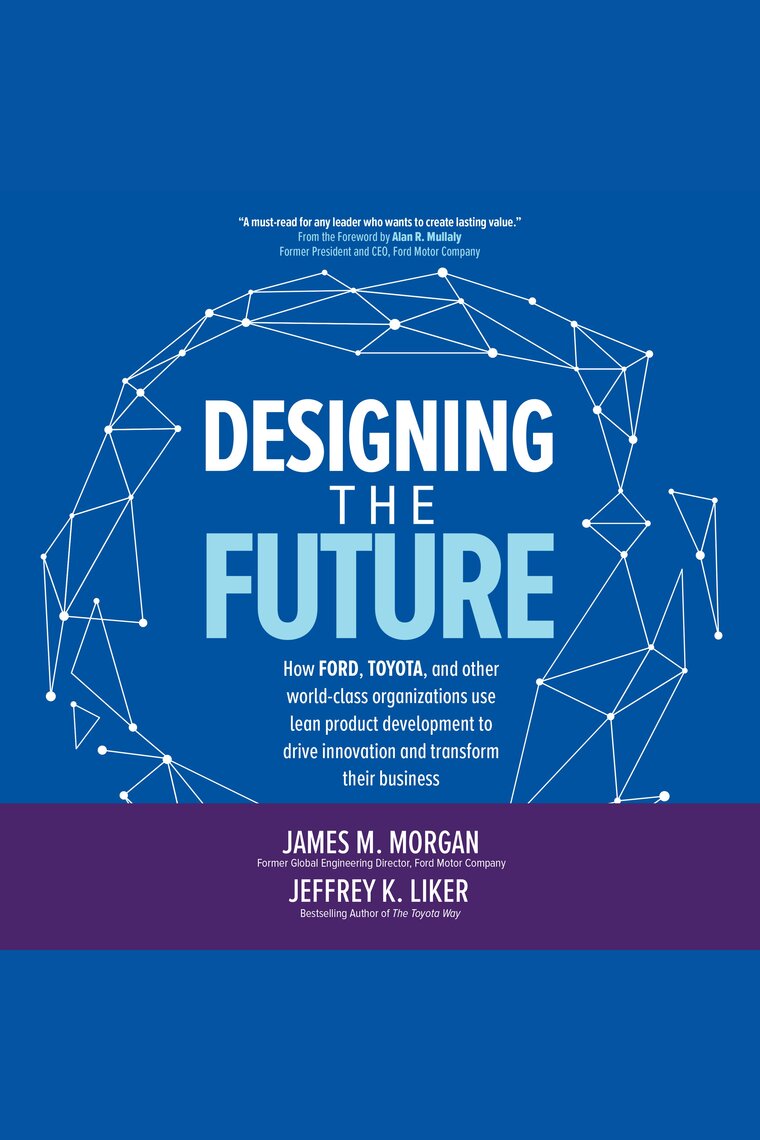
You will need a bachelor's in engineering if you are interested in working as an industrial engineer. A bachelor's degree is required in order to work as an Industrial Engineer. You also need to have knowledge of the municipal coding rules. A minimum of six years work experience is required for an Industrial Engineer. You should also be familiar with similar working conditions in other industries to which you are applying.
FAQ
What can I do to learn more about manufacturing?
The best way to learn about manufacturing is through hands-on experience. If that is not possible, you could always read books or view educational videos.
What are the products of logistics?
Logistics are the activities involved in moving goods from point A to point B.
They include all aspects of transport, including packaging, loading, transporting, unloading, storing, warehousing, inventory management, customer service, distribution, returns, and recycling.
Logisticians ensure that the product is delivered to the correct place, at the right time, and under safe conditions. They help companies manage their supply chain efficiency by providing information on demand forecasts, stock levels, production schedules, and availability of raw materials.
They also keep track of shipments in transit, monitor quality standards, perform inventories and order replenishment, coordinate with suppliers and vendors, and provide support services for sales and marketing.
What is it like to manage a logistics company?
You need to have a lot of knowledge and skills to manage a successful logistic business. To communicate effectively with clients and suppliers, you must be able to communicate well. You must be able analyze data and draw out conclusions. You need to be able work under pressure and manage stressful situations. You must be creative and innovative to develop new ideas to improve efficiency. Strong leadership qualities are essential to motivate your team and help them achieve their organizational goals.
It is important to be organized and efficient in order to meet tight deadlines.
How important is automation in manufacturing?
Automation is important not only for manufacturers but also for service providers. Automation allows them to deliver services quicker and more efficiently. In addition, it helps them reduce costs by reducing human errors and improving productivity.
What does manufacturing mean?
Manufacturing Industries are businesses that produce products for sale. These products are sold to consumers. These companies use various processes such as production, distribution, retailing, management, etc., to fulfill this purpose. They produce goods from raw materials by using machines and other machinery. This includes all types of manufactured goods, including food items, clothing, building supplies, furniture, toys, electronics, tools, machinery, vehicles, pharmaceuticals, medical devices, chemicals, and many others.
How can we reduce manufacturing overproduction?
In order to reduce excess production, you need to develop better inventory management methods. This would reduce time spent on activities such as purchasing, stocking, and maintaining excess stock. By doing this, we could free up resources for other productive tasks.
Kanban systems are one way to achieve this. A Kanban board is a visual display used to track work in progress. A Kanban system allows work items to move through several states before reaching their final destination. Each state has a different priority level.
If work is moving from one stage to the other, then the current task can be completed and moved on to the next. It is possible to keep a task in the beginning stages until it gets to the end.
This allows you to keep work moving along while making sure that no work gets neglected. A Kanban board allows managers to monitor how much work is being completed at any given moment. This information allows managers to adjust their workflow based off real-time data.
Lean manufacturing can also be used to reduce inventory levels. Lean manufacturing is about eliminating waste from all stages of the production process. Any product that isn't adding value can be considered waste. There are several types of waste that you might encounter:
-
Overproduction
-
Inventory
-
Packaging not required
-
Exceed materials
Manufacturers can increase efficiency and decrease costs by implementing these ideas.
What are the four types in manufacturing?
Manufacturing is the process of transforming raw materials into useful products using machines and processes. Manufacturing can include many activities such as designing and building, testing, packaging shipping, selling, servicing, and other related activities.
Statistics
- In the United States, for example, manufacturing makes up 15% of the economic output. (twi-global.com)
- Job #1 is delivering the ordered product according to specifications: color, size, brand, and quantity. (netsuite.com)
- (2:04) MTO is a production technique wherein products are customized according to customer specifications, and production only starts after an order is received. (oracle.com)
- It's estimated that 10.8% of the U.S. GDP in 2020 was contributed to manufacturing. (investopedia.com)
- According to a Statista study, U.S. businesses spent $1.63 trillion on logistics in 2019, moving goods from origin to end user through various supply chain network segments. (netsuite.com)
External Links
How To
How to use lean manufacturing in the production of goods
Lean manufacturing (or lean manufacturing) is a style of management that aims to increase efficiency, reduce waste and improve performance through continuous improvement. It was first developed in Japan in the 1970s/80s by Taiichi Ahno, who was awarded the Toyota Production System (TPS), award from KanjiToyoda, the founder of TPS. Michael L. Watkins published the book "The Machine That Changed the World", which was the first to be published about lean manufacturing.
Lean manufacturing, often described as a set and practice of principles, is aimed at improving the quality, speed, cost, and efficiency of products, services, and other activities. It emphasizes reducing defects and eliminating waste throughout the value chain. Lean manufacturing can be described as just-in–time (JIT), total productive maintenance, zero defect (TPM), or even 5S. Lean manufacturing focuses on eliminating non-value-added activities such as rework, inspection, and waiting.
Lean manufacturing improves product quality and costs. It also helps companies reach their goals quicker and decreases employee turnover. Lean manufacturing is considered one of the most effective ways to manage the entire value chain, including suppliers, customers, distributors, retailers, and employees. Lean manufacturing is widely used in many industries. Toyota's philosophy is the foundation of its success in automotives, electronics and appliances, healthcare, chemical engineers, aerospace, paper and food, among other industries.
Lean manufacturing is based on five principles:
-
Define Value - Identify the value your business adds to society and what makes you different from competitors.
-
Reduce Waste – Eliminate all activities that don't add value throughout the supply chain.
-
Create Flow - Ensure work moves smoothly through the process without interruption.
-
Standardize & simplify - Make processes consistent and repeatable.
-
Build relationships - Develop and maintain personal relationships with both your internal and external stakeholders.
Lean manufacturing isn’t new, but it has seen a renewed interest since 2008 due to the global financial crisis. Many businesses have adopted lean manufacturing techniques to help them become more competitive. Some economists even believe that lean manufacturing can be a key factor in economic recovery.
Lean manufacturing is becoming a popular practice in automotive. It has many advantages. These include higher customer satisfaction, lower inventory levels, lower operating expenses, greater productivity, and improved overall safety.
The principles of lean manufacturing can be applied in almost any area of an organization. This is because it ensures efficiency and effectiveness in all stages of the value chain.
There are three main types:
-
Just-in Time Manufacturing (JIT), also known as "pull system": This form of lean manufacturing is often referred to simply as "pull". JIT refers to a system in which components are assembled at the point of use instead of being produced ahead of time. This approach reduces lead time, increases availability and reduces inventory.
-
Zero Defects Manufacturing - ZDM: ZDM focuses its efforts on making sure that no defective units leave a manufacturing facility. You should repair any part that needs to be repaired during an assembly line. This applies to finished goods that may require minor repairs before shipment.
-
Continuous Improvement (CI): CI aims to improve the efficiency of operations by continuously identifying problems and making changes in order to eliminate or minimize waste. Continuous Improvement involves continuous improvement of processes.