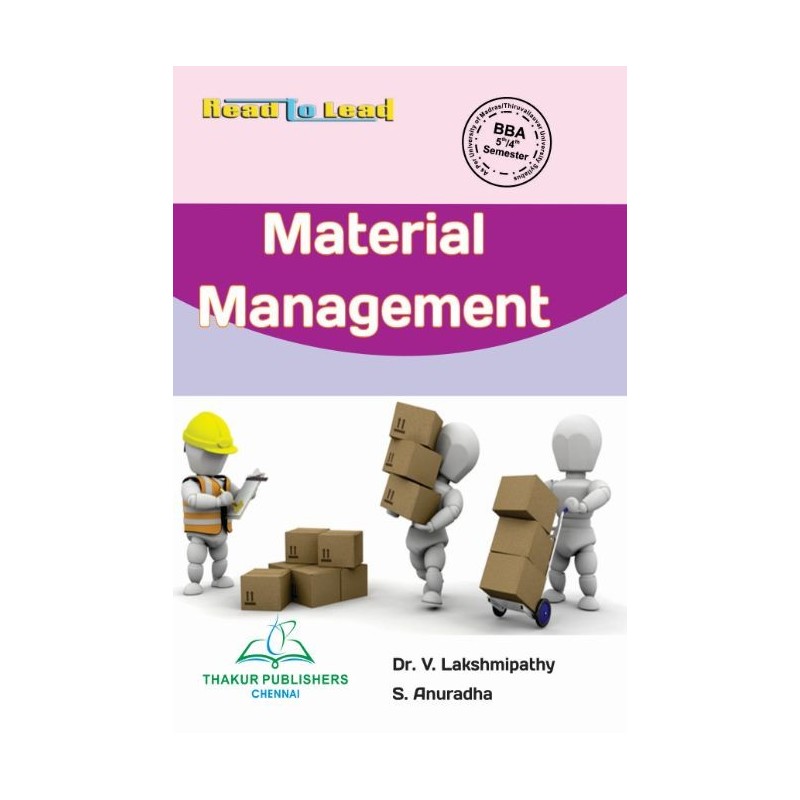
Among the tools in the lean toolbox are Hoshin Kanri, Visual board, Value Stream Mapping, and Process Observation and Analysis. These methods employ statistical data and quality controls measures to reduce defects, improve process performance, and increase efficiency. The safety and well-being of employees, the cycle time, delivery times, and quality of raw materials are all improved by Lean tools. Read our articles to learn more about these tools. We also give examples and explain the basics.
Hoshinkanri
It's important to communicate each department's goals when implementing Hoshinkanri principles. It's vital to clearly communicate your company's objectives and the results that they produce. Google Images has a sample Hoshin Kanri template. The idea behind the Hoshinkanri matrix is to ensure everyone is on the same page and can work together towards common goals.
Hoshin Kanri is an inclusive approach that will help you determine what areas of your business are in need of improvement. You can identify the specific activities that need improvement and create a clear plan from general goals to take concrete steps. You can also use it to track your progress and see how each step connects to the previous. Hoshin Kanri encourages collaboration to improve the company as a whole, rather than boring business plans.
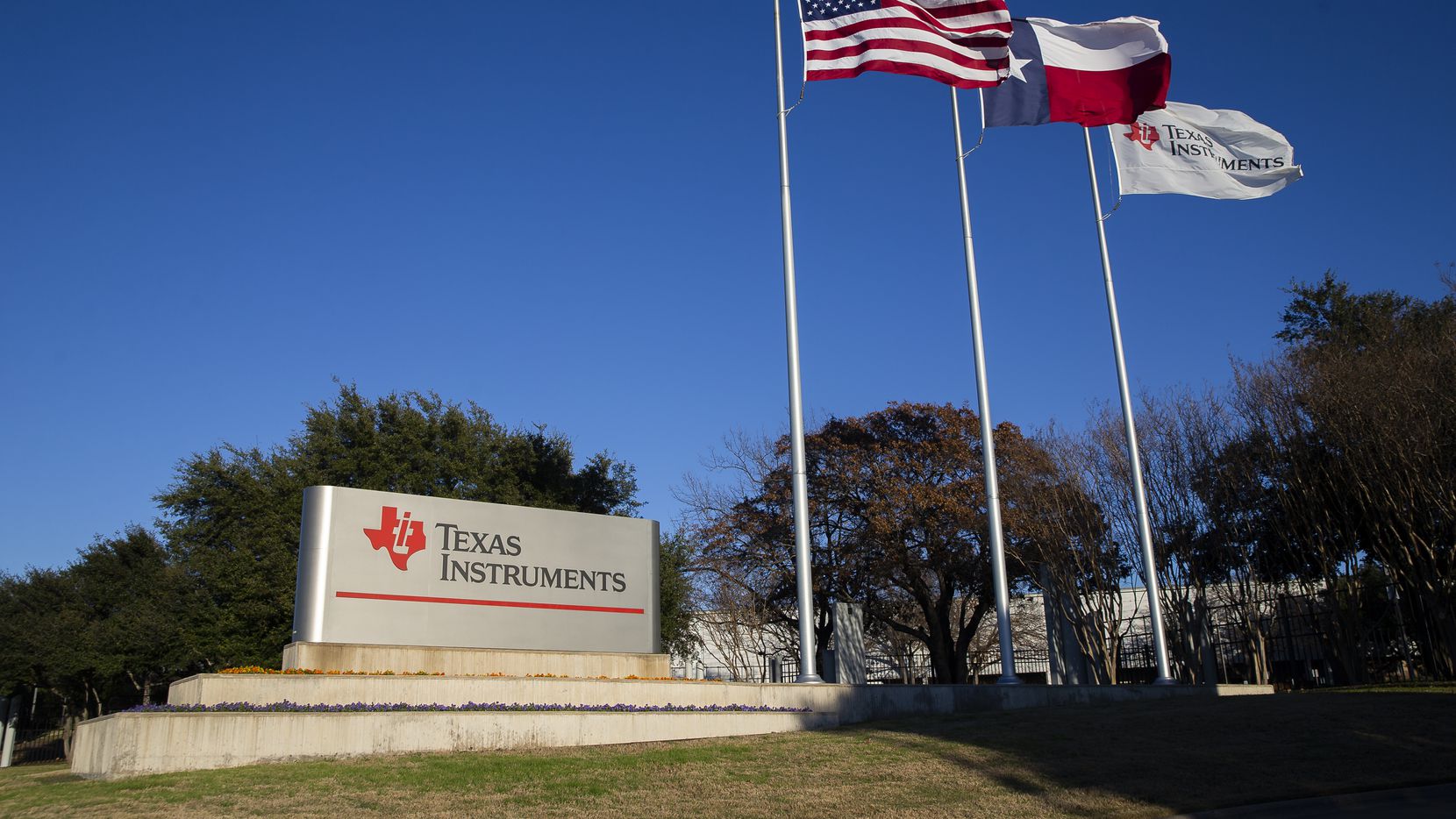
Visual board
While the visual board is a powerful tool for measuring the results of a process, it is not a universal tool. You cannot use it as a tool if the implementation involves people. The visual management board should be personalized for the user to bring out emotion behind the numbers. It can also serve as a tool to track performance indicators like the amount of work hours or pieces that were produced in standard time. Although there is no universal code, there a few key elements that make this tool work in a lean environment.
A visual management board's key feature is its ability to quickly communicate with all members of a team about what needs to happen and who is responsible. The board can display this information in less than 20 seconds. To ensure that everyone is on the exact same page, management must also see the results. Regular updates can be made to the visual management boards in order to ensure that everyone is on a similar page.
Value Stream Mapping
When using value stream mapping in tools lean, a facilitator must identify the bottleneck or constraint in the process. A bottleneck is the process step with the highest WIP. For example, suppose a three-step process has 60 units per an hour throughput but a potential total WIP of 42 units, Step 2 is the bottleneck. The value stream map is a tool that can be used to identify bottlenecks and help you find ways to improve your process.
Understanding the customer perspective and the system or process is key to a successful value stream mapping. This is often a multi-functional and complex process. It can require extensive involvement and training. Larger companies might have a value-stream manager who will lead the mapping. Value stream mapping is an important project. However, smaller ones can help you identify potential savings and areas that could be improved. In tools lean, value stream mapping can be a powerful tool.
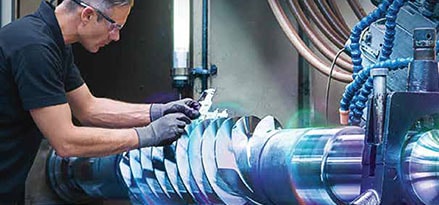
Process Observation and Analysis
Lean management is founded on continuous improvement and process observation. The goal of process observation is to ensure standards are maintained and processes are delivering the expected outcome. It is possible for processes to become inefficient if they are not used. Process observation can have cultural consequences, so managers must clearly explain why they are required to do it and the benefits it offers. Lean management systems include process observation and analysis. Managers need to communicate the importance of this part to their teams.
First, verifying the process flow map is essential to implement Lean. This can be done by walking through the process. After this step has been completed, it is time to analyze the data collected. The Measure phase involves gathering data on the current product, process, or service. The project leader applies statistical hypothesis-testing techniques to find the root cause. Analyses determine whether the problem can be eliminated or solved.
FAQ
How can manufacturing avoid production bottlenecks
Avoiding production bottlenecks is as simple as keeping all processes running smoothly, from the time an order is received until the product ships.
This includes both quality control and capacity planning.
Continuous improvement techniques like Six Sigma are the best way to achieve this.
Six Sigma is a management system used to improve quality and reduce waste in every aspect of your organization.
It seeks to eliminate variation and create consistency in your work.
What kind of jobs are there in logistics?
Logistics can offer many different jobs. Some of them are:
-
Warehouse workers: They load and unload trucks, pallets, and other cargo.
-
Transportation drivers – These drivers drive trucks and wagons to transport goods and pick up the goods.
-
Freight handlers, - They sort out and pack freight in warehouses.
-
Inventory managers – They manage the inventory in warehouses.
-
Sales reps are people who sell products to customers.
-
Logistics coordinators are responsible for organizing and planning logistics operations.
-
Purchasing agents: They are responsible for purchasing goods and services to support company operations.
-
Customer service representatives - They answer calls and emails from customers.
-
Ship clerks - They issue bills and process shipping orders.
-
Order fillers - They fill orders based on what is ordered and shipped.
-
Quality control inspectors (QCI) - They inspect all incoming and departing products for potential defects.
-
Others - There are many types of jobs in logistics such as transport supervisors and cargo specialists.
What does manufacturing mean?
Manufacturing Industries are companies that manufacture products. Consumers are the people who purchase these products. To accomplish this goal, these companies employ a range of processes including distribution, sales, management, and production. They make goods from raw materials with machines and other equipment. This includes all types manufactured goods such as clothing, building materials, furniture, electronics, tools and machinery.
Statistics
- [54][55] These are the top 50 countries by the total value of manufacturing output in US dollars for its noted year according to World Bank.[56] (en.wikipedia.org)
- (2:04) MTO is a production technique wherein products are customized according to customer specifications, and production only starts after an order is received. (oracle.com)
- It's estimated that 10.8% of the U.S. GDP in 2020 was contributed to manufacturing. (investopedia.com)
- In the United States, for example, manufacturing makes up 15% of the economic output. (twi-global.com)
- According to a Statista study, U.S. businesses spent $1.63 trillion on logistics in 2019, moving goods from origin to end user through various supply chain network segments. (netsuite.com)
External Links
How To
How to Use Lean Manufacturing for the Production of Goods
Lean manufacturing is an approach to management that aims for efficiency and waste reduction. It was developed in Japan between 1970 and 1980 by Taiichi Ohno. TPS founder Kanji Tyoda gave him the Toyota Production System, or TPS award. The first book published on lean manufacturing was titled "The Machine That Changed the World" written by Michael L. Watkins and published in 1990.
Lean manufacturing is often described as a set if principles that help improve the quality and speed of products and services. It emphasizes the elimination of defects and waste throughout the value stream. Lean manufacturing is called just-in-time (JIT), zero defect, total productive maintenance (TPM), or 5S. Lean manufacturing focuses on eliminating non-value-added activities such as rework, inspection, and waiting.
Lean manufacturing not only improves product quality but also reduces costs. Companies can also achieve their goals faster by reducing employee turnover. Lean manufacturing can be used to manage all aspects of the value chain. Customers, suppliers, distributors, retailers and employees are all included. Lean manufacturing is widely used in many industries. Toyota's philosophy is the foundation of its success in automotives, electronics and appliances, healthcare, chemical engineers, aerospace, paper and food, among other industries.
Lean manufacturing includes five basic principles:
-
Define Value - Identify the value your business adds to society and what makes you different from competitors.
-
Reduce Waste - Remove any activity which doesn't add value to your supply chain.
-
Create Flow - Ensure work moves smoothly through the process without interruption.
-
Standardize & Simplify - Make processes as consistent and repeatable as possible.
-
Develop Relationships: Establish personal relationships both with internal and external stakeholders.
Lean manufacturing is not a new concept, but it has been gaining popularity over the last few years due to a renewed interest in the economy following the global financial crisis of 2008. Many businesses are now using lean manufacturing to improve their competitiveness. Many economists believe lean manufacturing will play a major role in economic recovery.
Lean manufacturing is now becoming a common practice in the automotive industry, with many benefits. These benefits include increased customer satisfaction, reduced inventory levels and lower operating costs.
The principles of lean manufacturing can be applied in almost any area of an organization. Lean manufacturing is most useful in the production sector of an organisation because it ensures that each step in the value-chain is efficient and productive.
There are three main types:
-
Just-in-Time Manufacturing: Also known as "pull systems", this type of lean manufacturing uses just-in-time manufacturing (JIT). JIT refers to a system in which components are assembled at the point of use instead of being produced ahead of time. This approach is designed to reduce lead times and increase the availability of components. It also reduces inventory.
-
Zero Defects Manufacturing (ZDM),: ZDM is a system that ensures no defective units are left the manufacturing facility. If a part needs to be fixed during the assembly line, it should be repaired rather than scrapped. This is also true for finished products that require minor repairs before shipping.
-
Continuous Improvement (CI), also known as Continuous Improvement, aims at improving the efficiency of operations through continuous identification and improvement to minimize or eliminate waste. Continuous improvement involves continuous improvement of processes and people as well as tools.