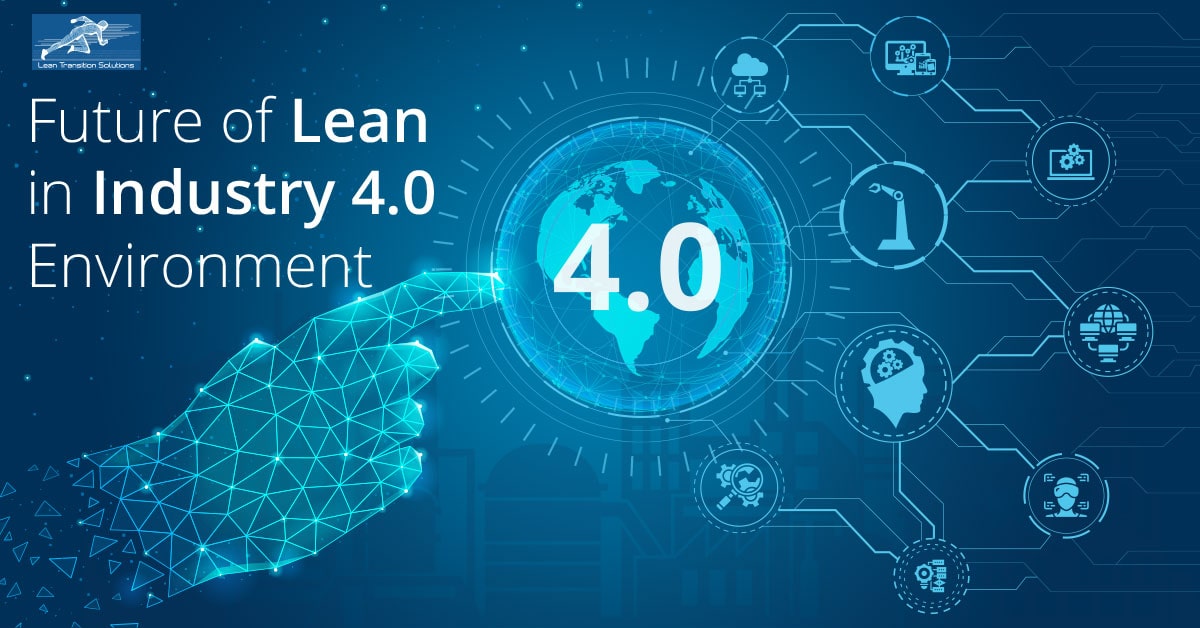
Hoshin Kanri and Value Stream Mapping are some of the lean tools. These tools use statistical data and quality control to reduce defects and improve processes performance. The safety and well-being of employees, the cycle time, delivery times, and quality of raw materials are all improved by Lean tools. Check out our articles about lean tools for more information. We also give examples and explain the basics.
Hoshin Kanri
Communication is key when it comes down to communicating the goals of each division to one another in order to implement the principles of Hoshin Kari. It is essential to communicate clearly the company's goals and the results they produce. Google Images gives you a sample Hoshin Kanri structure. The main idea of the matrix is that you want to make sure that everyone is aligned on the same goals, so that everyone can work towards them.
Hoshin Kanri is a comprehensive method that can help identify areas in your business that require improvement. The Hoshin Kanri method helps you identify the most important activities and help you create a clear path that leads from your general goals to specific actions. It can help you visualize the relationship between each step and how it relates to others. Hoshin Kanri believes in a collaborative approach to improving the company's overall performance.
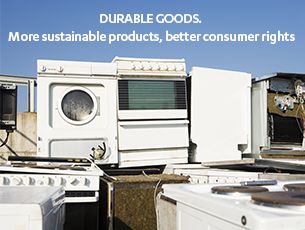
Visual board
Although the visual boards are a powerful tool to monitor the results of a project, they cannot be used as a general tool. It is only useful when there are people involved in the implementation. Visual management boards should be created for individual users to give the numbers a human touch. It can also serve as a tool to track performance indicators like the amount of work hours or pieces that were produced in standard time. It is possible to use this tool in lean production environments, but there are key elements.
One of the most important aspects of a visual board for management is the ability of all team members to quickly communicate what needs to be done, and who will do each task. This information can all be viewed on a board in less that 20 seconds. Management should also see the results to ensure everyone is on a similar page. A visual management board can be updated regularly to make sure that everyone is on the same page.
Value Stream Mapping
Value stream mapping in tools lean requires that a facilitator identify and address the bottlenecks and constraints in order to make the process more efficient. The bottleneck is the step in the process with the most WIP. If a three-step procedure has a throughput speed of 60 units an hour but a potential working capital of 42 units an hour, Step 2 will be the bottleneck. The value stream map can be used as a guide to pinpoint bottlenecks, and identify opportunities for process improvement.
A value stream mapping is only possible if you understand the customer's perspective and the system. This is a cross-functional process that can be complex. It may require training and extensive involvement from several people. Larger companies may hire a value stream manager for the mapping. Although value stream mapping may be a big project, smaller projects can identify areas where there are potential savings and improvements. A powerful tool in tools Lean is value stream mapping.

Process observation and analysis
Lean management centers on continuous improvement as well as process observation. Process observation is a way to make sure standards are being maintained and that processes deliver the desired outcome. In the end, abandoned processes will become less efficient. Process observation and analysis may have cultural implications. Managers should clearly communicate the reasons for process observation and the potential benefits. Process observation is an integral part of lean management. Therefore, managers need to explain why it is important to them and their staff.
To implement Lean, the first step involves verifying the process flow diagram by performing a walk-through. After this step has been completed, it is time to analyze the data collected. The Measure phase collects data regarding the current process, product, and/or service. The project leader applies statistical hypothesis-testing techniques to find the root cause. The analysis determines whether the problem was eliminated or ameliorated.
FAQ
What is manufacturing and logistics?
Manufacturing refers the process of producing goods from raw materials through machines and processes. Logistics manages all aspects of the supply chain, including procurement, production planning and distribution, inventory control, transportation, customer service, and transport. Logistics and manufacturing are often referred to as one thing. It encompasses both the creation of products and their delivery to customers.
What is production plan?
Production Planning includes planning for all aspects related to production. This document is designed to make sure everything is ready for when you're ready to shoot. This document should also include information on how to get the best result on set. This includes location information, crew details, equipment specifications, and casting lists.
The first step is to outline what you want to film. You may have decided where to shoot or even specific locations you want to use. Once you have identified the scenes and locations, you can start to determine which elements are required for each scene. You might decide you need a car, but not sure what make or model. You could look online for cars to see what options are available, and then narrow down your choices by selecting between different makes or models.
Once you have found the right car, you can start thinking about extras. Do you need people sitting in the front seats? Or maybe you just need someone to push the car around. Perhaps you would like to change the interior colour from black to white. These questions will help guide you in determining the ideal look and feel for your car. You can also think about the type of shots you want to get. Will you be filming close-ups or wide angles? Maybe you want the engine or the steering wheels to be shown. These details will help identify the exact car you wish to film.
Once you have made all the necessary decisions, you can start to create a schedule. A schedule will tell you when you need to start shooting and when you need to finish. You will need to know when you have to be there, what time you have to leave and when your return home. This way, everyone knows what they need to do and when. It is possible to make arrangements in advance for additional staff if you are looking to hire. It is not worth hiring someone who won’t show up because you didn’t tell him.
You will need to factor in the days that you have to film when creating your schedule. Some projects only take one or two days, while others may last weeks. When you are creating your schedule, you should always keep in mind whether you need more than one shot per day or not. Multiple takes at the same place will result in higher costs and longer completion times. It is better to be cautious and take fewer shots than you risk losing money if you are not sure if multiple takes are necessary.
Budgeting is another crucial aspect of production plan. As it will allow you and your team to work within your financial means, setting a realistic budget is crucial. Remember that you can always reduce the budget later on if you run into unforeseen problems. But, don't underestimate how much money you'll spend. You'll end up with less money after paying for other things if the cost is underestimated.
Production planning can be a complex process. However, once you know how everything works together it will become easier to plan future projects.
What are the 7 Rs of logistics.
The acronym 7R's for Logistics stands to represent the seven basic principles in logistics management. It was published in 2004 by the International Association of Business Logisticians as part of their "Seven Principles of Logistics Management" series.
The acronym consists of the following letters:
-
Responsive - ensure all actions are legal and not harmful to others.
-
Reliable - Have confidence in your ability to fulfill all of your commitments.
-
Be responsible - Use resources efficiently and avoid wasting them.
-
Realistic – consider all aspects of operations, from cost-effectiveness to environmental impact.
-
Respectful: Treat others with fairness and equity
-
Reliable - Find ways to save money and increase your productivity.
-
Recognizable is a company that provides customers with value-added solutions.
What is the distinction between Production Planning or Scheduling?
Production Planning (PP), or production planning, is the process by which you determine what products are needed at any given time. This is accomplished by forecasting the demand and identifying production resources.
Scheduling refers to the process of allocating specific dates to tasks in order that they can be completed within a specified timeframe.
Statistics
- According to the United Nations Industrial Development Organization (UNIDO), China is the top manufacturer worldwide by 2019 output, producing 28.7% of the total global manufacturing output, followed by the United States, Japan, Germany, and India.[52][53] (en.wikipedia.org)
- In the United States, for example, manufacturing makes up 15% of the economic output. (twi-global.com)
- It's estimated that 10.8% of the U.S. GDP in 2020 was contributed to manufacturing. (investopedia.com)
- [54][55] These are the top 50 countries by the total value of manufacturing output in US dollars for its noted year according to World Bank.[56] (en.wikipedia.org)
- Job #1 is delivering the ordered product according to specifications: color, size, brand, and quantity. (netsuite.com)
External Links
How To
How to use the Just-In Time Method in Production
Just-intime (JIT), which is a method to minimize costs and maximize efficiency in business process, is one way. This is where you have the right resources at the right time. This means you only pay what you use. Frederick Taylor developed the concept while working as foreman in early 1900s. He saw how overtime was paid to workers for work that was delayed. He then concluded that if he could ensure that workers had enough time to do their job before starting to work, this would improve productivity.
JIT is about planning ahead. You should have all the necessary resources ready to go so that you don’t waste money. Look at your entire project, from start to end. Make sure you have enough resources in place to deal with any unexpected problems. You'll be prepared to handle any potential problems if you know in advance. This way, you won't end up paying extra money for things that weren't really necessary.
There are different types of JIT methods:
-
Demand-driven JIT: You order the parts and materials you need for your project every other day. This will enable you to keep track of how much material is left after you use it. This will let you know how long it will be to produce more.
-
Inventory-based: You stock materials in advance to make your projects easier. This allows you to forecast how much you will sell.
-
Project-driven: This means that you have enough money to pay for your project. When you know how much you need, you'll purchase the appropriate amount of materials.
-
Resource-based JIT: This is the most popular form of JIT. You allocate resources based on the demand. You will, for example, assign more staff to deal with large orders. If you don't have many orders, you'll assign fewer people to handle the workload.
-
Cost-based : This is similar in concept to resource-based. But here, you aren't concerned about how many people your company has but how much each individual costs.
-
Price-based: This approach is very similar to the cost-based method except that you don't look at individual workers costs but the total cost of the company.
-
Material-based: This is quite similar to cost-based, but instead of looking at the total cost of the company, you're concerned with how much raw materials you spend on average.
-
Time-based JIT: A variation on resource-based JIT. Instead of focusing on the cost of each employee, you will focus on the time it takes to complete a project.
-
Quality-based JIT is another variant of resource-based JIT. Instead of focusing on the cost of each worker or how long it takes, think about how high quality your product is.
-
Value-based JIT: This is the latest form of JIT. In this instance, you are not concerned about the product's performance or meeting customer expectations. Instead, you focus on the added value that you provide to your market.
-
Stock-based. This method is inventory-based and focuses only on the actual production at any given point. This method is useful when you want to increase production while decreasing inventory.
-
Just-in-time planning (JIT): This is a combination JIT and supply-chain management. It refers to the process of scheduling the delivery of components as soon as they are ordered. It is essential because it reduces lead-times and increases throughput.