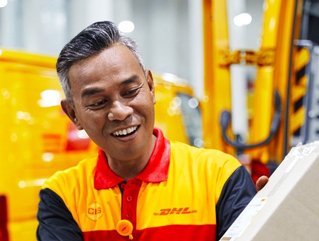
The state-by-state list shows a surprising trend. The top states are the ones you would expect to be there, like the southeastern. However, this trend is changing. Many states have shown that they can make tradeoffs between quality and cost to get the best deals. This trend shows there are many factors that influence a state’s ability to attract manufacturing jobs. So how do you choose the best place for your business?
Group Five
You've found the right place if you are looking for a state-by-state list of Group Five companies. The Group Five portfolio includes steel pipes and structural components as well as industrial engineering products. The company offers pipe design services. They offer the best price to quality ratio in steel thickness and grade. The company uses the latest CAD systems and computer finite analysis programs to ensure that the pipe design meets all of your needs.
Group Three
The United States Census Bureau estimates that there are about 50,000 manufacturers within Group Three. It has a low unemployment rate and a high rate economic growth. However it also has a low GDP growth rate. This is because the majority of manufacturers in this group have small businesses. These limitations aside, data can still be useful. Here is a list listing the top state manufacturers. Continue reading to find out more.
The three largest European manufacturers are Audi, Mercedes-Benz and BMW. Honda and Toyota have dropped to fifth and sixth, respectively. The Big Three title has been reclaimed by the Detroit Three. The following table lists these carmakers as well as their sales in each respective state. The link below will take you to the list of top-selling cars in each state. There are many models for these manufacturers, including SUVs, minivans, and midsize sedans.
FAQ
What does warehouse refer to?
A warehouse is a place where goods are stored until they are sold. It can be indoors or out. It may also be an indoor space or an outdoor area.
Why automate your warehouse
Modern warehousing is becoming more automated. E-commerce has brought increased demand for more efficient and quicker delivery times.
Warehouses have to be flexible to meet changing requirements. They must invest heavily in technology to do this. Automating warehouses has many benefits. Here are some reasons why it's worth investing in automation:
-
Increases throughput/productivity
-
Reduces errors
-
Improves accuracy
-
Safety Boosts
-
Eliminates bottlenecks
-
Allows companies scale more easily
-
Increases efficiency of workers
-
The warehouse can be viewed from all angles.
-
Enhances customer experience
-
Improves employee satisfaction
-
This reduces downtime while increasing uptime
-
Ensures quality products are delivered on time
-
Removing human error
-
It helps ensure compliance with regulations
How can we improve manufacturing efficiency?
The first step is to identify the most important factors affecting production time. The next step is to identify the most important factors that affect production time. If you aren't sure where to begin, think about the factors that have the greatest impact on production time. Once you identify them, look for solutions.
What kind of jobs are there in logistics?
There are many kinds of jobs available within logistics. Some of them are:
-
Warehouse workers – They load and unload pallets and trucks.
-
Transportation drivers – These drivers drive trucks and wagons to transport goods and pick up the goods.
-
Freight handlers – They sort and package freight at warehouses.
-
Inventory managers - They oversee the inventory of goods in warehouses.
-
Sales reps - They sell products and services to customers.
-
Logistics coordinators - They organize and plan logistics operations.
-
Purchasing agents - They purchase goods and services needed for company operations.
-
Customer service representatives are available to answer customer calls and emails.
-
Shipping clerks: They process shipping requests and issue bills.
-
Order fillers are people who fill orders based only on what was ordered.
-
Quality control inspectors (QCI) - They inspect all incoming and departing products for potential defects.
-
Others – There are many other types available in logistics. They include transport supervisors, cargo specialists and others.
What is the job of a production plan?
A production planner makes sure all project elements are delivered on schedule, within budget, as well as within the agreed scope. They also ensure the quality of the product and service meets the client's requirements.
What is it like to manage a logistics company?
It takes a lot of skills and knowledge to run a successful logistics business. Good communication skills are essential to effectively communicate with your suppliers and clients. You need to understand how to analyze data and draw conclusions from it. You will need to be able handle pressure well and work in stressful situations. You must be creative and innovative to develop new ideas to improve efficiency. You need to have strong leadership qualities to motivate team members and direct them towards achieving organizational goals.
You should also be organized and efficient to meet tight deadlines.
What is production planning?
Production planning is the process of creating a plan that covers all aspects of production. This includes scheduling, budgeting and crew, location, equipment, props, and more. This document ensures that everything is prepared and available when you are ready for shooting. You should also have information to ensure the best possible results on set. It should include information about shooting locations, casting lists, crew details, equipment requirements, and shooting schedules.
The first step is to outline what you want to film. You may have already decided where you would like to shoot, or maybe there are specific locations or sets that you want to use. Once you have identified the scenes and locations, you can start to determine which elements are required for each scene. One example is if you are unsure of the exact model you want but decide that you require a car. In this case, you could start looking up cars online to find out what models are available and then narrow your choices by choosing between different makes and models.
After you've found the perfect car, it's time to start thinking about adding extras. Do you have people who need to be seated in the front seat? Perhaps you have someone who needs to be able to walk around the back of your car. Perhaps you would like to change the interior colour from black to white. These questions will help guide you in determining the ideal look and feel for your car. You can also think about the type of shots you want to get. What type of shots will you choose? Maybe the engine or steering wheel is what you are looking to film. All of these things will help you identify the exact style of car you want to film.
Once you have determined all of the above, you can move on to creating a schedule. You can create a schedule that will outline when you must start and finish your shoots. Each day will include the time when you need to arrive at the location, when you need to leave and when you need to return home. Everyone knows exactly what they should do and when. If you need to hire extra staff, you can make sure you book them in advance. It is not worth hiring someone who won’t show up because you didn’t tell him.
Also, consider how many days you will be filming your schedule. Some projects take only a few days while others can last several weeks. You should consider whether you will need more than one shot per week when creating your schedule. Multiple takes at the same place will result in higher costs and longer completion times. It's better to be safe than sorry and shoot less takes if you're not certain whether you need more takes.
Budgeting is another important aspect of production planning. Setting a realistic budget is essential as it will allow you to work within your means. If you have to reduce your budget due to unexpected circumstances, you can always lower it later. It is important to not overestimate how much you will spend. Underestimating the cost will result in less money after you have paid for other items.
Production planning is a detailed process. But, once you understand the workings of everything, it becomes easier for future projects to be planned.
Statistics
- According to a Statista study, U.S. businesses spent $1.63 trillion on logistics in 2019, moving goods from origin to end user through various supply chain network segments. (netsuite.com)
- You can multiply the result by 100 to get the total percent of monthly overhead. (investopedia.com)
- According to the United Nations Industrial Development Organization (UNIDO), China is the top manufacturer worldwide by 2019 output, producing 28.7% of the total global manufacturing output, followed by the United States, Japan, Germany, and India.[52][53] (en.wikipedia.org)
- In 2021, an estimated 12.1 million Americans work in the manufacturing sector.6 (investopedia.com)
- (2:04) MTO is a production technique wherein products are customized according to customer specifications, and production only starts after an order is received. (oracle.com)
External Links
How To
How to Use the Just In Time Method in Production
Just-in-time (JIT) is a method that is used to reduce costs and maximize efficiency in business processes. This is where you have the right resources at the right time. This means that only what you use is charged to your account. Frederick Taylor was the first to coin this term. He developed it while working as a foreman during the early 1900s. He observed how workers were paid overtime if there were delays in their work. He decided to ensure workers have enough time to do their jobs before starting work to improve productivity.
JIT teaches you to plan ahead and prepare everything so you don’t waste time. You should also look at the entire project from start to finish and make sure that you have sufficient resources available to deal with any problems that arise during the course of your project. You can anticipate problems and have enough equipment and people available to fix them. This way, you won't end up paying extra money for things that weren't really necessary.
There are many JIT methods.
-
Demand-driven: This is a type of JIT where you order the parts/materials needed for your project regularly. This will allow you to track how much material you have left over after using it. It will also allow you to predict how long it takes to produce more.
-
Inventory-based: This is a type where you stock the materials required for your projects in advance. This allows you predict the amount you can expect to sell.
-
Project-driven : This is a method where you make sure that enough money is set aside to pay the project's cost. You will be able to purchase the right amount of materials if you know what you need.
-
Resource-based JIT: This is the most popular form of JIT. Here you can allocate certain resources based purely on demand. For example, if there is a lot of work coming in, you will have more people assigned to them. You'll have fewer orders if you have fewer.
-
Cost-based: This is the same as resource-based except that you don't care how many people there are but how much each one of them costs.
-
Price-based pricing: This is similar in concept to cost-based but instead you look at how much each worker costs, it looks at the overall company's price.
-
Material-based: This is very similar to cost-based but instead of looking at total costs of the company you are concerned with how many raw materials you use on an average.
-
Time-based JIT: This is another variant of resource-based JIT. Instead of focusing solely on the amount each employee costs, focus on how long it takes for the project to be completed.
-
Quality-based JIT - This is another form of resource-based JIT. Instead of thinking about how much each employee costs or how long it takes to manufacture something, you think about how good the quality of your product is.
-
Value-based JIT is the newest form of JIT. In this scenario, you're not concerned about how products perform or whether customers expect them to meet their expectations. Instead, you focus on the added value that you provide to your market.
-
Stock-based: This stock-based method focuses on the actual quantity of products being made at any given time. It is used when production goals are met while inventory is kept to a minimum.
-
Just-in time (JIT), planning: This is a combination JIT/supply chain management. It's the process of scheduling delivery of components immediately after they are ordered. This is important as it reduces lead time and increases throughput.