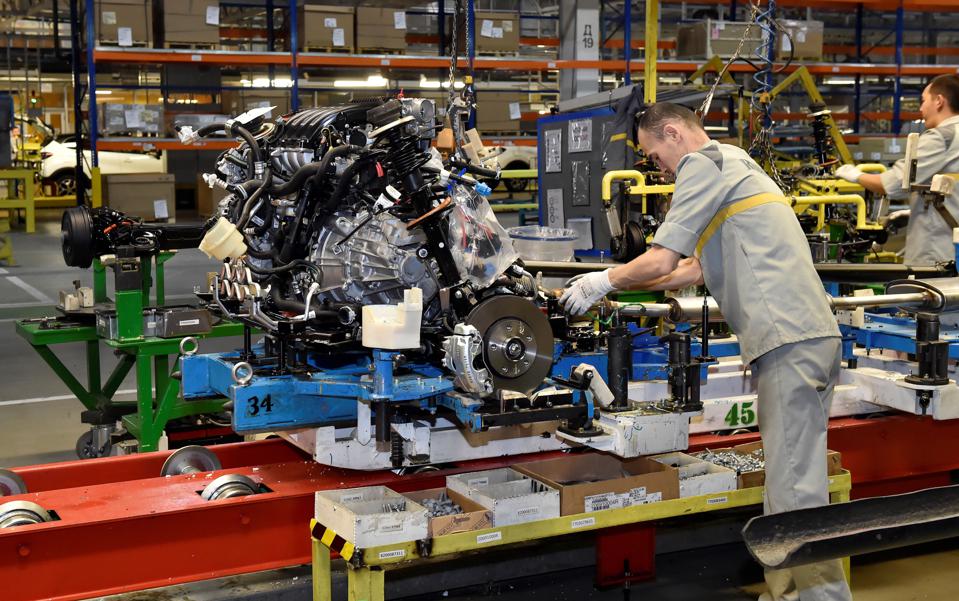
Typically, tool and die makers work in machine shops. They are responsible for operating lathes, milling machines, as well as other types of machine tools. They can also repair dies and tools for machinists. They may also design and manufacture tools for customers.
Tool and diemakers are required to adhere to high quality standards and maintain precision in their work. They test the accuracy of their work and examine finished items. Engineers might work with tool and die makers to improve processes. To see the tool in action, they may visit a customer's facility. They are required to keep their work space clean and organized. They may also wear protective gear. They might suggest new tools that make the process easier.
Tool and die-makers typically work 40 hours per week. They may also be expected moderately to heavy lifting. A solid educational background is required. Employers prefer associate's or bachelors degrees in related fields. They might also receive training on-the-job or apprentice programs.
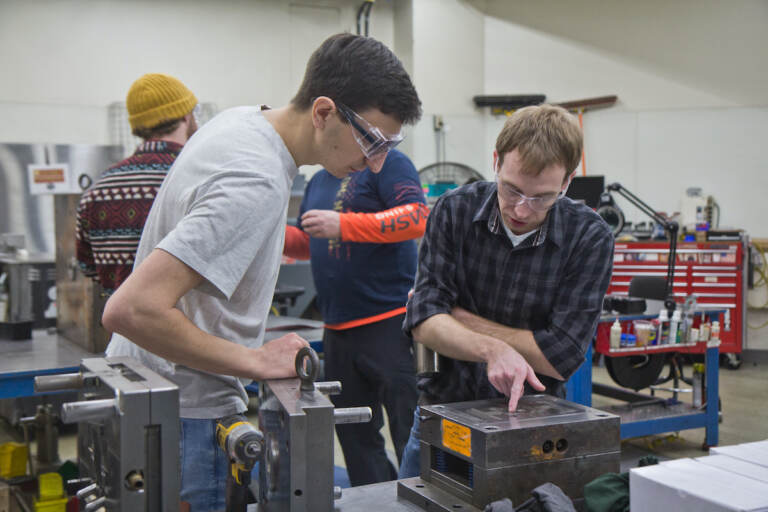
Four-year apprenticeship programs for tool and diemakers are typically offered by employers. They receive training on the job from an experienced worker during their apprenticeship program. They also attend technical college courses at night. This program offers both classroom instruction and hands-on training. They also may have the opportunity to perform computer-controlled machine tool programming. They could also be promoted to supervisory roles.
The majority of tool and diemakers hold a high-school diploma or an equivalent. They may also have a degree in a technical field, such as physics or engineering. They may also have some prior training in science or math. This training can be very helpful.
Good eyesight is crucial for tool and die-makers. They also need to have patience and focus. They also need physical strength to handle machinery. They should also have a strong work ethic. They should be capable of reading engineering drawings and specifications. They should also have excellent interpersonal skills. They should also be able to use computers effectively. They may also be required to maintain computer numerically controlled (CNC) machines.
The analytical mind of tool and die-makers is crucial. They need to know how tools and their functions work, as well as how to repair them. They should also possess problem-solving and mechanical skills. They may need to learn new techniques in machining. They should have substantial digital skills, such as computer-aided design (CAD) and computer-aided manufacturing (CAM) software. They should also be skilled in sales. They must be able work with and independently.
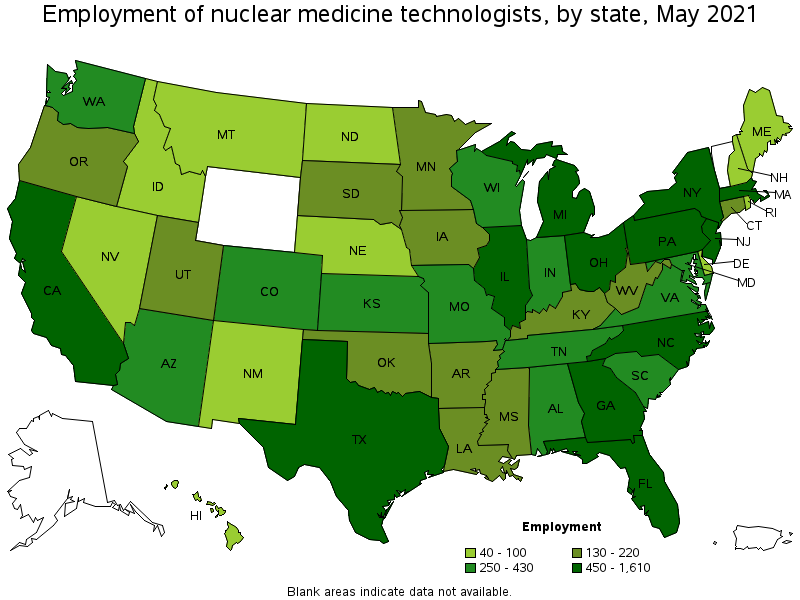
Apprentices usually work 40 hours per week in an apprenticeship program. They are required to attend school at night and do a job during work hours. They are eventually able to take on more difficult assignments. An apprenticeship requires a high-school diploma or equivalent. They should also take courses on science and math.
Some tool and diemakers go on to get a master's or bachelor's degree. Average income for tool and denter makers is $56,186. Automation is expected to reduce their employment prospects.
FAQ
What does manufacturing industry mean?
Manufacturing Industries is a group of businesses that produce goods for sale. These products are sold to consumers. These companies employ many processes to achieve this purpose, such as production and distribution, retailing, management and so on. They produce goods from raw materials by using machines and other machinery. This includes all types of manufactured goods, including food items, clothing, building supplies, furniture, toys, electronics, tools, machinery, vehicles, pharmaceuticals, medical devices, chemicals, and many others.
What does it take to run a logistics business?
To run a successful logistics company, you need a lot knowledge and skills. To communicate effectively with clients and suppliers, you must be able to communicate well. You need to understand how to analyze data and draw conclusions from it. You must be able manage stress and pressure under pressure. You must be creative and innovative to develop new ideas to improve efficiency. Strong leadership qualities are essential to motivate your team and help them achieve their organizational goals.
You must be organized to meet tight deadlines.
What are the 4 types manufacturing?
Manufacturing refers to the transformation of raw materials into useful products by using machines and processes. It can involve many activities like designing, manufacturing, testing packaging, shipping, selling and servicing.
How can we increase manufacturing efficiency?
The first step is to determine the key factors that impact production time. We must then find ways that we can improve these factors. If you don’t know where to begin, consider which factors have the largest impact on production times. Once you've identified them all, find solutions to each one.
What type of jobs is there in logistics
There are different kinds of jobs available in logistics. Here are some:
-
Warehouse workers - They load trucks and pallets.
-
Transportation drivers – They drive trucks or trailers to transport goods and perform pick-ups.
-
Freight handlers, - They sort out and pack freight in warehouses.
-
Inventory managers: They are responsible for the inventory and management of warehouses.
-
Sales representatives: They sell products to customers.
-
Logistics coordinators - They plan and organize logistics operations.
-
Purchasing agents - They buy goods and services that are necessary for company operations.
-
Customer service representatives - Answer calls and email from customers.
-
Ship clerks - They issue bills and process shipping orders.
-
Order fillers are people who fill orders based only on what was ordered.
-
Quality control inspectors (QCI) - They inspect all incoming and departing products for potential defects.
-
Others - There are many types of jobs in logistics such as transport supervisors and cargo specialists.
Statistics
- Many factories witnessed a 30% increase in output due to the shift to electric motors. (en.wikipedia.org)
- According to a Statista study, U.S. businesses spent $1.63 trillion on logistics in 2019, moving goods from origin to end user through various supply chain network segments. (netsuite.com)
- (2:04) MTO is a production technique wherein products are customized according to customer specifications, and production only starts after an order is received. (oracle.com)
- In the United States, for example, manufacturing makes up 15% of the economic output. (twi-global.com)
- According to the United Nations Industrial Development Organization (UNIDO), China is the top manufacturer worldwide by 2019 output, producing 28.7% of the total global manufacturing output, followed by the United States, Japan, Germany, and India.[52][53] (en.wikipedia.org)
External Links
How To
How to use lean manufacturing in the production of goods
Lean manufacturing (or lean manufacturing) is a style of management that aims to increase efficiency, reduce waste and improve performance through continuous improvement. It was developed by Taiichi Okono in Japan, during the 1970s & 1980s. TPS founder Kanji Takoda awarded him the Toyota Production System Award (TPS). Michael L. Watkins published the "The Machine That Changed the World", the first book about lean manufacturing. It was published in 1990.
Lean manufacturing is often defined as a set of principles used to improve the quality, speed, and cost of products and services. It emphasizes reducing defects and eliminating waste throughout the value chain. Lean manufacturing is also known as just in time (JIT), zero defect total productive maintenance(TPM), and five-star (S). Lean manufacturing is about eliminating activities that do not add value, such as inspection, rework, and waiting.
Lean manufacturing can help companies improve their product quality and reduce costs. Additionally, it helps them achieve their goals more quickly and reduces employee turnover. Lean manufacturing has been deemed one of the best ways to manage the entire value-chain, including customers, distributors as well retailers and employees. Lean manufacturing is widely practiced in many industries around the world. For example, Toyota's philosophy underpins its success in automobiles, electronics, appliances, healthcare, chemical engineering, aerospace, paper, food, etc.
Lean manufacturing is based on five principles:
-
Define Value - Determine the value that your business brings to society. Also, identify what sets you apart from your competitors.
-
Reduce Waste – Eliminate all activities that don't add value throughout the supply chain.
-
Create Flow. Ensure that your work is uninterrupted and flows seamlessly.
-
Standardize and simplify - Make your processes as consistent as possible.
-
Build Relationships - Establish personal relationships with both internal and external stakeholders.
Lean manufacturing is not a new concept, but it has been gaining popularity over the last few years due to a renewed interest in the economy following the global financial crisis of 2008. Many companies have adopted lean manufacturing methods to increase their marketability. In fact, some economists believe that lean manufacturing will be an important factor in economic recovery.
Lean manufacturing has many benefits in the automotive sector. These include better customer satisfaction and lower inventory levels. They also result in lower operating costs.
Any aspect of an enterprise can benefit from Lean manufacturing. It is especially useful for the production aspect of an organization, as it ensures that every step in the value chain is efficient and effective.
There are three types principally of lean manufacturing:
-
Just-in-Time Manufacturing (JIT): This type of lean manufacturing is commonly referred to as "pull systems." JIT stands for a system where components are assembled on the spot rather than being made in advance. This approach aims to reduce lead times, increase the availability of parts, and reduce inventory.
-
Zero Defects Manufacturing (ZDM): ZDM focuses on ensuring that no defective units leave the manufacturing facility. It is better to repair a part than have it removed from the production line if it needs to be fixed. This applies to finished products, which may need minor repairs before they are shipped.
-
Continuous Improvement (CI),: Continuous improvement aims improve the efficiency and effectiveness of operations by continuously identifying issues and making changes to reduce waste. Continuous improvement involves continuous improvement of processes and people as well as tools.