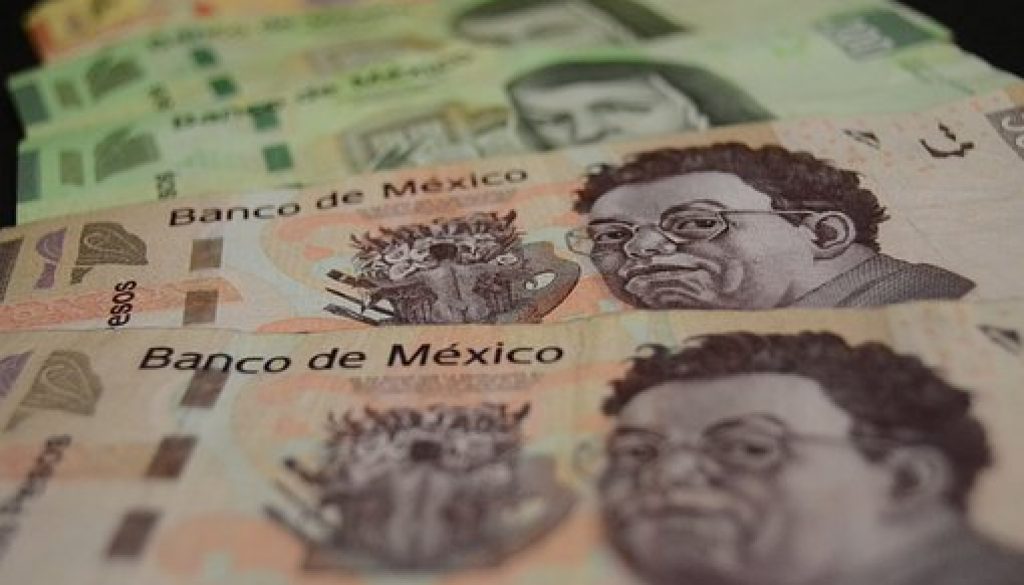
The National Network for Manufacturing Innovation's primary goal is to develop cutting-edge manufacturing technologies. President Obama announced the interagency initiative in his FY 2013 budget proposal. This interagency initiative is designed to bring together federal agencies, community colleges, university engineering schools and other institutions in order to commercialize new manufacturing technologies.
The United States' manufacturing sector plays a crucial role in the country's economy. American workers have access to good jobs in this sector. To stay competitive, manufacturing firms invest in technological innovations that increase productivity and reduce labor costs. Automation and green energy are two examples of these innovations. Companies invest in machine-downtime solutions. These innovative products include autonomous mobile robots that reduce labor costs and increase productivity. In addition, companies are investing in technologies that reduce resource wastage, such as smart sensors.
The "Maker's Economy," a new model for product manufacturing, is expected revolutionize how it works. This economy involves manufacturing users taking an active role when designing and building new products. It uses readily available technologies. These innovations are expected by the manufacturing sector, which is expected to benefit from them to increase productivity and operational efficiency as well as enhance decision-making. It is also expected that it will be a significant contributor to the nation’s overall productivity. The United States has a long history of being a world leader for manufacturing.
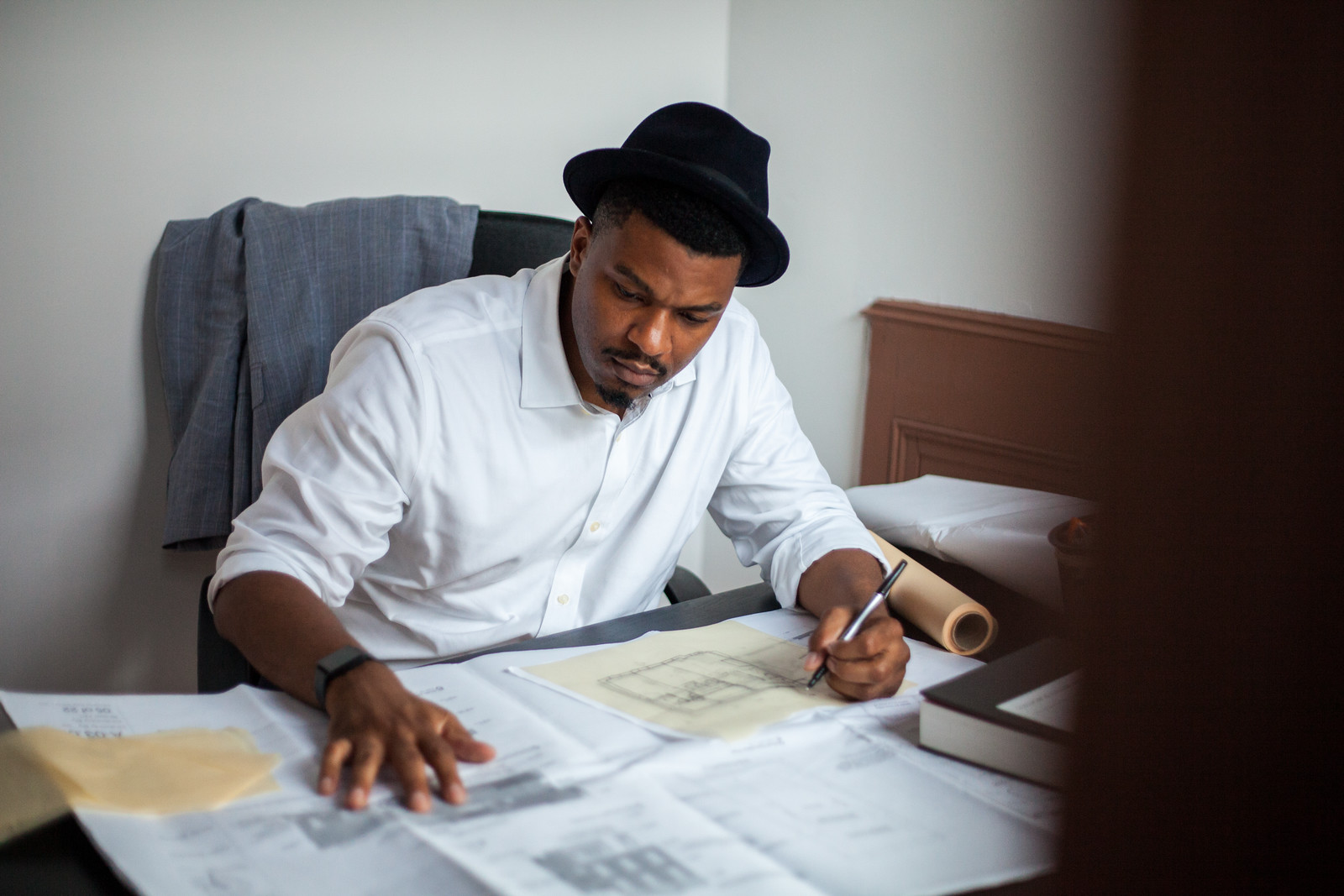
The "Maker's Economy" relies on a variety of technologies, including smart factories and artificial intelligence. These innovations help improve manufacturing productivity, increasing worker efficiency and decreasing time to produce products. The Industrial Internet of Things (IIoT), which uses sensors and data, helps to guide tasks. It also monitors industrial assets continuously. Secure connectivity and fast data transfer are also required for IIoT. It is also expected that it will increase warehouse efficiency and supply chain visibility.
The National Network for Manufacturing Innovation (NNNMI) will be composed of at minimum fifteen manufacturing institutes. This network is expected to assist in the rapid development of new manufacturing technologies. The network will also include public/private partnership from both government entities and private businesses.
There are currently fourteen manufacturing innovation centers in the United States. Three more will be funded by Commerce Department in May 2013. Two Institutes are expected to be funded in part by the National Institute of Standards and Technology. The total funding for each institute will be up to $70 millions over the course of five to seven year.
The Institutes for Manufacturing Innovation will each have a unique research concentration. They will act as hubs of manufacturing innovation for both state and local economies. These Institutes will be able to assist manufacturers with their integration efforts. These institutes offer access to cutting edge technology and will also provide training opportunities for workers. These institutes will also assist manufacturers in solving cross-cutting challenges in advanced production.
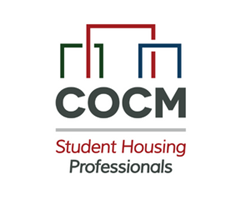
The Network for Manufacturing Innovation is a broad-based program that aims at accelerating the commercialization, application and transfer of innovative manufacturing technologies. It also seeks to strengthen the state's and local economies. The U.S. Department of Energy, which will operate the institutes, will fund the program through the U.S. Commerce Department’s National Institute of Standards and Technology.
FAQ
How can excess manufacturing production be reduced?
Better inventory management is key to reducing excess production. This would reduce the amount of time spent on unnecessary activities such as purchasing, storing, and maintaining excess stock. By doing this, we could free up resources for other productive tasks.
This can be done by using a Kanban system. A Kanban board, a visual display to show the progress of work, is called a Kanban board. Kanban systems allow work items to move through different states until they reach their final destination. Each state represents a different priority.
When work is completed, it can be transferred to the next stage. It is possible to keep a task in the beginning stages until it gets to the end.
This helps to keep work moving forward while ensuring that no work is left behind. A Kanban board allows managers to monitor how much work is being completed at any given moment. This information allows them to adjust their workflow based on real-time data.
Lean manufacturing is another way to manage inventory levels. Lean manufacturing is about eliminating waste from all stages of the production process. Anything that does nothing to add value to a product is waste. The following are examples of common waste types:
-
Overproduction
-
Inventory
-
Unnecessary packaging
-
Exceed materials
Manufacturers can increase efficiency and decrease costs by implementing these ideas.
What are the 7 Rs of logistics management?
The acronym 7R's of Logistic is an acronym that stands for seven fundamental principles of logistics management. It was developed and published by the International Association of Business Logisticians in 2004 as part of the "Seven Principles of Logistics Management".
The following letters form the acronym:
-
Responsive - ensure all actions are legal and not harmful to others.
-
Reliable - have confidence in the ability to deliver on commitments made.
-
Use resources effectively and sparingly.
-
Realistic - consider all aspects of operations, including cost-effectiveness and environmental impact.
-
Respectful: Treat others with fairness and equity
-
Resourceful - look for opportunities to save money and increase productivity.
-
Recognizable provides value-added products and services to customers
What kind of jobs are there in logistics?
There are different kinds of jobs available in logistics. Here are some examples:
-
Warehouse workers: They load and unload trucks, pallets, and other cargo.
-
Transportation drivers – They drive trucks or trailers to transport goods and perform pick-ups.
-
Freight handlers are people who sort and pack freight into warehouses.
-
Inventory managers - They oversee the inventory of goods in warehouses.
-
Sales reps - They sell products and services to customers.
-
Logistics coordinators are responsible for organizing and planning logistics operations.
-
Purchasing agents - They purchase goods and services needed for company operations.
-
Customer service representatives – They answer emails and phone calls from customers.
-
Shipping clerks – They process shipping orders, and issue bills.
-
Order fillers: They fill orders based off what has been ordered and shipped.
-
Quality control inspectors – They inspect incoming and outgoing products to ensure that there are no defects.
-
Others – There are many other types available in logistics. They include transport supervisors, cargo specialists and others.
Statistics
- According to a Statista study, U.S. businesses spent $1.63 trillion on logistics in 2019, moving goods from origin to end user through various supply chain network segments. (netsuite.com)
- Many factories witnessed a 30% increase in output due to the shift to electric motors. (en.wikipedia.org)
- You can multiply the result by 100 to get the total percent of monthly overhead. (investopedia.com)
- In the United States, for example, manufacturing makes up 15% of the economic output. (twi-global.com)
- It's estimated that 10.8% of the U.S. GDP in 2020 was contributed to manufacturing. (investopedia.com)
External Links
How To
How to Use the 5S to Increase Productivity In Manufacturing
5S stands for "Sort", "Set In Order", "Standardize", "Separate" and "Store". Toyota Motor Corporation developed the 5S method in 1954. It assists companies in improving their work environments and achieving higher efficiency.
The basic idea behind this method is to standardize production processes, so they become repeatable, measurable, and predictable. Cleaning, sorting and packing are all done daily. Because workers know what they can expect, this helps them perform their jobs more efficiently.
There are five steps that you need to follow in order to implement 5S. Each step requires a different action, which increases efficiency. You can make it easy for people to find things later by sorting them. You arrange items by placing them in an order. Once you have separated your inventory into groups and organized them, you will store these groups in easily accessible containers. You can also label your containers to ensure everything is properly labeled.
Employees need to reflect on how they do their jobs. Employees should understand why they do the tasks they do, and then decide if there are better ways to accomplish them. In order to use the 5S system effectively, they must be able to learn new skills.
In addition to improving efficiency, the 5S system also increases morale and teamwork among employees. They feel more motivated to work towards achieving greater efficiency as they see the results.