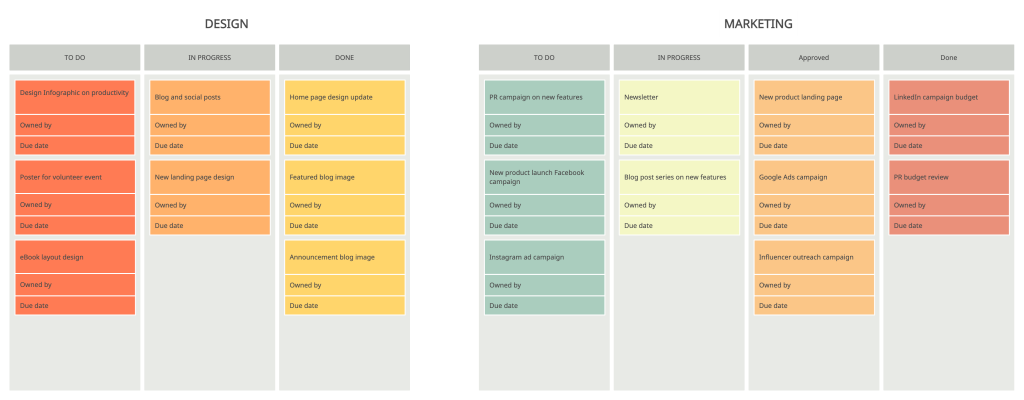
A job director is responsible for job manufacturing. The responsibilities and duties of a job manager are the same as those of a manufacturing associate. This article will discuss the qualifications for a job director of manufacturing. This job requires a highly skilled workforce to complete various operations. In addition, it is important to have erratic workflow, as it will help manage projects and track development. This type of production line requires a highly skilled workforce, as it requires employees who are able to keep up with the pace and deliver quality products on time.
The job of a job director in manufacturing
The duties of a job director of manufacturing include managing the daily operations of a manufacturing unit. They are responsible to ensure that products meet the highest standards and are completed on-time. A director of manufacturing must work closely with engineers and designers to create a new product. Before the product can be put into mass-production, they need to evaluate its marketability, feasibility, and impact on quality and process. Also, a director in manufacturing must be able to demonstrate leadership skills. They should be able supervise workers and implement process and equipment improvements.
Directors of manufacturing generally hold a bachelor’s degree. However, many employers prefer to hire candidates with advanced degrees. Directors of manufacturing need to have at most five years' experience in management. Candidates should have the ability to adapt to a steep learning curve.
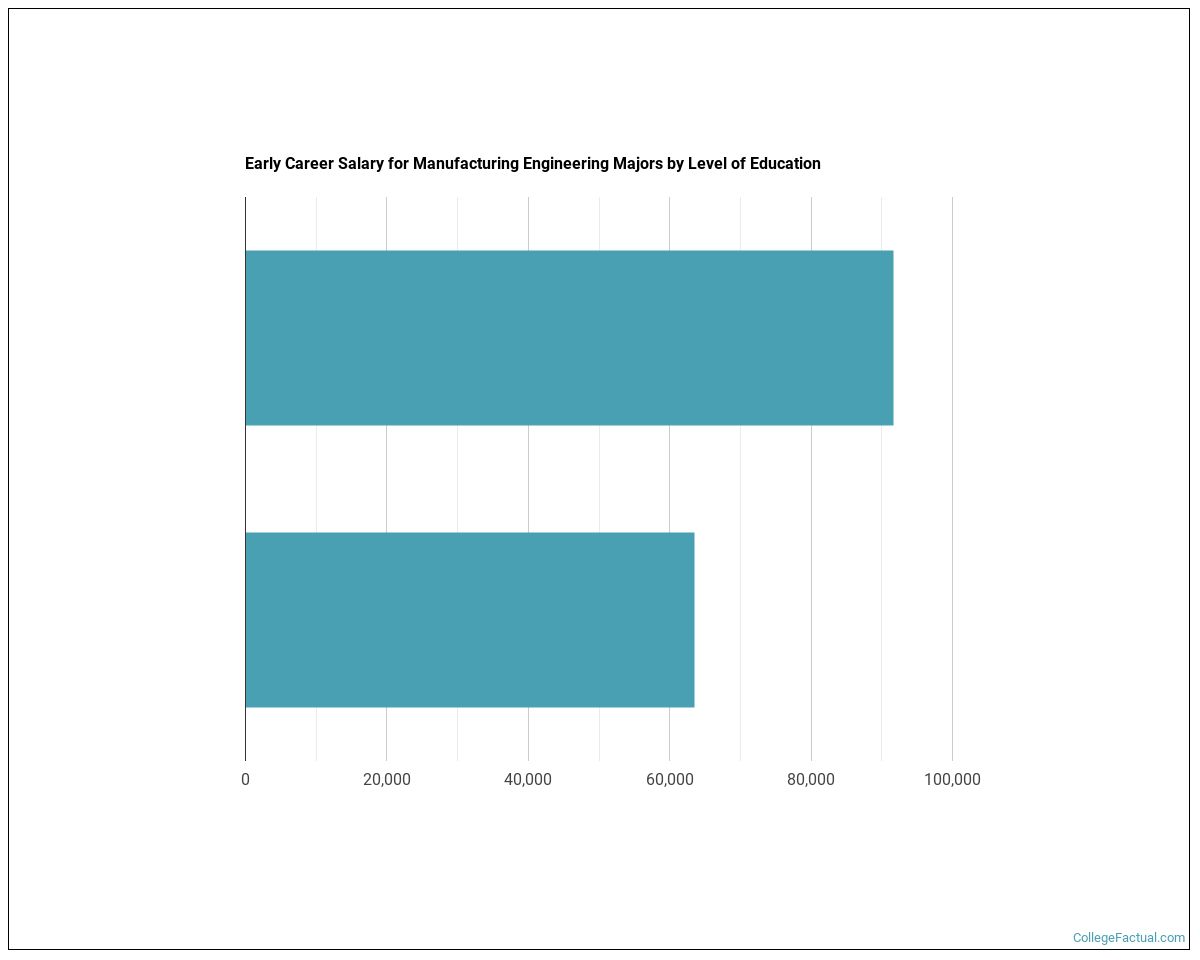
Assistant in manufacturing
Although the duties of a manufacturing associate are varied, they often involve repetitive motions and assembly line work. To avoid injury, associates should exercise proper body mechanics and stay in good physical condition. They may also have to lift heavy materials or stand for long periods of time.
Duties of a manufacturing associate can range from inspecting parts to reading engineering drawings and executing manufacturing documents. They must also coordinate with the other members of their team and produce reports. As a result, they need to be organized, detail-oriented, good communicators, and have previous experience in manufacturing.
Maintaining quality control over manufactured products is another major responsibility. They must have a good understanding of the manufacturing process and must be able check whether products comply with company standards. In addition, they must observe finished products and identify any defects that may affect the quality.
Qualifications required to become a job-director in manufacturing
As a director in manufacturing, you will be responsible for all operations within a unit. This includes creating schedules and overseeing production. This job requires you to maintain high standards of manufacturing quality and to implement new and improved techniques to lower costs. In addition, you will also be responsible for evaluating the performance of all staff members. A job title as director of manufacturing requires leadership, organizational skills, problem solving, and knowledge of the production processes.
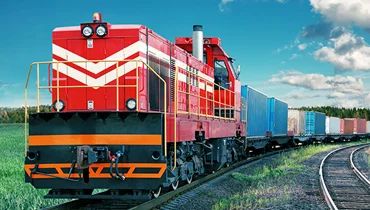
As a manufacturing director, you will work with engineers and designers to develop products and services for a company. Excellent communication skills are essential to ensure that everyone in the company is on the right page and understands their respective roles. If you are able to communicate well, you will be able to effectively oversee the entire company. A director of manufacturing will also need to be a mentor and coach for employees. Training employees on safety protocols and risk mitigation will be a requirement.
FAQ
How is a production manager different from a producer planner?
The main difference between a production planner and a project manager is that a project manager is usually the person who plans and organizes the entire project, whereas a production planner is mainly involved in the planning stage of the project.
What does it mean to be a manufacturer?
Manufacturing Industries are businesses that produce products for sale. These products are sold to consumers. These companies use various processes such as production, distribution, retailing, management, etc., to fulfill this purpose. These companies produce goods using raw materials and other equipment. This includes all types and varieties of manufactured goods, such as food items, clothings, building supplies, furnitures, toys, electronics tools, machinery vehicles, pharmaceuticals medical devices, chemicals, among others.
What does "warehouse" mean?
A warehouse or storage facility is where goods are stored before they are sold. It can be either an indoor or outdoor space. In some cases, it may be a combination of both.
What is the role and responsibility of a Production Planner?
Production planners ensure that all project aspects are completed on time, within budget and within the scope. They make sure that the product and services meet client expectations.
Statistics
- Many factories witnessed a 30% increase in output due to the shift to electric motors. (en.wikipedia.org)
- In the United States, for example, manufacturing makes up 15% of the economic output. (twi-global.com)
- According to the United Nations Industrial Development Organization (UNIDO), China is the top manufacturer worldwide by 2019 output, producing 28.7% of the total global manufacturing output, followed by the United States, Japan, Germany, and India.[52][53] (en.wikipedia.org)
- (2:04) MTO is a production technique wherein products are customized according to customer specifications, and production only starts after an order is received. (oracle.com)
- It's estimated that 10.8% of the U.S. GDP in 2020 was contributed to manufacturing. (investopedia.com)
External Links
How To
How to use the Just In-Time Production Method
Just-in-time (JIT) is a method that is used to reduce costs and maximize efficiency in business processes. It allows you to get the right amount resources at the right time. This means that you only pay the amount you actually use. Frederick Taylor was the first to coin this term. He developed it while working as a foreman during the early 1900s. Taylor observed that overtime was paid to workers if they were late in working. He concluded that if workers were given enough time before they start work, productivity would increase.
JIT is about planning ahead. You should have all the necessary resources ready to go so that you don’t waste money. You should also look at the entire project from start to finish and make sure that you have sufficient resources available to deal with any problems that arise during the course of your project. If you anticipate that there might be problems, you'll have enough people and equipment to fix them. This will prevent you from spending extra money on unnecessary things.
There are many JIT methods.
-
Demand-driven: This JIT is where you place regular orders for the parts/materials that are needed for your project. This will allow you to track how much material you have left over after using it. This will let you know how long it will be to produce more.
-
Inventory-based: This allows you to store the materials necessary for your projects in advance. This allows you to predict how much you can expect to sell.
-
Project-driven: This is an approach where you set aside enough funds to cover the cost of your project. If you know the amount you require, you can buy the materials you need.
-
Resource-based JIT: This is the most popular form of JIT. Here, you allocate certain resources based on demand. If you have many orders, you will assign more people to manage them. If you don't receive many orders, then you'll assign fewer employees to handle the load.
-
Cost-based : This is similar in concept to resource-based. But here, you aren't concerned about how many people your company has but how much each individual costs.
-
Price-based: This is similar to cost-based but instead of looking at individual workers' salaries, you look at the total company price.
-
Material-based: This is very similar to cost-based but instead of looking at total costs of the company you are concerned with how many raw materials you use on an average.
-
Time-based: This is another variation of resource-based JIT. Instead of focusing solely on the amount each employee costs, focus on how long it takes for the project to be completed.
-
Quality-based: This is yet another variation of resource-based JIT. Instead of thinking about how much each employee costs or how long it takes to manufacture something, you think about how good the quality of your product is.
-
Value-based: This is one of the newest forms of JIT. In this scenario, you're not concerned about how products perform or whether customers expect them to meet their expectations. Instead, your goal is to add value to the market.
-
Stock-based: This stock-based method focuses on the actual quantity of products being made at any given time. This method is useful when you want to increase production while decreasing inventory.
-
Just-in time (JIT), planning: This is a combination JIT/supply chain management. It's the process of scheduling delivery of components immediately after they are ordered. This is important as it reduces lead time and increases throughput.