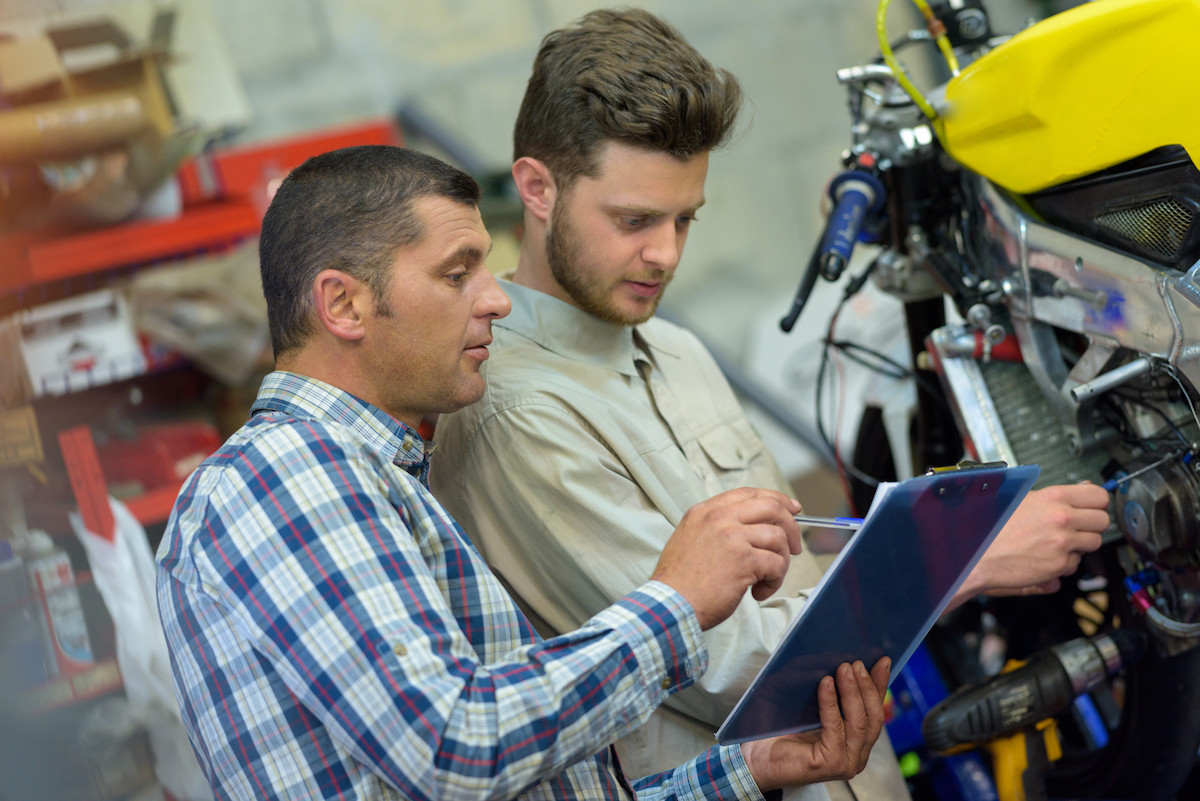
Industrial management is a field of engineering where various engineering processes are integrated to create an effective management system. These engineering processes are integrated into an integrated management system by the industrial manager. Here are some things you should know about the job. Listed below are some benefits and requirements for becoming an industrial manager. This career is for you if your qualifications are up-to-date and you're looking for a rewarding and challenging job. Continue reading to find out more.
Job description
An industrial manager oversees all aspects of the production process. Although the job is broad, it may also cover specific aspects such as how to source raw materials and use equipment. As computers play an increasingly important role in the coordination between different departments, suppliers, customers, and employees, industrial production managers need to be computer-literate. Industrial production managers should be knowledgeable about the latest management techniques and production technologies. Managers are often involved in professional organizations and attend trade shows and industry conferences. They also take courses to become certified in their fields.
Industrial managers coordinate activities across a company's departments. They ensure that production lines are productive and meet customer expectations in terms both quality and speed. They may also supervise staffing levels or change production levels as required to minimize inventory. They might also coordinate with other departments and oversee quality control programs. The majority of this job involves managing people.
Education necessary
It is not necessary to have a bachelor's in management, business, or engineering to become an industrial manager. Employers will prefer candidates who have a background in one or more of these fields. Industrial managers also need to be computer literate. Computers are increasingly becoming a crucial part of the manufacturing process, helping coordinate production across departments, suppliers, and clients. Interested individuals should obtain the proper education and experience to excel in this field.
Many industrial production managers started their careers as production workers before moving up to the first-line supervisory position. Professionals must have a business management degree to become industrial managers. However, there are some workers who can get this education on the jobs. Or they might choose to go to classes sponsored and paid by their company. Most managers will need to have between two and five years of relevant work experience before they are qualified to become managers.
Potential earning
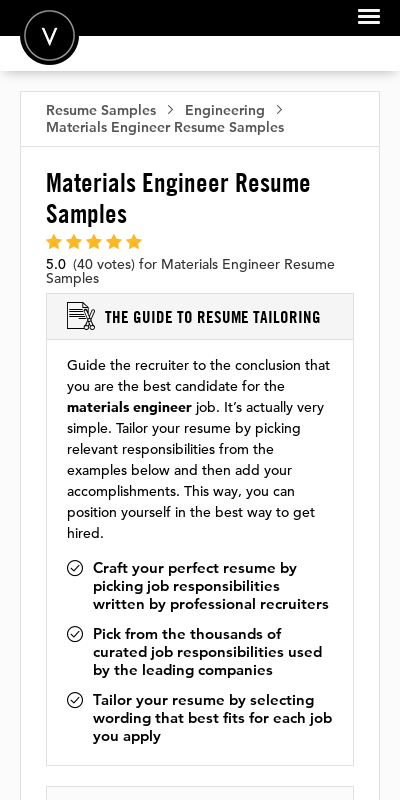
In manufacturing plants, industrial managers oversee the smooth running of the entire operation. They help to determine the best use of employees and equipment, establish production standards, and make strategic and tactical decisions. Their duties include hiring and evaluating workers, setting production schedules, and ensuring that safety procedures are followed. They are responsible for overseeing the day-to-day operations of a team and constantly analyzing the production process to ensure it is running efficiently and at peak performance.
The ability to earn an industrial production manager's salary depends on the experience of the worker and the employer. Although it's hard for anyone to predict what the future earnings will be, the median industrial manager salary was $103,380 as of May 2016. The highest paid industrial production workers earned $172,000. Higher earnings may also be available for industrial production managers who have completed advanced training or certification. According to U.S. Bureau of Labor Statistics, those who have earned a bachelor’s or higher in industrial production management can earn more.
Work environment
An industrial production manager divides his or her time between the production floor and an office, often in the same building. When working in a manufacturing area, industrial production manager must follow established health and safety protocols and use the proper protective equipment. They often spend significant time in meetings and analysis of production data. Reports may be written by these managers. An industrial production manager's work environment can be dynamic.
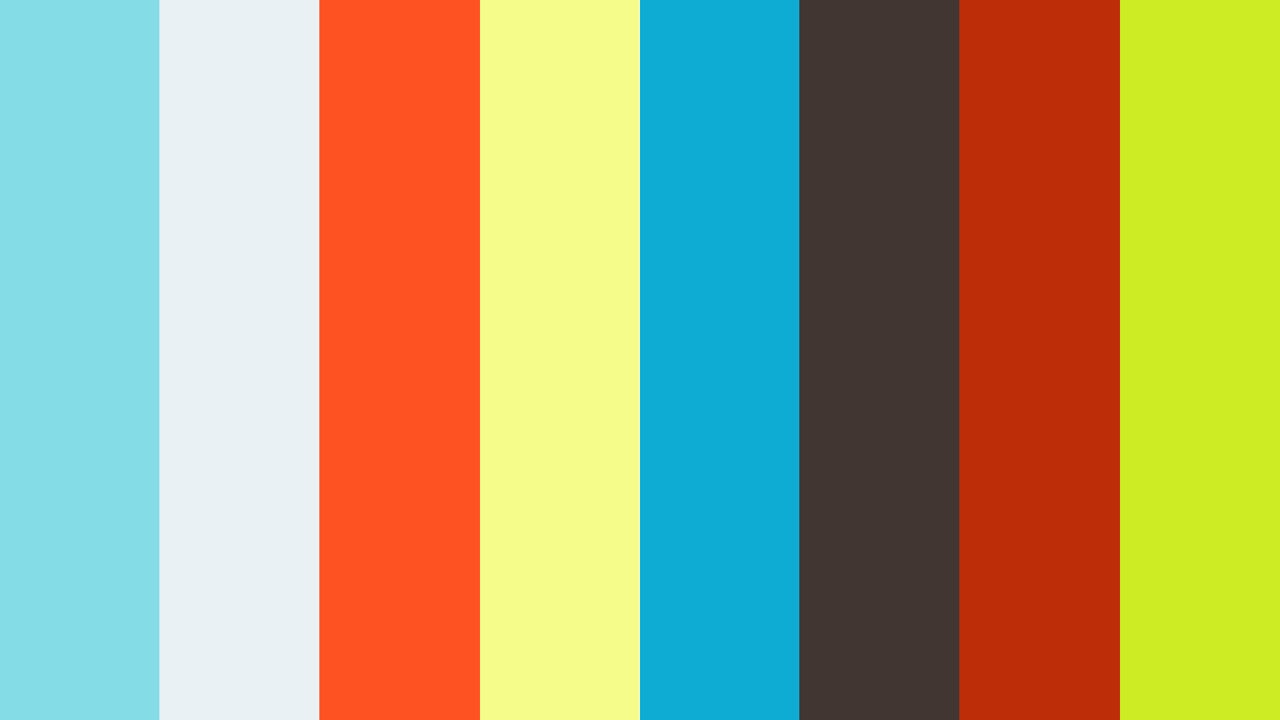
As part of a business's management structure, industrial production managers have many responsibilities. They must coordinate the activities of various workers and increase productivity. A primary responsibility of an industrial production manager is increasing productivity and ensuring safety. Because of corporate restructuring, many levels of management have been eliminated and support staff have been reduced, leaving more of the workload to production managers. This is a serious challenge for any manager and can make the job of a production manager difficult.
FAQ
Can we automate some parts of manufacturing?
Yes! Yes! Automation has existed since ancient times. The Egyptians invented the wheel thousands of years ago. Robots are now used to assist us in assembly lines.
Actually, robotics can be used in manufacturing for many purposes. These include:
-
Line robots
-
Robot welding
-
Robot painting
-
Robotics inspection
-
Robots that make products
Manufacturing can also be automated in many other ways. 3D printing is a way to make custom products quickly and without waiting weeks or months for them to be manufactured.
What is the importance of logistics in manufacturing?
Logistics are an essential component of any business. They are essential to any business's success.
Logistics also play a major role in reducing costs and increasing efficiency.
How can manufacturing efficiency improved?
The first step is to determine the key factors that impact production time. The next step is to identify the most important factors that affect production time. If you don’t know where to begin, consider which factors have the largest impact on production times. Once you have identified the factors, then try to find solutions.
What makes a production planner different from a project manger?
The difference between a product planner and project manager is that a planer is typically the one who organizes and plans the entire project. A production planner, however, is mostly involved in the planning stages.
What's the difference between Production Planning & Scheduling?
Production Planning (PP), also known as forecasting and identifying production capacities, is the process that determines what product needs to be produced at any particular time. This is accomplished by forecasting the demand and identifying production resources.
Scheduling refers the process by which tasks are assigned dates so that they can all be completed within the given timeframe.
What is the job of a logistics manger?
Logistics managers ensure that goods arrive on time and are unharmed. This is done using his/her knowledge of the company's products. He/she must also ensure sufficient stock to meet the demand.
What is the difference between manufacturing and logistics
Manufacturing refers to the process of making goods using raw materials and machines. Logistics includes all aspects related to supply chain management, such as procurement, distribution planning, inventory control and transportation. Manufacturing and logistics are often considered together as a broader term that encompasses both the process of creating products and delivering them to customers.
Statistics
- Many factories witnessed a 30% increase in output due to the shift to electric motors. (en.wikipedia.org)
- In the United States, for example, manufacturing makes up 15% of the economic output. (twi-global.com)
- You can multiply the result by 100 to get the total percent of monthly overhead. (investopedia.com)
- (2:04) MTO is a production technique wherein products are customized according to customer specifications, and production only starts after an order is received. (oracle.com)
- [54][55] These are the top 50 countries by the total value of manufacturing output in US dollars for its noted year according to World Bank.[56] (en.wikipedia.org)
External Links
How To
Six Sigma and Manufacturing
Six Sigma is defined by "the application SPC (statistical process control) techniques to achieve continuous improvements." Motorola's Quality Improvement Department created Six Sigma at their Tokyo plant, Japan in 1986. Six Sigma is a method to improve quality through standardization and elimination of defects. In recent years, many companies have adopted this method because they believe there is no such thing as perfect products or services. The main goal of Six Sigma is to reduce variation from the mean value of production. If you take a sample and compare it with the average, you will be able to determine how much of the production process is different from the norm. If this deviation is too big, you know something needs fixing.
The first step toward implementing Six Sigma is understanding how variability works in your business. Once you have this understanding, you will need to identify sources and causes of variation. It is important to identify whether the variations are random or systemic. Random variations are caused by human errors. Systematic variations can be caused by outside factors. These are, for instance, random variations that occur when widgets are made and some fall off the production line. But if you notice that every widget you make falls apart at the exact same place each time, this would indicate that there is a problem.
Once you identify the problem areas, it is time to create solutions. You might need to change the way you work or completely redesign the process. After implementing the new changes, you should test them again to see if they worked. If they don't work you need to rework them and come up a better plan.