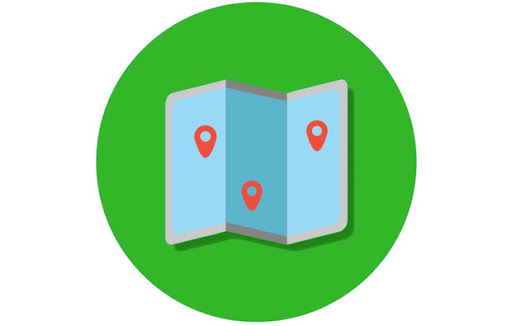
The Bureau Labor Statistics (BLS), an arm of Department of Labor, was established in 1884. It is a national statistical agency that collects, analyses, and disseminates vital economic information. It is responsible for conducting research and data analysis on a wide variety of economic issues, including labor market, prices, employment, wages and labor force. The agency also publishes statistical reports, and provides training on labor statistics to other countries.
To monitor wages and employment, the Bureau Labor Statistics conducts labor force surveys. It produces detailed industry estimates of nonfarm employment and wage rates. It also produces the Consumer Price Index which measures the price of common consumer products. The Bureau measures economic price changes, including transport, housing, and medical care.
BLS publishes data concerning employment and wage statistics for the United States and a variety of other areas. These data are frequently cited by economists and other market participants, as well as businesses. In addition to these reports, the Bureau also produces statistical tables, which allow users to view more detailed information on economic conditions. The Consumer Price Index, which is the most important report, is also very important. The Bureau also produces other economic data such as the Producers Price Index, and the Employment Situation Report.
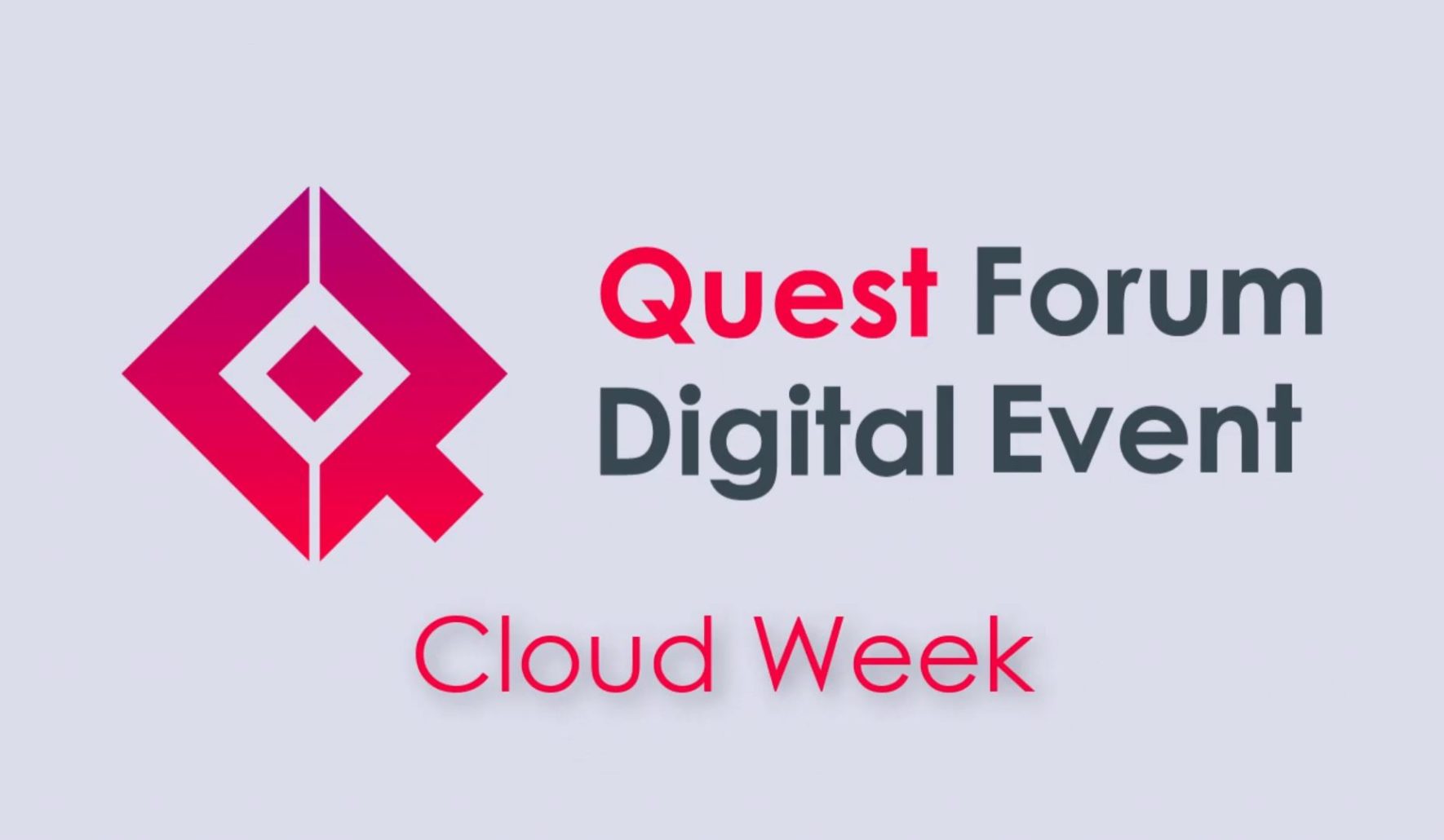
The Bureau of Labor Statistics performs research about the employment of men, women, and seniors. It also produces data on worker fatalities and nonfatal workplace injuries. It also creates data files on low-wage employees. The Bureau also conducts research into foreign-owned establishments with at least 10% stock owned by foreigners.
The Bureau also publishes information regarding the national unemployment rate. This data is derived from Current Population Survey. The bureau also publishes various supplemental surveys. Current Employment Statistics, (CES) surveys approximately 670,000 worksites. BLS also conducts research about the country's labor organizations and businesses.
The Bureau also publishes the Employment and Earnings report, which provides a national outlook of the labor market. This report provides information on the national unemployment rate, total employment, wages, and employment growth. The Bureau also publishes a list highlighting the most rapidly-growing jobs. The Bureau also publishes a list of the highest-paying jobs in the labor market.
The Bureau has an extensive staff. It also has six regional offices. The Bureau also operates several smaller local offices.
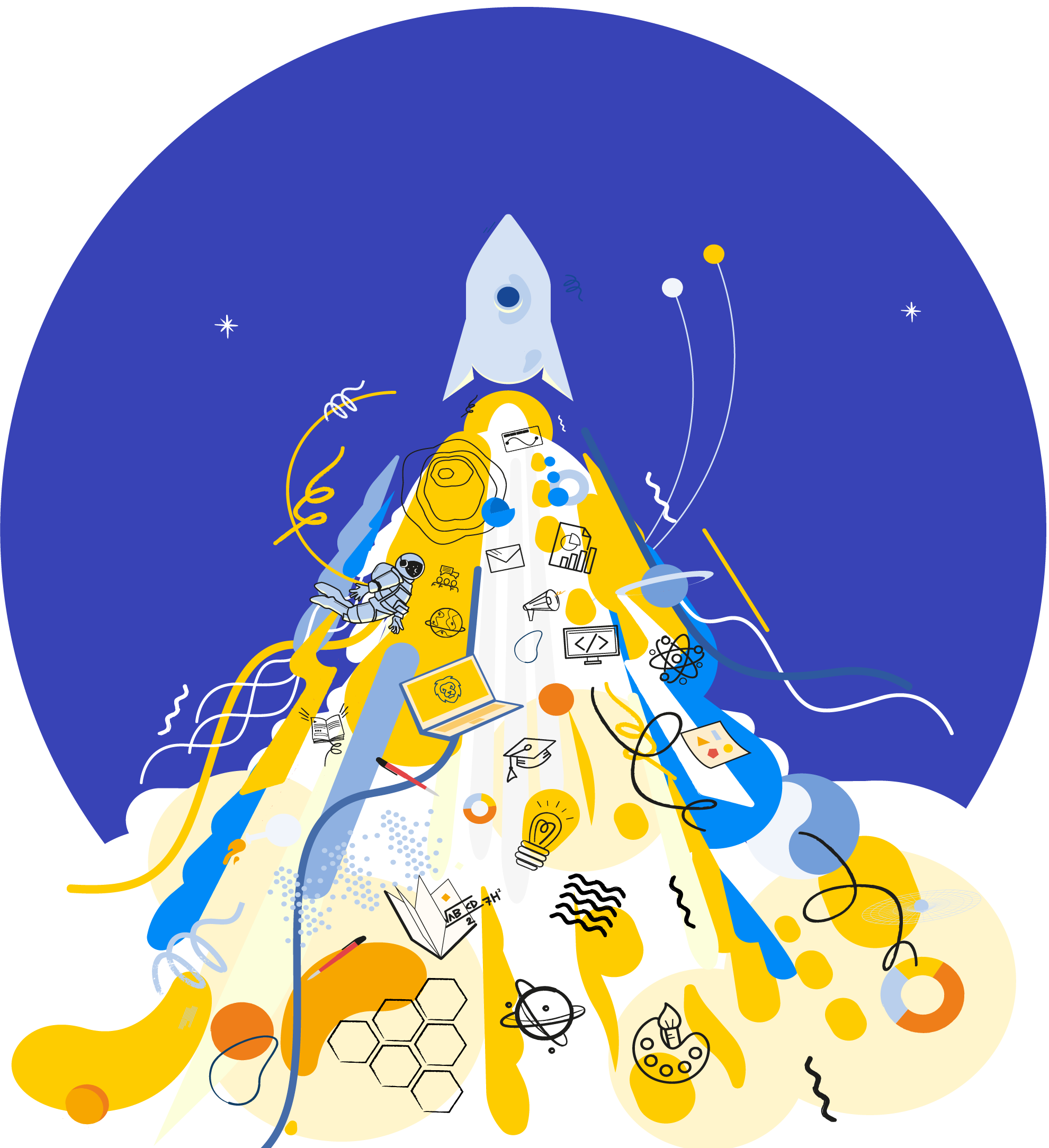
The Bureau also publishes a variety of reports, including the National Compensation survey. The National Compensation Survey, one of the United States' largest data-gathering programs, is a great example. This program gathers data on the average earnings, hours worked, and wages of employees working in all industries. The data is then used to create an industry-specific average. The report is published quarterly in many industries. The Occupational Outlook Quarterly also provides analysis on the labor market for certain occupations.
The Bureau also has an Office of Prices and Living Conditions, which measures price changes in the economy. The Producer Price Index and Consumer Price Index can be produced by the Office of Prices and Living Conditions. It also conducts research on export and import prices.
FAQ
Why automate your warehouse?
Modern warehouses have become more dependent on automation. The rise of e-commerce has led to increased demand for faster delivery times and more efficient processes.
Warehouses should be able adapt quickly to new needs. In order to do this, they need to invest in technology. The benefits of automating warehouses are numerous. Here are some benefits of investing in automation
-
Increases throughput/productivity
-
Reduces errors
-
Increases accuracy
-
Safety enhancements
-
Eliminates bottlenecks
-
Companies can scale up more easily
-
Makes workers more efficient
-
This gives you visibility into what happens in the warehouse
-
Enhances customer experience
-
Improves employee satisfaction
-
It reduces downtime, and increases uptime
-
Ensures quality products are delivered on time
-
Removing human error
-
This helps to ensure compliance with regulations
What is the difference between a production planner and a project manager?
The main difference between a production planner and a project manager is that a project manager is usually the person who plans and organizes the entire project, whereas a production planner is mainly involved in the planning stage of the project.
What is the difference in Production Planning and Scheduling, you ask?
Production Planning (PP) is the process of determining what needs to be produced at any given point in time. This is done through forecasting demand and identifying production capacities.
Scheduling is the process that assigns dates to tasks so they can get completed within a given timeframe.
What is the job of a production plan?
Production planners ensure all aspects of the project are delivered within time and budget. They also ensure the quality of the product and service meets the client's requirements.
What are the 7 Rs of logistics?
The acronym 7R's of Logistic is an acronym that stands for seven fundamental principles of logistics management. It was published in 2004 by the International Association of Business Logisticians as part of their "Seven Principles of Logistics Management" series.
The following letters make up the acronym:
-
Responsible – ensure that all actions are legal and don't cause harm to anyone else.
-
Reliable - You can have confidence that you will fulfill your promises.
-
Reasonable - make sure you use your resources well and don't waste them.
-
Realistic – consider all aspects of operations, from cost-effectiveness to environmental impact.
-
Respectful - show respect and treat others fairly and fairly
-
Responsive - Look for ways to save time and increase productivity.
-
Recognizable - provide customers with value-added services.
Statistics
- It's estimated that 10.8% of the U.S. GDP in 2020 was contributed to manufacturing. (investopedia.com)
- According to a Statista study, U.S. businesses spent $1.63 trillion on logistics in 2019, moving goods from origin to end user through various supply chain network segments. (netsuite.com)
- [54][55] These are the top 50 countries by the total value of manufacturing output in US dollars for its noted year according to World Bank.[56] (en.wikipedia.org)
- In the United States, for example, manufacturing makes up 15% of the economic output. (twi-global.com)
- (2:04) MTO is a production technique wherein products are customized according to customer specifications, and production only starts after an order is received. (oracle.com)
External Links
How To
How to use the Just-In Time Method in Production
Just-intime (JIT), a method used to lower costs and improve efficiency in business processes, is called just-in-time. It's the process of obtaining the right amount and timing of resources when you need them. This means that you only pay the amount you actually use. Frederick Taylor, a 1900s foreman, first coined the term. Taylor observed that overtime was paid to workers if they were late in working. He realized that workers should have enough time to complete their jobs before they begin work. This would help increase productivity.
JIT is a way to plan ahead and make sure you don't waste any money. Look at your entire project, from start to end. Make sure you have enough resources in place to deal with any unexpected problems. If you anticipate that there might be problems, you'll have enough people and equipment to fix them. You won't have to pay more for unnecessary items.
There are many types of JIT methods.
-
Demand-driven JIT: You order the parts and materials you need for your project every other day. This will allow for you to track the material that you have left after using it. This will let you know how long it will be to produce more.
-
Inventory-based: This is a type where you stock the materials required for your projects in advance. This allows one to predict how much they will sell.
-
Project-driven: This approach involves setting aside sufficient funds to cover your project's costs. When you know how much you need, you'll purchase the appropriate amount of materials.
-
Resource-based JIT: This type of JIT is most commonly used. Here you can allocate certain resources based purely on demand. You might assign more people to help with orders if there are many. If you don’t have many orders you will assign less people to the work.
-
Cost-based: This is a similar approach to resource-based but you are not only concerned with how many people you have, but also how much each one costs.
-
Price-based: This is a variant of cost-based. However, instead of focusing on the individual workers' costs, this looks at the total price of the company.
-
Material-based - This is a variant of cost-based. But instead of looking at the total company cost, you focus on how much raw material you spend per year.
-
Time-based: This is another variation of resource-based JIT. Instead of focusing solely on the amount each employee costs, focus on how long it takes for the project to be completed.
-
Quality-based JIT: This is another variation of resource based JIT. Instead of worrying about the costs of each employee or how long it takes for something to be made, you should think about how quality your product is.
-
Value-based JIT: One of the most recent forms of JIT. In this case, you're not concerned with how well the products perform or whether they meet customer expectations. Instead, you focus on the added value that you provide to your market.
-
Stock-based: This stock-based method focuses on the actual quantity of products being made at any given time. It's used when you want to maximize production while minimizing inventory.
-
Just-in-time planning (JIT): This is a combination JIT and supply-chain management. It refers to the process of scheduling the delivery of components as soon as they are ordered. This is important as it reduces lead time and increases throughput.