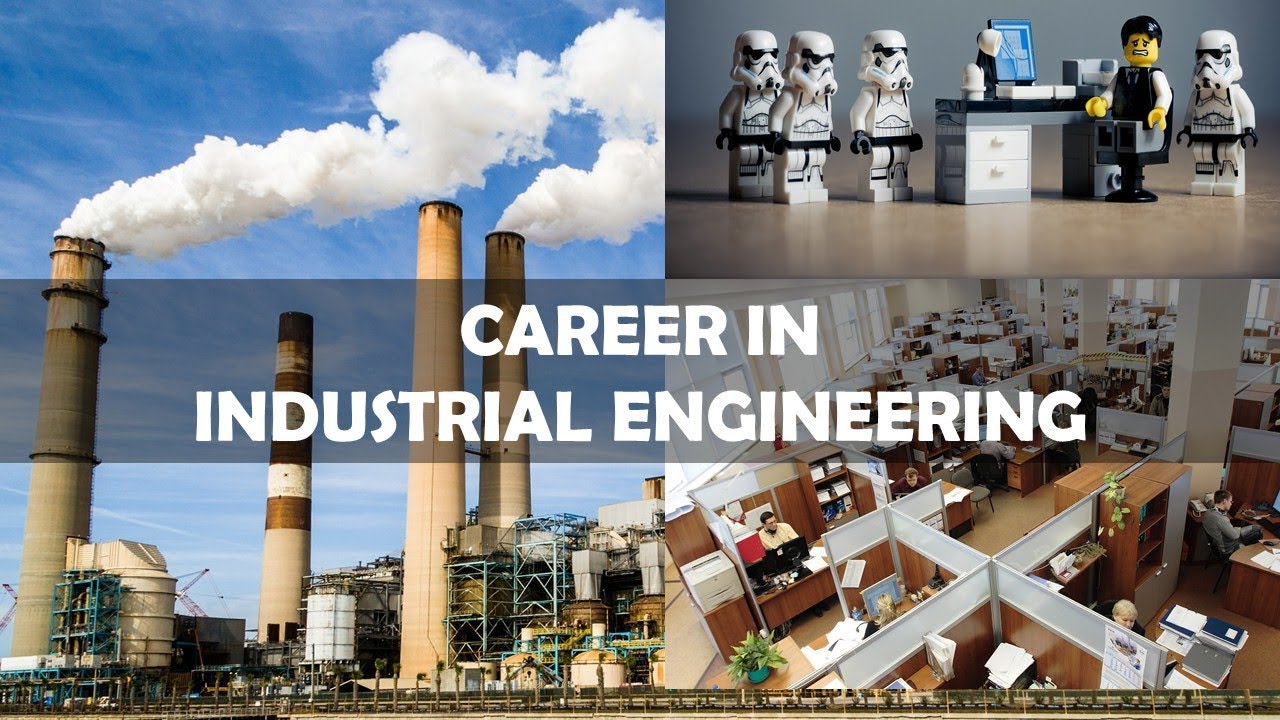
Drawing is a skill that requires a great deal of technical knowledge. They also need to be able to work with other people to help produce the best results. They might need to know how to read engineering plans or how to use particular software programs. They may also need to learn engineering formulas to calculate measurements.
Drawing professionals are often employed by engineering or architectural firms. They are responsible for creating plans for buildings, structures, as well as other products, using computer-aided engineering (CAD) software. Although they may work independently, many of these professionals work in teams to create unique designs. They often work full-time, but they also can take on a variety of jobs. It depends on which company they work for they might have to work overtime in order to meet deadlines.
Drafters typically obtain an associate's degree in drafting from a community college or a technical institute. After completing their associate's degree, they can go on to a 4-year program at university. You may be able transfer your degree depending on what course you take.
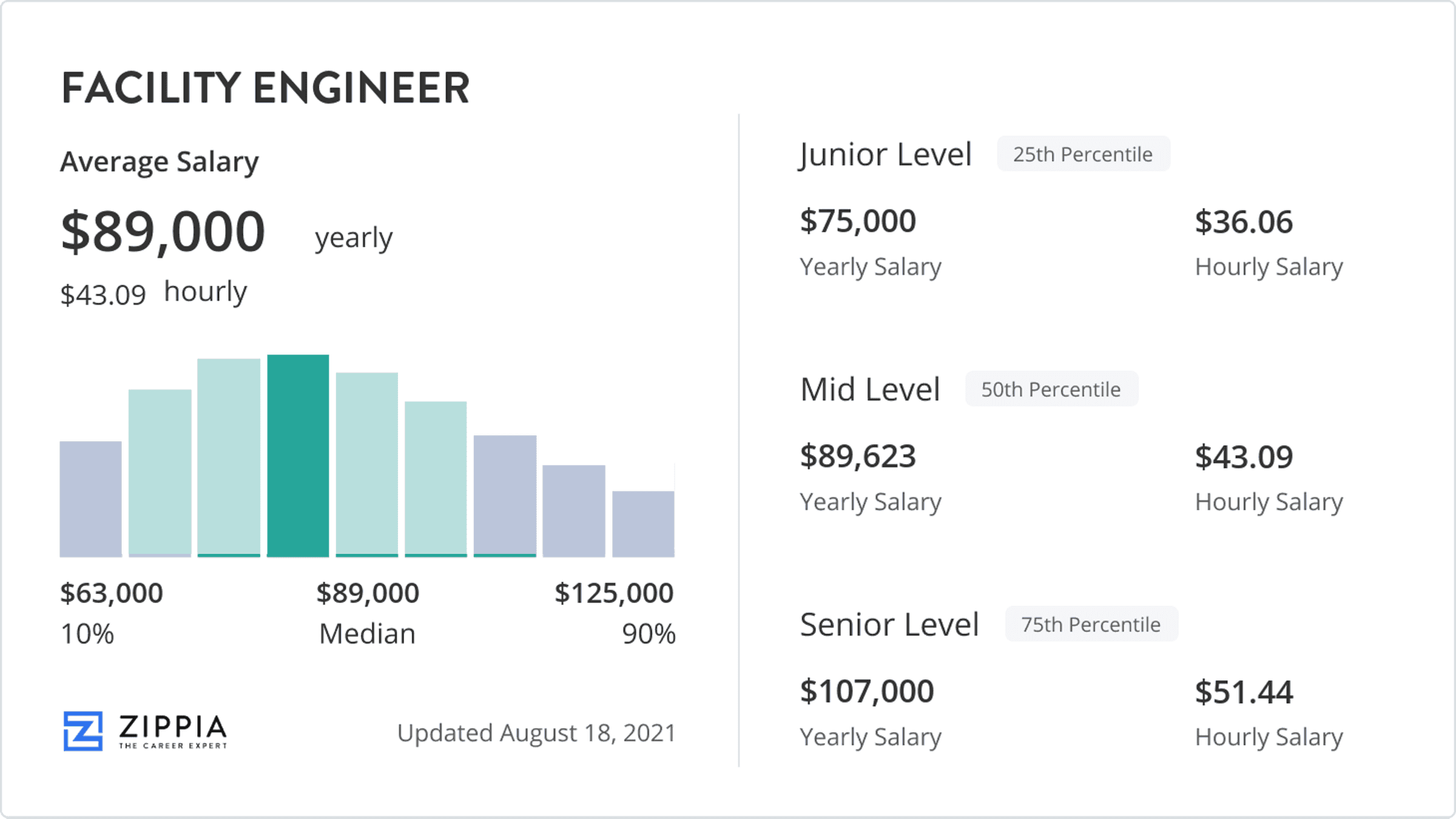
Drafters might also require professional experience. A firm may ask them to do an internship to gain practical experience. Drafters can benefit from this experience in securing a job. They may also be asked to submit a portfolio in order to demonstrate their drafting skills.
Drafters can also gain certifications. American Design Drafting Association, (ADDA), offers certification tests that test drafting knowledge. These tests can be used to evaluate your ability to tolerate and design geometrically. Many certifications are valid up to three years. To renew, candidates must take updated exams. The ADDA certifies a variety of drafting specialties.
Drafters typically work for construction, engineering, and manufacturing companies. They might also be employed in factories or with electricity. They may also work on a regular schedule, but some drafters work more than 40 hours a week. They also need to be able to manage their time well and understand how to use computer-aided drafting (CAD) software.
Drafters can profit from the growing use of technology in order to increase their efficiency. To be competitive, drafters need to be proficient in CAD and other programs. They also need to keep current with building codes. A master's degree may be an option for anyone who is interested in drafting. When it comes down to getting hired, people with master's degrees will be able to stand out from the rest. They will also be better qualified to present technical information for clients.
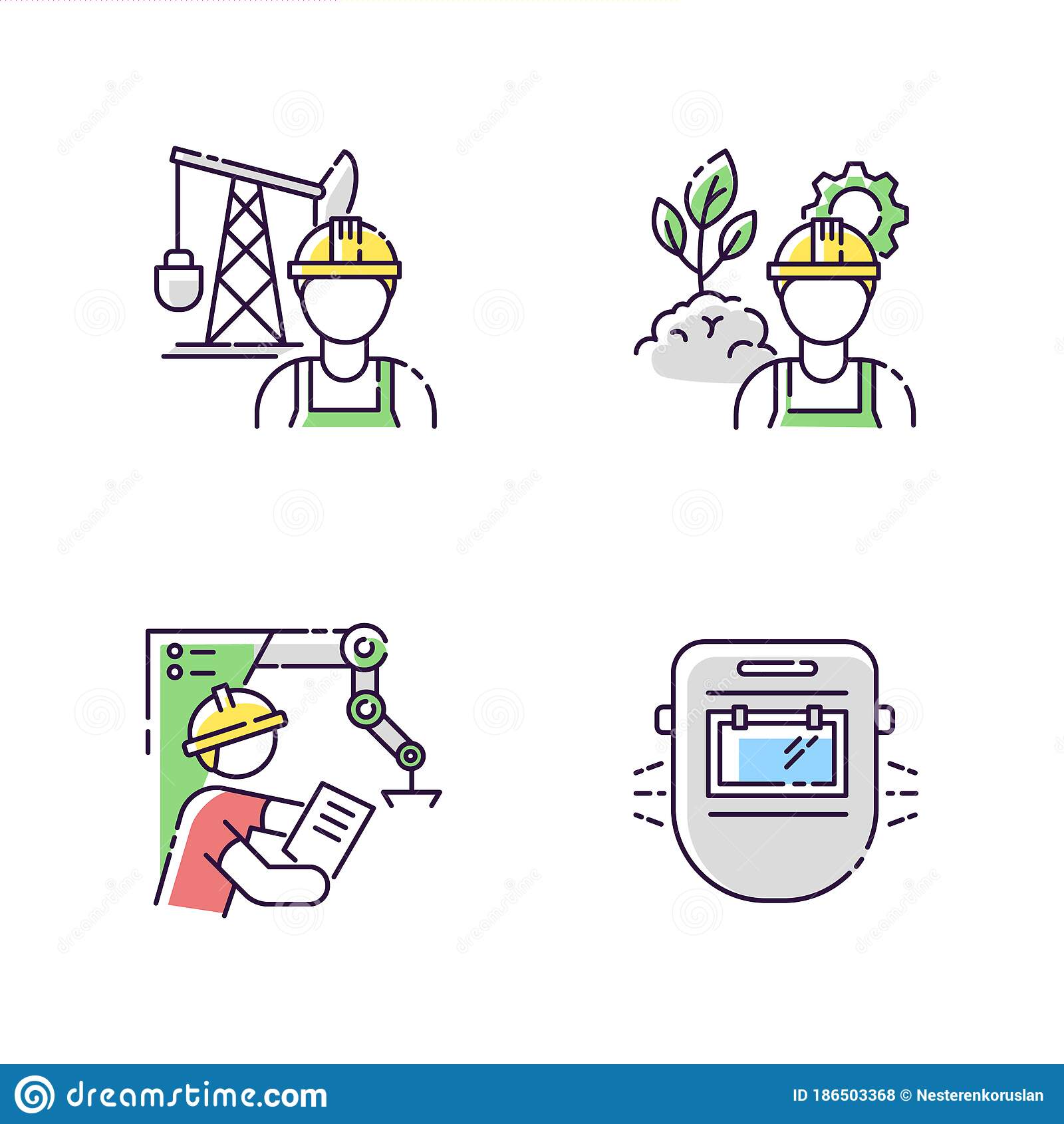
Drafters can also assist professional drafters. Volunteers may be available to help out with community projects. If you are interested in becoming a drafter, you should determine what type of project you are interested in before enrolling in classes. Some clients prefer hand-drawn sketches while others prefer computer generated drawings.
Draft technicians can gain work experience after they graduate from highschool. They should also be aware of computer and math classes.
FAQ
What do we need to know about Manufacturing Processes in order to learn more about Logistics?
No. It doesn't matter if you don't know anything about manufacturing before you learn about logistics. It is important to know about the manufacturing processes in order to understand how logistics works.
How can manufacturing avoid production bottlenecks
Avoiding production bottlenecks is as simple as keeping all processes running smoothly, from the time an order is received until the product ships.
This includes planning for capacity requirements as well as quality control measures.
The best way to do this is to use continuous improvement techniques such as Six Sigma.
Six Sigma Management System is a method to increase quality and reduce waste throughout your organization.
It focuses on eliminating variation and creating consistency in your work.
What's the difference between Production Planning & Scheduling?
Production Planning (PP), or production planning, is the process by which you determine what products are needed at any given time. This can be done by forecasting demand and identifying production capabilities.
Scheduling involves the assignment of dates and times to tasks in order to complete them within the timeframe.
What are the 7 Rs of logistics.
The acronym 7Rs of Logistics refers to the seven core principles of logistics management. It was developed and published by the International Association of Business Logisticians in 2004 as part of the "Seven Principles of Logistics Management".
The following letters make up the acronym:
-
Responsible – ensure that all actions are legal and don't cause harm to anyone else.
-
Reliable: Have faith in your ability or the ability to honor any promises made.
-
Be responsible - Use resources efficiently and avoid wasting them.
-
Realistic - consider all aspects of operations, including cost-effectiveness and environmental impact.
-
Respectful: Treat others with fairness and equity
-
Be resourceful: Look for opportunities to save money or increase productivity.
-
Recognizable - provide customers with value-added services.
What is production planning?
Production Planning refers to the development of a plan for every aspect of production. It is important to have everything ready and planned before you start shooting. You should also have information to ensure the best possible results on set. This includes shooting schedules, locations, cast lists, crew details, and equipment requirements.
The first step is to outline what you want to film. You may have decided where to shoot or even specific locations you want to use. Once you have identified the scenes and locations, you can start to determine which elements are required for each scene. You might decide you need a car, but not sure what make or model. To narrow your options, you can search online for available models.
Once you have found the right car, you can start thinking about extras. Are you looking for people to sit in the front seats? Maybe you need someone to move around in the back. Perhaps you would like to change the interior colour from black to white. These questions can help you decide the right look for your car. The type of shots that you are looking for is another thing to consider. Are you going to be shooting close-ups? Or wide angles? Perhaps you want to show the engine or the steering wheel? These details will help identify the exact car you wish to film.
Once you've determined the above, it is time to start creating a calendar. You can create a schedule that will outline when you must start and finish your shoots. Each day will include the time when you need to arrive at the location, when you need to leave and when you need to return home. This way, everyone knows what they need to do and when. Book extra staff ahead of time if you need them. There is no point in hiring someone who won't turn up because you didn't let him know.
Your schedule will also have to be adjusted to reflect the number of days required to film. Some projects are quick and easy, while others take weeks. When creating your schedule, be aware of whether you need more shots per day. Multiple takes of the same location will lead to higher costs and take more time. If you aren't sure whether you need multiple shots, it is best to take fewer photos than you would like.
Another important aspect of production planning is setting budgets. As it will allow you and your team to work within your financial means, setting a realistic budget is crucial. Keep in mind that you can always reduce your budget if you face unexpected difficulties. However, it is important not to overestimate the amount that you will spend. If you underestimate the cost of something, you will have less money left after paying for other items.
Production planning is a very detailed process, but once you understand how everything works together, it becomes easier to plan future projects.
What does the term manufacturing industries mean?
Manufacturing Industries are businesses that produce products for sale. Consumers are those who purchase these products. These companies use a variety processes such as distribution, retailing and management to accomplish their purpose. They make goods from raw materials with machines and other equipment. This includes all types of manufactured goods, including food items, clothing, building supplies, furniture, toys, electronics, tools, machinery, vehicles, pharmaceuticals, medical devices, chemicals, and many others.
Is automation important in manufacturing?
Automation is essential for both manufacturers and service providers. It allows them to offer services faster and more efficiently. They can also reduce their costs by reducing human error and improving productivity.
Statistics
- Job #1 is delivering the ordered product according to specifications: color, size, brand, and quantity. (netsuite.com)
- You can multiply the result by 100 to get the total percent of monthly overhead. (investopedia.com)
- According to the United Nations Industrial Development Organization (UNIDO), China is the top manufacturer worldwide by 2019 output, producing 28.7% of the total global manufacturing output, followed by the United States, Japan, Germany, and India.[52][53] (en.wikipedia.org)
- It's estimated that 10.8% of the U.S. GDP in 2020 was contributed to manufacturing. (investopedia.com)
- [54][55] These are the top 50 countries by the total value of manufacturing output in US dollars for its noted year according to World Bank.[56] (en.wikipedia.org)
External Links
How To
How to use 5S in Manufacturing to Increase Productivity
5S stands in for "Sort", the "Set In Order", "Standardize", or "Separate". Toyota Motor Corporation was the first to develop the 5S approach in 1954. It improves the work environment and helps companies to achieve greater efficiency.
This method aims to standardize production processes so that they are repeatable, measurable and predictable. This means that daily tasks such as cleaning and sorting, storage, packing, labeling, and packaging are possible. This knowledge allows workers to be more efficient in their work because they are aware of what to expect.
Implementing 5S requires five steps. These are Sort, Set In Order, Standardize. Separate. And Store. Each step requires a different action, which increases efficiency. Sorting things makes it easier to find them later. When you arrange items, you place them together. You then organize your inventory in groups. You can also label your containers to ensure everything is properly labeled.
This requires employees to critically evaluate how they work. Employees need to understand the reasons they do certain jobs and determine if there is a better way. In order to use the 5S system effectively, they must be able to learn new skills.
The 5S method increases efficiency and morale among employees. As they begin to see improvements, they feel motivated to continue working towards the goal of achieving higher levels of efficiency.