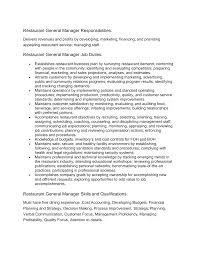
The US manufacturing sector makes up a large part of America's economy. About eleven percent of total national economic output is driven by the sector. It accounts for 18.2 percentage of all world goods, and is also a significant contributor to the country's overall economic output. However, manufacturing has seen a slowdown in growth in recent years.
The US has lost a third of its factory jobs since 2000. According to the Bureau of Labor Statistics(BLS), manufacturing productivity increased by 4.5 percent per year from 1995 to 2000. While once manufacturing was seen as a declining job generator but automation and other technological advances have led to a reexamination regarding how technology is impacting the employment market.
Walmart made an announcement in January 2013 that it would support American jobs. Walmart has committed to buying $250 billion in American products over the next ten-year period. Walmart will continue to support American manufacturing and encourage companies to explore possible opportunities with the giant retailer.
However, while the United States has become a leading player in the global market, it has faced challenges. The rising cost of labor in the United States, an increase in corporate taxes, and lack of expertise in trade negotiations are some of these problems. These issues could hinder the sector's future.
A skills crisis is also facing the US, with an estimated 1.4million factory workers in need of additional training. Trump's policies are aimed at expanding apprenticeship programs and training, but there have been concerns about the quality.
Despite all the challenges, however, the US manufacturing sector has seen a rebound since the Great Recession. In the first quarter of 2018, manufacturing output reached a record high of $2.00 trillion. This was significantly higher than the $1.95 billion that was reached in the prior year, before the recession.
While the US's manufacturing sector has experienced slower growth than the US overall economy, the industry is expected to grow at an even faster pace in the next few years. The industry is expected to grow by 2.4 percent in 2020 and 1.9% 2021.
The manufacturing sector will benefit from increased exports. The industry has also seen a reduction in energy costs due to shale oil. The United States also has a competitive corporate rate that is higher than many other countries around the globe.
China, Japan, South Korea and South Korea are all experiencing manufacturing contractions. This is the first time that the S&P Global purchasing managers index has gone below 50 in these countries in almost two years.
Trump is believed to be working with the federal government on a simpler program to help the manufacturing sector. Manufacturing Extension Partnership, (MEP), is one the most important federal programs. MEPs produce $21 in new client investment, for every $21 that is invested by the federal governments. MEPs are also available in the 50 US states, Canada, Mexico, and Europe.
The US's trade position is relatively poor compared to other industrialized nations. This means that the government does not have the skills to negotiate bilateral trade agreements. The US faces challenges in attracting more manufacturers and keeping existing companies.
FAQ
What is the difference between manufacturing and logistics
Manufacturing is the act of producing goods from raw materials using machines and processes. Logistics encompasses the management of all aspects associated with supply chain activities such as procurement, production planning, distribution and inventory control. It also includes customer service. As a broad term, manufacturing and logistics often refer to both the creation and delivery of products.
What are my options for learning more about manufacturing
You can learn the most about manufacturing by getting involved in it. But if that is not possible you can always read books and watch educational videos.
What skills is required for a production planner?
You must be flexible and organized to become a productive production planner. Also, you must be able and willing to communicate with clients and coworkers.
Statistics
- In 2021, an estimated 12.1 million Americans work in the manufacturing sector.6 (investopedia.com)
- According to the United Nations Industrial Development Organization (UNIDO), China is the top manufacturer worldwide by 2019 output, producing 28.7% of the total global manufacturing output, followed by the United States, Japan, Germany, and India.[52][53] (en.wikipedia.org)
- Job #1 is delivering the ordered product according to specifications: color, size, brand, and quantity. (netsuite.com)
- [54][55] These are the top 50 countries by the total value of manufacturing output in US dollars for its noted year according to World Bank.[56] (en.wikipedia.org)
- In the United States, for example, manufacturing makes up 15% of the economic output. (twi-global.com)
External Links
How To
How to Use Lean Manufacturing in the Production of Goods
Lean manufacturing is a management system that aims at increasing efficiency and reducing waste. It was created in Japan by Taiichi Ohno during the 1970s and 80s. He received the Toyota Production System award (TPS), from Kanji Toyoda, founder of TPS. Michael L. Watkins published the book "The Machine That Changed the World", which was the first to be published about lean manufacturing.
Lean manufacturing, often described as a set and practice of principles, is aimed at improving the quality, speed, cost, and efficiency of products, services, and other activities. It emphasizes eliminating waste and defects throughout the value stream. Lean manufacturing is also known as just in time (JIT), zero defect total productive maintenance(TPM), and five-star (S). Lean manufacturing seeks to eliminate non-value added activities, such as inspection, work, waiting, and rework.
Lean manufacturing not only improves product quality but also reduces costs. Companies can also achieve their goals faster by reducing employee turnover. Lean Manufacturing is one of the most efficient ways to manage the entire value chains, including suppliers and customers as well distributors and retailers. Many industries worldwide use lean manufacturing. Toyota's philosophy is a great example of this. It has helped to create success in automobiles as well electronics, appliances and healthcare.
Five principles are the basis of lean manufacturing:
-
Define value - Find out what your business contributes to society, and what makes it different from other competitors.
-
Reduce Waste - Eliminate any activity that doesn't add value along the supply chain.
-
Create Flow - Make sure work runs smoothly without interruptions.
-
Standardize & simplify - Make processes consistent and repeatable.
-
Build Relationships- Develop personal relationships with both internal as well as external stakeholders.
Lean manufacturing isn’t new, but it has seen a renewed interest since 2008 due to the global financial crisis. Many businesses have adopted lean production techniques to make them more competitive. Economists think that lean manufacturing is a crucial factor in economic recovery.
Lean manufacturing, which has many benefits, is now a standard practice in the automotive industry. These include improved customer satisfaction, reduced inventory levels, lower operating costs, increased productivity, and better overall safety.
It can be applied to any aspect of an organisation. This is because it ensures efficiency and effectiveness in all stages of the value chain.
There are three main types:
-
Just-in Time Manufacturing: This lean manufacturing method is commonly called "pull systems." JIT means that components are assembled at the time of use and not manufactured in advance. This approach is designed to reduce lead times and increase the availability of components. It also reduces inventory.
-
Zero Defects Manufacturing: ZDM ensures that no defective units leave the manufacturing plant. Repairing a part that is damaged during assembly should be done, not scrapping. This also applies to finished products that need minor repairs before being shipped.
-
Continuous Improvement: Continuous Improvement aims to improve efficiency by continually identifying problems and making adjustments to eliminate or minimize waste. Continuous improvement involves continuous improvement of processes and people as well as tools.