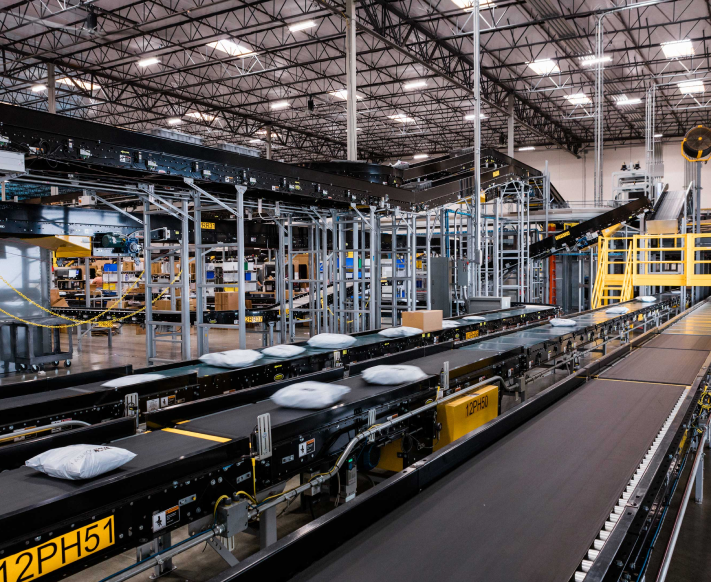
Industrial Engineering managers are essential members of the team. They play a vital role in the management of staff members and improving output. This includes coordination of the factory floor layout and supervision of the implementation process and procedures. Additionally, they offer technical knowledge and expertise that can be used to aid in the development of new products or processes.
They are responsible in developing and maintaining effective manufacturing processes. This requires the knowledge of the latest trends in automation and robotics. They are responsible for ensuring compliance with health and safety standards and monitoring and maintaining industrial processes. They also supervise the use of raw materials and consumables. They also perform studies to improve workflows and space usage. The manager oversees the implementation of all work projects, including cycle time reduction, product cost reduction, and process improvement. They also oversee preventative maintenance.
As a manager, you work with other teams to improve efficiency and streamline operations. The manager also supervises the renovation and installation of equipment. As part of the project management process, the manager communicates technical information to non-technical stakeholders. A manager is responsible for securing resources and making site visits to suppliers' facilities. He or she is a champion for members of the team and ensures they adhere to quality standards.
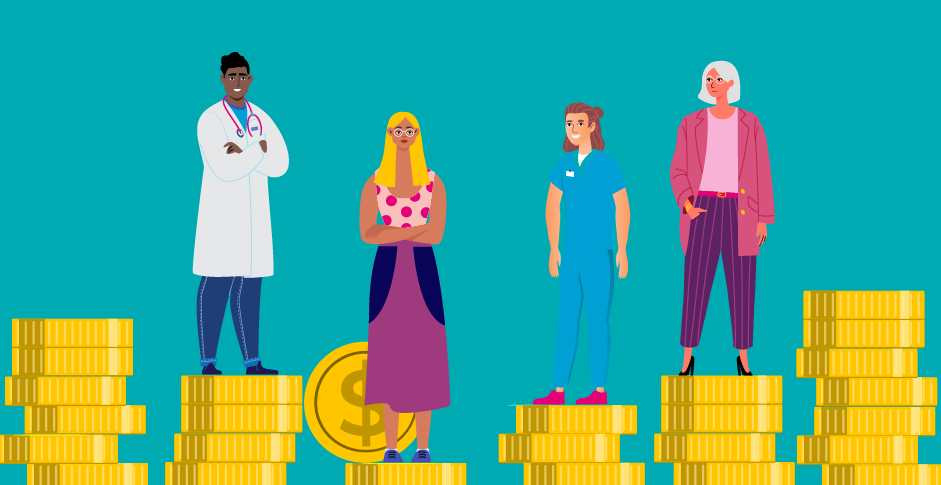
Industrial Engineering Managers are expected to be highly motivated, creative, and able to solve problems. They need to be able and able to work in cold and hot environments. In addition, they must be able to communicate effectively with all levels of employees.
The degree required to become an Industrial Engineering Manager is in engineering or a closely related field. They must also have at minimum five years of relevant experience. Employers prefer candidates who have completed postgraduate studies. You may also need specific skills like project management or logistics.
The Industrial Engineering Managers manage the design and development process for new products. They have strong skills in problem-solving, quality improvement, and other related areas. They enjoy working in a team. The manager is most successful when he or she is able to facilitate employees' growth.
Industrial Engineers are highly skilled at streamlining operations and cutting costs. They have a good understanding of manufacturing processes and are able to meet deadlines. They have also worked in human resources, logistics and vendor/supplier relations. They can set goals, manage procedures, and create budgets. They are also capable of preparing strategies to improve the efficiency and effectiveness of engineering projects.
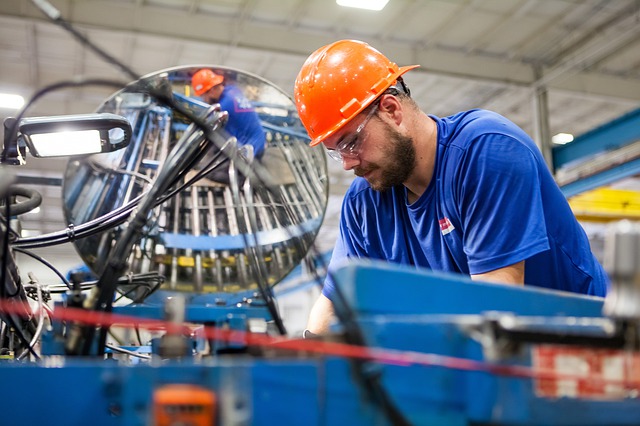
Industrial engineering managers may be responsible in designing and implementing new manufacturing techniques or operating equipment. They must develop plans for new equipment and operating methods using existing standards and guidelines. They are also responsible for overseeing the implementation and monitoring of waste elimination plans. In addition, they are responsible for analyzing labor productivity in the factory.
Industrial engineering managers can contribute their expertise to the development of strategies for increasing productivity, creating new products and managing human resource. They can also aid in the development and improvement of existing processes.
FAQ
How does a production planner differ from a project manager?
The major difference between a Production Planner and a Project Manager is that a Project Manager is often the person responsible for organizing and planning the entire project. While a Production Planner is involved mainly in the planning stage,
What are the responsibilities of a logistic manager?
A logistics manager makes sure that all goods are delivered on-time and in good condition. This is accomplished by using the experience and knowledge gained from working with company products. He/she should ensure that sufficient stock is available in order to meet customer demand.
What is production planning?
Production Planning involves developing a plan for all aspects of the production, including scheduling, budgeting, casting, crew, location, equipment, props, etc. It is important to have everything ready and planned before you start shooting. It should also provide information about how best to produce the best results while on set. This includes location information, crew details, equipment specifications, and casting lists.
The first step is to decide what you want. You may have already chosen the location you want, or there are locations or sets you prefer. Once you've identified the locations and scenes you want to use, you can begin to plan what elements you need for each scene. You might decide you need a car, but not sure what make or model. You could look online for cars to see what options are available, and then narrow down your choices by selecting between different makes or models.
After you have chosen the right car, you will be able to begin thinking about accessories. You might need to have people in the front seats. Perhaps you have someone who needs to be able to walk around the back of your car. You might want to change your interior color from black and white. These questions will help you determine the exact look and feel of your car. You can also think about the type of shots you want to get. Do you want to film close-ups, or wider angles? Perhaps you want to show the engine or the steering wheel? All of these things will help you identify the exact style of car you want to film.
Once you have made all the necessary decisions, you can start to create a schedule. You can create a schedule that will outline when you must start and finish your shoots. Each day will include the time when you need to arrive at the location, when you need to leave and when you need to return home. Everyone will know what they need and when. It is possible to make arrangements in advance for additional staff if you are looking to hire. It is not worth hiring someone who won’t show up because you didn’t tell him.
It is important to calculate the amount of filming days when you are creating your schedule. Some projects are quick and easy, while others take weeks. When you are creating your schedule, you should always keep in mind whether you need more than one shot per day or not. Multiplying takes in the same area will result both in increased costs and a longer time. If you aren't sure whether you need multiple shots, it is best to take fewer photos than you would like.
Budgeting is another crucial aspect of production plan. It is important to set a realistic budget so you can work within your budget. Keep in mind that you can always reduce your budget if you face unexpected difficulties. But, don't underestimate how much money you'll spend. Underestimating the cost will result in less money after you have paid for other items.
Production planning is a complicated process. But once you understand how everything works together, it becomes much easier to plan future project.
How can manufacturing reduce production bottlenecks?
The key to avoiding bottlenecks in production is to keep all processes running smoothly throughout the entire production cycle, from the time you receive an order until the time when the product ships.
This includes planning for both capacity requirements and quality control measures.
This can be done by using continuous improvement techniques, such as Six Sigma.
Six Sigma is a management system used to improve quality and reduce waste in every aspect of your organization.
It focuses on eliminating variation and creating consistency in your work.
What are the 7 Rs of logistics management?
The acronym 7Rs of Logistics refers to the seven core principles of logistics management. It was developed and published by the International Association of Business Logisticians in 2004 as part of the "Seven Principles of Logistics Management".
The acronym is made up of the following letters:
-
Responsible - ensure that all actions taken are within legal requirements and are not harmful to others.
-
Reliable - Have confidence in your ability to fulfill all of your commitments.
-
Be responsible - Use resources efficiently and avoid wasting them.
-
Realistic – consider all aspects of operations, from cost-effectiveness to environmental impact.
-
Respectful - Treat people fairly and equitably
-
You are resourceful and look for ways to save money while increasing productivity.
-
Recognizable: Provide customers with value-added service
How can manufacturing efficiency be improved?
First, determine which factors have the greatest impact on production time. Then we need to find ways to improve these factors. If you don’t know how to start, look at which factors have the greatest impact upon production time. Once you have identified them, it is time to identify solutions.
Statistics
- It's estimated that 10.8% of the U.S. GDP in 2020 was contributed to manufacturing. (investopedia.com)
- In 2021, an estimated 12.1 million Americans work in the manufacturing sector.6 (investopedia.com)
- You can multiply the result by 100 to get the total percent of monthly overhead. (investopedia.com)
- (2:04) MTO is a production technique wherein products are customized according to customer specifications, and production only starts after an order is received. (oracle.com)
- According to a Statista study, U.S. businesses spent $1.63 trillion on logistics in 2019, moving goods from origin to end user through various supply chain network segments. (netsuite.com)
External Links
How To
How to Use Just-In-Time Production
Just-intime (JIT), which is a method to minimize costs and maximize efficiency in business process, is one way. It allows you to get the right amount resources at the right time. This means that only what you use is charged to your account. Frederick Taylor was the first to coin this term. He developed it while working as a foreman during the early 1900s. He noticed that workers were often paid overtime when they had to work late. He decided that workers would be more productive if they had enough time to complete their work before they started to work.
JIT teaches you to plan ahead and prepare everything so you don’t waste time. Also, you should look at the whole project from start-to-finish and make sure you have the resources necessary to address any issues. You will have the resources and people to solve any problems you anticipate. This will ensure that you don't spend more money on things that aren't necessary.
There are several types of JIT techniques:
-
Demand-driven: This JIT is where you place regular orders for the parts/materials that are needed for your project. This will enable you to keep track of how much material is left after you use it. This will allow to you estimate the time it will take for more to be produced.
-
Inventory-based: This type allows you to stock the materials needed for your projects ahead of time. This allows you to forecast how much you will sell.
-
Project-driven: This method allows you to set aside enough funds for your project. If you know the amount you require, you can buy the materials you need.
-
Resource-based JIT: This is the most popular form of JIT. You allocate resources based on the demand. You might assign more people to help with orders if there are many. If there aren't many orders, you will assign fewer people.
-
Cost-based: This approach is very similar to resource-based. However, you don't just care about the number of people you have; you also need to consider how much each person will cost.
-
Price-based: This is a variant of cost-based. However, instead of focusing on the individual workers' costs, this looks at the total price of the company.
-
Material-based - This is a variant of cost-based. But instead of looking at the total company cost, you focus on how much raw material you spend per year.
-
Time-based JIT: This is another variant of resource-based JIT. Instead of focusing only on how much each employee is costing, you should focus on how long it takes to complete your project.
-
Quality-based JIT: Another variation on resource-based JIT. Instead of looking at the labor costs and time it takes to make a product, think about its quality.
-
Value-based JIT : This is the newest type of JIT. This is where you don't care about how the products perform or whether they meet customers' expectations. Instead, you're focused on how much value you add to the market.
-
Stock-based. This method is inventory-based and focuses only on the actual production at any given point. It's used when you want to maximize production while minimizing inventory.
-
Just-in-time (JIT) planning: This is a combination of JIT and supply chain management. It refers to the process of scheduling the delivery of components as soon as they are ordered. It's important because it reduces lead times and increases throughput.