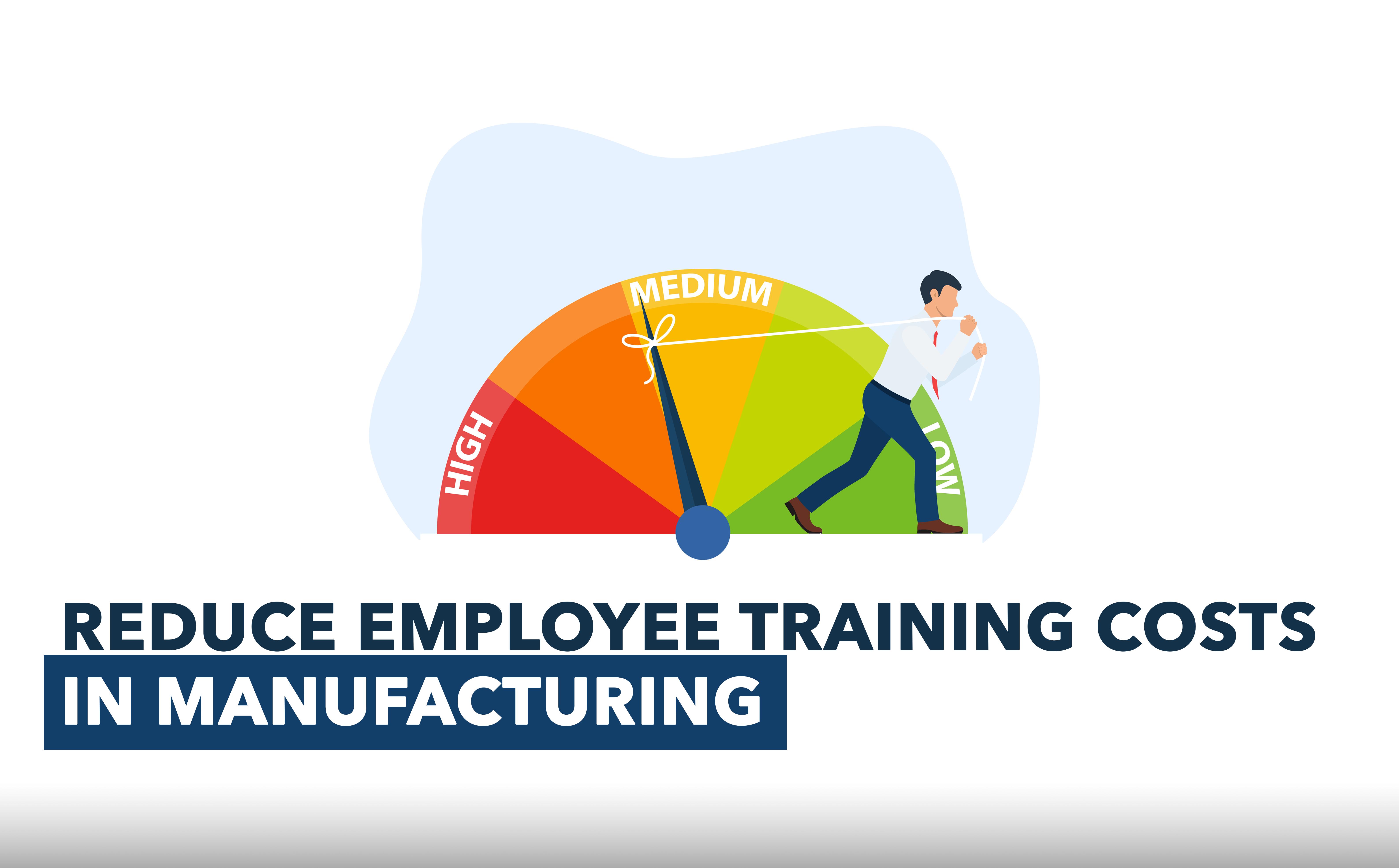
Creating a "Smart Factory" is more than just installing new technology. It's about changing the mindset of your factory and adapting to changes. You can help your customers and your business in a new stage of manufacturing with the right technology.
It is important to first decide what you want. One example is to create a smart factory that can respond to rapid changes in demand. You may also want to create a smart factory that helps your global supply chain partners. You may also want to build a smart factory to respond to an industry heavily dependent on manual labor. Whatever your goal, you need to create an ecosystem supporting it.
One key obstacle to a smart factory is a lack of connectivity. It can be hard to overcome this obstacle if you have outdated machinery and equipment. You may also find it difficult to get the necessary information on your machines and systems. The study showed that 33% thought a lack in IT infrastructure was a major barrier to smart factories.
Technology is the next most important factor. There are many advanced manufacturing techniques that are available. These technologies can improve your productivity as well as quality. These technologies can also make your plant more cost-effective.
Another factor to consider is people. You need to make investments in the right skill sets at the right times. You must have the right people, and also a skilled talent strategy. You need to ensure that you have a clear scope of work and that everyone's timelines and priorities align. You need to make sure that the right people are working on the right projects.
Process is the third important factor. You must ensure that your applications are able connect to a networking. This will help you to share information with other systems and processes in your factory. It is important to ensure that your data and analytics are available. This will enable you to make data-driven decision and self-heal.
People are the fourth most crucial factor. It is important to make sure that your executive team is fully committed to this initiative. A convener can be a valuable resource to coordinate efforts and align them across multiple vendors. It can also help to make sure that the scope of the project is aligned with your executive team.
Security is the fifth most critical factor. There are many technologies that can reduce the risk for cyberattacks in manufacturing environments. You should make sure that you have the best cybersecurity strategy. Also, you need to make sure that your cybersecurity strategy is always in place.
Finally, think about how you'll connect your machines to each other. While you can still use the existing solutions, it is worth looking into other options. This will allow you to create new data sets to support your smart factories initiatives.
FAQ
What are the 7 R's of logistics?
The acronym 7R's of Logistic is an acronym that stands for seven fundamental principles of logistics management. It was published in 2004 by the International Association of Business Logisticians as part of their "Seven Principles of Logistics Management" series.
The acronym is made up of the following letters:
-
Responsible - ensure that actions are in compliance with legal requirements and do not cause harm to others.
-
Reliable - have confidence in the ability to deliver on commitments made.
-
Reasonable - make sure you use your resources well and don't waste them.
-
Realistic – Consider all aspects, including cost-effectiveness as well as environmental impact.
-
Respectful: Treat others with fairness and equity
-
Be resourceful: Look for opportunities to save money or increase productivity.
-
Recognizable is a company that provides customers with value-added solutions.
How does manufacturing avoid bottlenecks in production?
To avoid production bottlenecks, ensure that all processes run smoothly from the moment you receive your order to the time the product ships.
This includes planning to meet capacity requirements and quality control.
The best way to do this is to use continuous improvement techniques such as Six Sigma.
Six Sigma Management System is a method to increase quality and reduce waste throughout your organization.
It focuses on eliminating variation and creating consistency in your work.
What is production planning?
Production planning is the process of creating a plan that covers all aspects of production. This includes scheduling, budgeting and crew, location, equipment, props, and more. This document will ensure everything is in order and ready to go when you need it. This document should include information about how to achieve the best results on-set. This includes location information, crew details, equipment specifications, and casting lists.
The first step in filming is to define what you want. You may have decided where to shoot or even specific locations you want to use. Once you have identified your locations and scenes it's time to begin figuring out what elements you will need for each one. Perhaps you have decided that you need to buy a car but aren't sure which model. In this case, you could start looking up cars online to find out what models are available and then narrow your choices by choosing between different makes and models.
After you have chosen the right car, you will be able to begin thinking about accessories. Do you have people who need to be seated in the front seat? Or maybe you just need someone to push the car around. Maybe you want to change the interior color from black to white? These questions can help you decide the right look for your car. Also, think about what kind of shots you would like to capture. Will you be filming close-ups or wide angles? Maybe the engine or steering wheel is what you are looking to film. All of these things will help you identify the exact style of car you want to film.
Once you have made all the necessary decisions, you can start to create a schedule. The schedule will show you when to begin shooting and when to stop. Each day will include the time when you need to arrive at the location, when you need to leave and when you need to return home. This way, everyone knows what they need to do and when. It is possible to make arrangements in advance for additional staff if you are looking to hire. You should not hire anyone who doesn't show up because of your inaction.
You will need to factor in the days that you have to film when creating your schedule. Some projects can be completed in a matter of days or weeks. Others may take several days. When you are creating your schedule, you should always keep in mind whether you need more than one shot per day or not. Shooting multiple takes over the same location will increase costs and take longer to complete. It is better to be cautious and take fewer shots than you risk losing money if you are not sure if multiple takes are necessary.
Another important aspect of production planning is setting budgets. As it will allow you and your team to work within your financial means, setting a realistic budget is crucial. It is possible to reduce the budget at any time if you experience unexpected problems. It is important to not overestimate how much you will spend. Underestimating the cost will result in less money after you have paid for other items.
Production planning can be a complex process. However, once you know how everything works together it will become easier to plan future projects.
What are the 4 types manufacturing?
Manufacturing is the process by which raw materials are transformed into useful products through machines and processes. It involves many different activities such as designing, building, testing, packaging, shipping, selling, servicing, etc.
What skills are required to be a production manager?
You must be flexible and organized to become a productive production planner. Communication skills are essential to ensure that you can communicate effectively with clients, colleagues, and customers.
How can we increase manufacturing efficiency?
The first step is to identify the most important factors affecting production time. Then we need to find ways to improve these factors. You can start by identifying the most important factors that impact production time. Once you identify them, look for solutions.
Statistics
- [54][55] These are the top 50 countries by the total value of manufacturing output in US dollars for its noted year according to World Bank.[56] (en.wikipedia.org)
- (2:04) MTO is a production technique wherein products are customized according to customer specifications, and production only starts after an order is received. (oracle.com)
- Job #1 is delivering the ordered product according to specifications: color, size, brand, and quantity. (netsuite.com)
- You can multiply the result by 100 to get the total percent of monthly overhead. (investopedia.com)
- According to the United Nations Industrial Development Organization (UNIDO), China is the top manufacturer worldwide by 2019 output, producing 28.7% of the total global manufacturing output, followed by the United States, Japan, Germany, and India.[52][53] (en.wikipedia.org)
External Links
How To
How to use 5S in Manufacturing to Increase Productivity
5S stands to stand for "Sort", “Set In Order", “Standardize", and "Store". Toyota Motor Corporation developed the 5S method in 1954. It helps companies achieve higher levels of efficiency by improving their work environment.
This method aims to standardize production processes so that they are repeatable, measurable and predictable. This means that daily tasks such as cleaning and sorting, storage, packing, labeling, and packaging are possible. Through these actions, workers can perform their jobs more efficiently because they know what to expect from them.
There are five steps to implementing 5S, including Sort, Set In Order, Standardize, Separate and Store. Each step is a different action that leads to greater efficiency. By sorting, for example, you make it easy to find the items later. When items are ordered, they are put together. After you have divided your inventory into groups you can store them in easy-to-reach containers. You can also label your containers to ensure everything is properly labeled.
Employees need to reflect on how they do their jobs. Employees must be able to see why they do what they do and find a way to achieve them without having to rely on their old methods. They will need to develop new skills and techniques in order for the 5S system to be implemented.
The 5S Method not only improves efficiency, but it also helps employees to be more productive and happier. They will feel motivated to strive for higher levels of efficiency once they start to see results.