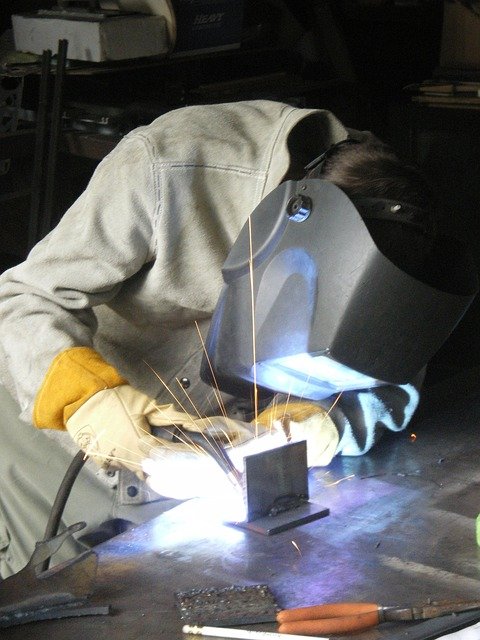
There are many manufacturers. But which one is right for you? Learn about discrete manufacturing, continuous manufacturing, job shop manufacturing, or process manufacturing. Each type of manufacturing has its advantages and disadvantages. This article will show you how the four types of manufacturing differ. Based on your industry, your location and your product type, you can determine which model is best for your company. Once you decide which type is best for your company, you'll need to consider your sales, production, and quality control.
Discrete manufacturing
Discrete manufacturing refers to a process where different products are made. Toys, cars, and aeroplanes are just a few examples of discrete manufacturing. Discrete Manufacturing allows companies to focus more on their individual products than on mass production. For example, discrete manufacturing makes it possible to create unique parts for an aeroplane by integrating several manufacturing processes. Discrete manufacturing is a popular method for manufacturing high-tech products.
Discrete manufacturing produces distinct items. Instead of producing multiple identical products, discrete manufacturing produces items that can be easily identified by serial numbers, labels, and other numerical attributes. A smartphone might be made up of parts from different factories located in different states. The individual pieces are only assembled once the product is sold. The bag of your smartphone is the same. It could contain parts from different plants, such as the Missouri plant headquarters.
Process manufacturing
The term process manufacturing is a branch in manufacturing that involves formulas and recipe. Distinctive manufacturing, which focuses on the manufacture of single units, bills, and components, is called process manufacturing. Both manufacturing methods have different goals. But each one is an important part of the manufacturing process. Here are three ways to differentiate process manufacturing from discrete manufacturing. Let's take a look at each of them.
Batch process manufacturing can be compared to continuous process production. It uses larger batches of raw materials, and works around the clock. Batch manufacturing is common in pharmaceuticals and paper production. However, it is not the right choice for every industry. It's often too complex and costly for smaller-scale businesses to use. This is why large-scale companies often use it when they need to make large quantities.
Manufacturing job shop
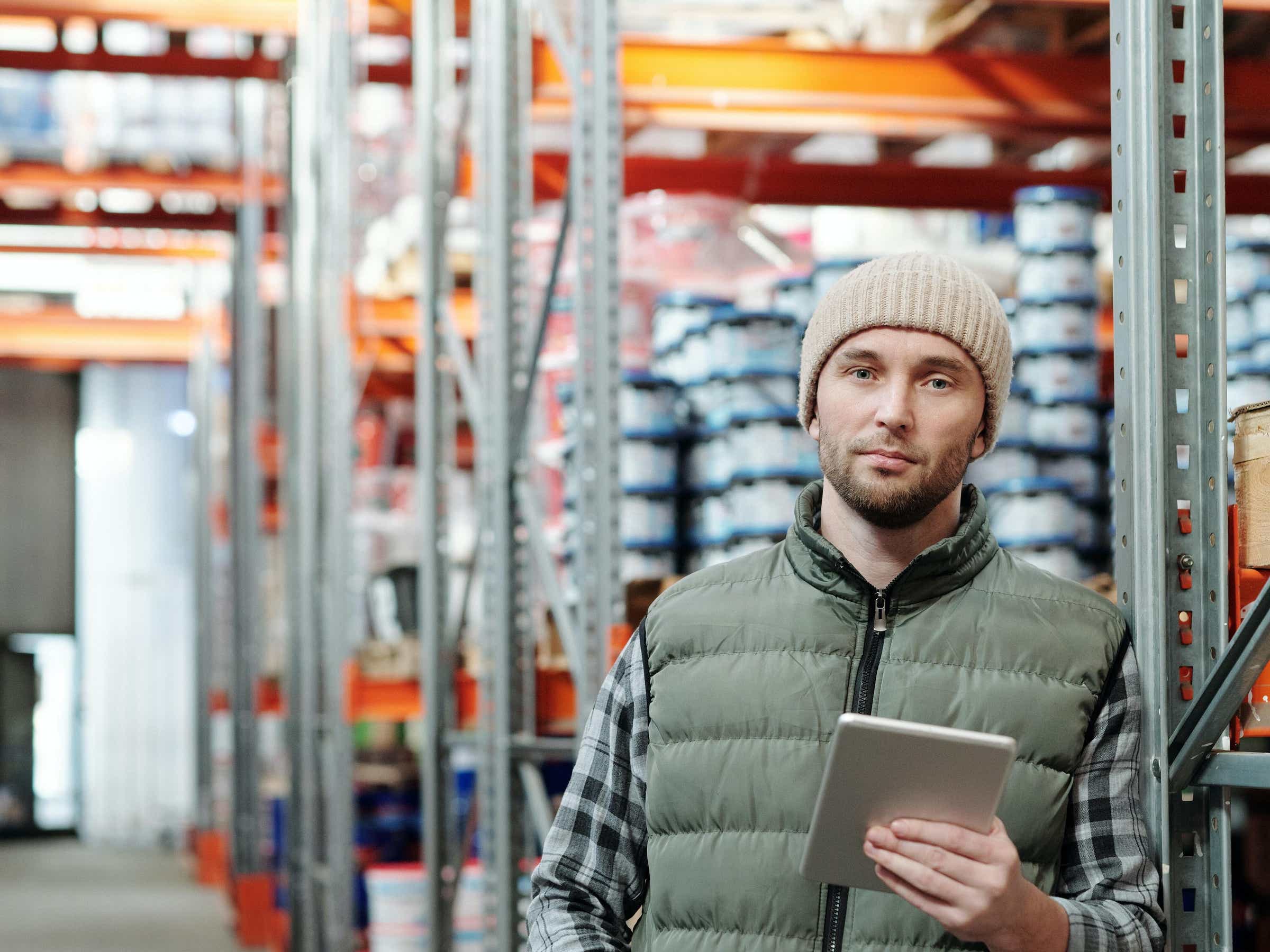
Job shop manufacturing is a small-scale system of production that specializes in custom, batch, and semi-custom manufacturing. Job shop systems can then move on to the next job as each job is finished. Lean manufacturing is another name for this method of production. Single-shift operations are more efficient than most other methods. Here are some of these benefits of jobshop manufacturing. Learn more about this manufacturing method. For your business, it might be worth considering for your product and service needs.
First, job shop efficiency must be improved. A critical factor in achieving a lean manufacturing system is incorporating new manufacturing principles. These principles are particularly relevant for high-volume operations and emphasize quality control and just in-time production. By adopting new manufacturing principles, a job shop can increase productivity while lowering costs at the same time. The job shop should ensure that each job is completed in its entirety, with no waiting.
Continuous manufacturing
Continuous manufacturing offers many benefits, including the flexibility of tracking. This is especially helpful in the event of product failure. Product data such as the amount of raw material used and the time stamp at each production line can be used for identifying defective batches. The increased tracking also helps the manufacturer reduce waste and the chance of a product shortage. Similarly, continuous manufacturing is becoming popular in the pharmaceutical industry.
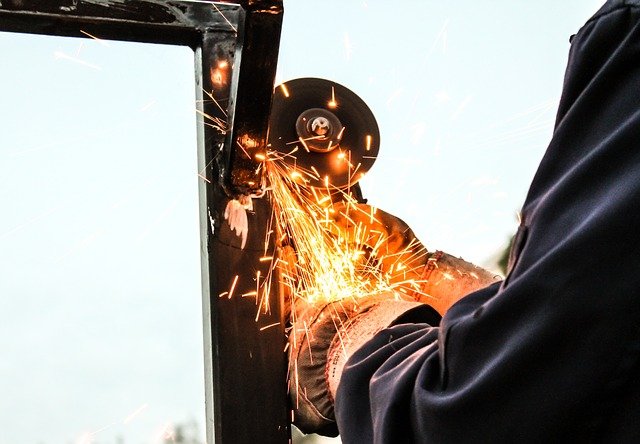
Although continuous manufacturing has many benefits, implementation can be difficult. Implementation can be difficult because the process is not fully integrated within the company. Continuous manufacturing can be a game-changer for the pharmaceutical sector, regardless of its benefits. The process must be seamless and integrate with continuous flow and end to end integration for it to be effective. The benefits of continuous manufacture have long been recognized by the pharmaceutical industries, but implementation has been slow.
FAQ
Why automate your factory?
Modern warehousing has seen automation take center stage. The rise of e-commerce has led to increased demand for faster delivery times and more efficient processes.
Warehouses have to be flexible to meet changing requirements. To do so, they must invest heavily in technology. The benefits of automating warehouses are numerous. Here are some of the reasons automation is worth your investment:
-
Increases throughput/productivity
-
Reduces errors
-
Increases accuracy
-
Safety enhancements
-
Eliminates bottlenecks
-
This allows companies to scale easily
-
Makes workers more efficient
-
Gives you visibility into all that is happening in your warehouse
-
Enhances customer experience
-
Improves employee satisfaction
-
It reduces downtime, and increases uptime
-
This ensures that quality products are delivered promptly
-
Eliminates human error
-
Helps ensure compliance with regulations
Are there any Manufacturing Processes that we should know before we can learn about Logistics?
No. No. It is important to know about the manufacturing processes in order to understand how logistics works.
What is production planning?
Production planning is the process of creating a plan that covers all aspects of production. This includes scheduling, budgeting and crew, location, equipment, props, and more. This document will ensure everything is in order and ready to go when you need it. This document should include information about how to achieve the best results on-set. This includes location information, crew details, equipment specifications, and casting lists.
It is important to first outline the type of film you would like to make. You may have already decided where you would like to shoot, or maybe there are specific locations or sets that you want to use. Once you have determined your scenes and locations, it is time to start figuring out the elements that you will need for each scene. One example is if you are unsure of the exact model you want but decide that you require a car. You could look online for cars to see what options are available, and then narrow down your choices by selecting between different makes or models.
After you have selected the car you want, you can begin to think about additional features. What about additional seating? Maybe you need someone to move around in the back. Maybe you'd like to change the interior from black to a white color. These questions will help to determine the style and feel of your car. It is also worth considering the types of shots that you wish to take. You will be filming close-ups and wide angles. Maybe the engine or steering wheel is what you are looking to film. All of these things will help you identify the exact style of car you want to film.
Once you have determined all of the above, you can move on to creating a schedule. A schedule will tell you when you need to start shooting and when you need to finish. The schedule will show you when to get there, what time to leave, and when to return home. So everyone is clear about what they need to do. Hire extra staff by booking them ahead of time. You don't want to hire someone who won't show up because he didn't know.
Your schedule will also have to be adjusted to reflect the number of days required to film. Some projects can be completed in a matter of days or weeks. Others may take several days. When creating your schedule, be aware of whether you need more shots per day. Multiple takes at the same place will result in higher costs and longer completion times. It's better to be safe than sorry and shoot less takes if you're not certain whether you need more takes.
Budget setting is an important part of production planning. You will be able to manage your resources if you have a realistic budget. You can always lower the budget if you encounter unexpected problems. However, it is important not to overestimate the amount that you will spend. If you underestimate how much something costs, you'll have less money to pay for other items.
Production planning is a complicated process. But once you understand how everything works together, it becomes much easier to plan future project.
Why is logistics so important in manufacturing?
Logistics are an essential component of any business. They can help you achieve great success by helping you manage product flow from raw material to finished goods.
Logistics plays a significant role in reducing cost and increasing efficiency.
What does manufacturing mean?
Manufacturing Industries refers to businesses that manufacture products. Consumers are those who purchase these products. This is accomplished by using a variety of processes, including production, distribution and retailing. They produce goods from raw materials by using machines and other machinery. This includes all types if manufactured goods.
How can efficiency in manufacturing be improved?
The first step is to determine the key factors that impact production time. Next, we must find ways to improve those factors. If you don’t know where to begin, consider which factors have the largest impact on production times. Once you've identified them, try to find solutions for each of those factors.
Statistics
- In 2021, an estimated 12.1 million Americans work in the manufacturing sector.6 (investopedia.com)
- [54][55] These are the top 50 countries by the total value of manufacturing output in US dollars for its noted year according to World Bank.[56] (en.wikipedia.org)
- In the United States, for example, manufacturing makes up 15% of the economic output. (twi-global.com)
- Job #1 is delivering the ordered product according to specifications: color, size, brand, and quantity. (netsuite.com)
- You can multiply the result by 100 to get the total percent of monthly overhead. (investopedia.com)
External Links
How To
Six Sigma and Manufacturing
Six Sigma refers to "the application and control of statistical processes (SPC) techniques in order to achieve continuous improvement." Motorola's Quality Improvement Department created Six Sigma at their Tokyo plant, Japan in 1986. The basic idea behind Six Sigma is to improve quality by improving processes through standardization and eliminating defects. In recent years, many companies have adopted this method because they believe there is no such thing as perfect products or services. Six Sigma's main objective is to reduce variations from the production average. If you take a sample and compare it with the average, you will be able to determine how much of the production process is different from the norm. If there is a significant deviation from the norm, you will know that something needs to change.
Understanding the dynamics of variability within your business is the first step in Six Sigma. Once you have this understanding, you will need to identify sources and causes of variation. You'll also want to determine whether these variations are random or systematic. Random variations happen when people make errors; systematic variations are caused externally. For example, if you're making widgets, and some of them fall off the assembly line, those would be considered random variations. You might notice that your widgets always fall apart at the same place every time you put them together.
Once you've identified the problem areas you need to find solutions. It might mean changing the way you do business or redesigning it entirely. After implementing the new changes, you should test them again to see if they worked. If they fail, you can go back to the drawing board to come up with a different plan.